15.1. - Методика оценки качества и эффективности сельскохозяйственных машин.
15.2. - Точность, устойчивость и чувствительность технологических процессов.
15.3. - Приемочные лабораторно-полевые испытания воздушно-решетной зерноочистительной машины ОЗС-50/25/10.
15.1. Методика оценки качества и эффективности сельскохозяйственных машин
В процессе разработки документации выбор и проверка новых технических решений, обеспечивающих достижение основных потребительских свойств продукции, должны осуществляться при лабораторных, стендовых и других исследовательских испытаниях моделей, макетов, натуральных составных частей изделий и экспериментальных образцов продукции в целом в условиях, как правило, имитирующих реальные условия эксплуатации (потребления).
Объем и содержание испытаний, необходимых для предотвращения постановки на производство неотработанной, недостаточно надежной продукции, определяет разработчик с учетом новизны, сложности, особенностей производства и применения продукции.
Для подтверждения соответствия разработанной технической документации исходным требованиям и выбора лучшего образца (при наличии вариантов) изготовляют опытные образцы (опытные партии). Необходимость изготовления опытных образцов (партий) и их количество (объем) указывают в техническом задании.
Испытания сельскохозяйственных машин относят к проблеме оценки точности, качества и эффективности технических систем. Они являются источником получения объективной информации о реальных свойствах техники и составляют основу оценки качества машиностроительной продукции в процессе ее разработки, производства и эксплуатации.
Виды испытаний сельскохозяйственной техники различаются по установившимся в практике и гостированным этапам создания новой техники. Действующие государственные (ГОСТ 15.001-88 «Система разработки и постановки продукции на производство. Продукция производственно-технического значения», ГОСТ 16504 -81 «Испытания и контроль качества продукции. Основные термины и определения») и отраслевые стандарты предусматривают около 40 различных видов испытаний. Среди них с организационно-технической точки зрения следует различать исследовательские и доводочные испытания на проектных стадиях создания новой техники, предварительные испытания опытного образца, приемочные испытания доработанных образцов, подготавливаемых к массовому выпуску (из опытной партии или установочной серии), периодические, контрольные испытания при массовом производстве машин и испытания образцов после капитального ремонта, а также сертификационные испытания.
Исследовательские и доводочные испытания проводит разработчик на стадии проектирования СХМ.
На первых двух этапах оценивается эффективность технологических и проектно-сметных решений в части выбранных параметров и типов рабочих органов, компоновочно - технологических схем машин в целом, степени оптимальности базовых параметров машин, показателей их агрегатирования и взаимосвязи с энергетическими средствами в сравнении с лучшими зарубежными аналогами. При этом выявляются ошибки, допущенные при проектировании, уточняются параметры основных рабочих органов и узлов, возможные потенциальные значения эксплуатационно-технических показателей и дается общая оценка соответствия конструкции агрозоотехническим и эргономическим требованиям или технической возможности их достижения.
Предварительные (заводские) испытания организует и проводит предприятие-разработчик изделия с целью предварительной оценки работоспособности изделия, проверки соответствия его основных параметров и характеристик требованиям технического задания, ГОСТ, конструкторской документации и выявления необходимости внесения изменений в конструкцию изделия и документацию на него до предъявления изделия на приемочные испытания.
Испытания проводятся, как правило, в заводских условиях или на специальных испытательных полигонах.
Положительное заключение дает возможность представить продукцию на приемочные испытания, которые проводит головная организация по испытаниям.
Опытные образцы изделий подвергают приемочным испытаниям в сравнении с аналогом. Цель приемочных испытаний та же, что и предварительных, но дополнительно устанавливается возможность представления продукции к производству. Приемочные испытания проводят в два этапа: в лабораторно-полевых условиях и в хозяйственных.
На первом этапе решаются следующие задачи:
- выбор и подготовка полевых участков или объектов для испытаний (зерно, удобрения и др.) и составление их характеристик;
- отладка и настройка СХМ на рациональные условия работы;
- определение качественных показателей работы СХМ;
- проверка эффективности регулировочных устройств и удобства управления машиной;
- определение энергетических показателей.
Приемочные испытания в хозяйственных условиях проводятся после удовлетворительных лабораторно-полевых испытаний. Целью этих испытаний является проверка устойчивости и надежности техпроцесса работы машины в разнообразных условиях, а также определение эксплуатационно-экономических показателей работы машины. В процессе этих испытаний проводят хронометраж для учета показателей надежности и ремонтопригодности, эксплуатационных показателей назначения (производительность и др.).
После положительных приемочных испытаний проводится корректировка конструкторской документации и изготавливается контрольный образец. Оформляется решение о постановке машины на производство, и все ее чертежи согласовываются на технологичность с заводом-изготовителем.
Периодическим испытаниям подвергаются серийно выпускаемые СХМ с целью проверки поддержания их технического уровня, в связи с тем, что при длительном сроке выпуска СХМ происходит износ технологического оборудования, частичная замена материала деталей, внедряются изменения в конструкцию СХМ, но качество машины при этом не должно снижаться.
В целях повышения гарантии качества и защиты интересов потребителя государственная оценка техники предусматривает также ее сертификацию (оценку соответствия требованиям) на основе государственных испытаний, проводимых в аккредитованных Госстандартом РФ испытательных центрах (институтах испытаний машин, испытательных центрах и машиностроительных станциях).
При испытаниях СХМ оценка ее эффективности проводится по различным показателям (табл.15.1).
Таблица 15.1
Основные показатели для оценки качества испытываемых СХМ
№
п/п |
Показатель |
Вид испытаний |
Приемочные |
Периодические |
лабораторно-полевые |
хозяйственные |
1 |
2 |
3 |
4 |
5 |
1 |
Экспертиза конструкции и качества изготовления машины |
+ |
- |
+ |
2 |
Оценка монтажепри-
годности |
+ |
- |
+ |
3 |
Показатели назначения
(агропоказатели) |
+ |
- |
+ |
Окончание табл.15.1
1 |
2 |
3 |
4 |
5 |
4 |
Энергетические |
+ |
- |
+ |
5 |
Оценка безопасности конструкции и ее соответствие санитарно-гигиеническим, эргономическим требованиям |
+ |
+ |
+ |
6 |
Эксплуатационно-
технологические |
- |
+ |
+ |
7 |
Показатель надежности, в т.ч. ремонтно-
пригодности |
- |
+ |
+ |
8 |
Экологические |
+ |
+ |
+ |
9 |
Экономические |
- |
+ |
+ |
По условиям, месту и применяемым методам различают испытания лабораторные (стендовые), лабораторно-полевые и эксплуатационные. В зависимости от продолжительности сроков и решаемых задач испытания проводятся как в нормальных, естественно-производственных условиях, так и имитационных, на специальных полигонах и стендах.
На всех этапах испытаний выполняются разнообразные технологические, эксплуатационные и технические эксперименты, предусмотренные программами испытаний по различным видам оценок (РД 10.1.1088 «Испытания сельскохозяйственной техники. Основные положения», ОСТ 10.1.2-86 «Техника сельскохозяйственная. Виды и программа испытаний»).
Значительное количество оцениваемых показателей качества определяется посредством соответствующих инженерных методов и приемов.
Структура показателей качества машин, в том числе сельскохозяйственных, включает показатели технического уровня, характеризующие прогрессивность новой разработки (степень повышения производительности труда, снижение удельной материало- и энергоемкости, надежность в соответствии с ГОСТ 27.002-83 и др.), функциональные показатели, определяющие качество выполнения машиной основной функции и ее универсальность (различные эксплуатационные и агро-зоотехнические показатели качества), эргономические и эстетические показатели (санитарно-гигиенические и физиологические, показатели безопасности, рациональность и выразительность формы, целостность композиции, товарный вид и др.), экономические показатели, характеризующие как частные издержки (потребителя, производителя) на единицу работы, так и интегральный показатель (ГОСТ 15467-79), отражающий соотношение суммарных затрат на создание новой машины и получаемого экономического эффекта при ее эксплуатации. Значительное количество упомянутых параметров стандартизировано в отраслевом масштабе. К общетехническим параметрам относятся ширина захвата, масса, установленная мощность двигателя, типы и параметры рабочих органов и др., к функциональным – технологические и эксплуатационные показатели качества, энергоемкость, надежность, ремонтопригодность, экономичность.
К инженерно-техническим вопросам оценки качества относится также выбор показателей эффективности, при котором рекомендуется учитывать необходимость и достаточность их количества, зависимость рассеивания показателей под влиянием стохастических свойств естественно-производственных условий, степень чувствительности их к изменению условий и управляющим воздействиям, реализуемость (временную и экономическую) схем испытаний, применяемых для определения тех или иных показателей, а также обеспеченность метрологическим оборудованием, стендами, средствами механизации и автоматизации экспериментов.
Особенность современного подхода к оценке качества состоит в необходимости учета не только структуры потребительских свойств, но и уровня инженерных решений и технико-экономических показателей изготовителя.
При создании новой сельскохозяйственной техники показатели качества задаются потребителем и согласовываются с изготовителями в виде агрозоотехнических требований, основанных на глубоких всесторонних научных изысканиях, отражающих биологические потребности растений и животных и технико-эксплуатационные и экономические требования производства. Заданные таким образом показатели качества составляют критерии его оценки. Соблюдение уровня их показателей качества и зависимости от условий и режимов эксплуатации проверяется при испытаниях.
Критерии качества могут быть отнесены к трем основным классам: критерии пригодности, критерии оптимальности и критерии превосходства. Доминирующее значение при испытании и оценке качества новой техники имеет критерий пригодности, а при решении перспективных задач - критерий оптимальности и превосходства.
Интегральная оценка новой техники определяется увеличением производства продукции, производительности труда и снижением затрат металла, энергии и средств. Однако методика эксплуатационной и технико-экономической оценки новых машин еще недостаточно совершенна и не в полной мере раскрывает показатели хозяйственного использования машин. Для обеспечения высокой достоверности оценки показателей качества, построения критериев эффективности и принятия решений испытания сельскохозяйственной техники должны производиться с достаточным охватом характерных и экстремальных зональных условий, как при реальной эксплуатации, так и при моделировании требуемых условий.
Принятие решения по результатам испытаний относится к многокритериальным задачам, которые решаются методами выделения главного критерия, нахождения компромисса между различными критериями, методами последовательных уступок или путем построения интегральных критериев.
Принятие решений по отдельным критериям эффективности осуществляется сравнением с нормативными данными полученных показателей, характеризующих эффективность применяемых машин с точки зрения качества выполнения технологического процесса, потребляемой энергии, затрат труда и прямых издержек, условий труда обслуживающего персонала, а также определением количественных значений этих показателей, соответствующих перспективным требованиям или же показателям лучших зарубежных аналогов.
Для случаев, когда условия эксплуатации отличаются высокой степенью неопределенности или весьма изменчивы в силу действия природных и других факторов, в общей теории статистических решений сформулирован ряд критериев, которые предостерегают от грубых ошибок. В таких случаях необходимо применять максиминные и минимаксные критерии. Максиминный критерий Yн = max min Yi обеспечивает гарантированный наибольший результат Yн при наихудших условиях. Если речь идет о возможных потерях урожая, продуктивности животных, снижении экономической эффективности, то применяется минимаксный критерий – критерий минимального риска Yн= min max Yr, где Yr= Ymax-Yэ - потери эффективности (условный риск) при экстремальных (наихудших) условиях.
Поиск максиминных и минимаксных критериев требует постановки специальных экспериментов в экстремальных условиях (при максимальной урожайности, наихудших погодных условиях, при влиянии сильнодействующих организационных факторов, различном их сочетании и т.п.), их частой изменчивости, а также накопления и обобщения априорной информации [29].
В целях повышения достоверности результатов испытаний и принятия объективных решений следует стремиться к повышению информативности испытаний, шире использовать обобщенные априорные и апостериальные данные, применять методы моделирования, особенно имитационные, существенно сужающие область неопределенности результатов испытаний.
С ростом числа определяемых показателей эффективности и расширением условий их определения точность, информативность и трудоемкость оценки испытываемых машин увеличивается. Изучение и раскрытие механизмов явлений и причинно-следственных связей при исследовательских и доводочных испытаниях значительно облегчаются построением методик испытаний. В результате повышается их качество и, естественно, результативность решения инженерных задач. Нахождение оптимальных параметров, регулировочных и других режимов работы машин, оценка степени оптимальности их параметров являются важной составной задачей испытаний и требует применения современных научных методов.
Среди задач оценки мобильных машинных агрегатов с эксплуатационной точки зрения большое значение имеют энергетический и динамический анализы процессов их функционирования в зависимости от конструктивных параметров, рациональности построения технологических схем, компоновки рабочей машины и энергетического средства.
При современных испытаниях необходимо не только уделять внимание оценке степени оптимальности выбранных решений по различным техническим, эксплуатационным и технологическим критериям, но и осуществлять всесторонний анализ машин в технологических линиях и комплексах.
Важное значение приобретает прогнозирование технико-экономических показателей испытываемых машин, особенно надежности на ранних стадиях испытаний. При разработке отраслевых и государственных стандартов целесообразно учитывать современные достижения системных наук, шире использовать методы конструктивного анализа машин, что позволит повысить результативность эксплуатационных испытаний машин и сократить сроки их доработки.
Для решения научно-технических задач испытаний сельскохозяйственной техники целесообразно использовать широко развивающиеся системные методы исследований, включающие такие необходимые для испытаний элементы, как иерархия целей и показателей функционирования, оценка процессов функционирования на множестве условий, выявление степени оптимальности (или оптимизация) параметров и типажа машин и прогнозирование возможной их эффективности в перспективе.
Основными направлениями совершенствования методов испытаний являются установление рациональной структуры, последовательности и объема активных и пассивных экспериментов, обеспечивающих получение объективных показателей функционирования машин, и выявление связей между показателями эффективности, естественно-производственными условиями эксплуатации, механико-технологичес-кими принципами построения схем машин и свойствами обрабатываемого материала, режимами работы и параметрами испытываемых объектов с использованием современного арсенала научных методов.
Системный анализ эффективности функционирования машин, оборудования, технологических линий и других объектов, взаимодействующих с обрабатываемыми материалами, животными, окружающей средой, при испытании их как органически целостных систем предполагает замену интуитивно-эмпирического подхода формализованными методами, позволяющими выделить взаимосвязанные элементарные структуры (подсистемы) объекта (этап структуризации), оценить их свойства и параметры (этап параметризации), установить зависимости между параметрами подсистем и действующими внешними и внутренними факторами (этап идентификации), а затем осуществить исследование системы известными методами анализа и синтеза.
При таком анализе важно установить рациональный уровень системного рассмотрения объекта в соответствии с его иерархией, имеющейся априорной информацией и поставленными задачами. Исходя из структуры технологических и производственных сельскохозяйственных процессов и объектов, рекомендуется различать три основных уровня их рассмотрения:
1) микроуровень, характерный для систем типа рабочий орган – перерабатываемый материал, животное-оборудование жизнеобеспечения, механизм-машина, в которых изучаются взаимодействие рабочих органов с обрабатываемым материалом и внешней средой, изменение отдельных функций живого организма под влиянием среды обитания, взаимодействие механизмов и элементов оборудования.
2) макроуровень – для систем, у которых в качестве подсистем могут быть объекты низшего уровня или их укрупненные объединения: машина – внешняя среда, ферма или комплекс машин – внешняя среда и т.п.
3) мегауровень – для систем типа комплексы машин – внешняя среда, сельскохозяйственное предприятие или объединение, действующее в районе, зоне или регионе, эффективность которых определяется валовым производством и экономическими критериями.
Для микроуровня применяются различные технологические, кинематические, энергосиловые и другие характеристики, а оператор отражает главным образом динамические соотношения входа-выхода.
При оценке эффективности функционирования систем двух уровней в качестве главных используются такие критерии эффективности, как производительность, надежность машин, укрупненные технологические показатели качества, продуктивность животных, стоимость произведенного продукта. При этом оператор системы описывается в основном статическими характеристиками.
Таким образом, при испытаниях и исследованиях в наиболее общем случае необходимо обеспечить теоретическую и методическую основу для решения двух главных задач: задачи объективного анализа на множестве внешних условий результатов функционирования сельскохозяйственных машин и комплексов при заданных значениях их параметров (прямая задача) и задачи синтеза, направленной на уточнение или определение оптимальных значений параметров, режимов и условий использования новых типов машин (обратная задача). Основными этапами при решении задач анализа и синтеза являются: точная формулировка целей и организационно-производственных условий функционирования машин, обоснование и выбор критериев показателей эффективности, составление плана-схемы испытаний, учитывающей особенности рассматриваемой системы, составление представлений, а в случае необходимости - построение математической модели системы и процессов ее функционирования, проведение натурных лабораторных и эксплуатационных испытаний, уточнение математической модели, оценка показателей эффективности и более широкое их изучение методом моделирования на ЭВМ, анализ результатов и принятие решений.
При оценке технологических и эксплуатационно-технических свойств современных конструкций сельскохозяйственных машин и машинных агрегатов в процессе испытаний в качестве основного используется метод, сочетающий экспериментальные и теоретические приемы с математическим моделированием. Так как испытания являются неотъемлемым и результативным этапом конструктивной доводки новой техники, то более эффективные результаты получаются тогда, когда аналитическая оценка характеристик машины и показателей их работы уточняется опытным путем, а экспериментальные данные анализируются и обобщаются на базе теоретических положений соответствующих научных дисциплин.
15.2. Точность, устойчивость и чувствительность технологических процессов
Точность и устойчивость работы механизмов и рабочих органов сельскохозяйственных машин – сеялок, разбрасывателей удобрений, опрыскивателей, различных уборочных машин, снабженных копирующими (в том числе автоматическими) и другими устройствами, в связи со спецификой выполняемых ими технологическими операций является определяющим критерием качества.
Задача оценки точности и устойчивости [28, 29], несмотря на большое разнообразие типов механизмов и рабочих органов, сводится к определению статистических (статических и динамических) характеристик выходных координат механизмов и рабочих органов, установлению показателей их динамических свойств при известных характеристиках входных воздействий и их сравнению с агрозоотехническими требованиями.
Достаточной для практических целей мерой точности оцениваемого параметра
при статистическом рассмотрении технологических и эксплуатационных процессов может служить вероятность
выполнения агрозоотехнических требований, что при превалирующем нормальном законе распределения позволяет легко вычислить:
, (15.1)
где Ф – функция Лапласа.
По аналогии с оценкой точности в машиностроении можно использовать показатель точности технологического процесса – коэффициент
, где
-технологический допуск;
- поле рассеяния. Для нормального закона
. (15.2)
Устойчивость и стабильность технологического процесса характеризуется способностью рабочих органов гасить колебания технологических характеристик при возмущениях и поддерживать технологические показатели на установленном уровне при изменении режимов и условий работы в установленных пределах.
Устойчивость технологического процесса можно характеризовать стабильностью его статистических характеристик, в частности, коэффициента вариации оценочных показателей.
(15.3)
при близком к нормальному их распределению.
Во многих случаях коэффициент вариации служит также критерием качества процесса при сравнении испытываемого образца с эталоном по таким показателям, как устойчивость орудий по глубине хода, равномерности распределения семян и удобрений и др. Чем меньше коэффициент вариации, тем меньше рассеивание показателей качества, тем устойчивее процесс.
Отрицательное влияние на точность процесса оказывает смещение (асимметрия) центра измеряемых показателей от срединного поля технологического допуска, оцениваемое коэффициентом смещения:
, (15.4)
где
- среднее значение показателя.
Для текущей оценки устойчивости технологического процесса целесообразно применять выборочный метод статистического оценивания показателей точности. Методы статистического оценивания основаны на проверке гипотезы о случайности выборочной совокупности и проверке отсутствия смещения центра рассеяния и изменения статистических характеристик изучаемого показателя качества. При использовании этих методов производят измерение (отбор) некоторого количества текущих выборок. Методом оперативной обработки получают оценки выборочных характеристик
и
, на основании анализа технологического процесса устанавливают закон распределения исследуемых параметров, а затем с помощью различных критериев согласия проверяют соответствие выборочных данных этому закону.
В большинстве случаев эксплуатационно-технологические характеристики сельскохозяйственных машин подвержены нормальному закону распределения, что свидетельствует о соблюдении условий центральной предельной теоремы, согласно которой на рассеивание технологических показателей оказывает влияние множество независимых маломасштабных факторов без какого-либо доминирующего воздействия. Для этих случаев подтверждение гипотезы о нормальности выборки и общая стабильность коэффициента вариации являются достаточным условием устойчивости и стабильности технологического процесса, что позволяет использовать критерий Романовского
, (15.5)
где
;
;
;
;
;
- дисперсия выборок;
- объем выборок.
При
расхождение между значениями дисперсий признается существенным, а процесс неустойчивым.
При наличии нескольких выборок
(повторений) одновременное их сравнение осуществляется с помощью критериев Кохрена или Бартлета.
Критерий Кохрена
. (15.6)
Если вычисленное значение
, определяемого по таблицам для количества повторностей
, числа степеней свободы
и принятого уровня значимости (обычно 0,05), то гипотеза постоянства рассеяния технологических показателей в анализируемых выборках отвергается.
Критерий Бартлета
, (15.7)
где
;
;
- средняя дисперсия выборок.
Для вычисленного значения
и k=m-1 по таблицам находят вероятность
. При
гипотеза постоянства дисперсий отвергается, что свидетельствует о неустойчивости процесса.
При обнаружении неустойчивости процесса устанавливают причины и вид систематических действующих факторов, вносящих нестабильность в технологический и производственный процесс. Такими факторами могут быть неправильно выбранные параметры рабочих органов или их настройка, а также внутренние факторы, проявляющиеся в машине (например, образование сводов, заторов и забиваний сыпучих и растительных материалов, залипание рабочих органов, проявление существенных нелинейностей в приводе).
На основании выявления физических причин неустойчивости и нестабильности процессов осуществляется конструктивная оценка рабочих органов и машин в целом, а также определяется эффективность вносимых в машину технологических усовершенствований.
С целью повышения объективности оценок качества эксплуатационно-технологических процессов необходимо переходить от средних значений и элементарных статистик к определению законов их распределения и вычислению вероятности обеспечения агротехнических требований.
Вместе с тем, в связи с усложнением конструкций машин, расширением числа и диапазона регулировок скоростных и нагрузочных режимов (например, для зернокомбайна не менее 10), а также в связи с изменением условий работы (состояния почвы, хлебостоя, рельефа и т.п.) обеспечение высокого (оптимального) качества протекания процесса на основе только субъективных визуальных оценок становится невозможным. Поэтому возникает необходимость создания многофакторных моделей процессов и построения соответствующих регулировочных диаграмм, нормативно-справочных материалов, что является особенно актуальным в связи с внедрением так называемых «пооперационных технологий», в которых настройка машин и специально организованный контроль качества с обратной связью, разработка и внедрение средств автоматизации и автоматизированных систем управления являются одним из основных факторов повышения технологической эффективности сельскохозяйственной техники.
Чувствительность процесса в общем случае
,
где
и
-изменение соответственно выходной и входной величин.
Функция чувствительности характеризует влияние отклонения параметров рабочего органа, условий работы или режима движения машин от номинальных значений на изменение выходной величины.
Для процессов, в которых участвуют большие массы материала, чем больше емкость объекта Т, тем медленнее изменяется выходная величина при изменении входной и тем меньше его чувствительность к возмущению.
Чувствительность к возмущению характеризует также динамическую точность рабочих органов. Мера чувствительности объекта к вариации конструктивного или внешнего параметра – коэффициент влияния.
. (15.8)
В качестве коэффициента влияния можно использовать коэффициенты ряда Тейлора:
. (15.9)
Установлено, что характерным свойством агротехнических показателей работы некоторых типов машин, обусловленным принятыми механико-технологическими принципами, является их чувствительность к изменению условий работы. Оценка функций чувствительности рабочих органов к вариациям внешних условий, и наоборот, агротехнических показателей качества к изменению параметров рабочих органов и режимов работы машин свидетельствует о том, что отклонение агротехнических характеристик от оптимальных (номинальных) значений
достигает значительной величины.
Однако в некотором ограниченном диапазоне условий и режимов работы, которые можно назвать номинальными, наблюдается слабая чувствительность показателей качества к их изменению.
Построение функций чувствительности по параметрам внешних условий (влажность почвы, изменение урожайности, качество распределения корней и др.) при их вариации в пределах 15-20% дало аналогичные результаты по таким показателям, как полнота уборки, засоренность вороха, технологическая надежность и др.
Обнаруженные общие закономерности слабого реагирования рабочих органов на контролируемое и неконтролируемое изменение (вариацию) статистических характеристик внешних условий в области оптимума агротехнологических показателей, и наоборот, слабая чувствительность агротехнологических показателей к контролируемым и неконтролируемым вариациям режимов работы машин и параметров рабочих органов, свидетельствует о том, что большинство принятых в практике механико-технологических процессов в большей или меньшей мере отвечают предъявленным требованиям только в достаточно узком диапазоне условий и режимов работы.
Задача совершенствования конструкций состоит в том, чтобы обеспечить максимальную нечувствительность рабочих органов и машин в целом – достаточную их «технологическую грубость».
Важные свойства структуры технологических, энергетических и других процессов могут быть оценены с привлечением теории выбросов. Представим реализацию случайного процесса, описывающего, например, глубину хода рабочего органа или распределение удобрений по полю (рис.15.1). С помощью теории выбросов можно проанализировать следующие показатели процесса:
- число нулей или пересечений некоторого фиксированного (например, по агротехническим требованиям) уровня
снизу вверх при положительной производной функции;
- момент времени первого пересечения уровня
;
- длительность выбросов за уровень
;
- средняя длительность выбросов до уровня
;
- средняя длительность интервала между выбросами и число выбросов;
- значение максимума функции
[28, 29].
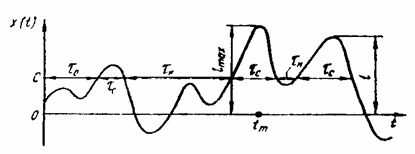
Рис.15.1. Характеристики выбросов случайного процесса
15.3. Приемочные лабораторно-полевые испытания воздушно-решетной зерноочистительной машины ОЗС-50/25/10
15.3.1. Назначение, устройство и техническая характеристика
Машина ОЗС-50/25/10 предназначена для выполнения следующих операций:
- для предварительной очистки поступающих от комбайнов и других молотильных устройств семян и зерна колосовых, крупяных и зернобобовых культур, кукурузы, сорго и подсолнечника от легких, крупных и мелких сорных примесей, отделимых воздушным потоком и решетами с целью лучшего сохранения зерна и семян, подготовки их к сушке и активному вентилированию и повышения эффективности последующей очистки;
- для первичной очистки указанных культур от примесей, отделяемых воздушным потоком и решетами с доведением содержания примесей в заготавливаемом зерне до базисных кондиций;
- для вторичной очистки, сортирования указанных культур и семян трав, используемых как для посева, так и для продовольственных целей.
Краткие сведения о работе и устройстве машин. Основными органами машины являются: рама 1, четыре решетных модуля 2, два эксцентриковых вала 3, механизм очистки решет 4, пневмоканалы 5, 12; осадочная камера 7, приемная камера 6 с сетчатым скельператорным барабаном 11, шнек 8, комплект рукавов 10, а также электроприводы 9 (рис.15.2).
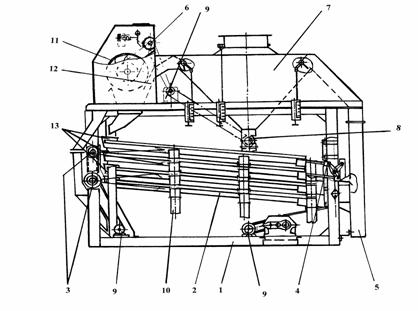
Рис 15.2. Воздушно-решетная зерноочистительная машина ОЗС 50/25/10
Зерновой материал, подлежащий очистке, согласно технологическому процессу поступает (см. рис.15.2) по зернопроводу в приемную камеру 6 на рифленый питающий валик, который равномерно распределяет материал по ширине камеры и через погруженный клапан подается на вращающийся сетчатый барабан 11 (скельператор). Очень крупные примеси, не прошедшие сквозь сетчатый барабан, выводятся из процесса течкой, а зерновой материал, прошедший через барабан, предварительно обрабатывается воздушным потоком в аспирационном канале 12 и поступает на делители потока 13, которые подают зерновой материал равномерно на 4 решетных модуля. В каждом решетном модуле 3 решета установлены последовательно. На первом решете В выделяются подсев, на втором решете Г выделяется фураж, на третьем решете Б сходом выделяется крупные примеси, а проходом - очищенный решетами зерновой материал.
Проход с третьих решет Б поступает в пневмоканал 5, где воздухом отделяются легкие примеси, которые выносятся в осадочную камеру 7 и выводятся из машины шнеком 8, а запыленный воздух через вентилятор и циклон выбрасывается в атмосферу.
Осадочная камера представляет собой сварную конструкцию из листовой стали. Заслонками регулируется скорость воздушного потока.
Решетный модуль представляет собой сварную конструкцию из листовой стали и состоит из каркаса, рамки для прижима решет; делителя зернового потока, стяжек, течек, полотен решетных, щеток. Решетный модуль подвешен на подвесках.
Рама (см. рис.15.2) является остовом для крепления всех узлов машины. Она представляет собой корпус, сваренный из гнутого профиля.
15.3.2. Цель и методы проведения испытаний
Приемочные испытания опытного образца очистителя зерна стационарного ОЗС-50/25/10 проводились с целью:
- проверки наличия конструктивных недостатков и выдачи рекомендаций по улучшению конструкции и качеству изготовления машины;
- определения технологических показателей функционирования очистителя зерна при выполнении им агротехнических требований к очистке различного зернового материала продовольственного и семенного назначения.
- решения вопроса о целесообразности постановки машины ОЗС-50/25/10 на производство и использования по назначению (ГОСТ 16504-81).
Очиститель зерна стационарный ОЗС-50/25/10 был установлен на строительной базе агрегата ЗАВ-20.
Технологический эффект от работы машины определялся степенью очистки поступающего зерна от примесей, отделяемых решетами и воздухом.
Отбор образцов проводился в соответствии с требованиями ГОСТ 13586.3-83.
15.3.3. Функциональные испытания
в режиме первичной очистки зерна пшеницы
Испытания проводились в соответствии с ГОСТ 15001-73, ГОСТ 5036-82Е в режиме первичной очистки зерна ячменя и пшеницы, поступавшего из бункера комбайна в период уборки.
Исходный материал:
- пшеница, содержащая зерновых примесей 4,0…4,3%, мелких сорных примесей 1,3…1,5%, крупных сорных примесей 1,5%, влажность 12,8%, натура 707,6 г/л.
Опытный образец зерноочистительной машины ОЗС-50/25/10, включающий четыре трехрешетных модуля 13 (см.рис.15.2.), оснащался решетными полотнами длиной каждое 790мм: решето №1 - □1,7мм, решето №2 - □2,0мм, решето №3 - □3,6мм. Кинематические параметры работы машины: n=475 об/мин, a=6°, R=8мм. Серийный образец зерноочистительной машины ЗВС-20А (эталон) снабжен стандартными решетными полотнами 740х990мм: решета «Б1» - □3,0мм, «Б2» - □3,2мм, «В» - □1,7мм, «Г» - □2,0мм.
Основные показатели функционирования очистителя зерна стационарного ОЗС-50/25/10 в режиме первичной очистки зерна пшеницы представлены в табл.15.2 и на рис.15.3-15.5.
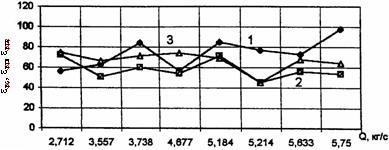
Рис.15.3. Полнота выделения из исходного материала пшеницы сорных
(1), легких
(2) и зерновых
(3) примесей при его первичной очистке в воздушно-решетной машине ОЗС-50/25/10 в зависимости от подачи
зернового материала в машину
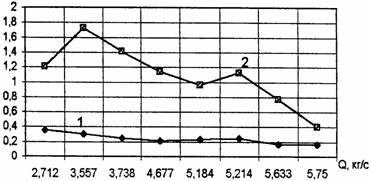
Рис.15.4. Выход зерна пшеницы в неиспользованные
(1) и фуражные
(2) отходы при первичной очистке зернового материала в зависимости от его подачи
в воздушно-решетную зерноочистительную машину ОЗС-50/25/10
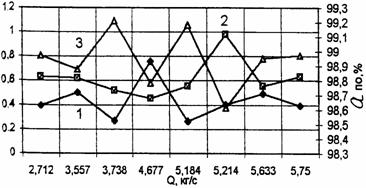
Рис.15.5. Содержание в зерне пшеницы после его первичной очистки воздушно-решетной машиной ОЗС-50/25/10 сорных
(1), зерновых
(2) примесей и чистота
(3) зерна в зависимости от подачи
исходного зернового материала в машину
Таблица 15.2
Основные показатели функционирования очистителя зерна стационарного ОЗС-50/25/10
в режиме первичной очистки зерна пшеницы
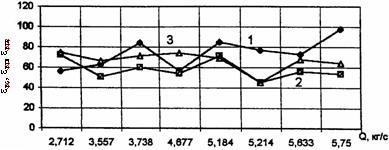
Продолжение табл.15.2
Номер опыта |
Рабочие органы; выход и состав основных фракций |
Решетный модуль |
Проход под решета |
1-е решета |
2-е решета |
Всего,
кг/с |
Процент
к исходному |
Содержание, % |
Всего,
кг/с
|
Процент к исходному |
Содержание, % |
зерно |
зерновые примеси |
сорные примеси |
зерно |
зерновые примеси |
сорные примеси |
1 |
13 |
14 |
15 |
16 |
17 |
18 |
19 |
20 |
21 |
22 |
1 |
0,025 |
0,922 |
41,625 |
45,186 |
13,189 |
0,039 |
1,436 |
82,931 |
14,381 |
2,688 |
2 |
0,043 |
1,212 |
38,085 |
54,028 |
7,887 |
0,071 |
2,010 |
81,314 |
18,045 |
0,641 |
3 |
0,030 |
0,802 |
36,985 |
56,730 |
6,285 |
0,060 |
1,616 |
83,724 |
15,007 |
1,269 |
4 |
0,035 |
0,740 |
38,122 |
55,321 |
6,557 |
0,066 |
1,422 |
79,380 |
19,809 |
0,811 |
5 |
0,044 |
0,859 |
34,401 |
57,563 |
7,836 |
0,065 |
1,254 |
76,578 |
22,759 |
0,663 |
6 |
0,045 |
0,860 |
28,257 |
63,058 |
8,685 |
0,073 |
1,402 |
81,314 |
18,045 |
0,641 |
7 |
0,029 |
0,513 |
39,053 |
53,535 |
7,412 |
0,054 |
0,962 |
79,892 |
19,279 |
0,829 |
8 |
0,030 |
0,522 |
38,565 |
53,102 |
8,333 |
0,063 |
1,099 |
82,569 |
16,590 |
0,841 |
Продолжение табл.15.2
Номер опыта |
Рабочие органы; выход и состав основных фракций |
Основные показатели процесса сепарации |
Решетный модуль |
Сход с 3-х решет |
Очищенное зерно |
Всего,
кг/с |
Процент к исходному |
Содержание, % |
Всего,
кг/с
|
Процент к исходному |
Содержание в зерне, % |
зерно |
зерновые примеси |
сорные примеси |
сорных примесей |
зерновых примесей |
всего |
в т.ч. легких |
всего |
1 |
23 |
24 |
25 |
26 |
27 |
28 |
29 |
30 |
31 |
32 |
1 |
0,036 |
1,327 |
0 |
14,942* |
85,058 |
2,588 |
95,435 |
0,395 |
0,109 |
0,633 |
2 |
0,086 |
2,411 |
0 |
22,973 |
77,027 |
3,324 |
93,455 |
0,503 |
0,20 |
0,621 |
3 |
0,071 |
1,911 |
0 |
20,930 |
79,070 |
3,556 |
95,129 |
0,272 |
0,162 |
0,519 |
4 |
0,053 |
1,133 |
0 |
19,608 |
80,392 |
4,50 |
96,441 |
0,757 |
0,183 |
0,458 |
5 |
0,044 |
0,854 |
0 |
21,818 |
78,182 |
4,975 |
95,967 |
0,266 |
0,112 |
0,553 |
6 |
0,062 |
1,183 |
0 |
19,048 |
80,925 |
4,993 |
95,948 |
0,403 |
0,218 |
0,980 |
7 |
0,089 |
1,586 |
0 |
21,739 |
78,261 |
5,428 |
96,425 |
0,496 |
0,185 |
0,555 |
8 |
0,078 |
1,350 |
0 |
20,896 |
79,104 |
5,539 |
96,172 |
0,395 |
0,078 |
0,633 |
* недомолоченные колоски.
Окончание табл.15.2
Номер опыта |
Основные показатели процесса сепарации |
Очищенное зерно, чистота зерна, % |
Выход зерна в отходы, % |
Полнота выделения отходов, % |
сорные |
зерновые |
сорных |
в т.ч. легких примесей, % |
зерновых |
сорных
и зерновых |
1 |
33 |
34 |
35 |
36 |
37 |
38 |
39 |
1 |
98,972 |
0,352 |
1,210 |
56,256 |
72,374 |
74,539 |
65,503 |
2 |
98,876 |
0,303 |
1,726 |
62,695 |
50,677 |
66,027 |
64,380 |
3 |
99,209 |
0,244 |
1,413 |
84,508 |
59,950 |
71,181 |
77,766 |
4 |
98,785 |
0,214 |
1,142 |
56,485 |
53,770 |
74,333 |
65,515 |
5 |
99,181 |
0,233 |
1,965 |
84,628 |
71,572 |
68,809 |
76,626 |
6 |
98,617 |
0,249 |
1,128 |
76,859 |
44,986 |
45,138 |
60,812 |
7 |
98,949 |
0,161 |
0,772 |
72,945 |
55,678 |
67,601 |
70,241 |
8 |
98,972 |
0,163 |
0,402 |
97,695 |
53,098 |
64,011 |
80,651 |
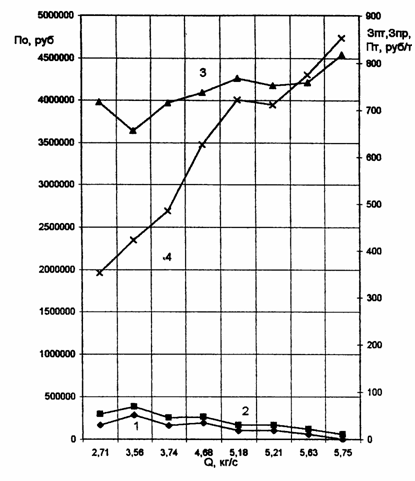
Рис.15.6. Изменение стоимости потерь
(1), связанных с изменением количества и качества очищенного зерна пшеницы, суммарных эксплуатационных затрат
(2) и прибыли от первичной очистки 1 т
(3) и всей партии
(4) исходного зерна пшеницы воздушно-решетной зерноочистительной машиной ОЗС-50/25/10 от величины подач
исходного зерна
При работе в режиме первичной очистки зерна пшеницы производительность зерноочистительной машины ОЗС-50/25/10 варьировалась в пределах от 2,712кг/с до 5,75 кг/с (20,7 т/ч). При этом чистота очищенного зерна колебалась в пределах от 98,6 до 99,2% (см. рис.15.5), полнота выделения сорных примесей составила в среднем 80%, полнота выделения зерновых примесей 60%, легких примесей 65-70% (см. рис.15.3).
Содержание в зерне пшеницы, после его первичной очистки, сорных примесей 0,25…0,8% (агропоказатель вс <1% выполняется), зерновых примесей 0,4…1,0% (агропоказатель впз<2% выполняется) (см. рис. 15.5).
При этом необходимо отметить, что для рассматриваемых случаев увеличение подачи зернового вороха на очистку не существенно влияет на технологические показатели работы зерноочистительной машины ОЗС-50/25/10. Стабильность выполнения машиной технологического процесса при малых и больших подачах показывает наличие значительного резерва увеличения ее производительности.
Таким образом, можно сделать вывод, что проведенные функциональные испытания зерноочистительной машины ОЗС-50/25 в составе отделения очистки зерноочистительного агрегата в режиме первичной очистки зерна пшеницы показали более высокую эффективность выполнения ею технологического процесса по сравнению с серийно выпускаемой зерноочистительной машиной ЗВС-20А.
15.3.4. Экономические показатели работы очистителя зерна
Оценка основных экономических показателей работы очистителя зерна ОЗС-50/25/10 в режиме первичной очистки зерна пшеницы проведены по известной методике (РТМ 8.52.00-107).
Исходные данные по различной пропускной способности агрегата (одна машина ОЗС-50/25/10), выработка агрегата исходя из заданной пропускной способности, принятом коэффициенте использования эксплутационного времени 0,7 и годового времени использования агрегата (400ч), содержание доли (к исходному зерновому материалу) полноценного зерна, доля выхода по массе к исходному зерновому материалу продовольственного зерна и фуражных отходов, содержание в зерне продовольственного назначения после очистки сорных и зерновых примесей определялись соответственно из табл.15.2.
Пример результатов экономического анализа работы очистителя зерна ОЗС-50/25/10 дан на рис.15.6.
Установлено, что для условий проведения функциональных испытаний при первичной очистки зерна пшеницы машиной ОЗС-50/25/10 прибыль от первичной очистке 1т и всей партии зерна соответственно колеблются в пределах (750…800 руб/т и 2000000…4750000 руб (см.рис.15.6).
15.3.5. Оценка надежности очистителя зерна
Надежность оценивалась свойствами безотказности в соответствии с ГОСТ 27.002-83, ГОСТ 23146-79, ГОСТ 23642-79.
Минимальная продолжительность испытаний:
,
где r0=1,61 для доверительной вероятности 0,8 (ГОСТ 11.005-74, табл.11); То-заданная наработка на отказ, То=100ч,
t min=1,61х100=161ч.
Время проведенных испытаний 960ч.
При оценке комплексного показателя надежности учитывались только конструкционные отказы (табл.15.3).
Величина коэффициента готовности:
,
где То - наработка на отказ, 
здесь Т - наработка машины, Т=960ч; К- число отказов за период наблюдений, К=4 (см. табл.15.3).
То = 960/4=240 ч.


Здесь tbi - время на отыскание и восстановление i-го отказа (см. табл.15.3).
ч.
При этом
.
Таблица 15.3
Учет наработки, отказов, времени, затраченного на устранение отказов
Номер отказа |
Наработка с начала наблюдений, ч |
Характер
отказа |
Причина отказа |
Способ устранения отказа |
Число рабочих, устраняющих отказ |
Время на устранения отказа, ч |
1 |
180 |
Поломка эксцентрикового вала привода верхних щеток |
Высокая силовая нагруженность |
Замена, восстановление сваркой |
1 |
2,2 |
2 |
350 |
Выпадание щетки из рамки 2-го решетного яруса |
Недостаточное крепление в рамке |
Восстановление запрессовкой щетки в полость крепления рамки |
1 |
1,5 |
3 |
810 |
Повышенный износ натяжной звездочки привода эксцентрикового вала |
Не упрочнена поверхность зубьев звездочки |
Замена |
1 |
0,8 |
4 |
920 |
Поломка эксцентрикового вала привода верхних щеток (повторно) |
Высокая силовая нагруженность |
Восстановление сваркой |
1 |
3,2 |
15.3.6. Заключение по результатам испытаний
С 1.07.2000г. по 21.03.2001г. Ростовской государственной МИС проведены приемочные испытания очистителя зерна стационарного ОЗС-50/25/10.
Очиститель зерна изготовлен ОАО ГСКБ «Зерноочистка» (г.Воронеж).
Испытания очистителя зерна проведены в условиях, соответствующих условиям его использования по прямому назначению с непосредственным оцениванием и контролем определяемых характеристик свойств объекта (натурные испытания). Место испытаний АОЗТ им.Шаумяна Мясниковского района Ростовской области.
За этот период очиститель зерна проработал 960ч. на очистке зерна пшеницы, ячменя, кукурузы и семян подсолнечника, обработав в общей сложности 13968т.
Испытания очистителя зерна на надежность проводились в хозяйственных условиях. За время испытаний (960 ч) выявлено четыре отказа, все отказы конструктивные, коэффициент готовности 0,992 (по ТУ-0,98).
Выявлено, что составные (транспортные) элементы очистителя зерна стационарного (машина, пылеотделитель, вентилятор с двигателем) при наличии грузоподъемных средств легко устанавливаются в зерноочистительные агрегаты типа ЗАВ-20, ЗАВ-40. Затруднение вызывает вывод фракций крупных примесей (сход с третьих решет решетных станов) и легких, после пылеотделителя, в первую секцию сорных отходов. Установка на машину возвратных течек (по типу машины ЗВС-20А) и пылеотделителя ближе к первой секции агрегата легко устраняет этот недостаток.
Выявлено качественное распределение зернового материала по ширине рабочих органов (пневмосепаратор, решета). Коэффициент вариации подачи зернового материала 14,7%.
Делитель потока удовлетворительно делит зерновой материал по решетным модулям (на четыре потока), коэффициент вариации 22,6%.
Испытаниями установлено, что в режиме первичной очистки зерна пшеницы при производительности машины в час основного времени 20,7 т/ч полнота выделения примесей следующая:
сорных - 97,695%;
зерновых - 64,011%;
всех примесей - 80,651%.
Выход полноценного зерна в отходы:
сорные - 0,163%;
зерновые - 0,402%;
всего - 0,565%.
Чистота очищенного зерна - 98,972%.
Следовательно, для указанной производительности технологическая эффективность очистителя зерна выше заданных агротребований.
По результатам приемочных испытаний приходим к выводу:
1. Очиститель зерна стационарный устойчиво выполняет технологические процессы первичной очистки зерна пшеницы.
2. Коэффициент готовности машины 0,992 (по ТУ-0,98).
3. ОАО ГСКБ «Зерноочистка» - устранить выявленные в конструкции очистительного зерна ОЗС-50/25/10 замечания.
4. Лабораторно-полевые испытания в Ростовской области опытного образца очистителя зерна ОЗС-50/25/10 показали, что после устранения выявленных недостатков в его конструкции, целесообразна его постановка на производство и использование по назначению.