2
ПРИЧИННО СЛЕДСТВЕННАЯ ДИАГРАММА (диаграмма Исикавы)
Качество изделий
обеспечивается в процессе их изготовления и является результатом
действия целой
системы факторов, влияющих на процесс. Причины, определяющие появление
и
степень воздействия этих факторов разнообразны. Поэтому для
производства
изделий, качество которых удовлетворяло бы запросам потребителей,
прежде всего
необходимо наиболее важным показателям качества (являющимся следствием)
поставить в соответствие различные факторы производства (составляющие
систему
причин). Для этого важно хорошо понимать и контролировать зависимости
между
характеристиками качества и параметрами процессов. Для этой цели удобно
использовать
так называемую причинно-следственную диаграмму,
которую, по имени ее
автора, часто называют диаграммой Исикавы, а также диаграммой
причин
и результатов (Х. Кумэ) или "рыбьим скелетом".
Причин появления
каждой производственной проблемы всегда множество. Но, прежде, чем
решать,
какие из них наиболее существенны, нужно их хотя бы перечислить,
сформулировать
для себя, систематизировать и, что особенно важно, установить
принципиальную
возможность влияния их
друг на друга и
на конечный результат, которым следует считать тот или иной показатель
качества, который необходимо улучшить. Однако, анализировать
эти причины
(или влияющие факторы) гораздо проще, если их структурировать, т.е.
установить
иерархическую зависимость их друг от друга и влияние на конечный
результат. ПРИЧИННО-СЛЕДСТВЕННАЯ ДИАГРАММА - -ГРАФИЧЕСКОЕИЗОБРАЖЕНИЕ
ИЕРАРХИЧЕСКИХ СВЯЗЕЙ МЕЖДУ ПОКАЗАТЕЛЕМ КАЧЕСТВА ПРОДУКЦИИ ИЛИ
ПРОЦЕССА И ФАКТОРАМИ, ЕГО ОПРЕДЕЛЯЮЩИМИ.
Она
помогает:
1. Сформулировать проблему
повышения качества
продукции или процесса.
2.
Выявить и систематизировать факторы, влияющие на выбранный показатель
качества.
3. Оценить возможность
влияния факторов друг на
друга и на показатель качества.
4. Определить
наиболее существенные для
качества факторы.
5. Показать
причинно-следственные отношения
между показателем
качества и
воздействующими на него факторами.
Впервые диаграмму
применил в 1953 г. профессор Токийского университета Каору
Исикава.
Обсуждая проблему на одном из заводов, он суммировал мнения группы
инженеров в
виде схемы, похожей на рыбий скелет.
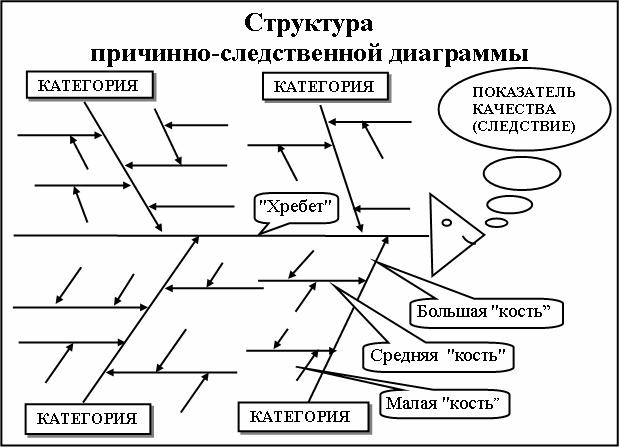
"Хребет" обозначает проблему,
для решения
которой строится диаграмма. Большие "кости" скелета составляют
крупные группы однородных факторов, названных "категориями",
влияющих на показатель качества. Средние и малые "кости" образованы
соподчиненными
группами факторов или отдельными факторами, входящими в каждую
категорию.
Глубина структурирования факторов в принципе не ограничена, на практике
анализ
диаграммы, имеющей более четырех ступеней группировки факторов весьма
сложен.
Очень важно
правильно определить основные категории причин. В зависимости от того,
где
проводят анализ – в производстве или в сфере обслуживания их
набор несколько
различен. В Японии для работников первой линии производства, процесс
представляют как принцип «5 М»:
Materials
(материал) + Machines (оборудование) + Manpower (кадры) + Methods
(методы) + Measurements (измерения). Для
анализа услуг используют принцип «5 Р»:
Peoples (персонал) + Procedures (процедуры) + Patrons (покупатели) + Plase (среда) + Provisions
(обеспечение).
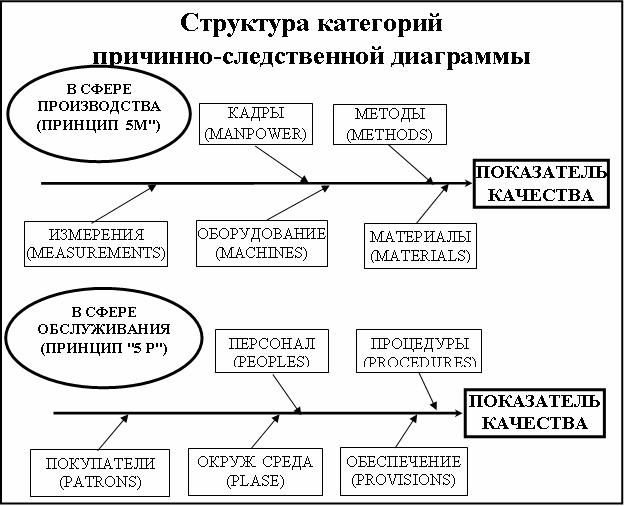
Но сама диаграмма –
не самоцель. Главная работа – впереди. Ее содержание
определяется задачей
анализа. Обычно ставят одну из двух задач:
1.
Для выделения основных причин
несоответствий из их
общего числа.
2.
Для
поиска возможно большего числа причин
несоответствий и их систематизации;
Методика (техника)
построения диаграммы чрезвычайно проста. Соответственно задачам
существует два
основных, принципиально различных метода построения диаграмм.
Первый метод можно характеризовать как движение
"от большого
к малому". Он заключается в поиске на первом этапе самых общих, крупных
причин (категорий), влияющих на выбранный показатель качества. На
втором этапе,
рассматривая поочередно каждую категорию причин, определяют все группы
причин
(вторичных), влияющих на данную категорию. На последующих этапах
последовательно определяют факторы, влияющие на каждую из групп
вторичных
причин. Таким образом поступают до тех пор, пока сохраняется
практическая
возможность для анализа причин. На заключительном этапе выделяют на
каждом
уровне один-два основных фактора и начинают улучшение с нейтрализации
действия
самых "мелких". Добившись этого, пересматривают значимость более
крупных групп, проверяя, не изменилась
ли значимость выделенных здесь ранее существенных групп
факторов.
Продолжая работать таким образом с "мелкими" факторами, добиваются
приемлемого уровня решения проблемы. Для этой работы весьма эффективен экспертный
анализ.
Второй метод построения причинно-следственной
диаграммы характеризуется
как движение "от
малого к
большому". На первом этапе находят как можно большее число любых
факторов,
потенциально способных оказать влияние на выбранный для анализа
"проблемный" показатель качества. Наилучшие результаты здесь дает мозговой
штурм, предусмотренный методикой. Затем последовательно
рассматривают
отношения между каждой парой факторов по принципу "причина –
следствие" и выделите пары, имеющие такую связь. Далее, группируя
отдельные факторы, влияющие на один более крупный, групповой фактор
(сочленяя
несколько мелких "костей" с одной средней. а средние – с
большими),
последовательно строят всю диаграмму. На последнем этапе выделяют на
каждом
уровне основные факторы и категории, оказывающие наибольшее влияние на
проблемный
показатель качества. Выделенные факторы ранжируют и начинают решение
проблемы с
наиболее значимого или с того, влияние которого можно устранить быстро
и с
малыми затратами.
Методика построения
диаграммы вторым методом приведена ниже.
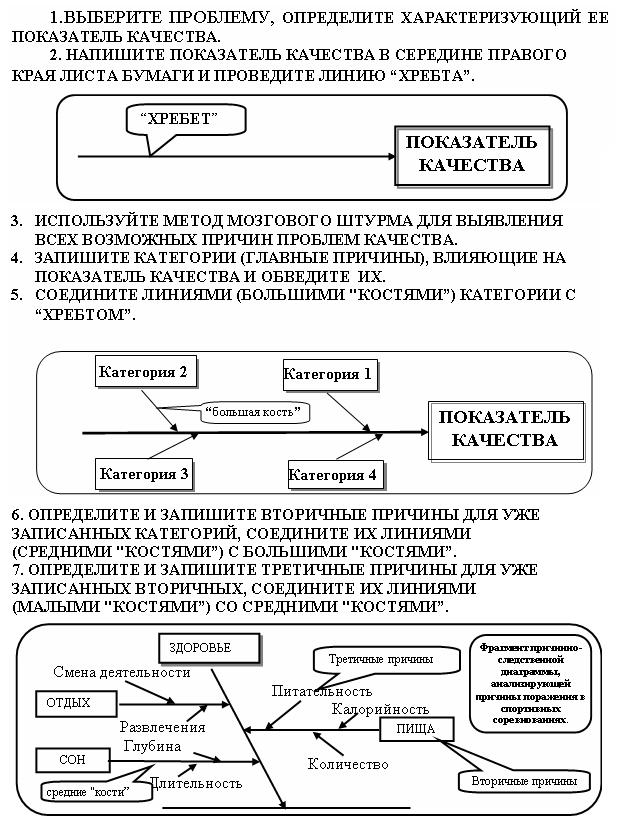
Однако не
обольщайтесь видимой простотой. Чтобы построить полноценную диаграмму,
надо
досконально, в деталях знать анализируемый объект (процесс). Сложность
– в
установлении внутренних, чаще всего неочевидных
причинно-следственных связей, в хорошем понимании не только конкретной
технологии, но и организации производства в целом. Вот почему для такой
работы
обычно привлекают большую группу не только ИТР, но и руководителей, и
опытных
рабочих. Японцы утверждают, что те, кто
умеет строить полноценные причинно-следственные диаграммы,
добились больших
успехов в решении проблем обеспечения качества. В настоящее время этот
инструмент
управления качеством включен в японский промышленный стандарт JIS, он
широко
используется во всем мире в самых разных областях деятельности.
Сколь многообразны
причины брака, можно видеть на следующем примере.
ПРИМЕР 1 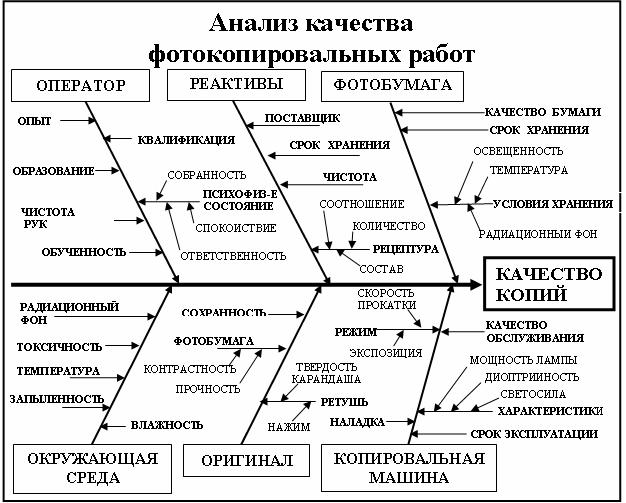
Перечень факторов,
приведенный в схеме, нельзя считать окончательным, его можно дополнить
и
углубить. Степень полноты и глубины диаграммы определяется эрудицией
специалиста, составляющего диаграмму и его опытом в этом деле.
С помощью причинно-следственной
диаграммы
можно решать широкий спектр конструкторских, технологических,
организационных,
экономических, социальных и других проблем.. При поиске причин важно
понимать,
что характеристики, являющиеся следствием, обязательно испытывают
разброс.
Поиск среди этих причин факторов, оказывающих особенно большое влияние
на разброс
характеристик (т.е. результат), называют исследованием причин. При анализе должны выявляться и фиксироваться все
факторы (даже те, которые кажутся незначительными), так как цель схемы
—
отыскать наиболее правильный и эффективный способ решения поставленной
проблемы. На практике достаточно часто встречаются случаи, когда можно
добиться
хороших результатов путем устранения нескольких, на первый взгляд
несущественных
причин. После этого необходимо выявить производственные
участки, отделы,
конкретных лиц, ответственных за доведение корректируемых факторов до
установленного уровня. Необходимо также разработать формы документов
для
слежения за корректируемыми факторами и назначить конкретных лиц,
ответственных
за достоверность собранной информации.
В дальнейшем
необходим регулярный анализ состояния
корректируемых факторов по собранным данным, в том числе и путем
разработки
новых, при необхдимости, более глубоких причинно-следственных диаграмм.
В
настоящее время чаще всего применяют совместно причинно-следственные
диаграммы
и диаграммы Парето. В сложных случаях для выявления
наиболее важных причин можно выяснить мнение
участников анализа экспертным методом, а затем с помощью диаграммы
Парето
установить причины первостепенной важности. При исследовании причин
явления
необходимо привлекать и третьих лиц, не имеющих непосредственного
отношения к
проблеме, так как у них может оказаться свежий взгляд на нее,
неожиданный
подход, которого могут не заметить лица, привычные к данной рабочей
ситуации.
ПРИМЕР
2
Рассмотрим проблему повышения
качества детали
товарного полувагона - закидки люка.
Эти вагоны, выпускаемые Уралвагонзаводом, можно увидеть в любой точке
железных
дорог России и ближнего зарубежья. УВЗ обеспечивает выпуск закидок люка
только
для их первоначального комплектования (28 штук на каждый вагон). Нишу
изготовления закидок в качестве запчастей
«заполнило» малое предприятие
«Урал».
На обоих предприятиях закидки
изготавливают по одной
технологии: литьем в песчаную форму заготовки, обрубкой литников,
обнаждачиванием грата и последующей горячей штамповкой. Проект
допускает
использование в качестве заготовки круглого проката.
Брак
выявляется на стадии эксплуатации вагонов в виде преждевременного
разрушения
закидок в отсутствие ненормативных условий. Разрушения – в
основном в двух сечениях:
- на внутреннем
радиусе крюка;
- в диаметральном
сечении отверстия оси.
На обоих
предприятиях контроль – выборочный, только готовой продукции,
внешним осмотром
и контролем геометрии на соответствие чертежу.
Результат
процесса зависит от многочисленных факторов, между которыми существуют
отношения типа причина-следствие. Проконтролировать все эти причинные
факторы
невозможно. Даже если бы это было возможным, такая работа была бы
нерентабельной.
Если следовать принципу Парето, требуется выделить два-три наиболее
важных фактора
и управлять ими. Но сначала нужно выявить эти главные факторы. Их можно
определить,
например, методом мозговой атаки ли экспертным методом. Потом берут
одну из
наиболее важных причин и, в свою очередь, разворачивают ее в схему,
которая
представляет собой цепь причин и следствий (рисунок 2.1).
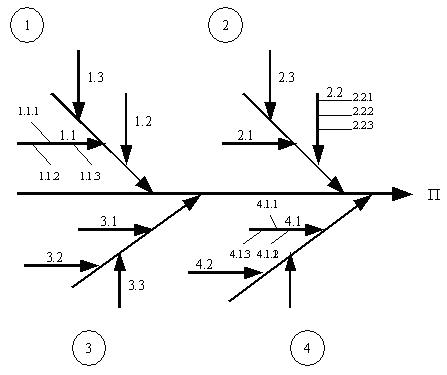
Рисунок
2.1-
Причинно-следственная диаграмма для
анализа причин, вызывающих брак готовой продукции
- закидки железнодорожного вагона
П
- брак готовой продукции;
1
– свойства материала
1.1-
механические
свойства материала:
1.4.1. - прочность
(временное сопротивление, предел текучести);
1.4.2. - ударная
вязкость;
1.4.3. -
пластичность (относительное удлинение, относительное сужение);
1.4.4. –
трещиностойкость (статическая, циклическая).
1.2 -
химический
состав (марка стали
- содержание
углерода, раскислителей, легирующих
элементов, примесей фосфора и серы):
1.2.1-
сталь марки 15Л III;
1.2.2
- сталь марки 20Л III;
1.2.3-
сталь марки 25Л III;
1.2.4
- сталь марки 20ФЛ;
1.3- поставщик
(металлургический комбинат):
1.3.1 – Магнитогорский;
1.3.2 – Череповецкий;
1.3.3 – Мариупольский.
2. -
Наличие
поверхностных дефектов.
2.1
– горячие поверхностные трещины;
2.2
- поверхностные дефекты в соответствии с ТТ чертежа:
2.2.1 - заштампованные усадочные раковины;
2.2.2 - заштампованные песочные, шлаковые
включения, газовые раковины;
2.2.3 - наплыв металла по внутреннему контуру и
по радиусу на
поверхности зуба.
3.- Качество штамповой оснастки.
3.1- сдвиг осей штампов;
3.2 -
недостаточные
штамповые уклоны;
3.3 -
выступ от среза
заусенца по линии разъема штампов.
3.4–
изношенность
штампа;
4 -
Механическая
обработка.
4.1 - Вид используемого
оборудования:
4.1.1 - простой сверлильный станок;
4.1.2 - многошпиндельный сверлильный полуавтомат;
4.1.3 - многошпиндельный сверлильный автомат;
4.2.
– состояние оборудования
4.3
- качество режущего инструмента;
4.4 -
качества рабочего:
4.4.1 – квалификация (разряд);
4.4.2 – стаж работы по специальности;
4.4.3 – период работы на данной операции;
4.4.4 -
морально-психологическое состояние.
Таким образом, получена информация,
необходимая специалисту для принятия управляющих решений, т.е. выявлены
факторы, которые влияют на качество готовой закидки на всех стадиях
технологического процесса.
|