13.1. Формирование проблемы, целей, задач и показателей оценки эффективности функционирования объектов параметрического и структурного синтеза.
13.2. Морфологические свойства, определяющие составные части объекта, связи между его элементами и подсистемами, их устройство.
13.3. Построение математической модели процессов функционирования отделений очистки зерноочистительного агрегата.
13.4. Моделирование процессов функционирования отделений очистки зерноочистительного агрегата, параметрический и структурный синтез рациональной схемы и технических средств отделения очистки агрегата.
Структурно-параметрический синтез ставит и решает задачи по обоснованию и разработке новых эффективных методов многооперационного воздействия на материалы, среды, перспективные структуры и образцы техники и комплексы машин, на различное оборудование и комплексы при реализации технологических процессов, взаимодействии с окружающей средой и др., с использованием методов моделирования.
Целью структурного синтеза является определение структуры, объема – перечня типов элементов, составляющих объект, и способа связи элементов между собой в составе объекта.
В качестве примера рассмотрим структурно-параметрический синтез отделения зерноочистительного агрегата (ЗОА) для очистки зерна продовольственного назначения.
13.1. Формирование проблемы, целей, задач и показателей оценки эффективности функционирования объектов параметрического и структурного синтеза
Проблема – повышение качественных показателей процесса сепарации зерновых материалов в отделении первичной очистки зерноочистительного агрегата путем обоснования рациональной совокупности частных технологических операций и технологического оборудования по различным альтернативам для их реализации на основе моделирования частных технологических операций и их различных подсистем, параметрической оптимизации и сравнения этой подсистемы по выбранным технологическим и экономическим показателям с целью создания рациональной структуры отделения очистки агрегата, обеспечивающего качественное выполнение заданного процесса сепарации с минимальными эксплуатационными затратами.
Цель - выявить новые закономерности функционирования рассматриваемых вариантов подсистем частных технологических операций отделения очистки зерноочистительного агрегата и обосновать его рациональную подсистему технологических операций, структуру и основные параметры технического оборудования, обеспечивающие качественную очистку зернового материала с минимизацией эксплуатационных затрат.
Задачи:
1. На основании результатов исследований, априорной информации предложить варианты функциональных схем отделений очистки агрегата как замкнутых систем взаимосвязанных частных технологических операций.
2. Построить адекватную математическую модель процессов функционирования отделений очистки зерноочистительного агрегата как выделенных различных замкнутых квазистатичных систем частных технологических операций, формирующих различные функциональные схемы.
3. Разработать алгоритм и программу ЭВМ для параметрической оптимизации (синтеза) отделений очистки агрегата с различными выбранными функциональными схемами, и техническими средствами для их реализации.
4. На основе сравнения показателей эффективности функционирования различных рассматриваемых функциональных схем и технических средств для их реализации в отделении очистки агрегата выбрать рациональную схему и оборудование (структурный синтез).
Критерий оценки эффективности функционирования отделений очистки зерноочистительного агрегата. Критерием оптимальности оптимизируемых систем при известных или прогнозируемых технико-экономических показателях их элементов (машины, рабочие органы) и системы в целом могут быть критерий Еф эффективности реализации технологического процесса (параметрическая оптимизация) и приведенные затраты 3пр на очистку единицы массы зернового материала, определяемые по показателям функционирования агрегата и нормативным экономическим показателям (структурная оптимизация). Такой подход позволяет сформулировать целевую функцию – минимизация приведенных затрат на очистку зернового материала при обеспечении выделения из него «деловых» фракций (зерно, фуражные и другие отходы) с заданными технологическими ограничениями на их качество.
13.2. Морфологические свойства, определяющие составные части объекта, связи между его элементами и подсистемами, их устройство
Функциональную схему ЗОА можно представить совокупностью технологических операций, обеспечивающих выделение из зерновых материалов с различным содержанием и технологическими свойствами j-х компонентов сорных и зерновых примесей, обеспечивая заданные агротребования. Очевидно, что для выделения этих фракций в агрегате должны присутствовать соответствующие рабочие органы: это пневмосепараторы, барабанные или транспортерные скельператоры для выделения грубых примесей, решетные модули с различными функциональными схемами, обеспечивающими выделение по размерам различных j-х компонентов, овсюжные и кукольные триерные цилиндры.
Последовательность расположения технологических операций определялась из анализа технологических свойств j-х компонентов, присутствующих в исходном материале, их содержанием (долей), предварительным статистическим анализом рациональности выделения различных j-х компонентов, функциональными возможностями существующих и разрабатываемых рабочих органов машин и современными тенденциями и разработками в развитии функциональных схем сепарирования зерновых и других сыпучих материалов.
Проведенный анализ, задачи по реализации в ЗОА унифицированных и перспективных рабочих органов и машин, проведенные предварительно поисковые исследования, а также логико-эвристический подход с целью минимизации частных технологических операций позволил выделить ряд функциональных схем ЗОА как системы взаимосвязанных частных технологических операций, отображенных конечным замкнутым подграфом (рис.13.1), включающим воздушно-решетные машины или решетные модули с четырьмя 3-решетными ярусами.
Каждая вершина
конечного замкнутого графа
предоставляет
-ю частную технологическую операцию множества (табл.13.1)
.
Здесь Х1- накопление исходного зернового материала; Х2 - распределение зернового материала по ширине транспортерного скельператора; Х3- выделение из зернового материала грубых примесей на транспортерном скельператоре; Х4- пневмосепарация зернового материала в канале МПО; Х5- распределение потока зернового материала; Х6- выделение грубых примесей на барабанном скельператоре; Х7- распределение зернового материала по ширине пневмосепаратора и решетных модулей; Х8- пневмосепарация зернового материала в 1-м канале воздушно-решетной машины; Х9- распределение зернового материала по решетным модулям.; Х10, Х13, Х16, Х19, Х27, Х30, Х33, Х36 – выделение из зернового материала мелкой сорной фракции; Х11, Х14, Х17, Х20, Х28, Х31, Х34, Х37 - выделение из зернового материала мелкой зерновой фракции; Х12, Х15, Х18, Х21, Х29, Х32, Х35, Х38 - просеивание под решета очищенного зерна; Х22- пневмосепарация зернового материала во 2-м канале воздушно-решетной зерноочистительной машины; Х23- выделение грубых примесей на барабанном скельператоре; Х24- распределение зернового материала по ширине пневмосепараторов и решетных модулей; Х25- пневмосепарация зернового материала в 1-м канале воздушно-решетной машины; Х26- распределение зернового материала по решетным модулям; Х39- пневмосепарация зернового материала во 2-м канале воздушно-решетной зерноочистительной машины; Х40 - распределение потока зернового материала; Х41, Х42, Х45, Х46 - выделение из зернового материала длинных компонентов; Х43- выделение из зернового материала коротких компонентов; Х47- выделение из зернового материала коротких компонентов; Х49- накопление сорных отходов; Х50- накопление отходов зерновых (фураж); Х51- накопление зерна очищенного мелкого продовольственного назначения (схема фракционная); Х52- накопление зерна очищенного крупного продовольственного назначения (схема фракционная).
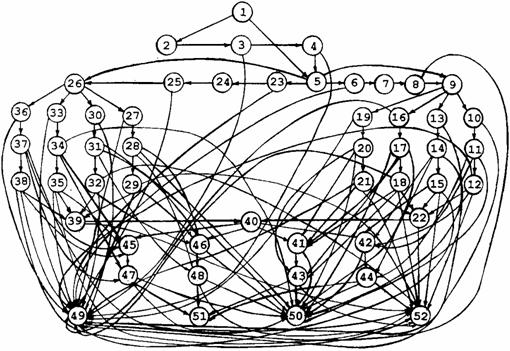
Рис.13.1. Ориентированный граф функциональных схем отделений очистки зерноочистительных агрегатов с использованием воздушно-решетных зерноочистительных машин с многоярусным решетным модулем: 1-52 – номер частной технологической операции (вершины графа)
Таблица 13.1
Элементы замкнутого направленного графа G(X,U) и их функциональные характеристики
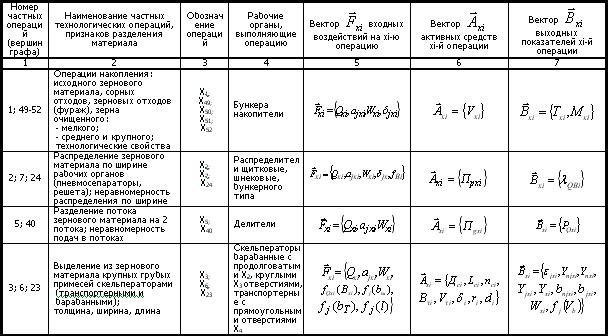
Продолжение табл.13.1
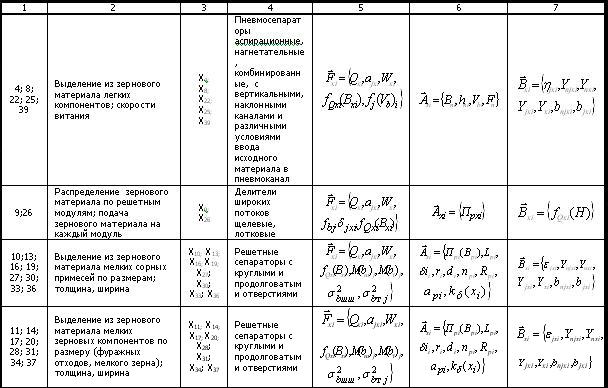
Окончание табл.13.1
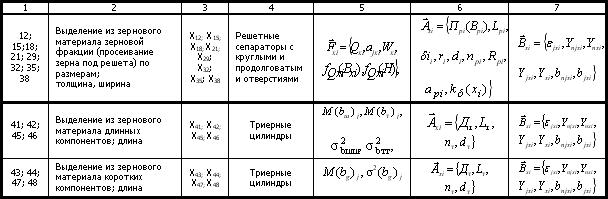
Множество дуг графа
, соединяющих его вершины, несут информацию о результатах технологической операции на предыдущей соединяемой вершине (операции и их связи отражают внутреннюю взаимосвязь системы). При решении задач многомерной оптимизации функциональных схем агрегата необходимо создать банк исходных данных: независимых путей графа и методов оценки весомости дуг графа.
Топологию мультиграфа
описали матрицей
смежности весов мультиграфа, определяющей взаимосвязи вершин графа и матрицей независимых путей графа, определяющей 8 функциональных схем всей исследуемой системы частных технологических операций (табл.13.2, рис.13.2-13.9).
В качестве эталона рассмотрена функциональная схема ЗОА №9 (рис.13.10), которая включает в себя две воздушно-решетные машины ЭВС-20А серийного производства и два триерных блока ЗАВ-10.90.000А.
Таблица 13.2
Матрица независимых путей графа G (X,U) функциональных схем зерноочистительных агрегатов
с использованием воздушно-решетных машин с многоярусным решетным модулем
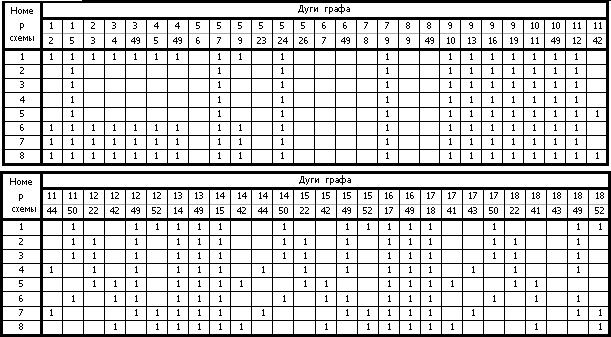
Продолжение табл. 13.2
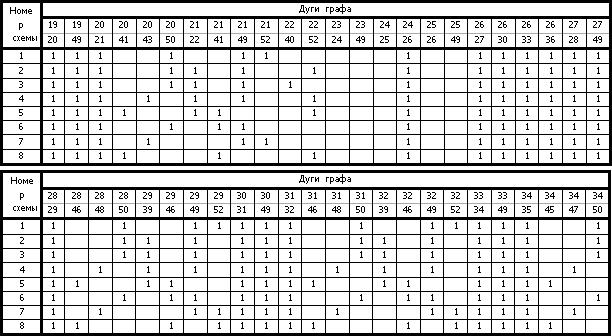
Окончание табл.13.2
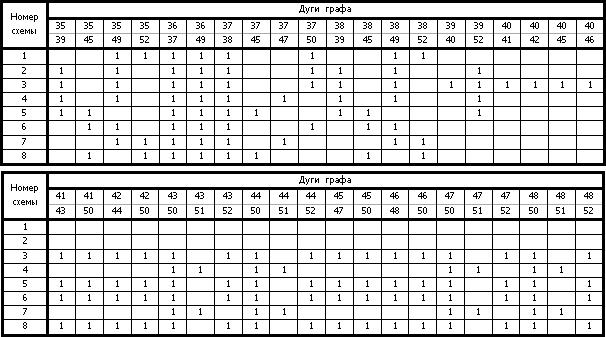
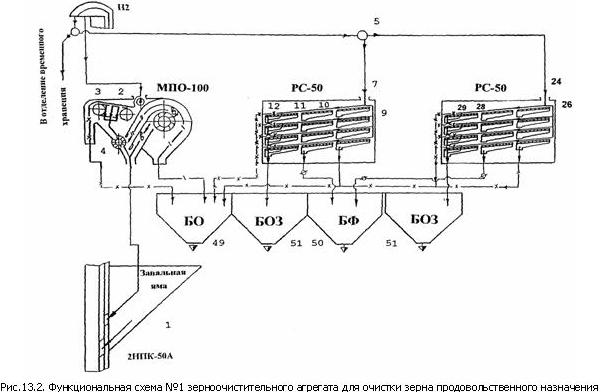
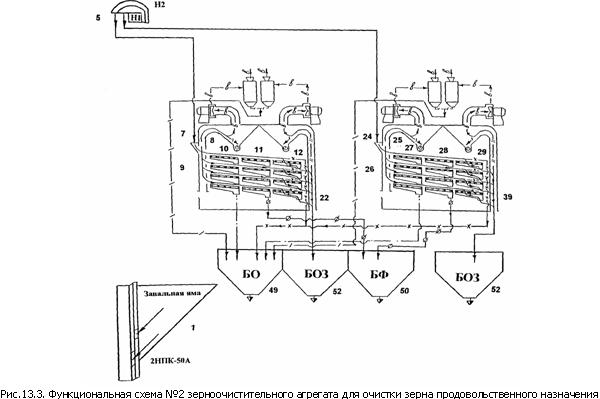
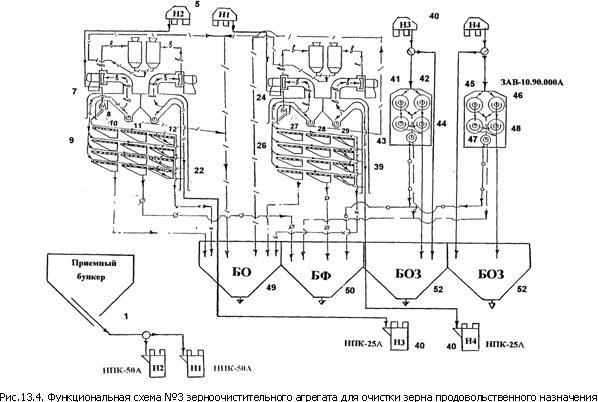
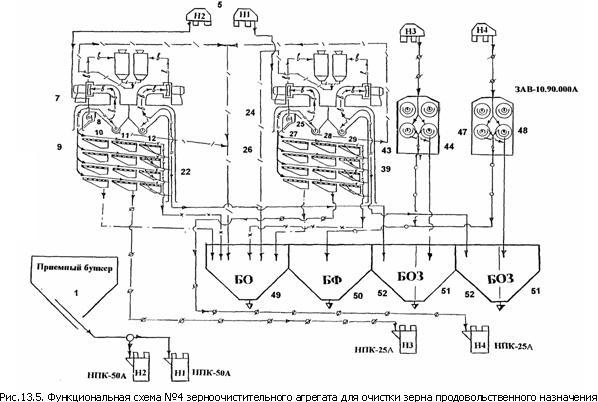
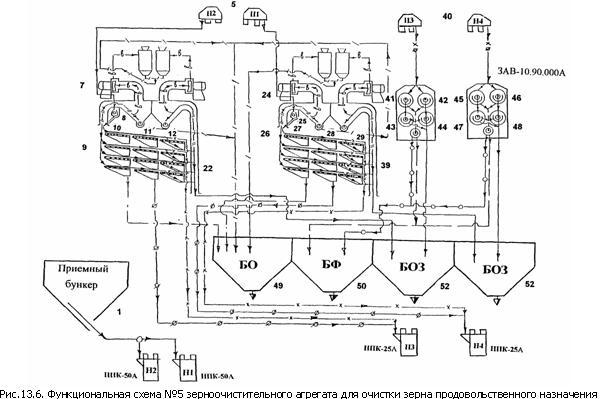
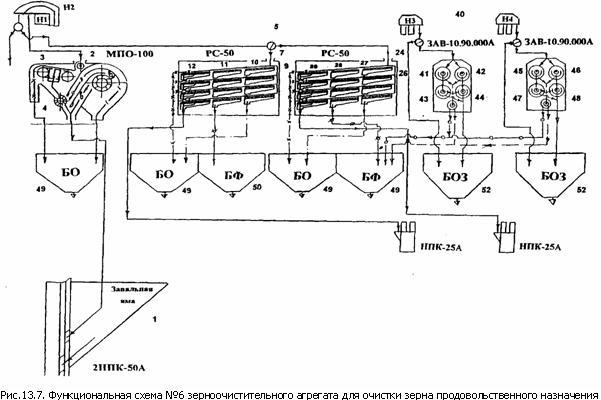
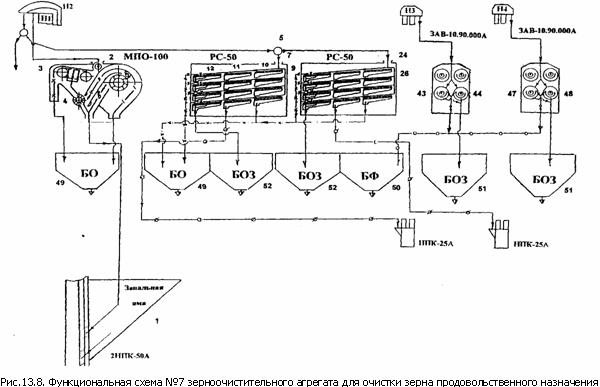
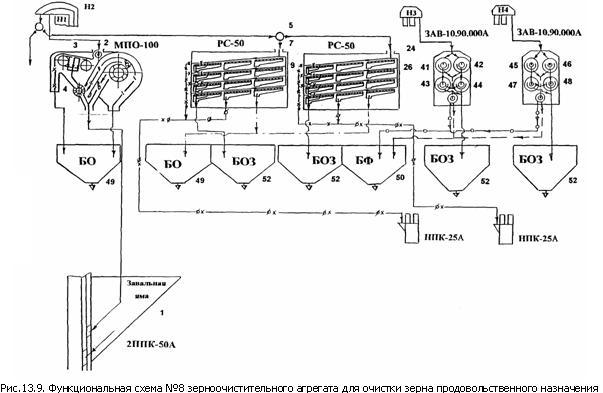
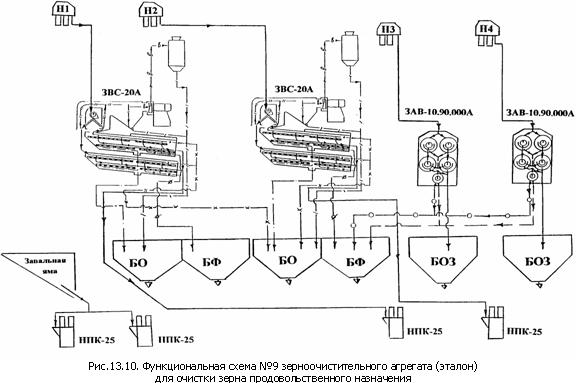
13.3. Построение математической модели процессов функционирования отделений очистки зерноочистительного агрегата
Математическую модель процесса функционирования зерноочистительного агрегата (ЗОА) как замкнутой квазистатичной системы с различными
-ми функциональными схемами в общем виде можно записать:
; (13.1)
(13.2)

,
ограничения на технологические показатели процесса сепарации зерна продовольственного назначения:
. (13.3)
Здесь
- вектор входных воздействий на рассматриваемую систему
, (13.4)
где
- подача зернового материала в агрегат;
- содержание в исходном материале j-х компонентов, их плотность и влажность;
-
математические ожидания и дисперсии размеров признаков разделения j-х компонентов.
- вектор управляющих факторов системы, обеспечивающих ее функционирование
(13.5)
где
- ширина и глубина i-го пневмосепаратора системы;
- рабочая скорость воздушного потока в i-м пневмосепараторе; fq(Bп) -плотность вероятностей распределения подачи зернового материала и воздушного потока fv(Bп) по ширине Вп пневмосепаратора;
- параметры скельператора (диаметр, длина, форма и размеры отверстий, кинематика);
- функциональные схемы решетных модулей;
- параметры решет в решетных модулях (размеры
решетных полотен, форма и рабочие размеры отверстий, эксплуатационная амплитуда колебаний); плотности вероятности распределения зернового материала по решетным ярусам fQx(H) и по ширине решет fQx(В) в решетных модулях зерноочистительных машин;
- функциональные схемы агрегата.
В формуле (13.2)
- функционал, определяющий показатели технологического процесса в агрегате (полнота выделения j-х компонентов, потери зерна, содержание в очищенном зерне других j-х компонентов), для различных
-х его схем;
- функционал, определяющий стоимость потерь, связанных с выходом
зерна в отходы, доли выхода очищенного зерна
, содержание в очищенном зерне сорных bcδ(х) и зерновых bпзδ(х) примесей в зависимости от реализации
схемы агрегата;
- функционал, определяющий изменение потребляемой агрегатом энергии
и балансовой цены оборудования
в зависимости от использования
схемы агрегата;
- графовая модель функциональных схем агрегата, определяющая вариант
-й схемы, минимизирующей
.
Выходные показатели системы определяются вектором
, аргументы которого случайные в вероятностно-статистическом смысле величины
(13.6)
где
- критерий эффективности реализации технологического процесса ЗОА;
- полнота выделения из зернового материала отделяемых j-х компонентов; содержание в очищенном зерне j-х компонентов
, зерновых
и сорных
примесей, потери зерна
на
операции и общие δз;
- массовые выходы очищенного зерна, фуражных отходов и отходов разных категорий; масса
j-х и всех компонентов, содержащихся в зерновом материале после реализации
-й операции; масса
j-х и всех компонентов, выделенных из зернового материала после реализации
-й операции; содержание j-го компонента в массе
очищаемого материала и в выделяемых фракциях
после выполнения
-й операции; полнота прохода
j-го компонента в
очищаемый зерновой материал после выполнения
-й операции.
Для конкретных условий оптимизации величина критерия
определяется как функция суммарных показателей всей системы операций , учитываемых в
-й функциональной схеме
, (13.7)
где
- затраты прямые на обработку 1т исходного зернового материала (ОСТ 70.10.2-83) [1],
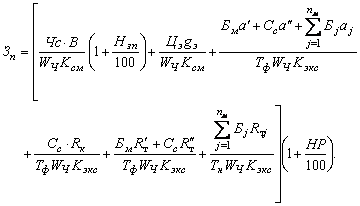
(13.8)
Здесь
- налог на фонд зарплаты; НР – накладные расходы;
- стоимость потерь, связанных с изменением количества и качества зерна продовольственного
(13.9)
Здесь
- массовая доля выхода очищенного зерна к исходному зерновому материалу; HDC – налог на добавленную стоимость;
-оптовая цена очищенного зерна.
Прибыль П при функционировании ЗОА рассчитывается по формуле
, (13.10)
где
- оптовая цена i-х фуражных отходов и их доля выделения из зернового материала при сепарации;
- оптовая цена исходного зернового
материала; обозначения показателей определены в ОСТ 70.10.2-74.
13.4. Моделирование процессов функционирования отделений очистки зерноочистительного агрегата, параметрический и структурный синтез рациональной схемы и технических средств отделения очистки агрегата
Проведем параметрическую оптимизацию (параметрический синтез) отделения очистки агрегата, при этом в качестве критерия, определяющего
функциональную эффективность отделения очистки, обеспечение маскимальной производительности (при выполнении всех заданных агропоказателей процесса сепарации), выбран известный критерий
(13.1). При сравнительной оценке различных отделений очистки агрегата (схемы, оборудование) использованы экономические критерии – суммарные приведенные затраты
(13.8) и прибыль
от очистки зерна в агрегате за период агросрока (13.10).
Сравнительный анализ этих критериев позволит выбрать рациональную схему и техническое оборудование для отделения очистки агрегата для принятых
условий ограничений при моделировании.
Учитывая, что параметры аргументов вектора
(13.5) управляющих факторов системы имеют дискретный характер (например, размеры отверстий решет в
решетном модуле), задачи параметрической оптимизации можно свести к задачам дискретного программирования с использованием при оптимизации метода
регулярного поиска – метода сканирования с ограничениями. При этом для оценки показателей функции цели (13.2) показатели технологического процесса
для различных вариантов функциональных схем рассчитывались и определялись на ПК по разработанным математическим моделям, описывающим
рассмотренные в схемах подсистемы при заданных аргументах векторов
(13.4) и
(13.5), функционал
определял
стоимость отходов и доли очищенного зерна, исходя из показателей функционирования ЗОА, принятой стоимости очищенного зерна и отходов (в зависимости от
содержания в отходах основного зерна и зерновых примесей) и затрат на очистку зерна (13.7) с учетом прямых затрат (13.8) и стоимости потерь, связанных с
изменением количества и качества зерна (13.9).
Параметры функционала
определены выбором современных зерноочистительных машин и оборудования, необходимых для использования
в различных функциональных схемах ЗОА.
Для анализа исследуемых функциональных схем ЗОА с учетом проведенных ранее исследований и априорной информации приняты следующие ограничения:
;
;

;
=28,28%;
(решетный модуль) 4-ярусный 3-решетный
(решето 990 х 790 мм);
R=7,5 мм; W=14%;
7,17≤n ≤8 кол/c; 1,5≤b1≤1,7 мм; 1,7≤b2≤2,0 мм;
3,2≤b3≤3,6 мм; 5,5≤Q≤17,16 кг/с;
5 ≤ Vb ≤ 7 м/с; λv(B)=22%; Mbj=2,645 мм; γ=760 кг/м3;
Содержание компонентов аoj :
аз = 0,898; азп = 0,04; асм = 0,01; ап = 0,005;
ас = 0,003; акп=0,04; аовс= 0,001; адп= 0,003.
PQ(H)1 =0,359; PQ(H)2 =0,266; PQ(H)3 =0,183; PQ(H)4 =0,192.
Аргументы вектора
управляющих факторов системы ЗОА приняты и определены следующими: ширина и глубина i-х пневмосепараторов определялась по техдокументации конкретных машин, используемых в ЗОА, например, пневмоканал МПО:
м,
м.
Входное воздействие на рассматриваемый решетный модуль, определяемое функционалом
, выражается вектором
, независимые аргументы которого
случайные, в вероятностно-статистическом смысле величины [21] (см. гл.11).
Для оценки показателей функционирования транспортерного скельператора в машине МПО-100 (см. рис.13.2) и в триерных блоках (см. рис.13.4), входящих в функционал
(13.2), использованы известные математические модели и разработанные программы (рис.13.11).
Исходные данные для оценки балансовой стоимости зерноочистительного агрегата с различными функциональными схемами отделения очистки приведены в табл.13.13.
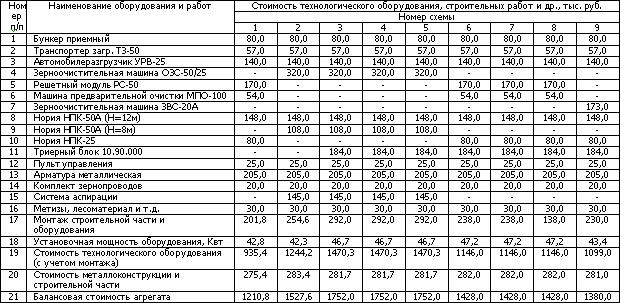
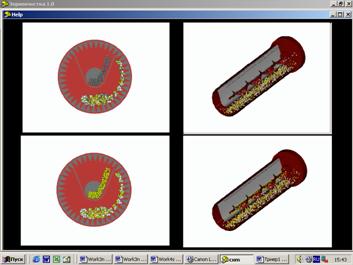
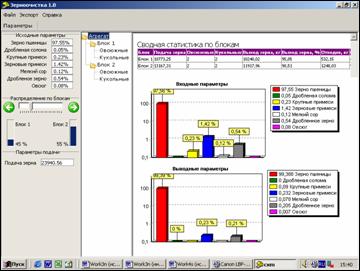
Рис.13.11. Окна ввода исходной информации в ЭВМ для параметрической
оптимизации и оценки показателей функционирования триерных блоков
Разработаны математические модели, адекватно описывающие различные процессы сепарации зернового материала [21-23], реализуемые в функциональных схемах 1-9, построены алгоритмы и программы для ПК, проведен многомерный анализ и параметрический синтез отдельных сепараторов и всего ЗОА, оценены основные его функциональные (показатели функционирования) и технико-экономические показатели (см. рис.13.12-13.14, табл.13.14).
Таблица 13.14
Основные показатели функционирования зерноочистительных
агрегатов с разными структурами
Показатель |
Номер зерноочистительного агрегата |
1 |
2 |
3 |
4 |
5 |
6 |
7 |
8 |
9 |
Рациональная производительность , кг/с |
13,02 |
13,02 |
13,02 |
11,50 |
11,50 |
13,02 |
11,40 |
13,02 |
10,26 |
Энергоемкость , кВт/(кг/с) |
2,68 |
2,49 |
2,92 |
3,21 |
3,21 |
2,94 |
3,37 |
3,95 |
3,60 |
Суммарные приведенные затраты , руб/т |
5,74 |
8,04 |
8,04 |
12,0 |
10,01 |
7,84 |
9,77 |
6,14 |
12,61 |
Прибыть от очистки 1т зернового материала , руб/т |
178,49 |
175,52 |
173,33 |
178,0 |
142,30 |
176,39 |
182,90 |
96,45 |
153,21 |
Прибыль от очистки зерна за агросрок , млн. руб. |
3,08 |
3,01 |
2,90 |
2,80 |
2,10 |
3,0 |
3,80 |
1,70 |
1,99 |
Полученные лучшие показатели функционирования ЗАО - схемы №1, 4, 7 (см. рис.13.2; 13.5; 13.8; 13.13; 13.14) (номера операций, выполняемых в агрегатах, соответствуют номерам операций, изображенных на графе, см. рис.13.1) при очистке зернового материала пшеницы, указывают на достаточную устойчивость выполнения технологического процесса при широкой вариации подач (8,14-13,82 кг/с). При этом выход очищенного зерна 90,48% к исходному зерновому материалу; содержание в очищенном зерне зерновых и сорных примесей соответственно 2,135% и 0,711%. При этом с учетом минимизации технологических операций (оборудования) в агрегате, простоты обслуживания – предпочтительнее ЗОА с функциональной схемой №1 (см. рис.13.2).
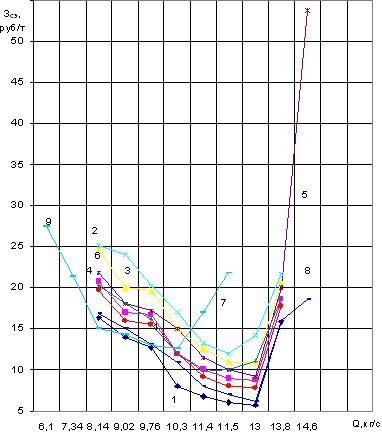
Рис.13.12. Зависимость величины суммарных эксплуатационных затрат Зсэ при очистке одной тонны зерна пшеницы продовольственного назначения в зерноочистительных агрегатах от подачи Q зернового материала в агрегат и его функциональной схемы: 1-схема №1; 2-схема №2; 3-схема №3; 4-схема №4; 5-схема 5; 6-схема №6; 7-схема №7; 8-схема №8; 9-схема №9
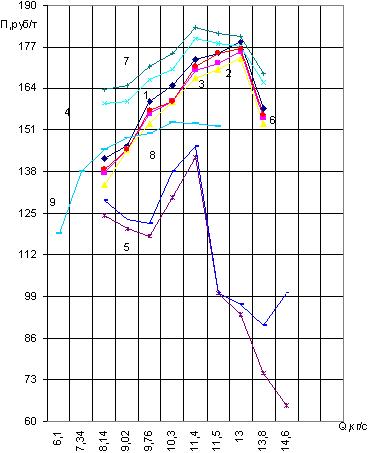
Рис.13.13. Зависимость величины прибыли П при очистке одной тонны зерна пшеницы продовольственного назначения в зерноочистительном агрегате от подачи Q зернового материала в агрегат и его функциональной схемы (обозначения схем см. на рис.13.12)
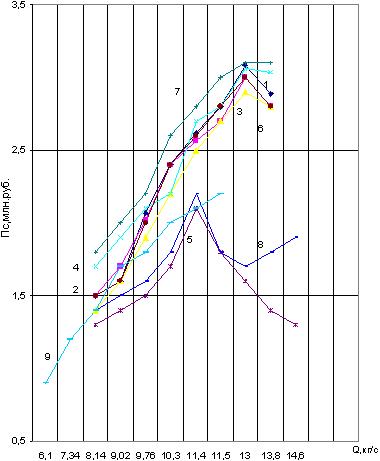
Рис.13.14. Зависимость величины прибыли Пс при очистке зерна пшеницы продовольственного назначения в зерноочистительных агрегатах за период агросрока от подачи Q зернового материала в агрегат и его функциональной схемы (обозначения схем см. на рис.13.12)