10.1. - Номенклатура и показатели качества объектов проектирования.
10.2. - Методы оценки уровня качества изделия.
10.3. - Стандарты ISO серии 9000.
10.4. - Система управления качеством.
10.5. - Качество машин при технологической подготовке производства.
10.1. Номенклатура и показатели качества объектов проектирования
Качество продукта человеческого труда рассматривается с точки зрения соответствия этого продукта потребностям, для удовлетворения которых он создается.
Качество продукции определяется как совокупность свойств продукции, обуславливающих её способность удовлетворять определенные потребности в соответствии с её назначением в конкретных условиях (ГОСТ 15467-79).
Поэтому при исследовании качества продукта труда рассматривается не вся совокупность свойств, присущих ему, а лишь та группа свойств, которые придаются изделию по воле человека, исходя из заданных условий производства и потребления этого изделия. Например, для потребителя (эксплуатационника) СХМ не имеют значения молекулярная структура и магнитные свойства рабочих органов зернокомбайна.
Качество любого предмета – категория абсолютная, поскольку оно присуще этому предмету независимо от того, подвергают его оценке или нет.
Относительной является количественная характеристика качества как мера качества, познающаяся в сравнении.
Качество продукции закладывается при проектировании и в производстве, а реализуется при её эксплуатации.
Для оценки качества машин применяются единичные и комплексные показатели. Наибольшее применение в машиностроении получили единичные показатели [49].
Основные показатели качества изделия:
1. Показатели назначения.
2. Показатели надежности.
3. Показатели технологичности.
4. Патентно-правовые показатели.
5. Эргономические показатели.
6. Эстетические показатели.
7. Показатели транспортабельности.
8. Показатели безопасности.
9. Экологические показатели.
10. Экономические показатели.
Практический интерес представляет более детальное рассмотрение показателей качества.
Показатели назначения характеризуют свойства продукции, определяющие основные функции, для выполнения которых она предназначена, и обуславливающие область её применения.
Группа разделена на четыре подгруппы:
- классификационные показатели;
- показатели функциональные и технической эффективности;
- конструктивные показатели;
- показатели состава и структуры.
К классификационным относят такие показатели назначения (функциональной пригодности), которые используют как признак классификации продукции (услуги). Классификационными показателями качества являются, например, для транспортных средств – грузоподъемность, эксплуатационная скорость, проходимость; для зерноуборочного комбайна – ширина молотилки, установочная мощность двигателя, емкость бункера, транспортная скорость, наличие адаптеров, позволяющих убирать различные культуры.
Показатели функциональные и технической эффективности характеризуют полезный эффект от эксплуатации или потребления продукции и прогрессивность технических решений, закладываемых в продукцию. Для технических объектов эти показатели называют эксплуатационные. К таким показателям относят: производительность, показатели выполнения технологического процесса (агропоказатели, зоопоказатели).
Конструктивные показатели характеризуют основные проектно-конструкторские решения, удобство монтажа и установки СХМ и оборудования, возможность их агрегатирования и взаимозаменяемости. К этой группе относят такие показатели: габаритные размеры; присоединительные размеры; наличие автоматической системы рациональной настройки СХМ, контроля основных показателей её функционирования и др.
Показатели состава и структуры характеризуют содержание в продукции химических элементов или структурных групп. В эту группу включают, например, такие показатели: процентное содержание легирующих добавок в стали, процентное содержание серы, золы в коксе; процентное содержание сахара, соли в пищевых продуктах; концентрация примесей в кислотах и др.
Показатели надежности определяют свойство объекта сохранять во времени в установленных пределах значения всех параметров, характеризующих способность выполнять требуемые функции в заданных режимах и условиях применения, технического обслуживания, ремонта, хранения и транспортирования. Надежность – сложное свойство, которое образуется в результате объединения четырех подгрупп показателей: безотказности; долговечности; ремонтопригодности; сохраняемости (см. гл.9).
Показатели технологичности характеризуют совокупность свойств конструкции изделия, которая определяет её приспособленность к достижению оптимальных затрат при производстве, эксплуатации и ремонте для заданных показателей качества, объемов выпуска и условий выполнения работ.
Изготовление (прямые затраты труда) любой продукции – невозможно без расходования сырья и материалов (добытых ранее и воплощающих в себя затраты прошлого труда), что и отражается в себестоимости продукции, которая учитывает затраты всех видов труда. Эта модель технологичности изделия с точки зрения затрат труда прямого (трудоемкость), прошлого (материалоемкость)и полного (себестоимость) принята в действующих нормативных документах. Трудоемкость, материалоемкость и себестоимость дополнительно делят на суммарную (общую), структурную, удельную, сравнительную и относительную.
Из характеристики этой группы показателей качества видно, что к показателям технологичности надо было бы отнести сами затраты на изготовление (технологию), а не то, что способствует уменьшению (оптимизации) этих затрат как на этапе проектирования продукции, так и на этапе её изготовления и эксплуатации. Например, удельный вес прогрессивных методов сборки и др.
Для потребителей продукции технологичность непосредственно не связана с удовлетворением какой-либо потребности. Эта связь косвенная и находит выражение как в цене продукции, так и в показателях её надежности. С этой точки зрения потребитель заинтересован в этой группе показателей качества [3].
К показателям технологичности относятся: трудоемкость, материалоемкость, энергоемкость, блочность (сборность), показатели конструктивной стандартизации и унификации.
Трудоемкость определяет количество труда, затрачиваемого на изготовление единицы продукции (или выполнение единицы работы). Необходимо различать следующие виды трудоемкости: общую, структурную, удельную и относительную.
Общая трудоемкость характеризует суммарные затраты труда на изготовление единицы продукции.
С помощью структурной трудоемкости определяют затраты труда по профессиям или по цехам предприятия (например, токарей, литейщиков, сварщиков и т.д.).
Удельную трудоемкость рассчитывают как отношение общей трудоемкости к одному из показателей назначения машины (например, к массе, к производительности, к вместимости разливочного ковша, длине ленточного конвейера и т.д.).
Относительная трудоемкость - это отношение трудоемкости проектируемого изделия к принятой для сравнения трудоемкости.
Если, например, общая трудоемкость выпуска машин ранее составляла 1000 ч, и это было лучшим достижением для данной отрасли, а вновь осваиваемая машина с аналогичными показателями имеет проектную (или фактическую) трудоемкость 800ч, то относительная трудоемкость будет равна 800/1000= 0,8.
С помощью материалоемкости определяют количество конструкционных материалов, необходимых для создания и применения машины с учетом её конструктивных особенностей, проявляемых в сфере производства, эксплуатации и ремонта.
Так же, как и трудоемкость, материалоемкость имеет следующие разновидности: общую, структурную, удельную и относительную.
Общая материалоемкость характеризует суммарную затрату материалов на изделие, причем ее находят двумя способами: по общей массе машины (за вычетом массы комплектующих изделий) и по массе материалов, израсходованных на производство, эксплуатацию и ремонт, включая все виды отходов и потерь.
Структурная материалоемкость характеризует затраты отдельных видов материалов: удельная –затраты материалов на один из показателей назначения машины, относительная рассчитывается по отношению к аналогичному показателю, принятому для сравнения.
Энергоемкость характеризует затраты энергии на единицу продукции, выраженные в киловатт-часах, килограммах пара или других единицах (например, кВт/ч/га).
Блочность (сборность) изделия характеризует трудоемкость ее монтажа.
Коэффициент блочности
, (10.1)
где
и
соответственно число унифицированных и неунифицированных составных частей изделия,
=
+
;
- общее число
составных частей изделия. Коэффициент блочности машин также можно определять по массе или стоимости элементов.
Показатели стандартизации и унификации позволяют определить степень конструктивного единообразия проектируемой или изготавливаемой машины; они свидетельствуют о достижениях конструктора в применении минимально необходимого количества типоразмеров составных частей изделия (деталей, комплексов, комплектов и т.д.) в целях повышения эффективности производства.
К числу важнейших показателей стандартизации и унификации относятся коэффициенты применяемости, повторяемости, насыщенности изделия, а также унификации группы изделий [20].
Коэффициент применяемости
, (10.2)
где n – общее число типоразмеров составных частей изделия; n
- число оригинальных типоразмеров.
К оригинальным типоразмерам относятся составные части, спроектированные или разработанные впервые для данного изделия.
Коэффициент повторяемости К
характеризует среднее число составных частей, приходящееся на один типоразмер, и определяется по формуле К
, где N - общее число составных частей, входящих в данное изделие.
Коэффициент насыщенности изделия повторяющимися составными частями К
вычисляется по формуле
К
=
. (10.3)
Коэффициент унификации группы изделий К
определяется следующим образом:
К
=
, (10.4)
где m – число изделий в группе;
- коэффициент применяемости для i-го изделия;
- годовая программа для i-го изделия;
- оптовая цена, а в отдельных случаях себестоимость i-го изделия.
При отсутствии данных о цене или себестоимости изделий коэффициент унификации можно определить по одной из следующих упрощенных формул:
К
=
; К
=
. (10.5)
Комплексные показатели характеризуют качество машины как совокупности её нескольких простых свойств или по одному сложному свойству, состоящему из нескольких простых. Комплексные показатели находят методом среднего взвешенного (арифметического, геометрического и т.п.).
Примером комплексного показателя, определенного методом среднего (арифметического), может служить показатель
, (10.6)
где
- показатель i-го свойства оцениваемой продукции; 
- коэффициент весомости показателя
.
В случае большего разброса значений
рекомендуется другая формула (среднее взвешенное геометрическое):
. (10.7)
Определяющим называют показатель, по которому оценивают качество продукции. Находят его по формулам (10.6) и (10.7), но при этом q
характеризует q
средние результаты оценки i-го свойства. В том случае, когда определяющий показатель является комплексным, он называется обобщенным. Если хотя бы один единичный показатель неудовлетворительный, то обобщенный показатель следует принимать равным нулю, т.е. качество изделия оценивается как неудовлетворительное.
Интегральным
называется комплексный показатель, характеризующий эффективность машины. Он определяется либо как отношение полезного суммарного эффекта (в натуральном выражении) от эксплуатации машины к затратам на её создание и работу за весь срок службы
=
, (10.8)
либо как обратное отношение этих затрат к полезному эффекту:
=
, (10.9)
где W – количество единиц продукции или выполненной машиной работы за весь срок службы её эксплуатации, например, число произведенных деталей, тонн и т.п.; К
- начальные капиталовложения, включающие ее оптовую цену, доставку, монтаж и наладку; S – эксплуатационные расходы за весь срок службы машины, включая расходы на её ремонт и обслуживание.
В первом случае интегральный показатель определяется работой, приходящееся на 1 руб. суммарных затрат, во-втором - суммой этих затрат в рублях, приходящихся на единицу работы.
Приведенные формулы (10.8) и (10.9) пригодны для вычисления интегрального показателя машины со сроком службы до одного года. При больших сроках службы необходимо учитывать фактор времени. При одинаковых годовых эксплуатационных расходах S в течение Т лет значение интегрального показателя рассчитывается по формуле
=
, (10.10)
где Е
- нормативный показатель эффективности, принимают Е
=0,15.
Патентно-правовые показатели качества изделия характеризуют патентно-правовой уровень защиты принятых при его разработке технических решений, а также конкурентоспособность изделия на мировом рынке.
Уровень качества изделия оценивают с учетом данных об их патентной защите, приводимых в патентном формуляре и карте технического уровня и качества изделия (ГОСТ 2.110-71).
Показатель патентной защиты характеризует количество и весомость новых отечественных изобретений, реализованных в данном изделии, т.е. степень защиты изделия принадлежащими российским предприятиям и организациям патентами внутри РФ и за рубежом.
Показатель патентной чистоты характеризует возможность реализации изделия в России и за рубежом.
При оценке патентной чистоты учитывается, что:
1) конструкция изделия не должна содержать технических решений, подпадающих под действие патентов и свидетельств исключительного права на изобретения зарубежных стран;
2) в нее не должны входить полезные модели, промышленные образцы и товарные знаки, зарегистрированные в странах, по отношению которых определяют патентную чистоту изделия;
3) изделие, выпускаемое для реализации только внутри страны, не должно нарушать действующие патенты исключительного права, выданные в России (зарубежные патенты, выданные только в России);
4) изделия, которые могут стать объектами экспорта, не должны нарушать действующие патенты третьих лиц, выданные в предполагаемых странах экспорта.
Эргономические показатели характеризуют систему «человек - изделие» (или «человек - машина») с позиций человека, как бы дают ей «человеческое измерение» (рис. 10.1). Они устанавливают соответствие свойств изделия (машины) тем или иным свойствам человека. Эргономические показатели охватывают всю область факторов, которые влияют на работающего человека, и используемое (эксплуатируемое) им изделие.
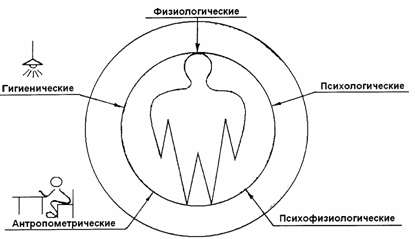
Рис. 10.1. Структура эргономических показателей
В эту группу входят следующие подгруппы показателей:
- антропометрические;
- гигиенические;
- физиологические и психофизиологические;
- психологические.
Антропометрические показатели определяют соответствие изделия (машины) размерам, форме и весу тела человека.
В эту подгруппу входят показатели соответствия:
- конструкции изделия размерам человека;
- конструкции изделия форме тела, человека и его отдельных частей, входящих в контакт с изделием;
- конструкции изделия распределению веса человека.
Выполнение требований этих показателей качества обеспечивает работающему (пользующемуся изделием) человеку рациональную и удобную позу, правильную осанку и т.д.
Гигиенические показатели определяют соответствие изделия (машины) гигиеническим условиям жизнедеятельности и работоспособности человека. В результате такого соответствия на рабочем месте (при пользовании изделием) создаются комфортные условия.
К этой подгруппе относят показатели уровней:
- освещенности;
- температуры;
- влажности;
- давления;
- запыленности;
- токсичности;
- шума;
- вибрации;
- перезагрузок (ускорений);
- напряженности магнитного и электрического полей.
Физиологические и психофизиологические показатели характеризуют соответствие изделия (всей системы «человек - машина» физиологическим свойствам человека и особенностям функционирования его органов чувств).
В подгруппу входят показатели соответствия конструкции изделия(размеры, формы, яркости, контраста цвета и пространственного положения) зрительным возможностям человека и т.д.
Психологические показатели характеризуют соответствие изделия психологическим возможностям человека.
Эстетические показатели характеризуют информационную выразительность, рациональность формы, целостность композиции, совершенство производственного исполнения.
Эта группа включает следующие подгруппы показателей:
- информационной выразительности;
- рациональности формы;
- целостности композиции;
- совершенства производственного исполнения и стабильности товарного вида.
Показатели информационной выразительности определяют способность изделия выражать своей формой эстетическое представление и культурные нормы, сложившиеся в обществе.
В эту подгруппу входят показатели:
- знаковости, оригинальности;
- стилевого соответствия;
- соответствия моде.
Показатели рациональности формы определяют соответствие формы изделия объективным условиям его изготовления и эксплуатации, а также выраженность в форме функционально-конструктивной сущности изделия.
В эту подгруппу входят показатели:
- функционально-конструктивной обусловленности;
- эргономической обусловленности.
Показатели целостности композиции определяют единство частей и целого, эффективность использования профессионально-художественных средств для создания полноценного композиционного решения, органичную взаимосвязь элементов формы изделия и его согласованности с ансамблем других изделий. Сюда входят показатели:
- организованности объемно-пространственной структуры;
- тектоничности (tektonikos (греч.)- относящийся к строительству);
- пластичности;
- упорядоченности и выразительности графических и изобразительных элементов;
- колорита и декоративности.
Показатели совершенство производственного исполнения и стабильности товарного вида определяют эстетическое восприятие формы изделия.
В эту подгруппу входят показатели:
- тщательности покрытия и отделки поверхностей;
- четкости исполнения фирменных знаков, указателей, упаковки и сопроводительной документации;
- устойчивости к повреждениям поверхности изделия.
Показатели транспортабельности характеризуют приспособленность продукции к перемещениям в пространстве (транспортированию), не сопровождающимся ее использованием или потреблением. Эти показатели следует выбирать с учетом конкретного вида транспорта (а иногда и конкретной разновидности транспортного средства). Основные показатели транспортабельности определяют затраты (трудовые и материальные) на операции по подготовке к транспортированию, непосредственно транспортные и завершающие весь цикл транспортирования.
К числу основных показателей транспортабельности относятся:
- средняя трудоемкость подготовки единицы продукции к транспортированию (включая погрузку и крепление);
- средняя стоимость упаковки продукции в определенную тару;
- средняя стоимость перевозки единицы продукции на 1 км пути определенным транспортным средством;
- средняя продолжительность разгрузки продукции и т.д.
Показатели безопасности характеризуют свойства продукции, обуславливающие безопасность человека (обслуживающего персонала) при потреблении или использовании продукции.
К таким показателям относят:
- вероятность безопасной работы человека в течение определенного времени;
- время срабатывания защитных устройств;
- сопротивление изоляции токоведущих частей;
- электрическую прочность высоковольтных цепей.
Экологические показатели характеризуют уровень вредных воздействий на окружающую среду, возникающих (сопутствующих) при потреблении продукции или её эксплуатации [2].
К этой группе относят следующие показатели:
- содержание вредных примесей в составе продукции и её отходах (выбросах);
- вероятность выбросов вредных частиц, газов, излучений при производстве, хранении, транспортировании, потреблении и эксплуатации продукции. Роль этой группы показателей качества продукции в настоящее время многократно возросла. Для многих видов продукции и технологий эта группа показателей стала приоритетной при определении их качества. Поставлена и решается задача создания безотходных технологий и экологически чистой продукции.
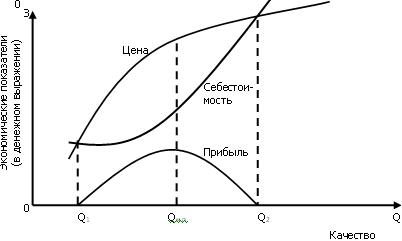
Рис.10.2. Зависимость цены и себестоимости от качества продукции
Особую группу составляют экономические показатели качества, исключительная ценность которых в универсальности, т.е. применимости к любому виду продукции (услуги), а также в том, что они определяют (раскрывают) связь качества продукции (услуги), себестоимости (цены производства) и цены (рыночной цены). Качество продукции (услуги), её потребительские свойства во многом определяют как цену производства (и себестоимость), так и рыночную цену (цену). Повышение качества продукции (услуги) требует дополнительных затрат (издержек производства), что приводит к росту себестоимости (цены производства). Повышенный спрос на продукцию (услугу) высокого качества приводит к росту цен (рыночных цен). Однако увеличение себестоимости и цены с повышением качества происходит по-разному (рис. 10.2). Повышение качества продукции означает появление у нее (за счет внесения новшеств на всех этапах жизненного цикла) свойств, которые удовлетворяли бы все большее число потребностей, обеспечивали их интеграцию и дифференциацию. В этом процессе повышения качества продукции с позиции экономических показателей можно выделить характерный цикл. За исходную точку этого цикла выбрано такое состояние, когда цена и себестоимость равны (на рис. 10.2 Q=Q
) и выпуск такой продукции экономически невыгоден, нерентабелен, так как не приносит прибыли. Для повышения рентабельности производства (получения прибыли) необходимо повышать качество продукции, чтобы создать повышенный спрос.
На рис. 10.2 качество продукции в относительных единицах откладывается по оси абсцисс, а цена и себестоимость в денежном выражении – по оси ординат. На участке 
повышение качества приводит к более быстрому росту цены, чем себестоимости, за счет этого прибыль растет и достигает максимального значения при 
. Дальнейший рост качества продукции (участок 
=
) ведет к уменьшению прибыли за счет того, что себестоимость растет быстрее, чем цена.
К экономическим показателям качества относят затраты на разработку, изготовление и испытания опытных образцов, себестоимость изготовления продукции, затраты на расходные материалы при эксплуатации технических объектов. При оценке экономического эффекта (экономической эффективности) от повышения качества продукции производят всесторонний учет экономических показателей на всех этапах жизненного цикла изделия (продукции).
10.2. Методы оценки уровня качества изделия
Под уровнем качества изделия понимается относительная характеристика качества, основанная на сравнении совокупности показателей качества изделия с соответствующей совокупностью базовых показателей.
Выявление относительных показателей качества и оценки уровня качества изделия проводится путем сопоставления показателей качества этого изделия с базовыми показателями, в числе которых используются показатели перспективных образцов, аналогов и стандартов.
Под перспективным образцом понимают изделие, совокупность показателей которого соответствует прогнозируемому экономически рациональному на определенный период уровню качества изделий данного вида.
Базовые показатели качества перспективного образца должны соответствовать показателям, наиболее полно учитывающим достижения науки, техники и требования потребителя.
При определении базовых показателей качества перспективного образца следует учитывать перспективу научно-технического прогресса в данной отрасли производства (с учетом прогнозирования их величин), ожидаемого изменения потребностей, выполнения технико-эконо-мических расчетов.
Экономически рациональный уровень качества перспективного образца определяется таким образам, чтобы этот образец «морально» не устарел к моменту освоения изделия в сфере потребления.
Под аналогом подразумевается изделие отечественного или зарубежного производства того же вида, конструктивного устройства, принципа действия, функционального назначения, масштабов производства и условий применения, что и сравниваемое изделие.
В качестве аналога в общем случае рекомендуется выбирать объект серийного или массового производства в количестве, как правило, не менее одного отечественного и одного зарубежного образца. Аналоги должны отражать передовые достижения науки и техники.
В отдельных случаях, когда в качестве аналога нельзя выбрать готовое изделие, используют данные доступных источников информации, например, аналога, составных частей изделия и т.п.
Количественная оценка уровня качества изделия производится с целью определения эффективности выполняемой или выполненной разработки и наилучших способов воздействия на процессы разработки, производства и эксплуатации изделия при управлении качеством продукции.
Полученные качественные оценки изделия сопоставляют с базовыми, делают выводы о целесообразности их изменения.
Уровень качества изделия (
- относительный показатель качества) должен рассматриваться в допустимых пределах:
,
где
- определяется в результате сопоставления требований потребителя с текущими технологическими и производственными возможностями реализации их производителем;
- верхний уровень качества, соответствующий уровню качества перспективного образца.
Оценка уровня качества конкретного изделия в зависимости от цели оценки и условий использования результатов может проводиться дифференциальным, комплексным или смешанным методом.
Оценка дифференциальным методом производится для выявления отдельных показателей.
Относительные показатели качества (
) определяются путем сопоставления частных показателей качества изделия (
) с единичными базовыми показателями качества (
) перспективного образца или аналога:
, (10.11)
где i – порядковый номер показателя.
Например, производительность перспективного образца (базовый показатель) СХМ
Q = 14 кг/с;
базовые показатели аналога Q=8 кг/с;
производительность проектируемой СХМ Q = 10 кг/с.
- относительный показатель i-го показателя качества. По сравнению с перспективным образцом;
- относительный показатель i-го показателя качества по сравнению с аналогом.
Оценка комплексным методом проводится тогда, когда уровень качества изделия необходимо охарактеризовать одним или несколькими обобщенными показателями.
Оценка смешанным методом проводится в случаях, когда расчеты не позволяют получить одновременно и обобщающие выводы, и выводы относительно отдельных групп показателей или отдельных показателей качества изделия.
Методы определения показателей качества изделия зависят от стадии его разработки, т.е. степени реализации технологических решений, при этом применяют приближенные, уточненные или окончательные методы определения показателей.
На исходных стадиях разработки проводят ориентировочные расчеты, показатели качества определяют укрупненно, с определённой степенью приближения.
На промежуточных стадиях разработки, на которых принимаются окончательные технические решения, производят оценку качества по уточненным методам.
На стадии внедрения в производство нового изделия определяют его фактические показатели по результатам его изготовления и испытаний, используя для этого методы окончательных расчетов.
В зависимости от используемых средств на той или иной стадии разработки различают следующие методы определения значений показателей качества изделий.
Экспериментальный (измерительный метод) базируется на информации, получаемой с использованием средств измерений и контроля. С помощью этого получают значения таких показателей качества, как масса изделия, сила, скорость, частота вращения и др.
Регистрационный метод осуществляется на основе наблюдений подсчета числа определенных событий, предметов или затрат, например подсчета отказов изделия при испытаниях, числа дефектных изделий в партии.
Расчетный метод действует на основе использования теоретических и эмпирических зависимостей показателей качества машины от её параметров. Применяется в основном при проектировании продукции. Позволяет установить зависимости между отдельными показателями качества. Служит для определения массы изделия, показателей его производительности (и др.).
Органолептический метод связан с анализом восприятия органов человека, например, при контроле окраски машины, при проверке дефектов обработанной поверхности и т.п. При его реализации возможно применение технических средств (лупа, микроскоп и т.п.), повышающих восприимчивость и разрешающие способности органов чувств.
Экспертный метод работает на основе решения, принимаемого экспертами, например, при оценке эстетической характеристики машины, её основных показателей.
Социологический метод осуществляется на основе сбора и анализа мнений фактических или возможных потребителей продукции.
При оценке качества продукции применяют обычно сочетание нескольких методов, используемых также при техническом контроле продукции в производстве.
Экспертный метод оценки качества осуществляется экспертной группой высококлассных специалистов, которые оценивают общее качество изделия или его отдельные параметры по балльной системе.
10.3. Стандарты ISO серии 9000
В 1987 году Техническим комитетом Международной организации по стандартизации ISO ТК-176 «Управление качеством и обеспечение качества» опубликована серия стандартов по Системам качества организаций (серии 9000), включающая следующие стандарты [6]:
- ISO 9000 «Общее руководство качеством и стандарты по обеспечению качества. Руководящие указания по выбору и применению»;
- ISO 9001 «Система качества. Модель для обеспечения качества при проектировании и/или разработке, монтаже и обслуживании»;
- ISO 9002 «Системы качества. Модель для обеспечения качества при производстве и монтаже»;
- ISO 9003 «Системы качества. Модель для обеспечения качества при окончательном контроле и испытаниях»;
- ISO 9004 «Общее руководство качеством и элементы Системы качества. Руководящие указания».
За год до этого ISO ТК-176 опубликовал трехъязычный словарь терминов и их определений в области управления и обеспечения качества – стандарт ISO 8402-86, который также явился составной частью стандартов ISO серии 9000.
Основными целями выпуска стандартов ISO серии 9000 являлись:
- укрепление взаимопонимания и доверия между поставщиками и потребителями продукции из разных стран мира при заключении контрактов;
- достижение взаимного признания сертификатов на Системы качества, выдаваемых аккредитованными органами по сертификации из разных стран мира на основе использования ими единых подходов и единых стандартов при проведении сертификационных проверок (аудитов);
- оказание содействия и методической помощи организациям различных масштабов из различных сфер деятельности в создании эффективно функционирующих Систем качества.
Как видно из названия стандартов, Системы качества организаций могут охватывать все этапы жизненного цикла продукции: от разработки до технического обслуживания её в условиях эксплуатации (стандарт ISO 9001) -либо только их часть, например окончательный контроль готовой продукции (ISO 9003). Выбор модели Системы качества должен при этом осуществляться на основе рекомендации стандарта ISO 9000. К критериям, которые должны учитываться при выборе одной из трех моделей для Системы качества, приведенных в стандартах ISO серии 9000, относятся, например, наличие и уровень сложности процессов проектирования (разработки) продукции, сложившаяся на предприятии производственная структура, технология и организация производства, специфические особенности продукции, экономические факторы и т.п.
Стандарт ISO 9004 является для организаций своеобразным методическим пособием по разработке и применению Систем качества. Стандарт содержит рекомендуемую структуру Системы качества, характеристики функциональных основных элементов Системы, определенные требования к организационной структуре, составу и содержанию данных, которые должны или могут применяться в Системе. В стандарте рассмотрены экономические аспекты качества, различные виды расходов и статьи затрат на качество, приведены указания по проведению внутренних проверок (аудитов) качества, позволяющих руководству организаций оценить степень готовности своих подразделений к стабильной поставке продукции, отвечающей требованиям спецификаций, стандартов и ожиданиям потребителей. Стандарт ISO 9004 применим, прежде всего, для решения задач в области внутреннего обеспечения качества и не должен использоваться в контрактных ситуациях или для целей сертификации.
Для контрактных ситуаций, а также для целей сертификации в стандартах ISO серии 9000 предусмотрено применение трех базовых моделей систем качества, требования, к которым регламентированы в стандартах ISO серии 9001, 9002 и 9003.
ISO 9001 является наиболее полным из трех стандартов, регламентирующих базовые модели Систем качества, и охватывает всю деятельность компании, рассматривая процессы обеспечения качества продукции от её разработки до эксплуатации. Важно отметить, что в стандарте нет специальных упоминаний о деятельности компании по идентификации продукции, определенного продукта, удовлетворенности потребителя, в общем, всего того, что является деятельностью по маркетингу. ISO 9001 представляет базовую модель Системы для обеспечения качества при проектировании (или улучшении продукта), производстве, установке (монтаже) продукции, сервисном обслуживании при её эксплуатации у потребителя. Поэтому этот стандарт применяют при проверках и сертификации той организации, которая имеет как производственные, так и разрабатывающие подразделения.
ISO 9002 учитывает лишь процессы производства и испытания продукции и представляет Систему качества как модель для обеспечения качества при производстве продукции и последующей её установке у потребителя.
ISO 9003 рассматривает только испытания готовой продукции и представляет Систему качества как модель для обеспечения качества окончательного контроля и испытаний готовой продукции.
Таким образом, ISO 9001, как наиболее всеобъемлющий, включает в себя стандарт ISO 9002, который, в свою очередь, включает ISO 9003; регулирование взаимоотношений между потребителем и поставщиком с помощью пяти стандартов ISO 9000 демонстрируется на рис.10.3.
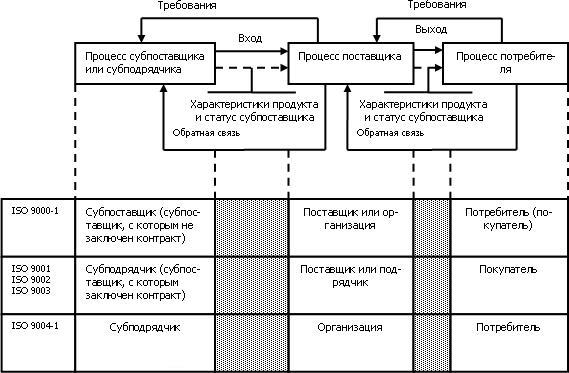
Рис. 10.3. Цепочка взаимосвязей потребителя и поставщика, предусмотренных стандартом ISO 9000
Процесс поставщика на рис.10.3 – это процесс рассматриваемой нами компании, продукт которой выходит на конечного потребителя и которая имеет с ним конкретные обязательства. Поэтому такая компания (в соответствии с названием, приведенным в стандартах ISO) именуется «поставщиком» или «подрядчиком».
В то же время под «организацией» понимается компания, которая пока не имеет контрактных отношений с потребителем. Аналогично поставщики подразделяются на субпоставщиков, которые не имеют с компанией контрактных отношений, и субподрядчиков, имеющих с ней контрактные отношения на поставку необходимых компании субпродуктов. Как видно из рис.10.3, стандарты серий 9001, 9002, 9003 применяются для уточнения контрактных взаимоотношений между потребителем и изготовителем на любом уровне (субподрядчик – поставщик, поставщик – потребитель).
Выполнение требований одного из стандартов ISO 9001, 9002 и 9003 является обязательным условием при сертификации Системы качества организации в зависимости от состава заявленной модели обеспечения качества (проектирование, производство, установка и сервисная поддержка, окончательный контроль и испытание готовой продукции).
Квалификация стандартов ISO серии 9000 может быть представлена в виде трех отдельных групп стандартов этой серии, каждая из которых имеет свое предназначение.
Первая (основная) группа стандартов ISO серии 9001, именуемая группой основных стандартов (рис. 10.4), включает четыре стандарта ISO (9001, 9002, 9003, 9004), регулирующих как контрактные, так и не контрактные ситуации.
Внутренняя проверка качества. Организация осуществляет всестороннюю проверку своей деятельности с целью определения эффективности Системы качества и ее соответствия требованиям выбранного стандарта из серии ISO 9000. Проверка должна носить форму запланированного аудита в различных областях в зависимости от состояния и степени важности операций и действий. Проверки проводятся обученным персоналом в соответствии с документально оформленными процедурами. Результаты проверок документально оформляются и доводятся до сведения руководства для осуществления своевременных корректирующих действий и устранения недостатков, выявленных в процессе проверки. Частота проверок определяется на основе опыта, а также важности производимой продукции. В одной и той же области проверки проводятся не реже одного раза в год и выполняются согласно плану, в котором точно определены место и время, квалификация аудиторов, требования к готовой продукции, методы проведения проверок, порядок приемки результатов. Проверки должны проводиться независимым, специально обученным и подготовленным персоналом.
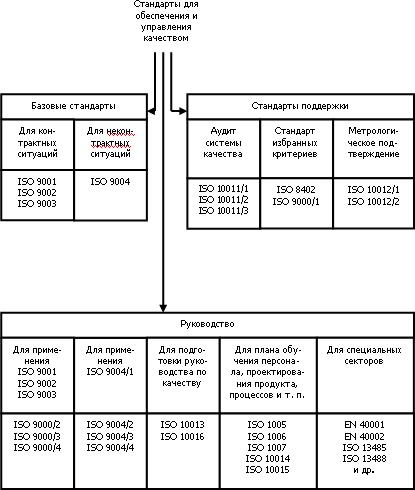
Рис. 10.4. Архитектура семейства стандартов ISO серии 9000
Подготовка кадров. Должна быть предусмотрена специальная подготовка персонала, чья деятельность влияет на качество продукции. Персонал должен быть обучен специфическим задачам, после обучения выдаются соответствующие документы. План обучения должен быть тесно связан с актуальными для организации задачами. Результаты подготовки и обучения персонала должны регистрироваться.
Техническое обслуживание. Исходя из заявленной политики качества и контрактов с потребителями, организация должна гарантировать услуги, уровень которых определен в плане по качеству. Все действия должны полностью соответствовать контрактам и гарантиям поставщика. Организация должна разработать план, процедуры, формы обучения и методы контроля для обеспечения принятого уровня услуг.
Статистические методы. Этот параграф стандарта говорит о том, что поставщик устанавливает адекватные статистические методы для подтверждения приемлемости возможностей процесса и характеристик продукции.
В случае необходимости поставщик должен разработать процедуры, обеспечивающие выбор статистических методов, необходимых для проверки возможности технологического процесса и приемлемости характеристик продукции. Область применения и планы статистических методов контроля устанавливает изготовитель. В необходимых случаях он согласовывает их с потребителем или заказчиком. Следует отметить, что в России основными документами для организации и применения статистических методов контроля являются:
а) для приемочного контроля: ГОСТ 18242-72; 20736-75; 18321-73; 24660-81; 16493-70; СТ СЭВ293-76; РД50-605-86; Р60-110-89;
б) для статистического регулирования технологических процессов «Рекомендации по статистическому регулированию технологических процессов» (М.:ВНИИС,1988).
В общем случае эффективность применения статистических методов следует рассчитывать в соответствии с «Методикой оценки экономической эффективности внедрения статистических методов контроля качества продукции» (М.: Изд-во стандартов, 1976).
Для сертификации на соответствие выбранному стандарту ISO серии 9000 в организации, подлежащей сертификации, должна быть спроектирована и должна функционировать Система качества, основным назначением которой является удовлетворение запросов потребителей. Соответствие функционирующей Системы качества требованиям выбранного стандарта ISO 9000 позволит организации достигать ожидаемого потребителем уровня качества (при оптимальных затратах)и поддерживать его.
Эффективная Система качества должна быть спроектирована и должна функционировать так, чтобы удовлетворялись запросы и ожидания как внешних потребителей, так и самой организации. Удовлетворенность запросов и ожиданий потребителей обеспечивается достижением и постоянным поддержанием установленного потребителями уровня качества. Удовлетворенность интересов и запросов организации достигается эффективностью использования имеющихся у нее ресурсов.
Необходимым условием результативности функционирования Системы качества является эффективный контроль за всеми техническими, административными и человеческими факторами, влияющими на качество выпускаемой продукции: технические средства, программные средства, перерабатываемые материалы или услуги. Такой контроль должен быть направлен на сокращение, устранение и, что наиболее важно, предотвращение несоответствий. Специфика требований к качеству продукции, производственным условиям, накопленным традициям и опыту решения задач объективно предопределяет различия в составе, структуре и содержании функций Систем качества различных организаций. Разработка и совершенствование Систем качества – творческая функция, требующая от организации иногда достаточно высоких затрат ресурсов, компетентных исполнителей, обязательного участия в этой работе высшего руководства предприятия.
В соответствии с идеологией стандартов семейства ISO 9000 можно выделить четыре следующих направления деятельности в области качества, посредством которых Система качества воздействует на процесс формирования качества продукции и услуг на различных этапах их жизненного цикла: планирование, управление, обеспечение и улучшение качества. Каждое направление деятельности имеет свои специфические особенности, носит интеграционный характер и представляет собой четыре основные функциональные подсистемы Системы качества.
Планирование качества включает в себя деятельность по установке целей и требований элементов Системы качества. Планирование качества процессов охватывает подготовку программы качества, выработку положений по улучшению качества, подготовку применения Системы качества, включающей составление календарных графиков ее ввода в действие и применение.
Управление качеством включает в себя методы и виды деятельности оперативного характера, используемые для выполнения требований к качеству. В состав процедур управления качеством входят контроль качества, разработка и реализация мер корректирующего воздействия. Основное назначение подсистемы управления качеством на предприятии – выявлять каждое отклонение от установленных требований к качеству продукции и услугам, применять решения по дальнейшему использованию продукции, имеющей отклонения или дефекты, не допускать появления повторных отклонений или дефектов за счет своевременной разработки и реализации мер корректирующего воздействия.
Обеспечение качества включает в себя все планируемые и систематически осуществляемые виды деятельности в рамках Системы качества, необходимые для создания и подтверждения достаточной уверенности в том, что объект (продукция, процесс или услуга) удовлетворяет требованиям качеству.
Различают внутреннее обеспечение качества – деятельность по созданию уверенности в выполнении требований к качеству продукции и услуг у руководства предприятия-поставщика и внешнее обеспечение качества – деятельность по созданию уверенности у потребителя или у других лиц (экспертов-аудиторов по сертификации Систем качества, государственных инспекторов по качеству и т.п.). В состав процедур обеспечения качества входят, прежде всего, процедуры внутренних проверок элементов Систем качества (внутреннего аудита качества), а также другие предупреждающие действия, предусмотренные в стандартах ISO серии 9000 или разработанные по инициативе поставщика исходя из специфики своей продукции и (или) производственных процессов. Основное назначение процедур обеспечения качества – предупреждать все возможные отклонения от установленных требований.
Улучшение качества включает в себя все мероприятия, осуществляемые в организациях в целях повышения эффективности и результативности деятельности и процессов для получения выгоды как для организации, так и для ее потребителей. Постоянной целью руководителей и исполнительного персонала организации должно быть стремление добиться непрерывного улучшения качества, что принесет пользу потребителям, самой организации, ее работникам и обществу в целом. В этом состоит один из основополагающих принципов стандартов ISO серии 9000.
По оценке Системы качества (п.4.2, ISO 9000), Система качества компании реализуется при помощи процессов, существующих как внутри, так и вне функционирования компании (рис. 10.5). На рис. 10.5,б показана основополагающая роль в этих процессах Системы качества, представляющей собой совокупность организационной структуры, методик, процессов и ресурсов, необходимых для осуществления общего руководства над качеством.
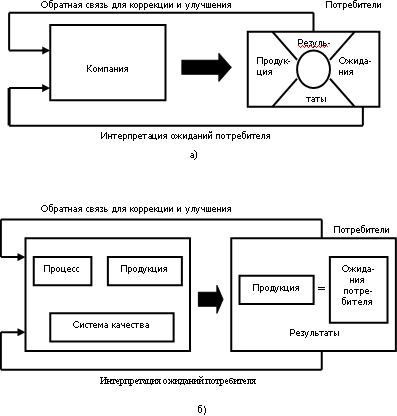
Рис. 10.5. Схема взаимодействия компании и потребителя (а)
и роль системы качества в удовлетворении ожиданий потребителя (б)
Для эффективности Системы качества необходима согласованность и совместимость процессов планирования, управления, обеспечения и улучшения качества с определением их интерфейсов. Система качества – это не только совокупность согласованных процессов, в которые она интегрирована.
При оценке Системы качества рассматриваются три основных вопроса (подход, развертывание и результат):
- определены ли процессы и документированы ли все их процедуры соответствующим образом (подход);
- полностью ли процессы развернуты, выполнены и документированы (развертывание);
- являются ли процессы эффективными для достижения желаемых результатов (результат).
Доказательством адекватности и эффективности Системы качества являются обязательностью поставщика.
Методы, показывающие соответствие Системы качества выбранной модели обеспечения качества, могут быть следующие:
- предоставление поставщиком декларации о соответствии;
- предоставление документированного доказательства;
- предоставление утверждений или регистрации потребителями;
- аудит потребителя (второго лица);
- аудит третьего лица (внешнего эксперта-аудитора);
- предоставление сертификатов компетентного третьего лица, Любой из этих методов можно использовать при контрактных ситуациях между первыми (поставщик/подрядчик) и вторыми (потребитель/покупатель) лицами; при утверждении или регистрации вторыми лицами.
Последние два метода применимы только при сертификации или регистрации третьими лицами.
Прежде чем начать процесс сертификации, Система качества компании должна быть документирована адекватно требованиям ISO 9001,9002 и 9003. Документация Системы качества должна обеспечивать полную информацию с подробным описанием системы и последовательности выполняемых работ, а также содержать информацию, следуя которой можно четко воспроизвести всю деятельность компании.
Описание и документирование Системы качества выполняются на четырех уровнях (рис. 10.6). Рассмотрим подробнее каждый из этих уровней документированной Системы качества.
Руководство по качеству – 1-й уровень документации Системы качества, который должен включать разделы, адресованные каждому параграфу выбранного поставщиком стандарта (ISO 9001,9002 или 9003). При этом нет необходимости в деталировке содержания. Аудитор, который проверяет наличие Руководства по качеству, обращает основное внимание на то, чтобы оно соответствовало всем параграфам выбранного поставщиком стандарта ISO. Как каждое подразделение адресуется соответствующему параграфу, покажут документы последующих уровней. Основным назначением Руководства по качеству является общее описание Системы и применяемых в ней методов планирования, управления, обеспечения и улучшения качества.
На практике часты случаи, когда сертификации компании в целом предшествует сертификация ее подразделений, которые в этом случае составляют свое руководство по качеству с ориентацией на общее руководство по качеству компании.
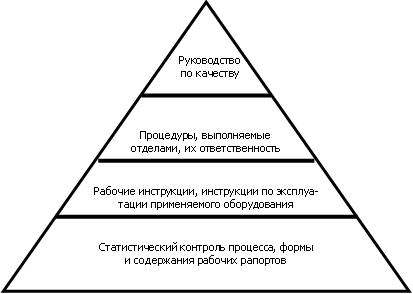
Рис. 10.6. Демонстрация четырех уровней Системы качества
Руководство по качеству выполняет функцию постоянного справочного материала при внедрении Системы качества, поддержания её в рабочем состоянии и совершенствовании. Как правило при проведении сертификации аудиторы в первую очередь знакомятся с Руководством по качеству, и если оно отсутствует, то дальнейшая работа по сертификации прекращается.
На крупных предприятиях может быть иерархия документов вида руководств по качеству:
- общее руководство по качеству;
- руководство по качеству для различных производств(по видам продукции);
- руководство по качеству для различных подразделений;
- руководство по качеству для различных этапов «петли качества» и связанных с ней функций, таких, как проектирование продукции, материально-техническое снабжение и др.
Порядок построения руководств по качеству носит необязательный характер и зависит от потребностей пользователя. В соответствии с Международным стандартом ISO 10013 «Руководящие указания по разработке руководств по качеству», в состав руководства по качеству рекомендуется включать следующие разделы:
- наименование, область деятельности и сферу применения;
- оглавление;
- вводную часть о соответствующей организации и самом руководстве по качеству;
- политику в области качества и задачи организации;
- описание организации, ответственности и полномочий;
- описание элементов Системы качества и (или) ссылки на процедуры Системы качества;
- определения, если в этом есть необходимость;
- путеводитель по руководству по качеству, если это уместно;
- приложения с дополнительной информацией, если это целесообразно.
Документ «Политика качества» содержит как цели, которые компания желает достичь, так и обязательства компании. Перед составлением такого документа важно все пункты обсудить с высшим уровнем руководства. Политика качества – это отправная точка для программы управления качеством компании. Это означает, что компания должна быть готова выполнять свои обязательства.
Политика качества – это дело как исполнителей, так и руководителей высшего уровня, включая правление компании (совет директоров). Наилучшая стратегия – применить программу обучения каждого члена коллектива (от главы правления до исполнителей самого низшего уровня); обучить деталям политики, применению и особенностям рабочих задач. Этот подпараграф требует от поставщика гарантии, что политика понятна, выполнена и поддержана на всех уровнях организации.
Система качества создается и внедряется на предприятии как средство, обеспечивающее проведение определенной политики и достижение поставленных целей в области качества.
Таким образом, первичными являются формирование и документальное оформление руководством организации политики в области качества. Она должна отражать основные направления, цели и задачи организации в области качества. Данное положение является принципиальным, так как в политике прежде всего отражается компетентность организации в вопросах качества.
По политике в области качества потребитель может составить представление об отношениях к его запросам и потребностям. Поэтому не случайно многие фирмы-потребители при оценке систем обеспечения качества предприятия-поставщика первостепенное значение придают наличию сформулированной политики в области качества.
Политика в области качества должна быть документально оформлена либо в виде самостоятельного документа, либо зафиксирована в других документах Системы (Общее руководство по качеству, Основной стандарт предприятия по Системам качества, Программа качества и др.).
Процедуры, выполняемые подразделениями и ответственность – 2-й уровень Системам качества, представляющей собой документ, описывающий общие процедуры (т.е. без поименного указания на исполнителей), которые могут сопровождаться структурной схемой подразделения с распределением функциональных обязанностей в нем. Документ описывает для каждого отдела процедуры и обязанности. Это очень полезно, так как позволяет внутренним заказчикам (поставщикам) увидеть обязанности друг друга. Документ должен быть организован в соответствии со следующей схемой:
- что? (функции отдела);
- кто? (организация отдела и обязанности, ответственность, функции и роль каждого);
- как? (ссылка на операционную инструкцию, где объяснено, как изделия должны быть сделаны);
- с кем? (кто является внутренним и/или внешним поставщиком и заказчиком отдела ).
Рабочие инструкции и инструкции по эксплуатации применяемого оборудования – 3-й уровень, представляющий собой документацию Системы качества в виде операционных инструкций.
Этот документ касается операционных или рабочих инструкций. Они описывают шаг за шагом, как может быть выполнена конкретная простая операция производства, сборка, установка оборудования, поддержание его в рабочем состоянии и т.п.; как может быть проконтролировано качество, какие средства могут быть использованы, какое измерительное оборудование может быть применено и т.п.
Статистический контроль процесса, формы и содержания рабочих рапортов – 4-й уровень, представляющий собой документ в виде формы статистического контроля процесса и различных отчетов в области качества.
Эти формы и связанные с ними инструктивные документы (как собирать информацию, как заполнять эту информацию в формы, как ее использовать, какие средства контроля качества могут быть использованы, как вносить поправки и т.п.) являются основной формой контроля за оперативными действиями.
Что касается п.4.1 ISO 9000 «Ответственность руководства», то в соответствии со стандартами ISO ответственность за качество несет либо руководитель фирмы, либо его представитель, наделенный необходимыми полномочиями и подчиняющийся непосредственно руководителю фирмы. Эта обязанность не может быть делегирована простому служащему фирмы, поэтому выполнение п. 4.1 подтверждается утвержденной структурой организации, в соответствии с которой была бы ясна иерархия подчиненности, ответственности и прав сотрудников организации.
10.4. Система управления качеством
Для разработки этой системы необходимо определить факторы, обеспечивающие качество машин.
Процесс формирования качества машин включает следующие работы [20]:
- изучение аналогов машин, данных по их эксплуатации и патентный поиск;
- проектирование и расчеты;
- унификацию, стандартизацию и отработку на технологичность;
- подбор покупных изделий;
- проведение исследовательских работ по качеству машин;
- доработку конструкции по результатам исследований;
- проектирование опытной технологии;
- разработку новых методов изготовления, направленных на повышение качества машин;
- проведение исследований по технологическому обеспечению качества машин;
- доработку опытной технологии;
- изготовление опытной партии машин;
- проведение стендовых или эксплуатационных испытаний;
- доработку «слабых звеньев, технологии их изготовления и ремонта;
- выделение изделий, подлежащих ремонту, определение срока их ремонта или восстановления;
- выдачу окончательного проекта машины оптимального качества;
- проектирование маршрутной технологии изготовления машины с учетом опытной технологии;
- расчет оптимальной цены машины с учетом ее качества;
- проектирование новых предприятий или модернизацию существующих для изготовления новой машины;
- проектирование маршрутной технологии ремонта и восстановления отдельных деталей и сборочных единиц машины;
- проектирование ремонтных предприятий под разработанные технологические процессы;
- разработку отраслевых руководящих материалов, направленных на обеспечение качества машин;
- проведение совместных работ с предприятиями по повышению качества машин.
Для обеспечения постоянного повышения качества выпускаемой продукции предприятие обязано:
- осуществлять диагностирование машин при эксплуатации и сбор статистических данных по их качеству;
- выявлять «слабые» звенья в процессе эксплуатации и проводить мероприятия, направленные на повышение качества машин;
- проводить дополнительные исследования, направленные на повышение качества;
- осуществлять механизацию и автоматизацию обработки, сборки и контроля;
- вводить конструктивные и технологические изменения по согласованию с проектными организациями;
- разрабатывать маршрутно-операционный технологический процесс изготовления машин на основе проектного маршрута и внесения изменений;
- выполнять перерасчет основной цены изделия с учетом повышения их качества;
- разрабатывать руководящие материалы, направленные на обеспечение и повышение качества машин;
- производить входной контроль комплектующих и покупных изделий;
- осуществлять контроль за состоянием оборудования и измерительными средствами, их профилактику, ремонт и своевременную замену;
- выполнять контроль за соблюдением технологической дисциплины;
- осуществлять стендовые испытания и конечный контроль;
- контролировать правильность эксплуатации машин.
Управление качеством продукции – это действия, осуществляемые при создании и эксплуатации или потреблении продукции в целях установления, обеспечения и поддержания необходимого уровня ее качества.
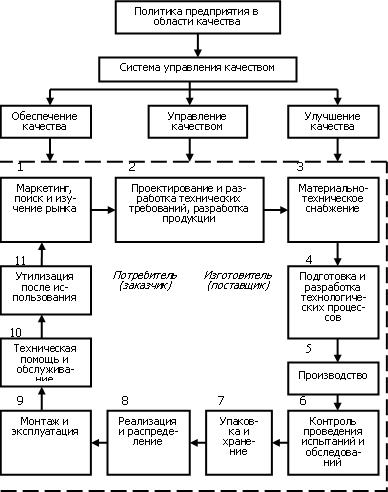
Рис. 10.7. Система качества промышленного предприятия
Система управления качеством – это совокупность управляющих органов и объектов управления, взаимодействующих с помощью материально-технических информационных средств при управлении качеством продукции (рис. 10.7) Она должна обеспечить качество конкретного изделия, и поэтому на одном и том же предприятии система может включать отдельные подсистемы по определенным видам изделий.
Система управления качеством должна охватывать все стадии жизненного цикла продукции.
В методологии управления качеством продукции рассматриваются четыре стадии жизненного цикла продукции: исследование и разработка; изготовление; обращение и реализация; эксплуатация и потребление.
В соответствии с ISO серия 9004 в жизненный цикл продукции («петля качества») входят следующие этапы [20]: 1- маркетинг, поиск и изучение рынка; 2- проектирование и (или) разработка технологических требований; 3- разработка продукции; 4- материально-техническое снабжение; 5- подготовка и разработка производственных процессов; 6- производство; 7- контроль и проведение испытаний и обследование; 8- упаковка и хранение; 9- реализация и распределение продукции; 10- монтаж, эксплуатация; 11- техническая помощь и обслуживание; 12- утилизация после использования (рис.10.8).
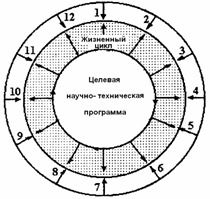
Рис. 10.8. Петля качества –
систематически проводимые
технологические мероприятия |
Обеспечение качества машин представляет собой совокупность планируемых и систематические проводимых, мероприятий, создающих необходимые условия для выполнения каждого этапа жизненного цикла таким образом, чтобы качество продукции удовлетворяло определенным требованиям (см. рис. 10.8). Применительно к машинам это значит, что проектирование и изготовление обеспечивается таким образом, чтобы все детали и соединения в целом изначально могли выполнять заданные функции.
Для планирования мероприятий по обеспечению качества целесообразно формировать целевые научно-технические программы повышения качества изделий. Программу разрабатывают на конкретную машину. Она должна содержать требования к техническому уровню и качеству создаваемой машины и к ресурсному обеспечению всех этапов жизненного цикла (например, требования к оборудованию, сырью, материалам, комплектующим изделиям, метрологическим средствам, необходимым для производства изделия нужного качества, производственному персоналу и т.д.). Кроме того перечень мероприятий на всех этапах жизненного цикла должен обеспечивать реализацию этих требований.
Порядок, правила и методы выполнения мероприятий программы определены документами системы обеспечения качества.
К систематически проводимым мероприятиям по обеспечению качества относятся те, которые выполняются предприятием постоянно или с определенной периодичностью, например, работа по изучению рынка, постоянное обучение персонала и т.д.
Особое место занимают мероприятия, связанные с предупреждением появления дефектов.
В соответствии ISO серии 9000 система управления качеством должна функционировать таким образом, чтобы предотвратить изготовление изделие низкого качества.
Мероприятиями по предупреждению несоответствий показателей качества требуемым могут быть: принудительная замена технологической оснастки и инструмента, планово-предупредительный ремонт оборудования, техническое обслуживание, обеспечение необходимой документацией всех рабочих мест, своевременное изъятие устаревшей документации и т.д.
Управлении качеством подразумевает собой управление процессами выявления различного рода несоответствий продукции в производстве или системе качества и устранение этих несоответствий, а также вызвавших их причин.
Пример управлении качеством – статистическое регулирование технологического процесса с помощью контрольных карт. Этот момент позволяет предупредить появление дефектов и поэтому предпочтительнее, чем методы, связанные с управлением качеством по уже появившимся дефектам.
В методологии Системы качества, применяемой в России, меры по выявлению и устранению отклонений и их причин известны как «замкнутый управленческий цикл», который включает контроль, учет, анализ (оценку) принятие и реализацию решения.
Решения могут применяться по результатам текущей информации, получаемой при контроле, учете и анализе, а также по результатам обработки анализа накапливаемой информации.
В общей Системе качества управление качеством предусматривается как необходимый принцип по отношению ко всем элементам системы качества во всех этапах жизненного цикла (рис. 10.9).
Улучшение качества продукции должно осуществляться постоянно посредством деятельности, направленной на повышение технического уровня машин, качество их изготовления, совершенствование элементов производства и системы качества.
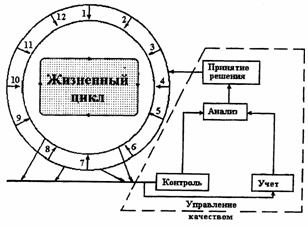
Рис. 10.9. Схема управления качеством
Объектом процесса улучшения качества может быть любой элемент производства или системы качества. Это направление деятельности связано с получением показателей выше, чем те, которые установлены нормами.
Постоянное улучшение качества прямо связано с тенденцией по повышению конкурентоспособности продукции. Такая продукция обладает высоким уровнем качества при более низкой цене. В связи с этим целью постоянного улучшения качества является либо улучшение параметров продукции, либо повышение стабильности качества изготовления, либо снижение издержек.
Развитие деятельности по улучшению качества требует специальной организации. Характерной организационной формой работы по улучшению качества являются группы качества (за рубежом - кружки качества).
Однако эта форма не является единственной. К ним можно отнести и организацию рационализаторской деятельности, и создание временных творческих коллективов (при этом в практике многих зарубежных фирм для решения определенных задач в такие коллективы входят и руководители фирм) для решения задач улучшения качества и т.д.
Соотношение трех направлений деятельности в системе управления качеством (обеспечение качества, управление качеством и улучшение качества) иллюстрирует рис. 10.10.
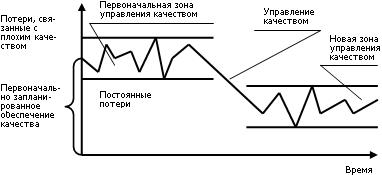
Рис. 10.10. Система мероприятий по обеспечению качества машин
Маркетинг должен играть ведущую роль в определении требований, предъявляемых к качеству машин. Его назначение – определять:
- потребности в машинах;
- рыночный спрос и область реализации, поскольку это важно для оценки сортности, нужного количества, стоимости и сроков производства машин;
- требования потребителя на основе постоянного анализа хозяйственных договоров, контактов или потребностей рынка (эти действия включают учет любых нужд или тенденций, проявляемых потребителями).
Кроме того, четко информировать предприятия обо всех требованиях предъявляемых потребителем.
Маркетинг должен обеспечивать предприятие подробным официальным отчетом или руководящими указаниями в соответствии с требованиями, предъявляемыми к изделию, например, кратким описанием машины. Краткое описание машины содержит требования и пожелания потребителя в виде предварительного перечня технических условий, которые послужат основой для выполнения последующих работ по проектированию. В числе элементов, включаемых в краткое описание машин, наряду с характеристиками самой машины, могут быть: схемы установки и монтажа; приемлемые стандарты и законодательные регламенты; упаковка; обеспечение и (или) проверка качества.
Маркетинг должен устанавливать на постоянной основе систему обратной связи и контроля получаемой информации. Всю информацию, относящуюся к качеству продукции, следует анализировать, сравнивать, интерпретировать и доводить до сведения производственных служб в соответствии с установленными процедурами. Подобная информация помогает определить характер и объем проблем, связанных с реализацией продукции, на основании опыта и пожеланий потребителя. Кроме того, обратная связь с потребителем может явиться средством получения данных, необходимых как для внесения возможных изменений в проект, так и для соответствующих действий руководства.
Система управления качеством в соответствии с нормативно-методическими документами должна предусматривать:
- обеспечение маркетинга всеми необходимыми ресурсами и надлежащими условиями;
- проведение мероприятий, предотвращающих ошибки в маркетинге;
- управление всеми условиями и факторами в маркетинге;
- постоянное улучшение работ по маркетингу.
Система управления качеством должна обеспечить создание проекта, отвечающего современным научно-техническим достижениям и требованиям потребителя. При наличии краткого описания машины, полученного в результате маркетинга, это краткое описание используется как исходные требования к проекту.
Система качества должна предусматривать:
- планирование работ по проектированию (например, в форме целевой научно-технической программы);
- комплекс мероприятий, направленных на предотвращение ошибок при проектировании, испытаниях и измерении параметров машин на различных этапах проектирования;
- проверку соответствия проекта исходным требованиям;
- периодический анализ всех компонентов проекта;
- анализ готовности потребителя к использованию машин;
- контроль за изменениями в проекте;
- последующие повторные оценки проекта.
Материалы, комплектующие детали и узлы, закупленные предприятием, становятся частью выпускаемой им машины и оказывают непосредственно влияние на конечное качество машины.
Предприятие несет ответственность за конечное качество машины в целом, независимо от качества закупленных им материалов, полуфабрикатов и комплектующих изделий.
С целью обеспечения качества поставок Система управления качеством как минимум должна включать следующие элементы:
- требования к покупным материалам, полуфабрикатам, комплектующим деталям и узлам;
- процедуры, методы и формы работы с поставщиками;
- входной контроль;
- процедуры согласования с поставщиками планов входного контроля;
- методы решения спорных вопросов по качеству покупной продукции и ведения претензионной работы;
- регистрацию данных о качестве покупных машин и оценку поставщиков.
Система управления качеством должна предусматривать обеспечения функции материально-технического снабжения всеми необходимыми ресурсами и условиями, контроль и управление ресурсами и условиями и постоянное их улучшение.
Уровень подготовки производства должен быть таким, чтобы технологический процесс и состояние всех элементов производства оборудования, материалов и комплектующих, технологической оснастки и инструмента, производственного персонала, вспомогательных материалов, технической документации, производственной среды обеспечивали изготовление машин в соответствии с требованиями технической документации.
Необходимо предусмотреть и обеспечить постоянно действующие или периодические мероприятия, направленные на предотвращение возникновения дефектов.
Система управления должна быть такой, чтобы все элементы производства контролировались и в случае необходимости приводились в надлежащее состояние. Особое внимание следует уделять производственным процессам, нормирующим параметры продукции, измерение которых связано с большими экономическими затратами или которые вообще не могут быть полностью проверены техническим контролем и путем испытаний.
Обязательными элементами системы управления должны быть контрольные испытания готовой машины, а также контроль и испытания в процессе производства. Там, где это затруднительно, необходимо применять статистические методы контроля.
Целесообразно осуществлять оценку качества изготовления машин на основе проверки машины, принятой отделом технического контроля (ОТК). Результаты такой оценки могут быть использованы для разработки корректирующих мероприятий, стимулирования подразделения отдельных работников за качество, целенаправленного планомерного улучшения качества изготовления.
Система управления качеством после производственных этапов должна обеспечивать требуемое качество машин при погрузочно-разгрузочных работах, хранении, транспортировании, монтаже. Должны быть предусмотрены необходимые ресурсы, условия и мероприятия, предотвращающие появление дефектов на непроизводственных этапах. Необходимо, чтобы все факторы, влияющие на качество изделий после производственных этапов, можно было проконтролировать и в случае необходимости на них воздействовать.
Целесообразно постоянно улучшать условия и выделять необходимые ресурсы после производственных этапов. Необходимо постоянно проводить технические консультации; обучать персонал, эксплуатирующий сложную технику; выполнять техническое обслуживание и ремонт изделий в период гарантийного срока, поставку запасных частей; снабжать персонал инструкциями по использованию, сборке, монтажу, вводу в эксплуатацию, обслуживанию и ремонту изделия. Система обратной связи по эксплуатационным характеристикам продукции должна обеспечивать контроль показателей качества используемой машины на протяжении всего срока службы и постоянный анализ соответствия качества машин потребностям потребителя, включая безопасность эксплуатации, воздействие на окружающую среду, надежность.
На стадии внедрения новых изделий целесообразно применять систему раннего обнаружения отказов или иных дефектов продукции с целью быстрого принятия корректирующих мер.
При развитии конкуренции и выходе предприятий на международный рынок, качество изделий и затраты, связанные с качеством, становятся важным фактором экономического положения предприятия и, в частности, такого показателя, как прибыль предприятия. Влияние качества на прибыль предприятия может проявляться следующим образом [3]:
- общий объем прибыли может увеличиваться (уменьшаться) вследствие расширения (сужения) рынка сбыта и объема реализации при улучшении (ухудшении) качества продукции; это экстенсивный путь повышения эффективности деятельности предприятия;
- объем прибыли может увеличиваться при снижении себестоимости продукции, полученной за счет уменьшения затрат, связанных с качеством продукции. Это интенсивный путь повышения эффективности деятельности предприятия.
В первом случае к затратам на качество относят все дополнительные расходы, связанные с повышением технического уровня продукции, снижением уровня дефектности продукции, улучшением и расширением услуг, что вызывается созданием более хороших условий эксплуатации продукции. Сюда следует относить затраты, связанные с рекламой продукции, сертификацией продукции, предоставлением потребителю доказательств эффективности системы управления качеством, демонстрационными испытаниями продукции с целью подтверждения ее качества.
Учет указанных затрат и сопоставление их с увеличением прибыли дают возможность оценивать экстенсивную эффективность системы управления качеством. Повышение эффективности деятельности предприятия в этом направлении прямо связано с развитием маркетинга.
Во втором случае затраты можно разделить на следующие группы:
1) вызванные появлением дефекта продукции. К ним относятся: исправимый брак; расходы на переработку и (или) исправление дефектных изделий, повторные контроль и испытание машин; затраты на возмещение прямого ущерба потребителю; затраты в связи с санкциями за поставку низкокачественной машины; потери в результате уменьшения цены на изделие более низкого качества; затраты на ремонт, представление запасных частей; затраты, связанные с исками о юридической ответственности за качество и др.;
2) связанные с выявлением дефектов и их причин, организацией технического контроля, испытаний машин, учетом и накоплением информации о качестве, анализом дефектов и их причин, корректирующими действиями по устранению дефектов и их причин. К этой группе затрат целесообразно относить все затраты на метрологическое обеспечение;
3) направленные на предупреждение появления дефектов. К ним относятся: затраты на планово-предупредительный ремонт и техническое обслуживание оборудования; издержки вследствие недоиспользования ресурса технологической оснастки и инструмента при принудительной их замене (если она применяется); расходы на повышение квалификации кадров и их обучение при изменении условий производства; расходы на поддержание параметров производственной среды, своевременное внесение изменений в техническую документацию и др.
Перечисленные затраты взаимосвязаны таким образом, что, увеличивая (уменьшая) одни затраты, можно соответственно уменьшать (увеличивать) другие затраты. Например, увеличивая объем затрат на профилактические мероприятия, можно добиться снижения потерь из-за дефектов и снижения расходов на контроль и испытания. Снижение затрат на профилактические мероприятия и контроль может привести к увеличению потерь, связанных с дефектами изделий.
Интенсивная эффективность системы управления качеством может проявляться в снижении себестоимости продукции благодаря минимизации суммарных затрат по всем трем группам. Для решения этой задачи целесообразно первоначально определить все потери, связанные с дефектами продукции, затем назначить мероприятия по предотвращению дефектов и регулированию контроля. Сопоставляя изменения затрат по трем группам, можно выбрать оптимальный вариант.
Экстенсивный и интенсивный эффекты взаимосвязаны между собой. Например, в определенных случаях предприятием может быть получен интенсивный максимальный эффект при увеличении количества проданных дефектных изделий. Однако со временем это может вызвать снижение спроса на изделия и, как следствие, - снижение объема реализации (т.е. экстенсивного эффекта качества) и общей прибыли предприятия. Учет затрат на улучшение качества требует упорядочения сбора первичной информации о дефектах, затратах на их устранение и взаимосвязан с бухгалтерским учетом.
Учет затрат на улучшение качества дает возможность руководству предприятия и подразделений принимать решения, связанные с качеством продукции и финансовым состоянием предприятия в целом.
Организационная структура системы управления качеством устанавливается в рамках организационной структуры управления предприятием в целом и представляет собой распределение руководства качеством.
Общее руководство качеством должно осуществляться руководством предприятия. Ответственность за деятельность, прямо или косвенно влияющую на качество, должна быть определена и документально зафиксирована. Ответственность за деятельность, влияющую на качество, может быть зафиксирована в документах двух видов:
- должностных инструкциях и положениях о подразделениях;
- документах, устанавливающих порядок выполнения функций и работ по качеству.
При этом первичными являются документы, устанавливающие порядок выполнения функций и работ по качеству. Только после разработки всего комплекса этих документов можно установить все обязанности должностных лиц и подразделений по повышению качества.
Опыт большинства зарубежных предприятий показывает, что в рамках системы управления качеством необходимо иметь должностное лицо, подчиненное непосредственно директору предприятия, и специальную службу по качеству. Данная служба включает одно подразделение или иерархию подразделений, занимающихся координацией деятельности по качеству, разработкой специальных методов обеспечения и управления качеством (например, статистических методов), - подразделений, осуществляющих анализ результатов деятельности предприятия по качеству, надзор за соблюдением требований системы качества, периодическую проверку системы качества и организацию работ по ее совершенствованию.
В соответствии со стандартами ИСО серии 9000 все элементы, требования и положения, принятые предприятием для общего руководства и системы управления качеством, должны быть документированы. Такая документация обеспечивает единое понимание политики, задач и области качества и процедур по обеспечению, управлению и улучшению качества, позволяет четко распределить ответственность, права и обязанности подразделений и исполнителей, занимающихся управлением качеством, установить порядок их взаимодействия. Она закрепляет традиции и концентрирует передовой опыт в области обеспечения, управления и повышения качества. Эта документация может быть успешно применена для обучения персонала.
Основным документом является руководство по качеству, в котором дается общее описание системы управления качеством. Руководство по качеству является справочным материалом при внедрении системы, при поддержании ее в рабочем состоянии и совершенствовании.
В отечественной практике руководство по качеству чаще всего разрабатывается на предприятиях в форме стандарта предприятия «Комплексная система управления качеством продукции. Основные положения».
На крупных предприятиях может быть следующая иерархия документов руководства по качеству:
- общее руководство по качеству;
- руководство по качеству для различных производств (по видам изделий);
- руководство по качеству для различных подразделений;
- руководство по качеству для различных этапов жизненного цикла и функций, например, при проектировании продукции, материально-техническом снабжении.
Важнейшим документом является целевая научно-техническая программа повышения технического уровня качества продукции.
Процедуры являются документами нижнего уровня. Целесообразно, чтобы они включали [3]:
- цель выполнения функции или работы;
- перечень этапов и последовательность их выполнения с указанием (в случае необходимости) промежуточных результатов по этапам и требований к этапам;
- порядок(методы) выполнения работ на каждом этапе и сроки их выполнения (в случае выборочного контроля могут быть приведены планы контроля);
- перечень подразделений, выполняющих функцию (работу), и требования квалификации исполнителей;
- порядок взаимодействия между подразделениями и исполнителями;
- требования к ресурсам, необходимым для выполнения функции (работы, включая необходимую информацию);
- порядок контроля выполнения функции (работы);
- критерии оценки выполнения функции (работы), а также порядок стимулирования в зависимости от качества и сроков выполнения работ.
По каждому изделию целесообразно вести справочник, в котором могут быть помещены данные, используемые при обеспечении управления улучшения качества (например, классификаторы дефектов, классификатор причин дефектов, нормативы уровня дефектности).
10.5. Качество машин при технологической подготовке производства
Важнейшим этапом в обеспечении качества спроектированной машины является технологическая подготовка производства, которая представляет собой совокупность взаимосвязанных процессов, обеспечивающих технологическую готовность предприятий (или предприятия) к выпуску изделий заданного уровня качества при установленных сроках, объеме выпуска и затратах.
10.5.1. Технологичность конструкций изделия
Под технологичностью конструкций изделия (ТКИ) понимают совокупность свойств конструкции изделия, определяющих ее приспособленность к достижению оптимальных затрат при производстве, эксплуатации и ремонте для заданных показателей качества, объема выпуска и условий выполнения работ (ГОСТ 14.205-83).
Технологичность конструкции изделия может оцениваться качественно и количественно [20].
Качественно ТКИ оценивают путем установления соответствия применяемых (или примененных) конструкторских решений при проектировании изделий и их составных частей (сборочных единиц, деталей) требованиям оптимальных прогрессивных технологических процессов изготовления, технического обслуживания и ремонта.
Количественно ТКИ оценивают с помощью численных методов с применением специальных показателей, характеризующих интенсивность проявления определенных свойств изделия.
Показатель технологичности конструкции – количественная характеристика технологичности.
Уровень технологичности конструкции – показатель ТКИ, выраженный отношением значения базового показателя ТКИ к фактически полученному его значению.
Базовый показатель ТКИ – показатель, принятый за исходный при оценке ТКИ и утвержденный в техническом задании на проектирование изделия.
Обеспечение технологичности конструкции изделия – это функция подготовки производства, включающая комплекс взаимосвязанных мероприятий по управлению ТКИ.
Для практического использования может быть рекомендована классификация способов обработки, которая в зависимости от конструктивных особенностей изделия и условий производства подвергается соответствующему изменению и дополнению [10].
Порошковая металлургия включает формирование, спекание и обработку материала. Формирование может осуществляться прессованием, прокаткой, свободной насыпкой, ковкой и выдавливанием. Прессование делится на холодное, которое может быть статическим, гидростатическим, изостатическим, мундштучным, взрывным, электроимпульсным, клиновым, центробежным и горячим; последнее бывает двух видов; изостатическое и динамическое. Прокатка может осуществляться холодным и горячим способами, аналогично и выдавливание может быть холодным и горячим.
Спекание осуществляется в инертной или защитной атмосфере или в вакууме. Этот процесс протекает в камерных печах с нагревом токами высокой частоты, проходных или шахтных печах.
Обработка металлов давлением разделена на прокатку(поперечно винтовая или клиновая); прессование (прямое и обратное); свободную ковку (биллетирование, обрубка, осадка (высадка); протяжку (разгонка, раскатка); прошивку; гибку. К этим способам также относится объемная штамповка, которая подразделяется на горячую и холодную или полугорячую листовую штамповку.
Горячая штамповка включает осадку, высадку, радиальное обжатие, раскатку на кольцераскатных машинах, гибку, выдавливание, калибровку, штамповку на высокоскоростных молотах, штамповочную вальцовку и волочение.
К холодной и полугорячей объемной штамповке относятся выдавливание, калибровка, чеканка, холодная высадка.
Листовая штамповка классифицируется на разделительную (резка, вырубка, пробивка, обрезка, зачистка) и формообразующую, которая подразделяется на гибку, вытяжку, формовку, отбортовку; импульсным магнитным полем; электрогидравлическую; эластичной средой и ротационную вытяжку.
Термическая обработка включает отжиг, нормализацию, закалку, отпуск, старение, обработку холодом и химико-термическую обработку.
Сварку можно разделить на две группы: сварку плавлением и сварку давлением. Сварка плавлением подразумевает газовую, дуговую, термическую, электролучевую, лазерную и сварку сопротивлением. Дуговая сварка может выполняться открытой или закрытой дугой, под флюсом или лежачим электродом. Дуговая сварка в защитной среде может осуществляться в инертном и активном газе. Дуговая сварка в защитном инертном газе осуществляется неплавящимся или плавящимся электродом, а также с принудительным формированием шва.
Дуговая сварка в защитном активном газе выполняется с применением СН
(атомно-водородная) или СО
(с принудительным формированием шва), или газовой смеси.
Сварка давлением подразделяется на сварку взрывом, трением, термопрессовую, газопрессовую, холодную, ультразвуковую, с расплавляемой канавкой, диффузионную. Этот вид сварки включает также дугопрессовую, контактную и индукционную сварку. Дугопрессовая сварка может быть использована для приварки болтов.
Контактная сварка подразделяется на точечную, шовную и стыковую.
Индукционная сварка давлением может осуществляться сваркой вращающимся трансформатором, а также токами высокой и средней частоты.
Нанесение защитных покрытий осуществляется различными способами на неорганической основе и на органической основе.
Защитные покрытия на неорганической основе делятся на металлические и неметаллические.
Металлическое покрытие может осуществляться гальваническим, химическим, конденсационным (в вакууме), контактным и газотермическими методами. Гальванический метод предусматривает цинкование, кадмирование, хромирование, оловянирование, меднение, никелирование, железнение, покрытие сплавами и драгоценными металлами.
Химическим методом осуществляется никелирование, оловянирование, меднение и покрытие драгоценными металлами.
Защитные покрытия, выполняемые погружением в расплав, включают оловянирование, покрытие сплавом «олово-свинец», свинцевание, цинкование.
Контактным методом осуществляется никелирование, оловянирование, цинкование или серебрение.
Газотермическое напыление наводится электродуговым, тигельным, газопламенным, детонационным и плазменным способами.
Неметаллическое покрытие включает анодное окисление, химическое оксидирование, фосфатировнаие.
Защитное покрытие на органической основе включает лакокрасочное, полимерное или пластмассовое покрытие.
Обработка металлов резанием осуществляется различными способами, которые включают лезвийную, абразивную и другие виды обработки.
Лезвийная обработка делится на обработку универсальным и специальным инструментом.
Специальный инструмент применяют при обработке зубчатых колес и шлицевых соединений, а также при нарезании резьбы.
Абразивная обработка выполняется закрепленным и свободным абразивом. Закрепленный абразив применяется при шлифовании, полировании, хонинговании, суперфинишировании, алмазном разглаживании.
Поверхностно-пластическое деформирование включает обкатку, раскатку, накатывание, калибрование, дорнирование и дробеструйную обработку.
К физико-химической обработке относятся электроэррозийная, электромеханическая, плазменно-механическая, ультразвуковая, электрохимическая.
Классификация сборочных процессов может осуществляться в зависимости от метода сборки, либо от формы организации сборочного процесса.
По методу сборки сборочные процессы можно разделить на сборку при полной взаимозаменяемости, сборку при неполной или групповой взаимозаменяемости.
По форме организации сборка разделяется на стационарную и поточную. Поточная сборка может осуществляться при неподвижном изделии или с перемещением изделия.
10.5.2. Качественная оценка технологичности конструкции
Качественная оценка базируется на сравнительном анализе возможности применения прогрессивных процессов изготовления при принятой и предлагаемой конструкции изделия [20].
При качественной оценке ТКИ используют технологические рекомендации, которые оформляются в виде нормативно-технических документов (НТД), Эти документы подлежат периодическому пересмотру с целью отражения в них новейших направлений прогрессивной технологии, но на каждый момент в них должны быть приведены конкретные технологические требования, связанные с соответствующими процессами обработки.
Нормативно-технический документ, в котором сформулированы технологические требования к конструкции, рекомендуется разрабатывать по конкретным процессам обработки.
Для учета всех процессов обработки необходимо осуществить классификацию всех возможных процессов, которые могут применяться при изготовлении изделий.
Способы переработки пластмасс можно разделить на шесть групп.
Первая группа – переработка пластмасс в вязкотекучем состоянии. Она включает прямое (компрессионное) горячее прессование, литьевое прессование, свободное и центробежное литье.
Вторая группа - переработка пластмасс в высокопластичном состоянии. Ее разновидность – пневматическая формовка и формоизменяющая штамповка.
Третья группа – изготовление изделий из стеклопластиков. В нее входят контактный способ, а также формование и прессование с предварительным формованием.
Четвертая группа – обработка пластмасс в твердом состоянии. Она включает разделительную штамповку и обработку резанием.
Пятая группа – сварка. Ее разновидности – сварка нагретым воздухом или газом, сварка нагретым инструментом, сварка с нагревом токами высокой частоты, сварка трением, ультразвуком и сварка с помощью инфракрасного (ИК) излучения.
Шестая группа – склеивание различными смолами и клеями.
Качественная оценка технологичности не определяет количественные отличия вариантов конструкции друг от друга и от нормативного варианта, принятого за эталон при сравнении, а устанавливает только, какой из вариантов в большей степени соответствует требованиям технологических процессов изготовления.
10.5.3. Количественная оценка технологичности конструкции
Количественные методы оценки технологичности позволяют количественно определить отличие возможных вариантов конструктивных решений друг от друга и установить, насколько принятый вариант соответствует эталонному, принятому за базу сравнения. Эти методы предусматривают применение показателей технологичности, позволяющих определить значение этих величин.
Согласно ГОСТ 14.201-83 рекомендуется 11 показателей ТКИ: трудоемкость изготовления изделия; удельная материалоемкость изделия (удельная металлоемкость, удельная энергоемкость и пр.); технологическая себестоимость изделия; средняя оперативная трудоемкость технического обслуживания (ремонта) данного вида; средняя стоимость технического обслуживания (ремонта) данного вида; удельная трудоемкость изготовления изделия; трудоемкость монтажа; коэффициент применяемости материала; коэффициент унификации конструктивных элементов; коэффициент сборности.
Исходя из экономического подходя все показатели производственной технологичности делят на две группы: показатели, прямо определяющие затраты на изготовление изделия; косвенные показатели, характеризующие метод снижения затрат на их производство.
К первой группе относятся удельные трудоемкость изготовления, удельная материалоемкость (металлоемкость), удельные расходы на содержание и эксплуатацию оборудования, технологическая себестоимость.
Во вторую группу входят коэффициенты применяемости, повторяемости, поэлементной стандартизации, блочности, собираемости, охвата составных частей изделия типовыми технологическими процессами.
При выборе числа и номенклатуры показателей ТКИ для конкретного изделия необходимо руководствоваться правилом, требующим применения минимального, но достаточного для характеристики изделий числа показателей.
Показатели первой группы как меры затрат труда следует применять постоянно. Из показателей второй группы следует выбирать наиболее важные для данного изделия.
Из экономического содержания понятия ТКИ следует, что изменение степени отработанности конструкции изделия на технологичность приводит к изменению потребных затрат рабочей силы, прошлого труда, воплощенного в орудиях и предметах труда при производстве, эксплуатации и ремонте изделия.
Характеристикой затрат живого труда при производстве изделия является технологическая трудоемкость его изготовления. Для обеспечения возможности сравнивания конструкций по этому показателю он должен быть приведен к сопоставимому виду путем оценки трудоемкости единицы полезности данного изделия, т.е. по удельному показателю трудоемкости.
Расчет этого показателя выполняют по формуле
(10.12)
где
- удельная трудоемкость;
- технологическая трудоемкость изготовления изделия; Х- показатель полезности изделия.
Показатель полезности изделия – это показатель, характеризующий основной выходной параметр изделия с учетом его назначения, надежности и т.д. Определение показателя полезности является самостоятельной сложной задачей, которую должен решать главный конструктор изделия. Слагаемые показателя полезности всегда вносятся в техническое задание на проектирование изделия.
Аналогично в удельных показателях, рассчитанных на единицу полезности, должны учитываться показатели материалоемкости и расходов на содержание и эксплуатацию оборудования.
При оценке технологичности конструкции изделий необходимо различать общую, конструктивную и технологическую материалоемкость (металлоемкость).
Под конструктивной материалоемкостью понимают чистую массу единицы изделия.
Она зависит от принятых конструктивных решений: кинематических схем, компоновки составных частей, коэффициентов запаса прочности и т.п. Этот показатель характеризует качество конструктивных решений, т.е. работу конструктора.
Под технологической металлоемкостью понимают разность массы металла по нормам расхода и чистой массы изделия, т.е. массу отходов при изготовлении изделия. Технологическая металлоемкость служит характеристикой выбранных вариантов технологических процессов получения заготовок деталей и их обработки с точки зрения рационального использования металлов при изготовлении изделия.
Общая металлоемкость изделия М
состоит из суммы конструктивной М
и технологической М
металлоемкостей:
. (10.13)
При переходе к удельным показателям эта формула приобретает следующий вид:
, (10.14)
где
- общая удельная металлоемкость;
- удельная конструкторская металлоемкость;
- удельная технологическая металлоемкость.
Удельные затраты, характеризующие расход затраченного труда, воплощенного в орудиях труда, определяются как частное от деления расхода на содержание и эксплуатацию оборудования (РСО), приходящегося на единицу изделия, на полезность изделия П:
РСО
= РСО/П.
В случае разнонаправленности количественных показателей ТКИ, характеризующих расходы ресурсов, следует применять обобщающий показатель в виде технологической себестоимости.
Под технологической себестоимостью понимают сумму затрат на производство изделия по тем расходным статьям, которые различаются при различных вариантах технологического процесса изготовления изделия:
(10.15)
где М –расходы на сырье и материалы за вычетом возвратных отходов;
- стоимость топлива и энергии, идущих на технологические цели;
- основная и дополнительная заработная плата производственных рабочих;
- отчисления на социальные нужды от суммы основной и дополнительной заработной платы по установленным нормативам;
-расходы на содержание и эксплуатацию оборудования;
- расходы на износ инструментов и приспособлений целевого назначения.
В качестве показателей технологичности конструкции изделий, относящихся к группе, характеризующей метод снижения затрат расходов ресурсов, выделяют: коэффициент унификации, коэффициент охвата основных частей изделия типовыми технологическими процессами, коэффициент блочности и взаимозаменяемости, поэлементной стандартизации, точности обработки, шероховатости поверхности, применяемости материалов.
В соответствии с методическими указаниями (РД 50-33-80) под унификацией понимают приведение изделий или их составных частей к единообразию на основе установления рационального числа их разновидностей. Уровень унификации и стандартизации изделий и их составных частей определяют с помощью систем показателей. К этим показателям относятся коэффициент применяемости (К
), коэффициент повторяемости (К
), коэффициент межпроектной унификации (К
). Для оценки уровня унификации конкретного изделия применяют коэффициент повторяемости (К
) и коэффициент применяемости (К
).
Коэффициент применяемости рассчитывают как отношение числа типоразмеров составных частей в изделии без оригинальных составных частей к их общему количеству в изделии:
К
= (П - П
)/П, (10.16)
где П- общее число типоразмеров составных частей в изделии; П
- количество оригинальных типоразмеров составных частей в изделии.
Под типоразмерами изделия понимают изделие конкретного типа и исполнения с определенными значениями параметров. Число типоразмеров всегда соответствует числу наименований составных частей в спецификации конструкторской документации.
К оригинальным относятся такие составные части, которые разработаны впервые для данного изделия.
Коэффициент применяемости показывает, как конструктор при разработке документации использовал предшествующий опыт разработок и применил его в новом изделии.
Коэффициент повторяемости представляет собой характеристику уровня применения взаимозаменяемых составных частей внутри данного изделия. Его рассчитывают как отношение числа повторяющихся составных частей изделия к общему их числу, которое отражает насыщенность изделия повторяющимися составными частями:
К
= (N- П)/(П – 1), (10.17)
где N – общее число составных частей в изделии.
Коэффициент повторяемости показывает, как конструктор при проектировании составных частей изделия использовал типовые решения и то, в какой степени обеспечено широкое применение одинаковых составных частей в изделии.
Если в качестве составных частей изделия применяются стандартные типовые детали или сборочные единицы, то в качестве характеристики насыщения изделия такими составными частями используют коэффициент стандартизации.
Увеличение рассмотренных коэффициентов свидетельствует о более тщательной отработке конструкции на технологичность , а за счет этих конструктивных мер добиваются снижения затрат на проектирование и изготовления изделий. Аналогичное влияние на экономические результаты показывают поэлементная стандартизация при проектировании и изготовлении изделия. Применение стандартных элементов при проектировании деталей значительно сокращает потребное количество технологической оснастки, снижает расходы труда на их производство.
Снижение сортамента применяемых материалов всегда положительно влияет на организационную и экономическую стороны производства.
Коэффициент блочности, собираемости, компоновки показывают, как конструктор при проектировании изделия решил вопросы сборочной и ремонтной технологичности.
Коэффициент охвата составных частей изделия типовыми технологическими процессами отражает возможность их применения при данном варианте конструкции:
, (10.18)
где
- трудоемкость исполнения изделия по типовым технологическим процессам;
- технологическая трудоемкость изготовления изделия.
10.5.4. Взаимосвязь качественной и количественной оценок технологичности конструкции
Качественная и количественная оценка ТКИ отнесены к одному и тому же объекту – конструкции изделия, они тесно связаны и взаимообусловливают друг друга. Различие оценки конструкции на этапах проектирования позволяет обеспечить в конечном итоге высокую степень отработки конструкции на технологичность.
Принципиальная укрупненная структурная схема отработки конструкции изделий на технологичность при проектировании показана на рис. 10.11 [20].
На первом этапе проектирования конструкции количественная оценка ТКИ является главной. На этом этапе выбирают номенклатуру показателей, характеризующих это свойство. Отработка конструкции на технологичность начинается при формировании технического задания на проектирование путем определения нормативных показателей ТКИ и внесения их в техническое задание. Решение этой задачи осуществляется количественными методами.
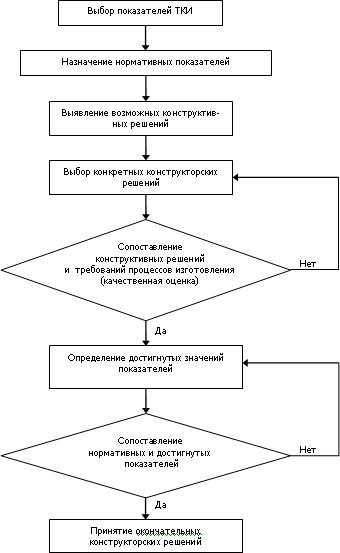
Рис. 10.11. Структурная схема отработки конструкции на технологичность
В процессе проектирования изделия и его составных частей на первый план выдвигается качественная оценка возможных вариантов технических решений и выбор из них наиболее технологичного варианта. Она заключается в сопоставлении возможных технических решений с технологическими требованиями процессов изготовления деталей и сборочных единиц. Если конструктивные и технологические характеристики данного варианта детали соответствуют рекомендациям и требованиям, заключающимся в возможности применения прогрессивной технологии, вариант принимают для окончательной проработки.
Далее вновь применяют количественную оценку технологичности. Определяют достигнутые значения показателей технологичности и сопоставляют их с нормативами (базовыми показателями).
Таким образом, качественная и количественная оценки ТКИ являются неразрывными частями общего процесса отработки конструкции изделия на технологичность, взаимно дополняют друг друга, являются, по существу, методической основой отработки конструкции на технологичность.
Нормативные (базовые) показатели и их определение. Полученные значения показателей технологичности необходимо сравнить с эталонными, называемыми нормативными (базовыми) показателями. Их значения по номенклатуре определяют до начала проектирования изделия и вносят в его техническое задание.
Значения нормативных (базовых) показателей технологичности нового изделия – удельной трудоемкости (
) и удельной материалоемкости (М
) – находят путем умножения значения этих показателей: изделия-аналога на коэффициент снижения трудоемкости (материалоемкости) в зависимости от роста (снижения) выходного параметра и коэффициента, учитывающего плановое снижение трудоемкости (материалоемкости) за период с момента утверждения технического задания на проектирование изделия до момента постановки его на производство или определения уровня его технологичности.
Эти зависимости могут быть выражены следующими формулами [20]:
=
; (10.19)
М
=
(10.20)
где
- удельная трудоемкость базового изделия –аналога;
- коэффициент, учитывающий изменения удельной трудоемкости в зависимости от изменения выходного параметра;
- коэффициент, учитывающий плановое снижение трудоемкости за период с момента утверждения технического задания до момента определения уровня технологичности;
- коэффициент, учитывающий снижение трудоемкости благодаря возникновению и внедрению трудосберегающей технологии в период с момента утверждения технического задания до момента определения уровня технологичности;
- коэффициент, учитывающий снижение трудоемкости благодаря внедрению в конструкцию изделия новейших технических решений, снижающих трудоемкость его изготовления, за период с момента утверждения технического задания до момента определения уровня технологичности;
- удельная материалоемкость базового изделия-аналога;
- коэффициент, учитывающий изменение удельной материалоемкости в зависимости от изменения выходного параметра;
- коэффициент, учитывающий плановое снижение материалоемкости за период с момента утверждения технического задания на проектирование изделия до момента определения его уровня технологичности;
- коэффициент, учитывающий плановое снижение материалоемкости благодаря возникновению и внедрению ресурсосберегающей технологии в период с момента утверждения технического задания на проектирование изделия до момента определения его уровня технологичности;
- коэффициент, учитывающий снижение материалоемкости благодаря внедрению в конструкцию изделий новейших ресурсосберегающих технических решений за период с момента утверждения технического задания до момента определения уровня технологичности.
Коэффициенты
и
определяют по формулам:
=
/
;
=
, (10.21)
где
- удельная трудоемкость нового изделия;
- удельная материалоемкость нового изделия.
Величины
,
находят по графику зависимости удельной трудоемкости от выходного параметра, построенного для данного класса изделий по опытно-статистическим данным.
Величины
и
находят по графику зависимости удельной материалоемкости от выходного параметра, построенного для данного класса изделий по опытным данным.
Коэффициенты
и
определяются по формулам:
=
=
, (10.22)
где
и
- соответственно плановое годовое снижение трудоемкости и материалоемкости, %; t – число лет с момента утверждения технического задания до момента определения уровня технологичности.
Коэффициенты снижения трудоемкости и материалоемкости изделий, учитывающие возникновение и внедрение трудо- и ресурсосберегающей технологии, а также внедрение в конструкцию трудо- и ресурсосберегающих технических решений (К
, К
, К
, К
) определяют экспертным путем, исходя из тенденций развития науки и техники, одним из методов, применяемых при прогнозировании их развития.
Нормативные (базовые) значения показателя расходов на содержание оборудования (РСО) необходимо назначить по фактически сложившимся значениям РСО на предприятиях, имеющих наиболее высокий технический уровень производства и изготовляющих аналогичную продукцию, входящую в конечную классификационную группу данных изделий.
Нормативные РСО следует назначать как удельные показатели, т.е. затраты РСО, приходящиеся на единицу потребительного эффекта при использовании изделия [7].
Определение нормативных показателей технологичности, выражаемых различными коэффициентами (коэффициент применяемости, коэффициент охвата типовыми технологическими процессами составных частей изделия и т.д.) основано на использовании статистических данных по изготовляемым и спроектированным конструкциям изделий, имеющим общие конструктивные и технологические признаки и вошедшим в одну конечную группу.
При узкой номенклатуре выпускаемых изделий в подотрасли нормативные показатели технологичности следует устанавливать на основе данных аналогов, а при широкой номенклатуре – на основе типовых представителей.
При их определении нулевым этапом является разработка классификационной таблицы изготовляемых изделий (естественно, эта разработка имеет место при отсутствии четкой классификации данных изделий).
При разработке принципов классификации необходимо в основу каждой группировки закладывать свой (как правило, один) классификационный признак, уточняющий и детализирующий признак, принятый по более укрупненной классификационной группировке.
В состав конечной подгруппы следует включать изделия, являющиеся по отношению к друг к другу аналогами. В эту подгруппу должны входить все аналоги.
Для каждой типовой конечной подгруппы назначают типовой представитель, для которого устанавливают нижний и верхний пределы нормативного (базового) показателя технологичности.
Нижний предел показателей следует назначать как среднее арифметическое по данному показателю по изделиям, вошедшим в конечную подгруппу:
К
, (10.23)
где К
- нижний предел нормативного показателя технологичности; К
- значение показателей технологичности i-го изделия, вошедшего в конечную группу;
- число изделий, вошедших в конечную классификационную группу.
Верхний предел базовых показателей технологичности конструкции следует назначать исходя из показателей технологичности лучших образцов изделий, которые вошли в данную классификационную подгруппу.
10.5.5. Система мероприятий по обеспечению технологичности конструкции
Система мероприятий по обеспечению технологичности конструкции изделия (СМОТКИ) делится на две группы: организационное и методическое обеспечение. Состав системы приведен на рис. 10.12.
Работы на стадиях проектирования, изделия по обеспечению ТКИ приведены в табл.10.1.
Рассмотрим функции конструкторских и технологических организаций по обеспечению отработки конструкции на технологичность. Важным моментом в обеспечении ТКИ является четкое разграничение функций между конструкторами и технологическими организациями, подразделениями), совместно выполняющими техническую подготовку производства изделия.
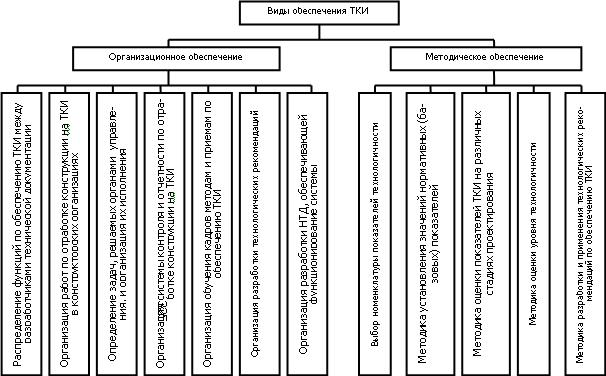
Рис.10.12. Система мероприятий по обеспечению технологичности конструкций
Таблица 10.1
Работы по обеспечению ТКИ
Стадии
проектирования |
Основные работы |
Разработка технического задания |
Уточнение изделия- аналога, состава показателей технологичности. Выбор принципиальных технологических схем работы изделия. Определение нормативных (базовых)показателей ТКИ |
Разработка технического предложения |
Определение технологической трудоемкости изготовления будущего изделия. Предварительная оценка показателей ТКИ, выбор оптимальных вариантов из возможных технических решений. |
Разработка эскизного проекта |
Уточнение значений показателей ТКИ по установленной номенклатуре, определение возможности применения стандартных унифицированных и заимствованных составных частей основных марок. Проведение качественного анализа принимаемых конструктивных решений. |
Разработка технического проекта |
Качественная оценка принимаемых конструктивных решений. Определение значений показателей ТКИ, принятие окончательных конструктивных решений |
Разработка рабочей конструкторской документации |
Выполнение качественной и количественной оценок принимаемых конструктивных решений. Определение уровня ТКИ. Согласование конструкторской документации с технологическими организациями, оформление соответствующего протокола. |
Технологические подразделения должны выполнять следующие функции по отработке конструкции на технологичность:
- проводить технологическую экспертизу конструкторской документации и анализ технологичности будущих изделий, вносить предложения по повышению технологичности, а также оформлять протокол согласования;
- принимать участие в разработке нормативно-технической документации, определяющей значение нормативных (базовых) показателей ТКИ по определенной номенклатуре изделий ТКИ по накопленной номенклатуре изделий (в отношении назначения значений характеристики уровня технологии);
- разрабатывать нормативно-технические документы, в которых отражается качественная оценка технологичности конструкции по закрепленным за организацией процессам изготовления и видам изделий, изготовляемых закрепленными за ней предприятиями;
- по результатам изготовления опытных образцов изделий на предприятиях-изготовителях вносить в конструкторские организации предложения о внесении изменений в конструкторскую документацию, вытекающих из требований повышения технологичности;
- осуществлять отработку конструкции на технологичность на всех стадиях конструкторской подготовки производства;
- проводить качественную и количественную оценку технологичности изделий на всех стадиях проектирования;
- выполнять расчеты фактически достигнутых показателей технологичности и уровня ТКИ;
- предоставлять конструкторскую документацию на контроль в технологические подразделения и оформлять соответствующие протоколы;
- по результатам технологического контроля документации и замечаниям технологических подразделений вносить собственные соответствующие изменения в конструкторскую документацию, обеспечивающие повышение технологичности конструкции;
- по результатам производства опытных образцов вносить изменения в конструкторскую документацию, обеспечивающие повышение технологичности конструкции.
Для отработки ТКИ конструкторские организации должны выполнять следующие работы:
разрабатывать нормативно-техническую документацию, определяющую значение нормативных (базовых) показателей технологичности по закрепленной за ними номенклатуре изделий; определять и устанавливать основной технический показатель, относительно которого определяются данные показатели.
Таким образом, ответственность за соответствие расчетных показателей технологичности нормативным (базовых) на стадии проектирования возлагается на конструкторское подразделение.
Контроль за правильностью исполнения этой работы возлагается на технологические подразделения. Все замечания и предлагаемые конструктивные изменения вносятся в протокол, содержащий анализ ТКИ. Одновременно с оформлением протокола технологическая служба подготавливает ведомость оценки уровня технологичности, которая является результатом проверки количественных показателей технологичности и отражает достигнутый уровень технологичности.
После оформления этого протокола и ведомости технологическое подразделение дает заключение о технологичности конструкции данного изделия. В нем приводится общая оценка технологичности конструкции с точки зрения ее подготовленности к изготовлению изделия на предприятии, приводятся принципиальные предложения по изменению конструкции с целью повышения уровня технологичности, а также рекомендации по проведению поисковых и экспериментальных работ.
После соответствующей доработки конструкторской документации в соответствии с протоколом анализа ТКИ технологическая служба проводит повторную оценку достигнутого уровня технологичности с оформлением нового протокола.
После передачи конструкторской документации с протоколом согласования технологическим подразделением в производство ответственность за соответствие фактически достигнутых показателей технологичности расчетным, полученным в процессе исполнения конструкторской подготовки производства, несет технологическое подразделение.
В случае возникновения разногласий между конструкторскими и технологическими подразделениями по оценке показателей технологичности окончательное решение принимает главный инженер предприятия (объединения).
Если технологическое подразделение не входит в состав производственного объединения (предприятия), то разногласия решает комиссия, назначаемая сторонами.