8.1. - Оценка производительности мобильных машин и агрегатов.
8.2. - Оценка производительности стационарных машин и агрегатов.
8.1. Оценка производительности мобильных машин и агрегатов
Производительностью СХМ или агрегатов называется максимальный объем работы в установленных единицах (масса продукта, площадь и т.д.), выполняемый СХМ или агрегатом в единицу времени (секунда, час) при их рациональной эксплуатационной настройке и при обеспечении всех агропоказателей. Работа, выполненная СХМ или агрегатом за рассматриваемый период времени (смена, месяц, год, агросрок), является его выработкой или наработкой.
Производительность - один из важнейших технико-экономи-ческих и эксплуатационных показателей. С её помощью определяются основные удельные показатели: материалоёмкость; трудоёмкость; капитальные затраты и другая информация, необходимая для расчёта экономической эффективности нового агрегата или СХМ. Производительность СХМ или агрегата подразделяется на:
1) производительность за час чистого времени (без учета снижения рабочего времени для выполнения операций, не связанных с реализацией технологических операций: время на холостой ход; технологическое обслуживания; восстановление агрегата; переезд с поля на поле и др.);
2) эксплуатационную производительность – реальная производительность, определяемая в конкретных условиях функционирования СХМ или агрегата по фактически выполненному объему работ.
3) расчетную эксплуатационную производительность, которая используется на стадиях проектирования с учетом задаваемых параметров будущей СХМ или агрегата и учетом возможных условий их эксплуатации. Например, при эксплуатации рабочая ширина захвата жатки меньше её конструктивной ширины; учёт снижения рабочего времени для выполнения операций, не связанных с реализацией технологических операций (время на восстановление, время на технологическое обслуживание, время на переезды с поля на поле и др.).
Расчетная (на стадиях проектирования) эксплуатационная производительность W мобильных СХМ или агрегатов определяется
из выражения [4,19]
W = C × B × V ×t , га/ч, (8.1)
где В – рабочая ширина захвата; V – рабочая скорость; t - коэффициент использования рабочего времени (t<1); С- коэффициент, связывающий размерности величин, входящих в это выражение, если размерности В, (м), V, (км/ч), то С=0,1.
Коэффициент использования рабочего времени – это отношение чистого времени работы СХМ или агрегата (время выполнения технологических операций) к промежутку всего времени, в течение которого оно замерялось (смена, агросрок и т.д.).
. (8.2)
Здесь t
- время чистой работы СХМ или агрегата в период агросрока, ч; t
- время агросрока, ч.
Длительность агросрока зависит от выполнения вида технологических процессов (вспашка, посев, уборка зерновых и т.д.), природно-климатической зоны, в которой выполняется процесс экономической целесообразности.
Оценку величины t, с учетом того, что плановые технологические обслуживания и ремонты будут проводиться вне периода агросрока или в часы, когда СХМ или агрегат не могут работать (например, дождь), рассмотрим для различных схем организаций взаимодействий агрегатов.
8.1.1. Перегрузочная организация работы СХМ и агрегатов на уборочно-транспортных и транспортно-распределительных операциях
Рассмотрим схему организации взаимодействия мобильных агрегатов, при которой возможно максимальное время чистой работы агрегата в период агросрока. СХМ или агрегат работают по схеме –перегрузочные работы агрегатов на уборочно-транспортных и транспортно-распределительных операциях (например, зернокомбайн и транспортные средства для отвоза зерна).
Примем условие «идеальной организации взаимодействия», предусматривающее отсутствие потери времени на маневрирование СХМ или агрегата по полю (без выполнения технологических операций) и времени, затрачиваемого на ожидание загрузки ((разгрузки) (нехватка транспортных средств)).
Для этих условий структура времени агросрока
t
=t
+t
+t
+t
+t
+t
, (8.3)
где t
- время холостого хода СХМ или агрегата в поле; t
- время внепланового восстановления и технологического обслуживания при случайных отказах (время ремонта и обслуживания); t
- время технологического обслуживания (разгрузка бункера (зернокомбайн), загрузка бункера (сеялка)); t
- время переезда с поля на другое поле; t
- время на отдых и естественные надобности оператора.
Конструктивный анализ агросрока должен быть направлен на уменьшение непроизводительной части времени агросрока (при этом возрастёт t
). Для расчета величины коэффициента
удобно каждую из составленных времени агросрока выразить через t
.
Время холостого хода
агрегата выразим через коэффициент полезного использования времени движения агрегата (коэффициент рабочих ходов F)
F =
, при 0<F<1,
где
- длина рабочего хода агрегата;
- длина холостого хода агрегата;
- длина технологического перемещения агрегата за один цикл работы.
Если выразить величину S= V× t и принять различную, но постоянную в пределах выполнения только рабочего или только холостого хода скорость СХМ или агрегата при работе (V
) и на холостом ходу (V
), то
F=
=
;
F+F
=1® t
=
.
При V
= 
F =
.
Отсюда
(
)×F=t
. (8.4)
Величина коэффициента рабочих ходов F зависит от размеров, кинематических характеристик, видов и способов движения СХМ и агрегатов по полю (челночный, петлевой, диагональный и др. (рис. 8.1), размеров поля, схемы холостых поворотов агрегата (рис. 8.2) и др. [19].
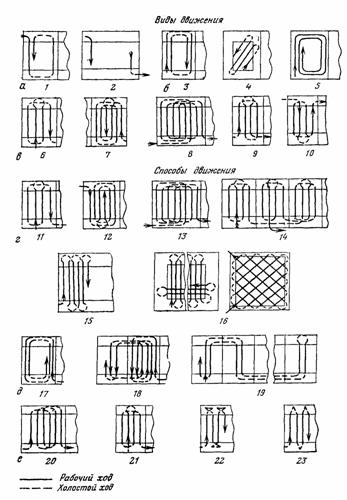
Рис.8.1. Классификация видов и способов движения агрегатов: а - по организации территории; б- по направлению рабочих ходов; в - по общему направлению движения; г – по схеме обработки участка (загона); д- по числу одновременно обрабатываемых загонов; е- по виду поворотов: 1-загонный; 2- беззагонный; 3 – гоновый; 4- диагональный; 5- круговой; 6-правоповоротный; 7- левоповоротный; 8-двухсторонний; 9- от периферии к центру; 10 - от центра к периферии; 11- в свал; 12- вразвал; 13- комбинированный; 14 – с чередованием загонов; 15- челночный; 16-перекрестный; 17- однозагонный; 18 – двухзагонный; 19- многозагонный; 20-беспетлевой; 21- петлевой; 22- с задним ходом; 23 – игольчатый (реверсный)
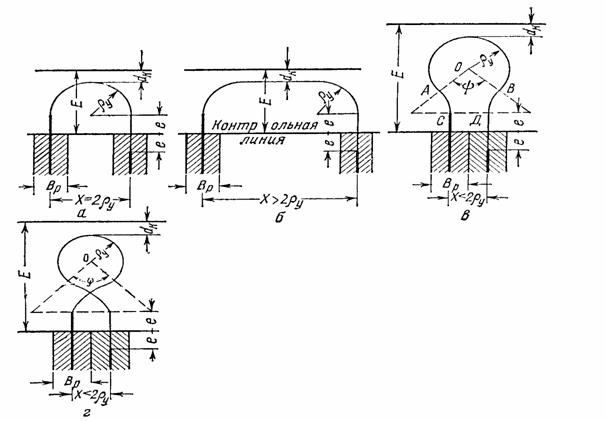
Рис. 8.2. Схемы холостых поворотов агрегата (
- условный радиус поворота): а – по окружности; б- с прямолинейным участком; в – открытый петлевой (грушевидный); г – закрытый петлевой (восьмеркой)
Например [19]:
для челночного способа движения (см. рис.8.1, №15; рис.8.2)
F
=
; (8.5)
для петлевого способа движения (см. рис.8.1, №21; рис.8.2, в)
F
=
; (8.6)
для беспетлевого способа движения (см. рис.8.1,№20; рис.8.2,б)
F
=
, (8.7)
где е,
,
(см. рис. 8.2),
- ширина участка; S
- дополнительное перемещение агрегата, связанное с заделкой поворотных полос (выравнивание почвы, её вспашка и др.);
- оптимальная ширина загона; К
- коэффициент пропорциональности, зависящий от способа движения СХМ или агрегата по полю.
Минимальный радиус r
поворота СХМ или агрегата на поворотной полосе
r
= R
× К
. (8.8)
Здесь R
- минимальный радиус поворота при скорости V= 5 км/ч (см. табл.8.1); В
- конструктивная ширина агрегата); К
- коэффициент изменения радиуса поворота (см. табл.8.2)
Таблица 8.1
Значение наименьшего радиуса поворота для различных агрегатов
Навесной
и полуприцепной
агрегат |
Минимальный радиус поворота R0, м |
Прицепной
агрегат |
Минимальный радиус поворота
R0, м |
Пахотный трех-
восьмикорпусной |
3Вк |
Пахотный трех-
восьмикорпусной |
4,5 Вк |
Культиваторный для сплошной
обработки |
0,9 Вк |
Культиваторный
одномашинный |
1,5 Вк |
Посевной одно-
секционный |
1,1 Вк |
Культиваторный
одномашинный |
1,2 Вк |
Пропашной одно-
секционный |
0,9 Вк |
Культиваторный
Трехмашинный
Бороновальный |
Вк
Вк |
Таблица 8.2
Значения коэффициента К
изменения радиуса поворота
Навесной
агрегат |
К при скорости |
Прицепной
агрегат |
К при скорости |
до 7 км/ч |
7-9
км/ч |
до
7 км/ч |
7-9 км/ч |
Пахотный |
1,05 |
1,20 |
Пахотный |
1,15 |
1,42 |
Культиваторный |
1,06 |
1,32 |
Культиваторный |
1,20 |
1,50 |
Посевной |
1,08 |
1,41 |
Бороновальный |
1,35 |
1,68 |
Пропашной |
1,06 |
1,34 |
Пропашной |
1,32 |
1,57 |
Величина
e ( см. рис.8.2.) прямолинейного выезда с поля на поворотную полосу
e = Е×
, (8.9)
где
- кинематическая длина агрегата
=
, (8.10)
- кинематическая длина трактора (расстояние от кинематического центра трактора до точки присоединения к трактору орудия или сцепки), м;
- кинематическая длина сцепки (расстояние от точки присоединения к трактору до крайней точки сцепки), м;
- кинематическая длина машины или орудия (расстояние от точки присоединения к трактору или к сцепке до крайней точки), м; Е- коэффициент: для агрегатов с задним расположением машин (прицепной агрегат) Е=0,5; для задней навесной машины Е=0,1; для агрегатов с передней фронтальной навесной машиной Е=1.
Значения кинематической длины основных марок тракторов и некоторых машин приведены в табл.8.3. Для машин, кинематическая длина которых не приводится в таблице, её значение можно взять равное габаритной длине из технической характеристики.
Таблица 8.3
Кинематическая длина тракторов и орудий
Марка трактора, сцепки
или орудия |
Кинематическая длина, м |
Марка трактора, сцепки
или орудия |
Кинематическая длина, м |
Трактор:
Т-16МГ,Т-25,Т-30
Т-40М
МТЗ-80, МТЗ-82
Т-150К
Т-70С,Т54В
ДТ-75МЛ, ДТ-75Н
Т-4,Т-4А
Т-150
Т-130
Сцепка:
СП-16
С-11У |
1,00
1,32
1,2/1,3
2,9/2,4
1,85
2,35/1,55
2,45/1,65
2,12/2,55
2,60
6,40
6,80 |
С-18У
СП-15
СП-11
Плуг:
«Труженик»
ПЛН-5-35
ПЛН-4-35
Борона-:
БЗТС-1
БЗСС-1
Культиватор:
КПС-4, КПГ-4Г
КПГ-2,2 |
8,00
7,20
6,70
6,90
4,30
2,60
1,45
1,45
1,0/4,6
3,9 |
Время восстановления t
- выразим через время чистой работы
с помощью коэффициентов технического использования К
К
=
;
=
+
.
Здесь
- время ремонта;
- время обслуживания.
Отсюда
=
.
Если в агрегате много j-х машин, то
t
= t
. (8.11)
Коэффициент технического использования
может быть определен прогнозированием величины
для машин этого класса.
Время на технологическое обслуживание СХМ или агрегата
включает в себя время простоя на загрузку или разгрузку Т
бункеров машин, вошедших в агрегат основным или вспомогательным материалами (бункер зерноуборочного комбайна, бункер сеялки и др.) и числом n этих остановок за один цикл их работы
t
= n ×T
, (8.12)
n =
. (8.13)
где
- длина рабочего пути СХМ или агрегата от одного технологического обслуживания до другого, м.
Для определения рабочего пути СХМ или агрегата обозначим:
вместимость бункера для семенного ящика, определяющего количество остановок - V
, м
;
массу продукции с единицы площади поля (заполняющую или опорожняющуюся на поле) (урожайность, норма высева) –
, кг/га;
объемную массу (плотность) -
, кг/м
;
коэффициент максимального заполнения бункера -
<1 (безразм.).
Тогда
·
= V
·
·

=10
м,
где
- рабочая ширина машины, м.
Подставим
в выражение (8.13), заменив S
= V
· t
, n из (8.13) в (8.12), получим время, затраченное на технологическое обслуживание СХМ или агрегата
=
·T
. (8.14)
Время переезда t
СХМ или агрегата с поля на поле зависит от средней площади (F
) полей, на которой выполняется сельхозоперация проектируемой СХМ или агрегата, расстояния между полями (S
), транспортной скорости (V
) и времени t
перевода агрегата из рабочего положения в транспортное и обратно в рабочее.
t
= К (t
+ t
) ,
где К – количество переездов за время агросрока; t
- среднее время переезда СХМ или агрегата между полями.
С учетом известных зависимостей
t
=
. (8.15)
Здесь
- время перевода j-й машины в агрегате с ее рабочей шириной
из рабочего положения в транспортное и назад в рабочее;
- рабочая ширина агрегата.
Время на отдых и естественные надобности t
оператора определяют долей К
от всего времени его работы
t
= К
. (8.16)
Здесь
- коэффициент использования рабочего времени рассмотренных СХМ или агрегатов можно определить методами краткосрочного прогнозирования (например, методом статистического прогнозирования) по данным аналогов.
Подставив все найденные величины составляющих время t
в выражение агросрока (8.3) и соответственно в выражение (8.2) , разделив числитель и знаменатель на
, получим расчетное усредненное для различных СХМ и агрегатов, выполняющих различные операции , в различных природно-климатических зонах страны, величину коэффициента Т использования рабочего времени агросрока мобильных СХМ или агрегатов для условий перегрузочной организации их функционирования
Т=
.(8.17)
Проведем анализ возможностей обеспечения заданной производительности. В выражении (8.17) к внешним существующим или задаваемым факторам, которые не зависят от конструкций проектируемых СХМ или агрегатов, относятся g ,
, F
, S
, К
, а также длина S
- усредненная длина рабочего хода СХМ или агрегатов по полю, определяющая величину F.
Анализ выражения (8.17) позволяет на проектной стадии оценить возможные пути роста величины Т, а следовательно, и величины эксплуатационной производительности агрегата (8.1) .
Для определения рациональных величин Т
, V
,V
, T
на проектной стадии необходимо ставить и решать инженерные задачи, используя априорную информацию о машинах-аналогах, результатах НИР и ОКР и ограничения, обеспечивающие высокие качественные (гл. 10) показатели СХМ и агрегатов. В связи с этим рассмотрим общие подходы к возможному росту величины Т.
Необходимо стремиться к росту величины коэффициента F рабочих ходов, который зависит от способа движения СХМ или агрегатов по полю (челночный, в свал, вразвал, круговой, диагональный и др.) [19], выбираемый из различных условий (технологических, например, полеглость убираемых зерновых, и экономических). Но для основных способов движений важнейшим фактором, увеличивающим F, на который может влиять проектировщик, является уменьшение длины пути е выезда СХМ или агрегата с конца поля до начала поворота (см. рис. 8.2), зависящее от кинематической длины (8.10) агрегата и его минимальной величины радиуса поворота (8.8).
Увеличение комплексного показателя надежности К
СХМ или агрегата (см. гл. 9) предопределяется определенной системой действий при их проектировании.
Рост объема бункера V
и величина коэффициента его заполнения
теоретически увеличивают коэффициент Т, но при этом существуют известные ограничения: на смещение вверх центра масс машины; допустимые удельные давления колёс на поле (уплотнение почвы колесами СХМ или агрегатов ухудшает её структуру и снижает урожайность, а также изменяет управляемость машин). Для СХМ, работающих на уборке культур, для которых въезд на поле транспортных машин приводит к их травмированию (например, уборка хлопка), ограничением на объем бункера может быть возможность разгрузки бункера только на краю поля. Другим ограничением объема бункера может быть его кратность общему объему V
кузова транспортного устройства:
V
/ V
= С.
Существует необходимость согласования этих и других ограничений при обосновании параметров бункера.
Рост величины коэффициента
определяется формой бункера, использованием устройств для его равномерного заполнения (распределительный шнек).
Стремление к уменьшению времени T
требует рассмотрения и решения комплекса соподчиненных задач: время подъема и опускания рабочих элементов СХМ ограничиваются возможностями гидросистемы её механизмов, их силами инерции, предопределяемыми движущими массами и др.; есть проблемы в сокращении времени на перевод СХМ из рабочего положения в транспортное и наоборот, при переезде СХМ с поля на поле узкозахватные агрегаты переводятся в транспортное положение только с помощью механизмов навески и гидравлики. Для широкозахватных агрегатов необходимо предусмотреть возможность использования складывающихся (с помощью гидросистемы, например, широкозахватные культиваторы) или перевозимых на специальных прицепных транспортных тележках (например, широкозахватные жатки для зернокомбайнов). Все эти и другие технические решения направлены на уменьшение времени T
.
Улучшение эргономических показателей работы оператора (удобство рабочего положения, обзор приборов контроля и управления машиной, освещенность рабочего места, допустимые нормы шумов, загазованности, вибраций и др. (см. гл.10) позволяет при эксплуатации уменьшить долю К
времени на отдых и естественные надобности оператора.
Формула (8.17) может быть применена для расчета величины коэффициента использования рабочего времени СХМ и агрегатов при отсутствии в них бункера; при этом следует принять
=0. (8.18)
Для стационарных машин в выражении (8.17) принимаем
(
. (8.19)
При отсутствии в этих машинах бункера дополнительно принимаем условие (8.18).
При наличии в стационарной машине бункера, выгружаемого после заполнения, количество остановок машины (см. выражение (8.12))
,
где
- производительность машины за 1 час чистого времени, если рассматривается бункер исходного материала, или выход готовой продукции в единицу времени, если рассматривается бункер готовой продукции.
Подставив
в выражение (8.12), получим
. (8.20)
Для этих условий в выражении (8.17)
заменим на
.
При наличии в стационарной машине системы автоматического управления возможно
. (8.21)
Если, на стадии проектирования, СХМ или агрегат характеризуются не рабочей шириной В
захвата, а производительностью Q (кг/с), то из выражения
Q =
получим
. (8.22)
Здесь
- коэффициент, определяющий содержание массы основного продукта в исходной массе убираемой сельхозкультуры (например,
); g – урожайность, ц/га.
Рассмотрим схемы организации взаимодействия мобильных СХМ и агрегатов, при которых коэффициенты Т использования их рабочего времени меньше, чем при выше рассмотренной схеме «перегрузочная организационная работа СХМ агрегатов».
8.1.2. Прямоточная организация работы СХМ и агрегатов на уборочно-транспортных и транспортно-распределительных операциях
Приведенная схема прямоточной организации работы агрегатов и машин (см. рис.6.1, гл.6) показывает, что в рассмотренную выше структуру времени агросрока (8.3) для рассматриваемой прямоточной организации работы агрегата, дополнительно войдут временные составляющие, не связанные с реализацией СХМ или агрегатами технологических операций:
,
,
,
,
, и выводится время
, затрачиваемое на загрузку (разгрузку) на поле. Тогда, для этих условий структура времени агросрока
будет иметь вид
=
. (8.23)
При аналогии с вышеизложенным выразим дополнительные временные составляющие агросрока
( см. п.6.2 (6.8)):
время, затраченное мобильной СХМ или агрегатом на доставку материала (семян, удобрений) или холостой пробег длиной
(км) (при выгрузке на складе материала, например, зерно) «склад-поле», в первом приближении
t
= t
; (8.24)
время
, затраченное на переезд «поле-склад», в первом приближении
= t
· 0,01; (8.25)
время, затраченное на маневрирование СХМ или агрегата в поле (например, для зернокомбайна въезд в полосу для продолжения процесса уборки зерновых)
= 
, (8.26)
где
- длина рабочего гона в поле, м;
время,
, затраченное СХМ или агрегатом на разгрузку (например, зерно из бункера зернокомбайна) или загрузку (например, сыпучие удобрения в бункер разбрасывателя удобрений) на складе
= 
, (8.27)
где
- производительность выгрузного (загрузочного) устройства, кг/ч;
время t
, затраченное СХМ или агрегатом на ожидание загрузки (выгрузки) у склада
t
· t
, (8.28)
где К
- доля времени ожидания от t
, определяется методом краткосрочного прогноза.
Подставив известные (
и найденные величины составляющих t
времён в выражение агросрока ( 8.23) и соответственно в выражение (8.2), разделив числитель и знаменатель на t
, получим расчётное усредненное для различных СХМ и агрегатов, выполняющих различные операции, в различных природно-климатических зонах страны, величину коэффициента Т
использования рабочего времени агросрока мобильных СХМ или агрегатов для условий прямоточной организации работы СХМ или агрегатов
Т
=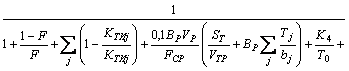
. (8.29)
Анализ выражения (8.29) аналогичен анализу выражения (8.17), позволяет оценить пути роста величины Т
, а следовательно, и эксплуатационной производительности мобильных СХМ и агрегатов при прямоточной системе организации их функционирования.
8.1.3. Групповая организация работы СХМ или агрегатов на уборочно-транспортных и транспортно-распределительных операциях
Проведенный анализ (см. п.6.1) групповой схемы организации работ СХМ или агрегатов показывает, что в рассмотренную структуру времени агросрока (8.3.) дополнительно войдут временные составляющие, не связанные с реализацией технологических операций:
и
.
Тогда, для этих условий, структура времени агросрока
будет иметь вид
=
+
. (8.30)
По аналогии с вышеизложенным, выразим дополнительные временные составляющие агросрока через
:
время
, затраченное СХМ или агрегатом на холостой пробег к обслуживающей машине
; (8.31)
время
ожидания при последовательном заезде СХМ или агрегата в обрабатываемый загон, ожидание в загоне при отказе идущей впереди СХМ или агрегата, ожидание при технологическом обслуживании агрегата и др.
= К
. (8.32)
Здесь К
- доля времени ожидания от
, определяется методами краткосрочного прогноза.
Проведя аналогичные преобразования (п.п.8.1.1 и 8.1.2), получим расчётную усредненную величину коэффициента Т
использования рабочего времени агросрока мобильных СХМ и агрегатов для условий их групповой организации работы

. (8.33)
Анализ выражения (8.33), аналогично анализу выражения (8.17), позволяет оценить пути роста величины
, а следовательно, и эксплуатационной производительности мобильных СХМ и агрегатов при групповой системе организации их функционирования.
8.1.4. Примеры оценочных расчётов эксплуатационной производительности СХМ на проектной стадии
Задача №1. Определить расчетную эксплуатационную производительность Q, (кг/с) и выработку W
, (т) за агросрок самоходного зерноуборочного комбайна, работающего с использованием перегрузочной организации работ и условии отсутствия времени ожидания перегрузочного транспорта (см. п.6.3).
Исходные данные:
1. Ширина захвата жатки В
=6 м; рабочая скорость V
=6 км/ч; объем бункера V
=6,0 м
; производительность за час чистого времени Q =9,0 кг/с; длина зернокомбайна L
=6 м; коэффициент заполнения бункера
=0,85; транспортная скорость
=15 км/ч; время перевода зернокомбайна в транспортное (рабочее) положение Т
= 30 с; ширина зернокомбайна В
=3м; время выгрузки зерна из бункера Т
=0,08 ч.
1. Длина рабочего гона на поле
=1000 м; среднее расстояние между полями
= 1,2 км; движение агрегата по полю челночное; средняя площадь полей
=300 га; средняя урожайность g= 45 ц/га; отношение зерна к соломе с=1/1; плотность зернового материала
=700 кг/м
.
2. Коэффициент технического использования зернокомбайна К
= 0,95.
3. Время агросрока
= 150 ч.
4. Доля времени, от времени агросрока зернокомбайна, на отдых и естественные надобности оператора К
= 0,05.
Коэффициент использования рабочего времени машин прототипов, определенный методом статистического прогнозирования Т
= 0,7.
Решение.
1. Расчетная эксплуатационная производительность Q зернокомбайна
Q = W·
,
где d – коэффициент, определяющий содержание массы зерна в хлебной массе, для заданной величины С
d =
.
Выработку W определим из выражения (8.1.), тогда
Q = 0,1·B
, кг/с.
2. Коэффициент Т использования рабочего времени агросрока:
определим величину коэффициента F рабочих ходов
F =
;
R=1,3 B
= 1,3·3 = 3,9 м;
м.
Величину Т определим из выражения (8.17)
.
3. Расчетная эксплуатационная производительность зернокомбайна
Q =0,1·6·6·0,660·
. кг/с.
4. Выработка W
зернокомбайна
W
= 3,6 · Q ·
= 3,6 · 5,94 · 150 = 3207,6 т.
Задача № 2. Определить расчетную эксплуатационную производительность Q, (кг/с) и выработку W
, (т) за агросрок самоходного зерноуборочного комбайна, работающего по схеме прямоточной организации работы на уборочно-транспортной операции (см. п.6.2).
Исходные данные аналогичны задаче №1; дополнительные данные:
1. Расстояние
от поля до склада выгрузки зерна из бункера зернокомбайна
= 1,5 км;
2. К
= 1,5;
3. Скорость маневрирования зернокомбайна на поле V
=8 км/ч;
4. К
= 0,1 час;
5. Производительность разгрузки бункера зернокомбайна Q
=52500 кг/ч;
6. Доля времени ожидания зернокомбайна на выгрузку зерна у склада от t
- K
= 0,05.
Решение.
1. Расчетная эксплуатационная производительность Q зернокомбайна
Q = 0,1·В
· V
·T
·
, кг/с.
2. F =0,974 (см. решение задачи № 1).
Величину T
определим из выражения (8.29)
T
=

3. Расчетная эксплуатационная производительность зернокомбайна
Q = 0,1·6·6·0,415·
кг/с.
4. Выработка W
зернокомбайна
W
= 3,6 · Q ·
= 3,6 ·3,74· 150 = 2019,6 т.
Задача №3. Определить расчетную эксплуатационную производительность Q, кг/с и выработку W
, т за агросрок самоходного зерноуборочного комбайна, работающего по схеме групповой организации работ (см. п.6.1).
Исходные данные аналогичны задаче №1; дополнительные данные:
1. К
= 1,5;
2. К
= 0,05.
Решение:
1. Q = 0,1·В
·T·
, кг/с
2. F= 0,974 (см. решение задачи №1);
Величину Т
определим из выражения (8.33)
Т
=
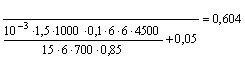
3. Расчетная эксплуатационная производительность зернокомбайна
Q = 0,1·6·6·0,604·
кг/с.
4. Выработка W
зернокомбайна.
W
= 3,6 · Q ·
= 3,6 ·5,44· 150 = 2937,6 т.
8.2. Оценка производительности стационарных машин и агрегатов
Для стационарных СХМ или агрегатов производительность - максимальная подача в них обрабатываемого материала (кг/с) при их рациональной эксплуатационной настройке и обеспечении при этом всех агропоказателей.
При задаваемой или расчетной (на стадии проектирования) производительности Q
за час чистого времени j-й стационарной машины или агрегата их расчетную эксплуатационную производительность Q
определим из выражения
Q
= Q
·Т, (8.34)
где Т - величина коэффициента использования рабочего времени определяется из выражения (8.17) с изменениями (8.18-8.21):
- при наличии загружаемого (разгруженного) бункера с остановкой работы СХМ или агрегатов, без наличия системы автоматического управления СХМ или агрегатов
Т=
; (8.35)
- при отсутствии бункера или возможности его загрузки или выгрузки без остановки СХМ
= 0;
- при наличии системы автоматического управления
= 0.
Производительность Q
за час чистого времени определяется расчетным путем при наличии математических моделей, позволяющих адекватно оценивать заданные величины агропоказателей в зависимости от подачи обрабатываемого материала в СХМ или агрегат при оптимизации их рациональных параметров.
Пример. Оценим расчетным путём производительность
за час чистого времени воздушно-решетной зерноочистительной машины ОЗС-50/25/10 (см. рис.11.59) при очистке зерна пшеницы продовольственного назначения.
Основные характеристики машины, условия и агротребования на функционирование приведены в гл. 11; 15, ввод в программный комплекс ЭВМ для параметрической оптимизации (выбор рациональных размеров отверстий на решетах, частоту их колебаний, рациональной скорости воздушного потока в пневмоканалах) приведен на рис. 11.27, 11.41.
Расчетные функциональные зависимости агропоказателей на очистку зерна пшеницы для фиксированных технологических свойств и задаваемой подачи
в воздушно-решетную машину приведены на рис.8.3.
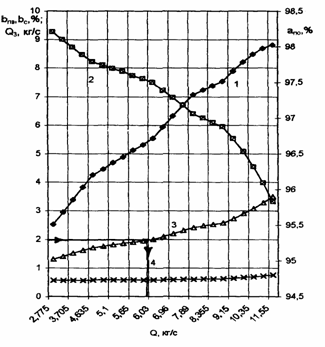
Рис.8.3. Зависимость выхода
(1) зерна пшеницы, очищенного воздушно-решетной машиной, его чистоты апо (2), содержания в нем зерновых
(3) и сорных
(4) примесей от подачи Q исходного зернового материала в машину
Анализ полученных результатов показывает, что агропоказатель b
% (b
cодержание в очищенном зерне сорных примесей, линия №4 на рис. 8.3) выполняется для всего интервала
(2,775…11,55 кг/с). Агропоказатель b
% (b
-содержание в очищенном зерне зерновых примесей, линия №3 на рис.8.3.) выполняется для максимальной подачи, обеспечивающей b
% -
= 6,03 кг/с (21,71 т/ч). Следовательно, для рассмотренных условий работы воздушно-решетной зерноочистительной машины ОЗС-50/25/10 её производительность за час чистого времени
= 6,03 кг/с (27,71 т/ч).
Зависимость расчетной производительности
этой машины от изменения технологических свойств (содержание зерновых примесей) исходного зерна пшеницы приведена на рис. 8.4.
Эксплуатационная производительность и выработка за агросрок этой машины (для условий отсутствия бункера постоянной подачи зернового материала, К
=0,95; К
=0,05; Т
=0,7; t
=500 ч) определяются из выражений (8.35) и (8.37):
=
· Т; (8.36)
Т =
;
= 6,03 · 0,896 = 5,403 кг/с (19,45 т/ч).
Выработка за агросрок
W
=
· t
=19,45·500=9725,18 т. (8.37)
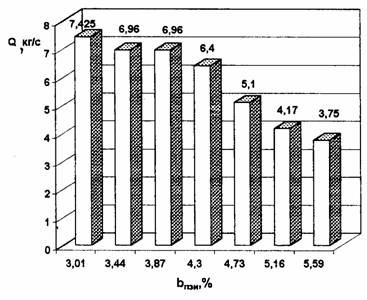
Рис. 8.4. Зависимость производительности Q воздушно-решетной зерноочистительной машины при очистке зерна пшеницы продовольственного назначения от содержания в исходном зерновом материале зерновых b
примесей