4.1 Принцип Парето
Изучение
этого инструмента управления качеством начнем с принципа, который
сформулировал
еще в 1897 году итальянский экономист и социолог Вильфредо
Парето: "В
любом деле 20 процентов затраченных усилий дают 80
процентов результата,
остальные же 80 процентов усилий – лишь 20 процентов
результата". Этот
принцип носит имя автора, однако часто его называют "принципом
20/80". Иными словами,
причин, реально и значительно снижающих качество
не так уж
много, и они, как правило, не сосредоточены в одном процессе.
Подавляющее
большинство (80%) дефектов и связанных с ними потерь (прежде всего
–
материальных) возникает из-за небольшого числа причин (20%). Из этого следует,
что не обязательно,
чтобы любая работа была выполнена наилучшим образом. Часто бывает
вполне
достаточно удовлетворительного результата, поскольку упорное стремление
к
совершенству не всегда оправдано с точки зрения затрат
материальных и трудовых ресурсов. Ведь не зря
же народная мудрость гласит: "Лучшее – враг хорошего" и
"Овчинка
выделки не стоит". Аналогичные поговорки есть и у других народов.
Однако на деле
следовать этому привлекательному
принципу непросто. Для этого в любой проблеме, в том числе
и
производственной, необходимо из огромного числа факторов, влияющих на
нее,
выделить те 20 процентов "немногочисленных, существенно важных"
факторов, которые в основном (на 80 процентов), и порождают проблему.
Остальные относят к
"многочисленным, несущественным" факторам.
Сделать такое разделение позволяет диаграмма
Парето.
Диаграмма Парето
- специфический
комбинированный график, на котором совмещены столбчатая диаграмма и
ломаная
кривая. На оси абсцисс указанны анализируемые факторы, на левой оси
ординат –
"весомость" факторов (в рублях, количестве дефектов или других
показателях), на правой - шкала процентов от 0 до 100.
Это
инструмент, позволяющий:
-
наглядно представить относительную значимость ("удельный
вес") основных факторов, влияющих на решаемую проблему;
-
выделить группу наиболее "весомых", на которых необходимо
сосредоточить усилия для достижения наибольшего положительного эффекта
в
решении проблемы;
-
оценить эффективность приложенных усилий.
Диаграмма
Парето используется и в противоположном случае,
когда положительный опыт отдельных цехов или подразделений хотят
внедрить на
всем предприятии. С помощью диаграммы Парето выявляют основные
причины успехов
и широко пропагандируют эффективные методы работы.
При
использовании диаграммы Парето для контроля важнейших
факторов наиболее распространённым методом анализа является так
называемый АВС
- анализ.
Допустим, на
складе находится
большое число деталей - 1000, 3000 и более. Проводить контроль всех
деталей
одинаково, без всякого различия, очевидно, неэффективно. Если
же эти детали
разделить на группы, допустим, по их стоимости, то на долю группы
наиболее
дорогих деталей, составляющей всего 10-15% от их общего количества придется 60-70 % от общей
стоимости всех
деталей, а на долю группы самых дешевых деталей, составляющей 40-50 %
от всего
количества деталей, придётся всего 5-10 % от общей стоимости.
Назовём первую
группу - А, вторую - группой С. Промежуточную
группу, стоимость которой составляет 20-35 % от общей
стоимости, назовем
группой В. Теперь ясно, что контроль деталей на складе будет
эффективным в том
случае, если контроль деталей группы А будет самым жестким, а контроль
деталей
группы С - упрощенным.
Диаграмма
Парето для решения
таких проблем, как появление брака, неполадки оборудования, контроль
деталей на
складах и т.д. строится не в одном варианте. Рекомендуется составлять
несколько
вспомогательных диаграмм, входящих в состав группы А.
4.2
Виды диаграмм
Различают два вида диаграмм Парето:
- по
результатам деятельности;
- по
причинам.
Диаграмма
Парето по результатам деятельности предназначена
для выявления главной
проблемы и отражает следующие нежелательные результаты деятельности:
· качество (несоответствия,
ошибки, рекламации, ремонт, возвраты продукции);
· себестоимость ( объем потерь,
непроизводительные затраты);
· сроки поставок ( нехватка запасов,
ошибки в составлении счетов и срыв сроков поставок);
· безопасность ( несчастные
случаи, аварии).
Диаграмма
Парето по причинам отражает причины
проблем, возникающих в ходе
производства, и используется для выявления главной из них:
· исполнитель работы (смена,
бригада, возраст, опыт работы, квалификация, индивидуальные
характеристики);
· оборудование ( станки,
агрегаты, инструменты, оснастка, организация использования, модели,
штампы);
· сырье (изготовитель, вид
сырья, партия, условия транспортирования и хранения);
· метод работы (условия
производства, приемы работы, последовательность операций);
· контроль и испытания
(качество методики, точность измерения, достоверность и
воспроизводимость
результатов, тип и
состояние измерительных
средств, метрологическое обеспечение производства).
4.3
Методика построения диаграммы
Методика
построения диаграммы Парето состоит в следующем
1.
Решите, какие
проблемы надлежит исследовать и
как собирать данные.
1.1.
Какого типа
проблемы вы хотите исследовать?
(дефектные
изделия, потери в деньгах, несчастные случаи и т.д.).
1.2.
Какие данные надо
собирать и как их
классифицировать? (по видам дефектов, по месту их появления, по
процессам, по
станкам, по рабочим, по технологическим причинам).
1.3.
Установите метод и
период сбора данных
(если
необходимо, используйте специальный бланк).
2.
Разработайте
контрольный листок для регистрации
данных с перечнем видов собираемой информации и возможностью
графической
регистрации данных
проверок.
3.
Заполните листок регистрации
данных и
подсчитайте итоги. Например, по видам дефектов при контроле
пластмассовых деталей.
Контрольный
листок
данных
Дата_______
Смена____ Цех________
Бригада____
Изделие______
Типы
дефектов | Группа
данных | Кол–во
|
Деформация
| / / /
| 3
| Трещины
| /
/ / /
/ / / /
/ / / /
/ / / /
/ / /
| 23
| Разрыв
| /
/ / /
/ / / /
/ / / /
/ / / /
/ / / /
/ / / /
| 29
| Царапины
| /
/ / /
/ / / /
/ / / /
/ / / /
/ / / /
/ / / /
/ /
| 32
| Раковины
| /
/ / /
/ / /
| 8
| Прочие
| /
/ / /
/ / / /
/ |
11
| Итого
| 106
|
Объем
партии ________ Контролер_____________
4.
Для
построения диаграммы Парето заготовьте бланк
таблицы ранжированных данных, предусмотрев в нем графы:
-
итогов
по каждому проверяемому признаку;
-
накопленной
(кумулятивной) суммы числа
дефектов
-
процентов
к общему итогу;
-
накопленных
процентов.
5.
Расположите
данные, полученные по каждому типу
дефектов, в порядке убывания их числа и заполните таблицу.
Примечание: группу
"прочие" поместите в последнюю строку вне зависимости от того,
насколько большим получилось число, т.к. ее составляет совокупность
признаков,
числовой результат по каждому из которых меньше, чем минимальное
значение,
полученное для признака, выделенного в отдельную строку.
Таблица 4.1 -
Ранжированные данные контроля
Типы
дефектов |
Число
дефектов |
Накопленная
сумма дефектов |
Процент
числа дефектов |
Накопленный
процент |
1.
Царапины |
32
| 32
| 30
| 30
| 2.
Разрывы |
29
| 61
| 27
| 57
| 3.
Трещины |
23
| 84
| 21
| 78
| 4.
Раковины |
8
| 92
| 9
| 87
| 5.
Деформация |
3
| 95
| 3
| 90
| 6.
Прочие |
11
| 106
| 10
| 100
| Итого:
| 106
| -
| 100
| -
|
Объем
партии______________
Контролер_______________
6.
Начертите одну горизонтальную и две вертикальные оси. 6.1
Вертикальные оси:
- левая ось: шкала числа дефектов с
интервалами от 0 до числа, соответствующего общему итогу;
- правая ось: шкала процентов с
интервалами от 0 до 100%.
6.2
Горизонтальную
ось разделите на интервалы в соответствии с числом контролируемых
дефектов
(рис. 4.1а)
7. Постройте
столбчатую диаграмму (рис.4.1б).
Начертите
кумулятивную кривую (кривую Парето):
на
вертикалях,
соответствующих правым концам каждого интервала на горизонтальной оси,
нанесите
точки накопленных сумм (результатов или процентов) и соедините их между
собой
отрезками прямых.
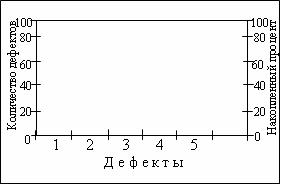 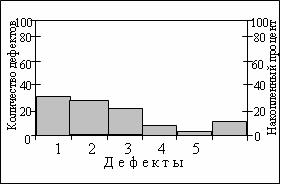
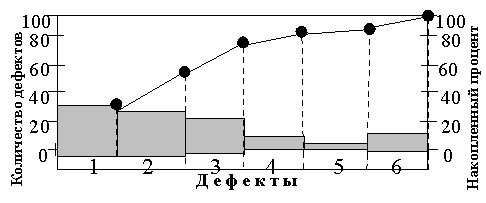
Рисунок 4.1 Последовательность
построения диаграммы
Парето
9
Нанесите на диаграмму все обозначения и надписи: 9.1 Надписи,
касающиеся диаграммы (названия,
разметка осей, наименование изделия, имя составителя диаграммы). 9.2
Надписи,
касающиеся данных (период сбора информации, объект исследования, место
его
проведения, общее число объектов) (Рис. 4.2).
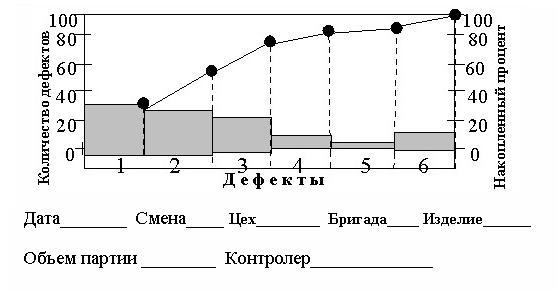
Рисунок 4.2 – Окончательный вид диаграммы
4.4 Особенности
применения
диаграммы
При взгляде
на
построенную диаграмму Парето становится ясным, что группа дефектов 1,
2, 3
(царапины, разрывы и трещины)
составляет
85 процентов от общего числа дефектов и
является основной причиной
потерь.
Естественно, прежде всего необходим анализ причин появления именно этих
дефектов: их устранение наиболее эффективно для решения проблемы
повышения качества
деталей. На левой оси можно было бы отложить финансовые потери,
связанные с
дефектностью продукции. Тогда порядок расположения дефектов на
горизонтальной
оси был бы иной, поскольку потери от разных дефектов различны.
При
построении
диаграмм Парето необходимо обращать внимание на следующие
моменты:
· диаграмма Парето оказывается
наиболее эффективной, если число факторов составляет
7-10;
· при обработке данных
необходимо проводить их расслоение по отдельным факторам, которые
должны быть
хорошо известны (время отбора данных, тип изделий и партия материалов,
процесс,
руководитель, оператор и т.д.);
· при
построении диаграммы
Парето для числа случаев, процента и т.п. в случае возможности подсчета
при
этом суммы затрат следует отражать на диаграмме Парето также и сумму
затрат;
· в
случае, когда фактор
"прочие" оказывается слишком большим по сравнению с другими
факторами, следует повторить анализ содержания фактора
«прочие», а также вновь
проанализировать все факторы;
· если фактор, стоящий первым
по порядку, технически труден для анализа, следует начать с анализа
следующего
за ним;
· если обнаруживается фактор, в
отношении которого легко
провести улучшение,
то его следует проводить, не обращая внимания на его место в порядке
расположения
факторов в диаграмме;
· при систематическом
ежемесячном составлении диаграмм Парето для одного и того же процесса и
сравнении этих диаграмм в некоторых случаях, несмотря на отсутствие
заметных
изменений общего количества брака, меняется порядок расположения
факторов,
влияющих на появление брака. При нарушении стабильности процесса это
сразу
будет замечено.
Если удается
уменьшить влияние всех факторов в одинаковой степени, будет достигнута
высокая
эффективность улучшения.
В сложной
экономической жизни предприятия проблемы могут
возникнуть в любой момент в любом подразделении. Анализ этих проблем
всегда целесообразно
начинать с составления диаграммы Парето. С их помощью можно
анализировать
широкий круг проблем, относящихся практически к любой сфере
деятельности
предприятия. Например:
Качество:
число случаев брака, виды его; потери от брака по видам брака; дефекты
комплектующих; затраты, связанные с рекламациями; причины простоев,
аварий,
поломок технологического оборудования, оснастки; причины несоблюдения
технологической дисциплины; и т.д.
Финансы:
анализ себестоимости изделий (отдельно по видам изделий, по отдельным
статьям
производственной сметы, по затратам на обеспечение качества в процессе
производства); общие затраты на производство;
соотношение затрат на контроль и испытания; анализ прибыли
отдельно по
видам изделий; анализ процента прибыли и т.д.
Сбыт: анализ
прогноза требований
потребителей отдельно по видам изделий; анализ
продаж отдельно по продавцам и по материалам; анализ
случаев получения
рекламаций отдельно по содержанию рекламаций; анализ числа возвращенных
изделий
отдельно по видам изделий; и т.д.
Производство:
анализ числа доработок отдельно по рабочим участкам; анализ
числа неполадок
отдельно по станкам; анализ случаев выхода из строя оборудования по его
видам и
участкам; анализ процента брака отдельно по дням недели; анализ случаев
остановки по процессам; и т.д.
Материально-техническое
снабжение:
анализ
числа дней задержки
поставок отдельно по видам сырья и материалов, по поставщикам; анализ потерь от задержек на
складах отдельно по
видам сырья и материалов; и т.д.
Безопасность
труда: анализ причин несчастных случаев, аварий;
обеспеченность
средствами защиты по их видам, по участкам, по профессиям работников;
травматизм по профессиям, по цехам, по времени; и т.д.
Делопроизводство: анализ числа
предложений по сотрудникам; анализ
продолжительности обработки документов по подразделениям; анализ числа
ошибок в накладных по их видам; и т.д.
Данные,
представленные на диаграмме Парето, нужны для корректной оценки
состояния и
разработки мероприятий по улучшению работы. Поэтому очень важно, чтобы
таким
анализом владели непосредственные исполнители
-
рабочие, контролеры, руководители производственных участков.
Некоторые
выводы из принципа Парето позднее сделал
англичанин Ричард Кох:
Значимых
факторов немного, а
факторов тривиальных - множество и лишь единичные действия приводят к
важным
результатам.
Большая
часть усилий не дает
желаемых результатов.
То,
что мы видим, как правило,
отличается от того, что мы получаем, – всегда существуют
скрытые силы.
Обычно
слишком сложно и
утомительно разбираться в том, что происходит, а часто это и не нужно:
необходимо лишь знать – работает ли Ваша идея или нет, и
изменять ее так, чтобы
она заработала, а затем поддерживать ситуацию до тех пор, пока идея не
перестанет работать.
Большинство
удачных событий
обусловлено действием небольшого числа высокопроизводительных сил;
большинство
неприятностей связано с действием небольшого числа высокодеструктивных
сил.
Большая
часть действий,
групповых или индивидуальных, являет собой пустую трату времени. Они не
дают
ничего реального для достижения желаемого результата.
Он
же рекомендует несколько
правил экономии усилий при любом виде деятельности:
Концентрируйтесь
только на ресурсах,
приносящих наибольшую прибыль, не пытайтесь повысить эффективность всех
ресурсов сразу.
Лучше
“срезать” углы, чем идти
по дороге, делая все крутые повороты.
Пытайтесь
достичь высоких
результатов лишь по нескольким направлениям, а не повышать показатели
по всем
направлениям сразу.
Вместо
того чтобы выполнять
повседневную или (с Вашей точки зрения) рутинную работу самому,
перепоручайте
ее специалистам, которые могут сделать ее более профессионально.
Делайте
только то, что у Вас
получается лучше всего, и то, что Вам нравится делать больше всего.
В
каждой важной для Вас
области старайтесь определить, какие 20% усилий могут привести к 80%
результатов.
Успокойтесь, работайте меньше и ставьте перед собой только
самые важные
цели, при достижении которых закон 20/80 будет работать на Вас, а не
против
Вас; помните: “всех денег не заработаешь”.
Максимально используйте те немногие удачные моменты, когда
Вы способны
показать наивысшие результаты.
|