14.1. - Перечень работ, выполняемых при разработке технического проекта.
14.2. - Обеспечение ремонтопригодности машин при проектировании.
14.3. - Стендовые испытания макетов проектируемого изделия.
14.4. - Оценка показателей назначения.
14.1. Перечень работ, выполняемых при разработке технического проекта
Технический проект (ГОСТ 2.120-73) разрабатывают, если это предусмотрено техническим заданием, протоколом рассмотрения технического предложения или эскизного проекта.
Технический проект разрабатывают с целью выявления окончательных технических решений, дающих полное представление о конструкции изделия, когда это целесообразно сделать до разработки рабочей документации.
При необходимости технический проект может предусматривать разработку вариантов отдельных составных частей изделия. В этих случаях выбор оптимального варианта осуществляется на основании результатов испытаний опытных образцов изделия.
При разработке технического проекта выполняют работы, необходимые для обеспечения предъявляемых к изделию требований и позволяющие получить полное представление о конструкции разрабатываемого изделия, оценить его соответствие требованиям технического задания, технологичность, степень сложности изготовления, способы упаковки, возможности транспортирования и монтажа на месте применения, удобство эксплуатации, целесообразность и возможность ремонта и т.п.
В общем случае при разработке технического проекта проводят следующие работы:
1) разработку конструктивных решений изделия и его основных составных частей;
2) выполнение необходимых расчетов, в том числе подтверждающих технико-экономические показатели, установленные техническим заданием;
3) выполнение необходимых принципиальных схем, схем соединений и др.;
4) разработку и обоснование технических решений, обеспечивающих показатели надежности, установленные техническим заданием и предшествующими стадиями разработки (если эти стадии разрабатывались);
5) анализ конструкции изделия на технологичность с учетом отзывов предприятий-изготовителей промышленного производства в части обеспечений технологичности в условиях данного конкретного производства, в том числе по использованию имеющегося на предприятии оборудования, а также учета в данном проекте требований нормативно-технической документации, действующей на предприятии-изготовителе; выявления необходимого для производства изделий нового оборудования (обоснование разработки или приобретения); разработку метрологического обеспечения (выбор методов и средств измерения);
6) разработку, изготовление и испытание макетов;
7) оценку изделия в отношении его соответствия требованиям эргономики, технической эстетики;
8) оценку возможности транспортирования, хранения, а также монтажа изделия на месте его применения;
9) оценку эксплуатационных данных изделия (взаимозаменяемости, удобства обслуживания, ремонтопригодности, устойчивости против воздействия внешней среды, возможности быстрого устранения отказов, контроля качества работы изделия, обеспеченность средствами контроля технического состояния и др.);
10) окончательное оформление заявок на разработку и изготовление новых изделий (в том числе средств измерения) и материалов, применяемых в разрабатываемом изделии;
11) проведение мероприятий по обеспечению заданного в техническом задании уровня стандартизации и унификации изделия;
12) проверку изделия на патентную чистоту и конкурентоспособность, оформление заявок на изобретения;
13) выявление номенклатуры покупных изделий, согласование применения покупных изделий;
14) согласование габаритных, установочных и присоединительных размеров с заказчиком или основным потребителем;
15) оценку технического уровня и качества изделия;
16) разработку чертежей сборочных единиц и деталей, если это вызывается необходимостью ускорения выдачи задания на разработку специализированного оборудования для их изготовления;
17) проверку соответствия принимаемых решений требованиям техники безопасности и производственной санитарии;
18) составление перечня работ, которые следует провести на стадии разработки рабочей документации, в дополнение и (или) уточнение работ, предусмотренных техническим заданием, техническим предложением и эскизным проектом
Макеты должны быть предназначены для проверки (в необходимых случаях – на объекте заказчика или потребителя) конструктивных и схемных решений разрабатываемого изделия и (или) его составных частей, а также для подтверждения окончательно принятых решений. Испытания макетов должны проводиться в соответствии с программой и методикой испытаний, разработанной по ГОСТ 2.106-68. Необходимость изготовления макетов и их количество устанавливаются организацией-разработчиком (если требуется, то совместно с заказчиком).
В технический проект включают конструкторские документы в соответствии с ГОСТ 2.102-68, предусмотренные техническим заданием и протоколом рассмотрения технического предложения, эскизного проекта.
При разработке технического проекта могут быть использованы отдельные документы, разработанные на предыдущих стадиях, если эти документы соответствуют требованиям, предъявляемым к документам технического проекта, или если в них внесены изменения с целью обеспечения такого соответствия. Разработанным документам присваивают литеру «Т».
14.2. Обеспечение ремонтопригодности машин при проектировании
14.2.1. Ремонтопригодность как одно из важнейших свойств конструкции машины
Большинство современных машин с длительным сроком службы являются восстанавливаемыми, т.е. возникшие при эксплуатации дефекты (препятствующие нормальному выполнению обусловленных конструкцией функций), могут быть устранены средствами ремонта.
Работы, осуществляемые в процессе эксплуатации машин по поддержанию и восстановлению работоспособности, характеризуются значительными затратами труда, материальных и денежных средств. Как правило, эти затраты во время эксплуатации машины значительно превышают затраты на ее изготовление. Например, затраты на техническое обслуживание и ремонт тракторов типа ДТ-75 за 8 лет их эксплуатации в 4-5 раз превышают затраты на их изготовление.
Необходимо также иметь в виду, что обслуживание и ремонт СХМ, осуществляемый в профилактическом или аварийном порядке, сопровождаются их простоем, нанося экономический ущерб предприятию.
Современное состояние науки и техники не позволяет при приемлемых затратах на проектирование и производство, создавать конструкции СХМ, которые бы не требовали обслуживания и ремонта в эксплуатации. Кроме того, не исключена возможность аварии, при которых возможны повреждения, для устранения которых необходимы ремонтные работы.
Следовательно, одно из основных требований к машине – ремонтопригодность.
Ремонтопригодность – свойство объекта, заключающееся в приспособлении к предупреждению и обнаружению причин возникновения его отказов, повреждений и устранению их последствий путем проведения ремонтов и технического обслуживания.
В соответствии с практикой эксплуатации СХМ совокупность работ по поддержанию и восстановлению их работоспособности ресурса делится на техническое обслуживание (ТО) и ремонт (Р). ТО и Р делятся на профилактические, осуществляемые в плановом порядке, и аварийные, проводимые по мере возникновения отказов или аварийных состояний.
Свойство ремонтопригодности СХМ влияет на величину затрат труда, материальных и денежных средств в процессе эксплуатации и на длительность простоев в связи с обслуживанием и ремонтом.
Ремонтопригодность тесно связана с другими свойствами: безотказностью и долговечностью.
В общем случае ремонтопригодность представляет собой одно из свойств конструкций машин, характеризующих их качества.
Свойство ремонтопригодности закладывается и обеспечивается, как и другие свойства СХМ, при их проектировании и изготовлении. Проявляется это свойство в конкретных условиях использования СХМ, т.е. при воздействии определенного сочетания климатических факторов, организационно-технических условий обслуживания и ремонта и др.
Характеристики ремонтопригодности являются функцией конструктивных и эксплуатационных факторов, которые могут изменяться в определенных границах. Следовательно, свойством ремонтопригодности можно управлять. Отсюда следует, что количественные значения показателей ремонтопригодности могут устанавливаться, обеспечиваться и оцениваться при проектировании, изготовлении и эксплуатации машин.
14.2.2. Основные показатели ремонтопригодности
Основные показатели ремонтопригодности должны задаваться в техническом задании на проектирование СХМ и оцениваться при разработке конструкции и их изготовлении, в процессе их испытаний и эксплуатации.
К числу показателей собственно ремонтопригодности относятся:
оперативные показатели:
- среднее время восстановления;
- вероятность восстановления в заданное время;
экономические показатели:
средние и удельные затраты труда и денежных средств на техническое обслуживание и ремонт;
комплексные показатели надежности:
- коэффициент готовности;
- коэффициент технического использования.
Под средним временем восстановления
СХМ понимают математическое ожидание времени восстановления работоспособности:
, (14.1)
где
- математическое ожидания времени восстановления работоспособности;
- плотность вероятности распределения времени восстановления.
При оценке среднего времени восстановления по статистическим данным
, полученным в результате испытаний или эксплуатации, этот показатель находим из выражения
, (14.2)
где
- время восстановления
-го отказа;
- количество отказов, наблюдаемых в процессе испытаний или эксплуатации.
В связи с тем, что
входит в состав комплексных показателей надежности, этот показатель получил широкое распространение.
Значительно большей информационностью о свойствах конструкции обладает другой показатель ремонтопригодности – вероятность восстановления машины в заданное время
, определяется из соотношения
,
где
- заданное время восстановления.
Этот показатель характеризует вероятность того, что возникший отказ будет обнаружен и устранен за время, не превышающее время
.
Он определяется из выражения
, (14.3)
где
- плотность вероятности времени восстановления.
Статистическое значение вероятности восстановления определится из выражения
, (14.4)
где
- число устройств, не восстановленных за промежуток времени от
до
;
- общее число устройств, подлежащих восстановлению за этот же период времени.
Для оценки оперативной стороны ремонтопригодности, кроме приведенных показателей, используются комплексные показатели.
Наиболее широкое распространение среди них получили коэффициент готовности и коэффициент технического использования.
Коэффициент готовности
представляет собой вероятность того, что изделие будет работоспособно в произвольно выбранный момент времени, кроме периодов времени выполнения планового технического обслуживания
, (14.5)
где
- наработка на отказ.
Вид этой характеристики показывает, что надежность машины является функцией не только ее безотказности, но и ремонтопригодности:
,
где
- число изделий (машин);
- количество отказов этих изделий;
- наработка
-го изделия между отказами.
Коэффициент технического использования
- определяют отношением средней наработки машин
(в единицах времени) до контрольного ремонта, между капитальными ремонтами, до списания, или за период испытаний к сумме, состоящей их этой наработки, времени, затраченного на техническое обслуживание
и времени, затраченного на устранение отказов и неисправностей
за тот же период
. (14.6)
К числу экономических показателей ремонтопригодности, являющимися комплексными, относятся: средние затраты денежных средств на техническое обслуживание и ремонты -
; средние затраты труда на техническое обслуживание и ремонты
; суммарные затраты денежных средств на техническое обслуживание и ремонт
.
Сельскохозяйственные машины на стадиях проектирования и разработки конструкторской документации целесообразно с позиций ремонтопригодности характеризовать показателями технологичности при техническом обслуживании и ремонта. Они характеризуют общее совершенство конструкции машины с точки зрения ее приспособленности к ремонту и техническому обслуживанию). К ним в соответствии с ГОСТ 21623-76 относят:
коэффициент доступности
, (14.7)
где
- основная трудоемкость (ч) выполнения операций технического обслуживания (ремонта);
- время вспомогательной трудоемкости, связанное с выполнением работ (например, снятие щитков, трубопроводов и других сборочных единиц, мешающих демонтажу заменяемой сборочной единицы, их монтаж после замены, смена инструмента, приспособлений для работы и др.);
коэффициент взаимозаменяемости
, (14.8)
где
- оперативная трудоемкость замены сборочной единицы или детали без учета трудоемкости
пригоночных, регулировочных и селективных работ
;
коэффициент легкосъемности
, (14.9)
где
- оперативная трудоемкость демонтажно-монтажных работ на прототипе объекта проектирования.
Коэффициент унификации
- показывает, какая часть из использованных в изделии деталей является унифицированной, и определяется как отношение количества унифицированных деталей и сборочных единиц
рассматриваемой конструкции к общему количеству деталей и сборочных единиц (
) в машине
.
Коэффициент применяемости конструктивных элементов
представляет собой отношение количества наименований типоразмеров стандартизированных
, нормализованных
, покупных
и заимствованных
сборочных единиц и деталей к общему количеству
наименований сборочных единиц и деталей, применяемых в изделии:
. (14.10)
Коэффициент конструктивной преемственности 
, (14.11)
где
- количество наименований ранее освоенных сборочных единиц и деталей.
При оценке коэффициентов применяемости
, унификации
и конструкции преемственности
из расчетов исключаются стандартизированные крепежные детали (болты, гайки, шайбы и др.).
Заимствованные и нормализованные сборочные единицы комплексного изделия подсчитываются по количеству входящих в них деталей; покупные сборочные единицы (комплектующие изделия и элементы) – по собранным единицам в целом. При этом к заимствованным сборочным единицам и деталям относятся детали и сборочные единицы, ранее спроектированные как оригинальные для конкретного изделия или сборочной единицы и применяемые в двух и более изделиях (внешнее заимствование), а также в двух или более группах одного изделия (внутреннее заимствование).
Коэффициент применяемости
вместе с коэффициентами унификации
и конструктивной преемственности
являются важнейшими показателями уровня стандартизации.
14.2.3. Обеспечение ремонтопригодности
При разработке конструкций машин и их изготовлении решаются три группы задач по обеспечению ремонтопригодности [32]:
а) устанавливаются требования к ремонтопригодности;
б) прогнозируются характеристики ремонтопригодности;
в) производится оценка достигнутого уровня характеристик ремонтопригодности.
Содержание работ по обеспечению требований ремонтопригодности оформляется в виде программы, являющейся частью программы обеспечения надежности изделий.
14.2.3.1. Требования к ремонтопригодности
На основании накопленного опыта обеспечения и оценки ремонтопригодности СХМ можно указать следующие требования к технологичности в обслуживании и ремонте.
Требования к стандартизации и унификации
При разработке конструкции новых СХМ должны быть широко использованы стандартизированные и унифицированные составные части, выпускаемые промышленностью, высокое качество которых подтверждено опытом эксплуатации.
Конструкция СХМ должна обеспечивать минимальное использование при техническом обслуживании и ремонте специального инструмента и приспособлений, дефицитных материалов.
Конструирование СХМ одного вида должно идти по линии создания параметрических и типоразмерных рядов унифицированных сборочных единиц с максимальным использованием их в компоновке машин, с тем, чтобы номенклатура запасных частей была минимальной.
Общее количество используемых в изделии крепежных деталей и их типоразмеров должно быть минимальным. Должно быть ограничено также количество типоразмеров подшипников качения, пресс-масленок, пробок и заглушек, резинотехнических изделий.
Конструкция машины должна предусматривать использование ограниченного количества типов смазочных материалов.
Требования к преемственности технологических процессов технического обслуживания и ремонта конструктивно однотипных машин. При создании новых машин должна учитываться принятая в отрасли система технического обслуживания и ремонта, а также возможность применения наилучших образцов серийно изготавливаемых средств механизации для проведения технического обслуживания и ремонта.
Требования к контролепригодности машин. Сборочные единицы СХМ, для контроля технического состояния которых требуется большой объем разборочных работ, должны быть приспособлены к диагностированию при помощи способов и средств косвенного контроля. Особенно легко доступными для контроля технического состояния должны быть сборочные единицы и детали, ресурс которых меньше межремонтного ресурса машины.
Требования к принципам рационального расчленения и расположения сборочных единиц машины. Конструкция машины должна обеспечивать удобство и легкость независимого расчленения ее на сборочные единицы, что очень важно при агрегатном способе ремонта. В местах соединений сборочных единиц должны быть установлены быстроразъемные соединения для электроцепей, маслопроводов, топливопроводов и др.
Расположение сборочных единиц машины должно обеспечивать возможность независимого выполнения операций технического обслуживания.
Детали, имеющие ответственные сопряжения, обработанные при изготовлении совместно или приработанные в процессе использования, должны иметь метки спаренности (поршни и цилиндры, золотники), предотвращающие их «обезличивание» при ремонте.
Облегчение сборки и разборки. При проектировании сборочных единиц необходимо обеспечить удобство обслуживания, разборки, сборки и регулировки, доступность агрегатов для осмотра.
Приведем несколько примеров облегчения сборки и разборки соединений, часто разбираемых в эксплуатации. Надевание мягкого рукава на трубу (рис.14.1): а) затруднительно в конструкции; б) облегчено введением направляющего участка с входной кромкой.
Для упрощения сборки уплотнений с разрезными прижимными кольцами корпус должен быть снабжен пологой заходной фаской
(рис.14.1,г).
Рис.14.1. Конструкции элементов СХМ для облегчения сборки и разборки соединений
В труднодоступных соединениях, особенно когда сборка производится вслепую, детали, вводимые в отверстие, целесообразно снабжать конусами-искателями, а в отверстиях предусматривать конусы-ловители (рис.14.1,е).
Требования к доступности деталей и сборочных единиц. При конструировании СХМ должна учитываться необходимость проведения работ по техническому обслуживанию и ремонту в установленные сроки и с заданной трудоемкостью.
Части машины, подлежащие техническому обслуживанию и ремонту (резьбовые соединения, прочие крепежные детали, точки смазки, места регулировки, контроля и т.д.), должны быть доступны. Требования к доступности должны исключать необходимость работы персонала по техническому обслуживанию и ремонту в неудобных позах.
Не допускается использование конструкций резьбовых соединений, расположенных в труднодоступных местах, у которых при отворачивании гаек проворачивались бы болты. Нарезка резьбовых соединений должна быть защищена от механических повреждений и коррозии.
Требования к легкосъмности деталей и сборочных единиц. У деталей и сборочных единиц, имеющих большой вес, должны быть предусмотрены элементы их захвата (рым-болты, усики, приливы и др.) подъемно-транспортными устройствами.
Система крепления деталей, конструкции разъемов должны обеспечивать легкосъемность деталей и сборочных единиц, особенно требующие периодической замены (рис.14.2).
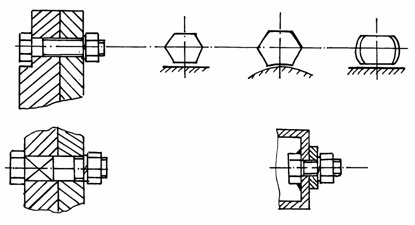
14.2. Способы фиксации болта от проворота при затяжке
Требования к взаимозаменяемости однотипных деталей и сборочных единиц. Детали и сборочные единицы, выполняющие одинаковые функции и несущие близкие по величине нагрузки, должны быть взаимозаменяемые по геометрическим размерам, характеру посадок, рабочим параметрам в пределах технических возможностей и экономической целесообразности.
Требования к приспособленности составных частей СХМ для выполнения регулировочных и доводочных работ. Конструкции СХМ должны иметь необходимое количество регулируемых элементов в составных частях машины, обеспечивающих необходимые пределы изменения значений параметров.
Пример регулировки зазоров между ножом и противорежущей пластинкой приведен на рис.14.3.
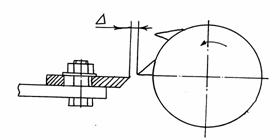
Рис.14.3. Конструкция противорежущей пластины, обеспечивающей регулировку зазора
Требования к конструкции изнашивающихся деталей. Изнашивающиеся детали СХМ, ремонт которых экономически целесообразен, должны быть приспособлены к восстановлению до первоначальных или ремонтных размеров с применением прогрессивных восстановительных процессов, например, лемех (магазины для вытяжки).
Для восстановления режущей способности рабочих органов должны быть предусмотрен доступ к ним заточных устройств или обеспечена легкосъемность режущих элементов.
Базовые конструктивные элементы (рамы, корпуса и др.) не должны иметь изнашивающихся участков, срок службы которых меньше полного срока службы СХМ. При невозможности выполнение этого условия целесообразно использовать сменные части (втулки, накладки и т.п.) с указанием в технической документации (ГОСТ 2.602-88), ремонтных и выбраковочных размеров по условиям смены этих частей.
Односторонне изнашивающиеся детали целесообразно конструировать с учетом возможности подстановки их для работы другой стороной (например, опорная пластинка режущего аппарата жатки, дека молотильного аппарата зерноуборочного комбайна).
Ресурс изнашивающихся деталей, как правило, должен быть равен заданному межремонтному периоду сборочной единицы машины или большему (кратному ему).
Ресурс быстроизнашивающихся легкосъемных деталей (ремней, пальцев и ножей режущих аппаратов и др.) может быть меньше межремонтного периода сборочных единиц.
14.2.3.2. Прогнозирование ремонтопригодности СХМ при проектировании
В ходе проектирования машины перед конструктором возникает задача оценки ремонтопригодности создаваемой конструкции с целью убедиться в обосновании принятых решений. Оценить ремонтопригодность можно, используя комплексные и единичные показатели, характеризующие машину в целом или отдельные ее составные части.
Оценка показателей ремонтопригодности сложна из-за ряда особенностей.
1. Показатели ремонтопригодности зависят от большого числа конструктивных и внешних факторов. Эти зависимости в большинстве своем еще не установлены.
2. Не все свойства конструкции, влияющие на ремонтопригодность, можно оценить количественно (например, конструктивные факторы, обеспечивающие удобство проведения ремонтных и профилактических работ, защищенность от ошибок и др.).
Указанные особенности вынуждают решать задачу прогнозирования уровня ремонтопригодности СХМ в основном известными качественными методами: методом сравнения с прототипоми; методом экспертных оценок. Достоинство этих методов заключается в их простоте.
Для ряда конструктивно несложных изделий такие методы позволяют получать вполне удовлетворительную оценку ремонтопригодности на стадиях проектирования.
Количественные методы задания и оценки ремонтопригодности позволяют создать методы прогнозирования показателей ремонтопригодности, основанные на использовании аппарата статистики, многофакторного и регрессионного анализа. Эти методы позволяют выявить существенные факторы и установить количественные связи между показателями ремонтопригодности, параметрами конструкции и факторами внешней среды.
Третья группа методов прогнозирования ремонтопригодности занимает положение между качественными (метод сравнения с прототипом, экспертный метод) и количественными (использование уравнений регрессии). Эти методы базируются на использовании аналогии операции обслуживания и ремонта изделий, обладающих широкой конструктивной преемственностью. В этом случае технологические процессы обслуживания и ремонта делятся на типовые операции, продолжительность, трудоемкость, стоимость выполнения которых являются достаточно стабильными величинами. Эти величины позволяют определить показатели ремонтопригодности проектируемого однотипного изделия.
Развитием такого подхода является метод нормативов, базирующийся на определении времени или трудоемкости выполнения типовых операций технологического процесса обслуживания и ремонта. Например, на основе анализа обслуживания или ремонта ряда изделий устанавливается нормативное время отвертывания – завертывания болтов, винтов, гаек, время спрессовывания и напрессовывания подшипников и др. В силу детализации процессов обслуживания ремонта до уровня типовых операций со стандартными элементами конструкции метод нормативов не требует для своего применения преемственности проектируемого изделия.
На каждой из стадий проектирования возникают различные задачи прогнозирования ремонтопригодности. Уже на ранних стадиях разработки проекта необходимо ориентировочно оценить предполагаемые значения показателей ремонтопригодности изделия и сравнить их с заданными.
Результаты сравнения предопределяют последующие мероприятия по обеспечению ремонтопригодности машины.
Если прогнозируемые показатели соответствуют заданным, то в ходе проектирования используют уже известные принципы и методы обеспечения ремонтопригодности, основанные на опыте проектирования предшествующих изделий.
Если предварительная оценка показала, что заданные требования не выполняются, в программе обеспечения ремонтопригодности должно уделяться больше внимания изысканиям новых конструктивных решений, направленных на достижение высокого уровня ремонтопригодности.
14.2.3.3. Методы качественной оценки ремонтопригодности
Один из методов качественной оценки ремонтопригодности СХМ на стадии проектирования – метод сравнения с прототипом.
Прогнозирование ремонтопригодности производится на первых этапах путем сравнения эксплуатационной технологичности сборочных единиц проектируемой СХМ и прототипа. Оцениваемыми признаками являются
1) конструктивные характеристики:
- число и доступность мест обслуживания и ремонта;
- периодичность обслуживания;
- необходимость проведения дополнительных работ при обслуживании и ремонте;
- вес сборочных единиц;
- число точек крепления сборочных единиц;
- номенклатура масел и топлива;
- наличие и тип датчиков контроля технического состояния машины.
2) компоновочные параметры:
- количество сборочных единиц;
- расположение двигателя (открытое, закрытое, в передней, средней или задней части);
- количество предварительно снимаемых элементов для доступа с целью замены основных сборочных единиц (двигателя, трансмиссии и др.);
- плотность компоновки отдельных систем;
- рабочие позы ремонтника при обслуживании или замене сборочных единиц;
- расположение и площадь люков для доступа и др.
Большинство перечисленных компоновочных и конструктивных параметров можно определить по чертежно-технической документации на стадии технического проекта СХМ.
Оценка каждого варианта проекта проводится последовательно по всем параметрам путем сравнения с прототипом и принятия одного из следующих решений: «лучше», «без изменений», «хуже». Если число положительных решений равно числу отрицательных решений, то считается, что ремонтопригодность проекта одинакова с ремонтопригодностью прототипа. Если же число решений «лучше» больше, чем решений «хуже», то ремонтопригодность проекта выше.
Вариант проекта, имеющий наибольшую разность положительных и отрицательных решений, считается рациональным с позиций ремонтопригодности. Когда одинаковой разностью «лучше» – «хуже» обладают несколько вариантов проекта, выбор следует остановить на варианте, обладающем наибольшим числом решений «без изменений».
14.2.3.4. Методы количественной оценки ремонтопригодности
В последние годы все более широко начали применяться количественные методы оценки ремонтопригодности СХМ. Одним из методов решения этой задачи явилось применение регрессионного анализа, позволяющего установить количественные зависимости между параметрами конструкции и показателями ремонтопригодности.
Разработаны на базе специально проводимых экспериментов уравнения регрессии [32], где в качестве факторов использованы конструктивные характеристики изделия:
- доступность и легкосъемность (количество предварительно снимаемых сборочных единиц, деталей, количество креплений, соединений, использование стандартного и специального инструмента, приспособлений, масса снимаемых сборочных единиц и др.);
- взаимозаменяемость (общее количество регулируемых и контролируемых параметров, требуемая точность подгонки и регулировки).
Построенные уравнения регрессии для оценки значений показателей ремонтопригодности на каждой из стадий проектирования позволяют учитывать информацию о конструктивных характеристиках машины.
На стадии эскизного проекта разрабатываются компановочные чертежи общих видов машины. По этим данным возможно определить число предварительно снимаемых элементов для обслуживания или замены данного элемента, их масса.
На стадии технического проекта уточняется количество крепежных деталей и соединений, а также становится возможным определить общее число контролируемых и регулируемых параметров при замене элемента и точность подгонки, предварительного подбора или регулировки.
Чтобы оценить, например, время замены элемента проектируемого однотипного изделия, необходимо по данным чертежно-технической документации определить значения независимых переменных (количество предварительно снимаемых сборочных единиц, деталей; их массы; количество креплений) и подставить их в соответствующее уравнение регрессии.
Найденные показатели времени выполнения различных операций ремонта позволят оценить основные показатели ремонтопригодности (см. п.14.2.2) и сравнить их с заданными.
14.2.3.5. Контрольные испытания на ремонтопригодность
Цели испытаний на ремонтопригодность:
- определение значений количественных показателей ремонтопригодности;
- контроль соответствия требованиям по ремонтопригодности, заданным в нормативно-технической документации на изделия;
- выявление конструктивных недостатков, снижающих ремонтопригодность, и разработка мероприятий по их устранению;
- оценка полноты и качества эксплуатационной и ремонтной документации;
- выявление схемно-конструктивных недостатков, снижающих уровень ремонтопригодности, и разработка рекомендаций по их устранению.
Контроль изделий осуществляется в составе испытаний:
- предварительных;
- приемочных;
- периодических (по требованию заказчика);
- типовых.
Испытания на ремонтопригодность проводят, как правило, экспериментальными методами. Испытания изделия на ремонтопригодность проводят по программам и методикам, составляемым организацией, проводящей испытания, и подлежащим согласованию с разработчиком (изготовителем), заказчиком (основным потребителем) и утверждению в установленном порядке.
Испытания на ремонтопригодность могут проводиться отдельно или совместно с другими испытаниями.
При испытании изделий на ремонтопригодность применяют следующие методы:
- испытания с возникающей необходимостью восстановления;
- испытания с моделированием отказов;
- комбинированные испытания.
Метод испытания на ремонтопригодность с возникающей необходимостью восстановления заключается в том, что изделия подвергают нормальным или ускоренным испытаниям на безотказность и долговечность в условиях и в объеме, установленных программой испытаний, а необходимую для оценки ремонтопригодности информацию получают при выполнении операции технического обслуживания и плановых ремонтов, предусмотренных эксплуатационной и ремонтной документацией, а также неплановых ремонтов по выявлению и устранению отказов и повреждений, возникающих в процессе испытаний.
Метод испытания на ремонтопригодность с моделированием отказов заключается в том, что отказы изделия имитируют или преднамеренно создают в соответствии с программой испытаний.
Метод комбинированных испытаний на ремонтопригодность заключается в использовании перечисленных выше методов в любом их сочетании, установленном в методиках испытаний.
При контроле ремонтопригодности используют следующие источники информации:
- данные хронометрических наблюдений за выполнением всех операций по ремонту изделий;
- данные о затратах времени, труда и средств, установленные при проведении подобных операций на аналогах или прототипах;
- результаты анализа выявленных конструктивных недостатков, ухудшающих ремонтопригодность, и принятых по ним мероприятиям.
Результаты испытаний СХМ на ремонтопригодность считаются положительными тогда, когда величины выбранных показателей оценки ремонтопригодности соответствуют записанным в техническом задании на проектирование.
14.3. Стендовые испытания макетов проектируемого изделия
На стадии технического проекта с целью выполнения требований технического задания (показатели назначения, надежности) проводят разработку, изготовление и стендовые испытания макетов отдельных элементов СХМ (решетный модуль, вентилятор, молотильный аппарат).
14.3.1. Оценка надежности
Главным источником информации о надежности машин после изготовления макетов образцов являются экспериментальные исследования и испытания. Испытания изделий на безотказность и долговечность принято называть ресурсными. От ресурса конструкционных элементов машины зависят ее основные показатели надежности. Кроме ресурсных испытаний очень ценные информации о надежности машин дают массовые наблюдения за эксплуатацией и ремонтом их в хозяйственных условиях. Этим создается база данных для статистических обобщений, позволяющих получить более достоверную оценку о надежности машин и их элементов.
В процессе создания или усовершенствования СХМ возникает необходимость в сравнительных испытаниях деталей одного и того же функционального назначения, но имеющих различные конструктивные решения или изготовленных из различных материалов или по разным технологиям. Поэтому целесообразно проводить испытания отдельных элементов конструкций и агрегатов, в которых эти элементы взаимодействуют с другими. Это должно выполняться на отдельных стендах. Такие стенды позволяют проводить испытания разных объектов машин независимо друг от друга, т.е. отказ одного объекта не останавливает испытания другого (что имеет место при испытаниях полнокомплектной СХМ). Такое решение существенно упрощает конструкцию стенда, комплекс системы для оценки показателей функционирования и нагружения, автоматизацию, увеличивает производительность стенда (т.е. наработку стенда в сутки), уменьшает стоимость выполняемых работ.
Стендовые натурные испытания представляют собой испытания деталей и сборочных единиц, изготовленных в натуральную величину согласно техдокументации СХМ. При таких испытаниях на стационарных установках, с помощью специальных нагружающих устройств создаются условия, вызывающие появление физической картины отказов (характерные для отказов этих элементов в реальных условиях эксплуатации машины).
Натуральные стендовые испытания сборочных единиц и агрегатов занимают промежуточное место между полевыми испытаниями сельхозмашин в эксплуатационных режимах и лабораторными испытаниями элементов деталей на образцах с помощью универсальных машин. Обычно при работе в эксплуатационных режимах изнашивание и усталостные повреждения деталей в сложных сборочных единицах и агрегатах СХМ развиваются одновременно и взаимосвязанно. Поэтому во многих случаях необходимо проводить ресурсные стендовые испытания в составе агрегата или сборочной единицы, несмотря на то, что испытания отдельных деталей дешевле и менее трудоемки.
Стендовые ресурсные испытания имеют следующие преимущества по сравнению с эксплуатационными [1].
1. Сокращение сроков создания новой техники за счет:
- возможности круглогодичных испытаний;
- воспроизведения форсированных режимов;
- возможности отработки конструкций деталей и сборочных единиц до изготовления машины в целом.
2. Обеспечивается большая точность проведения экспериментов за счет:
- устранения множества сопутствующих случайных факторов, которые невозможно избежать при полевых испытаниях;
- воспроизведения основных возможных нагрузок, встречающихся при работе на разных агрофонах и при переходных режимах;
- возможности реализации требуемого числа повторностей испытаний;
- возможности изучать зарождение и развитие повреждений в испытываемых деталях;
- возможности проведения аппаратурного контроля (измерений).
3. Достигается значительный экономический эффект за счет:
- сокращения сроков создания СХМ;
- снижения стоимости объекта испытаний, так как на испытания представляются отдельная деталь, простейшая сборочная единица или агрегат, а не машина в целом;
- стенды обладают большим ресурсом и универсальностью, что позволяет реализовать на них много повторностей испытаний, а также проводить испытания других объектов (рис.14.4-14.10);
- снижения расходов на обслуживание стендов;
- возможности автоматизации процесса испытаний.
Выбор состава и вида объектов испытаний. При подготовке к стендовым ресурсным испытаниям осуществляют структурный анализ всей машины, т.е. ее делят на агрегаты, сборочные единицы, сопряжения и детали. Полученную номенклатуру анализируют с точки зрения ожидаемой долговечности и влияния на надежность машины в целом. После этого все составляющие элементы машины делят на требующие стендовых ресурсных испытаний, требующие проведения специальных исследований, а также требующие стендовых испытаний, оставляя оценку их надежности на время эксплуатационных испытаний.
Элементы машины, подлежащие стендовым ресурсным испытаниям, могут быть в виде отдельных деталей, сборочных единиц или агрегатов. Экономичнее, по возможности, проводить стендовые испытания деталей, а не сложных агрегатов.
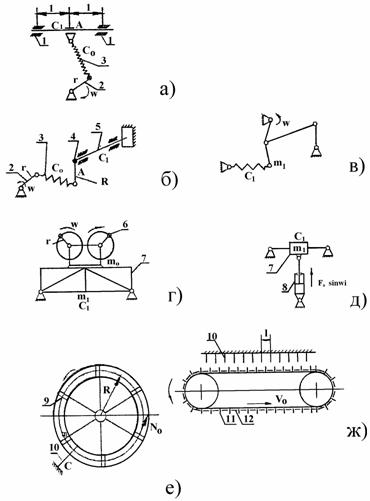
Рис.14.4. Схемы стендов с нагружением переменной нагрузкой при постоянной закономерности изменения усилия воздействия: 1 – подшипники; 2 – кривошип; 3 – упругий шатун; 4 – испытуемая ступица; 5 – торсион; 6 – инерционный вибратор; 7 – испытуемая конструкция; 8 – гидроцилиндр; 9 – испытуемые лопасти; 10 – упругая лопасть; 11 – лента транспортера; 12 – дополнительные грузы; а-ж – виды стендов
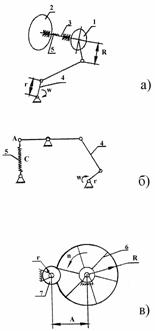
Рис.14.5. Схемы стендов с нагружением переменной нагрузкой при постоянной закономерности изменения переменной: 1 – испытуемая ступица; 2 – маховик; 3 – испытуемый вал с тензорезисторами; 4 – кривошипно-шатунный механизм; 5 – испытуемая пружина; 6 – палец; 7 – валик для торможения; а-в – виды стендов
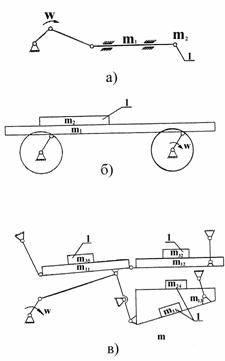
Рис.14.6. Схемы стендов с нагружением силами инерции колеблющихся масс объекта испытаний: с дополнительными грузами (1); а-в – виды стендов
Испытания деталей целесообразно проводить при условии возможности увеличения числа повторностей, при необходимости изучения состояния детали в процессе реализации ее ресурса, так как это невозможно сделать из-за сложности агрегата, в который входит эта деталь. Вместе с тем при испытании детали вне агрегата теряется возможность непосредственного воздействия соседних деталей друг на друга (условия сборки, зазоры, погрешности изготовления).
Рис.14.7. Схемы стендов для нагружения равномерно вращающихся объектов постоянной силой: 1 – шкив; 2 – камера с абразивной средой; 3 – ремень; 4, 5 – рычаги с грузами; 6 – двигатель; 7 – объект испытаний; 8 – тормоз; а-г – виды стендов
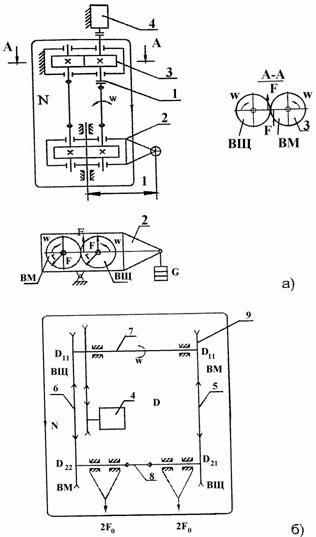
Рис.14.8. Схемы стендов с замкнутым контуром: 1 – муфта; 2 – планетарный нагружатель; 3 – зубчатые колеса; 4 – двигатель; 5, 6 – ремни; 7 – вал; 8 – натяжной вал; 9 – шкивы; а, б – виды стендов
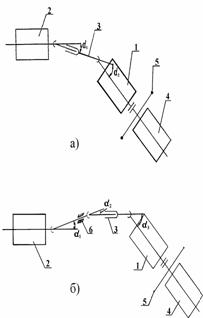
Рис.14.9. Схемы стендов с нагружением силами инерции вращающихся масс при циклическом измерении угловой скорости; а, б – виды стендов
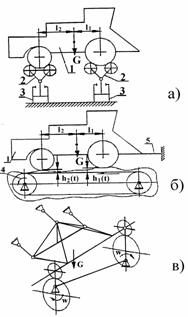
Рис.14.10. Схемы стендов, имитирующих дорожные условия: 1 – испытуемый зерноуборочный комбайн; 2 – роликовая опора; 3 – гидроцилиндры; 4 – опорный транспортер; 5 – растяжки; а-в – виды стендов
Использование результатов, предшествующих исследований и испытаний. Анализ предыдущих испытаний позволяет прогнозировать и уточнять места и виды отказов, значимые для надежности испытуемой детали или сборочной единицы. Создается возможность расширить программу испытаний по тем деталям и сборочным единицам, надежность которых существенно сказывается на надежности агрегата или машины, к которым они принадлежат.
Анализ и обобщение данных об эксплуатационной надежности предшествующих образцов машин или машин-аналогов позволяет построить кривую вероятности распределения основных составляющих нагрузки, схематизировать процессы нагружения, выделить уровни нагруженности, малозначащие в процессе накопления повреждений в испытуемых объектах.
Анализ предшествующих исследований, экспертных оценок и проведенных прочностных расчетов позволяет точнее выбрать условия и режимы нагружения при разработке методики испытания, создать возможность выбора методов ускорения испытаний, а также методов осуществления периодических измерений и проведения технической экспертизы.
Анализ и обощение отказов, полученных предшествующими испытаниями и исследованиями рассматриваемой машины, а также машин-аналогов, во многих случаях позволяет оценить законы распределения показателей надежности. Эти данные используются для выбора объема испытаний и уровня достоверности планируемых ресурсных стендовых испытаний.
14.3.2. Виды и средства ресурсных стендовых испытаний
Виды ресурсных стендовых испытаний определяются разнообразием конструкций, режимов работы и видов отказов элементов СХМ, а также исследовательских и планово-нормативных требований при решении задач управления надежностью.
Виды ресурсных стендовых испытаний можно классифицировать по следующим признакам:
1. По объектам испытаний: полнокомплектные машины; агрегаты; сборочные единицы; детали; натуральные и модельные образцы.
Многие из этих объектов могут быть новыми или проработавшими определенное время, а также отремонтированными.
2. По темпам и нагруженности объектов испытаний: нормальные, ускоренные (по уплотнению времени испытаний или по увеличению нагруженности – форсированные) испытания.
3. По воспроизводимым повреждениям: усталостные разрушения; износ; ударные повреждения; коррозия; потеря устойчивости, реологические повреждения и др.
4. По способу оценки результатов испытаний: сравнительные испытания, при которых оценивается ресурс исследуемого изделия в сравнении с исследованными ранее в реальных эксплуатационных условиях, испытания новых объектов без сравнения с другими.
5. По планам испытаний: полные, проводимые до предельного состояния всех изделий выборки; усеченные или цензурированные, при которых доводится до предельного состояния только назначенное количество изделий выборки или до назначенной наработки; проводимые с заменой или без замены отказавших деталей.
Средства для ресурсных испытаний (стенды) можно классифицировать по следующим признакам:
1) по характеру изменения во времени воспроизводимых нагрузок: статические; циклические в установившемся режиме: циклические, изменяющиеся во времени по блокам программного нагружения; случайные, воспроизводящие реальные эксплуатационные нагрузки; ударные; комбинированные, сочетающие силовое нагружение с тепловым воздействием или воздействием загрязненности окружающей среды;
2) по видам силовозбуждающих механизмов; инерционные, в резонансном режиме силовозбудителя; гидравлические; электродинамические; статические;
3) по степени универсализации имеющегося оборудования: на стандартных стендах; на специальных стендах, созданных для конкретного исследования;
4) по степени автоматизации процессов испытаний: автоматическое воспроизведение циклов нагружения; автоматическая фиксация режимов работы; автоматика выключения стенда при отказах деталей или аварийных ситуациях.
По методам и видам реализации ресурсных стендовых испытаний имеется ряд НТД.
В нормативных документах приведены некоторые данные о методах ускоренных испытаний на надежность, испытаний в условиях эксплуатации и на полигонах, а также ресурсных стендовых испытаниях различных типов сельхозмашин. Изложенным выше классификациям видов и средств стендовых ресурсных испытаний в целом отвечают и действующие ОСТ 23.2.158-86 и ОСТ 23.2.25-81.
14.3.3. Методы оценки показателей надежности при проведении стендовых ресурсных испытаний
При проведении стендовых ресурсных испытаний характерными показателями надежности принято считать:
- вероятность безотказной работы;
- среднюю наработку до отказа (медианное значение);
-
-процентную наработку до отказа.
Эти показатели определяются на базе экспериментально построенных кривых вероятности распределения наработки до отказа объекта испытаний.
При оценке надежности объектов машиностроения применяют ряд вариантов проведения испытаний.
В сельхозмашиностроении и для ЗУК при стендовых ресурсных испытаниях можно рекомендовать применение следующих вариантов планов проведения испытаний:
а) до предельного состояния всей выработки ([NUN]);
б) до заданной наработки независимо от состояния объектов испытания ([NUT], или [NRT], или [NMT]);
в) до наступления
отказов выборки ([NUr], или [NRr], или [NMr]).
Вариант «а» дает наиболее полную информацию, но создает самые длительные по времени испытания. Этот вариант целесообразно применять при оценке норм расхода запасных частей.
Показатели надежности оцениваются двумя методами:
- непараметрическим – при неизвестном математическом законе распределения;
- параметрическим – при известном законе распределения.
Расчет объема испытаний. Перед проведением стендовых ресурсных испытаний после выбора плана испытаний ([NUN], [Nur], [NUT]) решается вопрос об объеме испытаний, т.е. определяется число повторностей опыта, которое удовлетворяет требованиям точности получаемых результатов.
Исходными данными для расчета объема испытаний служат следующие (табл.14.1):
а) доверительная вероятность
, определяющая долю случаев, при которых оценка показателей надежности, полученная с данной относительной погрешностью, будет правильной в
случаях из ста.
Таблица 14.1
Рекомендуемые значения
и 
Назначение объекта испытаний |

|

|
Объекты, влияющие на безотказность |
0,95…0,99 |
0,05 |
Базовые объекты, определяющие надежность изделия |
0,80…0,90 |
0,15…0,20 |
Объекты, обслуживающие внешний вид изделия, комфортабельность |
0,75…0,80 |
0,20…0,25 |
б) относительная ошибка
соответствующего показателя надежности.
Предельная ошибка рассчитывается из выражений:
; (14.12)
для позитивных показателей надежности ведется оценка снизу:
; (14.13)
для негативных показателей надежности ведется оценка сверху:
, (14.14)
где
- полученное значение показателя надежности;
- нижняя и верхняя доверительные границы показателя надежности;
в)
-коэффициент вариации распределения показателей надежности
; (14.15)
где
- среднеквадратическое отклонение;
- математическое ожидание;
г) вид закона распределения показателя надежности;
д) план проведения испытаний.
Определение объема испытаний при плане [NUN] ведется для средней наработки до отказа, а для оценки
-процентной наработки определение объема
испытаний ведется для средней наработки до отказа по табл. 4, 5, 6, по которым вместо
находят значение
. Определение
ведется по следующим формулам:
- для нормального распределения
, (14.16)
где
- функция Лапласа – функция нормированного нормального распределения;
- относительная продолжительность испытаний;
- продолжительность испытаний;
- среднее значение времени отказов;
- для распределения Вейбулла и экспоненциального распределения:
, (14.17)
где
- гамма функция;
- параметр распределения Вейбулла
;
- для логнормального распределения
; (14.18)
Определение объема испытаний при плане [NUR] для
-процентной наработки
ведется по табл.7, 8, 9, по которым вместо
находят значение
, а
находят по одной из формул (14.16)-(14.18).
Определение объема испытаний при плане [NUT] ведется по такой же методике, как и при плане [NUr]. В этом случае, если
не задано, то можно принять значение
и по одной из формул (14.16)-(14.18). Значение
и
находят как для средней, так и
-процентной наработки.
Во всех рассмотренных случаях, если по результатам испытаний коэффициент вариации окажется больше предварительно выбранного значения, то объем испытаний пересчитывается по уточненному значению
и испытания должны быть соответственно продолжены.
Если вид закона распределения случайной величины неизвестен (непараметрические испытания), то объем испытаний, определяющих среднюю наработку до отказа для испытаний на износ выбирается по табл.4, а для испытаний на прочие виды разрушений – по табл.63. Для определения объема испытаний при
-процентной наработке до отказа следует использовать табл.10. При этом необходимо задаться значением
, а по соответствующим
и
определить
.
Первичная обработка экспериментальных данных. Полученные в результате проведенных стендовых ресурсных испытаний материалы представляют ряд значений времени наработки до отказа и цензурирования
объекта исследований. Эти исходные данные обрабатываются в следующем порядке.
Полученный ряд значений
вместе с данными об отказах и цензурировании выстраиваются в вариационный ряд. Этот вариационный ряд делят по интервалам, определяют их частоту. Форма таблицы этой обработки приведена в табл.14.2.
Таблица 14.2
Данные о наработке до отказа
Показатели |
Обозначения |
Числовые значения |
Наработка до отказа |

|

|

|
… |

|
… |

|
Частота отказов |

|

|

|
… |

|
… |

|
Частота цензурирования |

|

|

|
… |

|
… |

|
Сумма отказавшихся и цензурированных объектов |

|

|

|
… |

|
… |

|
Примечания:
1. При плане [NUN]
; при планах [NUr], [NUT]
.
2. Числовые значения
могут быть записаны дискретно, без интервала;
- количество объектов испытаний.
Расчет показателей надежности непараметрическими методами. Средняя наработка до отказа (средний ресурс)
определяется в зависимости от плана испытаний.
Для плана [NUN]
. (14.19)
Для планов [NUr], [NUT]
, (14.20)
где
- число объектов испытаний;
- сумма отказавших
цензурированных
объектов до окончания испытаний.
Предполагается, что число цензурированных деталей намного меньше, чем отказавшихся (
).
Функцию распределения отказов можно определить по формуле
,
, (14.21)
где
- количество работоспособных объектов испытания до
-го отказа в вариационном ряду.
Зависимость (14.21) справедлива и для планов с наличием заметного количества цензурированных объектов, например, при планах [Nur]. В этом случае средняя наработка до отказа (средний ресурс) может быть вычислена по формуле
, (14.22)
где
- время прекращения испытаний в случае цензурирования в последнем числе вариационного ряда;
- время прекращения испытаний в случае наступления отказа, т.е. последний член вариационного ряда содержит отказ;
- значение
или
в последнем члене вариационного ряда;
- процентная наработка
(
-процентный ресурс) независимо от планов испытаний при
, (14.23)
определяется по формуле
, (14.24)
Если
, то
. (14.25)
Нижняя и верхняя доверительные границы
для средней наработки до отказа могут быть определены по следующей формуле независимо от планов испытаний, указанных для (14.19), (14.20):
; (14.26)
, (14.27)
где
- коэффициент, зависящий от объема испытаний и доверительной вероятности.
Расчет показателей надежности параметрическими методами. В случае априорного представления о законе распределения отказов исследуемого объекта можно воспользоваться формулами и таблицами.
В табл.14.3 приведены формулы для оценки показателей надежности параметрическими методами.
Нижняя и верхняя доверительные границы для средней наработки до отказа (среднего ресурса) при параметрических методах оценки определяются также, как и при непараметрических методах и могут быть найдены по формулам (14.26) и (14.27).
Применение методов теории планирования многофакторного эксперимента при стендовых ресурсных испытаниях. На определенных стадиях стендовых ресурсных испытаний возникает необходимость оценить значимость влияния отдельных параметров или факторов объекта испытаний на его долговечность. Например, влияние характера изменения и уровня нагрузки, зазоров в сопряжениях, вид смазки, температуры. При оценке влияния нескольких факторов существенную экономию проведения стендовых ресурсных испытаний создает применение теории планирования многофакторного эксперимента. Применение этой теории позволяет уменьшить число повторностей при проведении стендовых испытаний, и в то же время позволяет оценить значимость нескольких факторов, влияющих на ресурс объекта испытаний, и оценить связь между этими факторами.
Таблица 14.3
Формулы для вычисления показателей надежности по известным законам распределения
Обозначения:
- функция Лапласа;
- гамма-функция;
- квантиль нормального распределения, соответствующий вероятности
.
14.3.4. Режимы стендовых ресурсных испытаний
Режимы испытаний являются средством реализации выбранного метода испытаний. Режимом стендовых ресурсных испытаний называют правила реализации совокупности факторов нагрузки, определяющих физическую сущность разрушения машин и их соединений, а также распределение действия этих факторов за время испытаний. К факторам нагрузки в первую очередь относятся уровни и частота силовых и кинематических нагрузок, состояние среды в нагруженном контакте деталей (смазка, абразив), факторы воздействия внешней среды (температура, влажность, запыленность, агрессивность среды).
Базой для выбора режимов стендовых ресурсов испытаний являются данные об отказах и нагруженности в эксплуатационных условиях объекта исследования и его аналогов, а также данные аналитических расчетов.
Критерием правильности выбора режима стендовых ресурсных испытаний является адекватность видов и интенсивности повреждений и отказов, полученных на стендах и в эксплуатационных условиях.
Основные требования, предъявляемые к выбору режимов стендовых ресурсных испытаний, могут быть сведены к следующим:
- выполнение критерия адекватности отказов;
- информативность – полнота данных о процессах разрушения;
- минимизация сроков проведения испытаний;
- доступность и рентабельность реализации выбранного режима испытания.
Ускорение процессов испытаний. Стендовые ресурсные испытания являются длительным процессом. Поэтому при выборе режимов стендовых ресурсных испытаний возникает вопрос о способах ускорения процессов испытаний.
Пути сокращения продолжительности стендовых ресурсных испытаний выбираются в зависимости от ряда условий и их реализации. Возможны следующие способы ускорения стендовых ресурсных испытаний.
1. Максимальное использование календарного времени. Например, круглосуточное проведение стендовых испытаний без выходных дней, сокращение сроков замены отказавших деталей.
2. Испытания одновременно нескольких (или всех) объектов исследования.
3. Выбор рационального плана испытаний.
4. Форсирование режимов испытания.
Форсирование ведется за счет увеличения уровня действия нагрузки, кинематических или других факторов, а также увеличения времени действия тяжелых режимов. Однако чрезмерная интенсификация режимов может привести к искажению результатов испытаний. Каждый процесс разрушения имеет свою критическую область, при переходе которой происходят качественные его изменения. Ниже приведены примеры, подтверждающие возможность наступления качественных изменений в процессах испытаний.
Для процессов трения после превышения определенного уровня удельных давлений или скоростей скольжения наступают качественно новые процессы износа.
При увеличении температуры выше определенного уровня изменяются свойства смазки, что приводит к изменению эффектов трения.
При заметном увеличении частоты вращения ряда механизмов возникает рост инерционных сил, искажающих напряженное состояние конструкции.
При чрезмерном увеличении нагрузки процесса многоциклового усталостного разрушения превращаются в процессы малоциклового разрушения.
При увеличении нагрузок, вызывающих большие деформации валов, меняется характер разрушения несущих подшипников.
Создание имитационных режимов. При сохранении сопоставимости отказов в имитационных условиях с условиями реальной эксплуатации создается возможность значительно ускорить процессы испытаний. Ниже приведены примеры применяемых имитационных режимов при проведении стендовых ресурсных испытаний:
- Применение форсированных испытаний за счет введения в смазку абразивных составляющих.
- Повышение температуры окружающей среды при испытаниях деталей из полимерных материалов.
- Применение конструкционных материалов – имитаторов. Например, изготовление испытуемой детали из более податливого материала.
- Проведение исследований процессов износа на алюминиевых парах вместо черных металлов.
- Нанесение дополнительных концентратов напряжений для ускорения процессов усталостного разрушения.
Сокращение времени испытаний при использовании расчетных методов. Ниже приведены приемы применения этого способа.
Если известен закон распределения отказов, то можно испытать небольшое количество объектов, чтобы определить параметры закона распределения и аналитически рассчитать ресурс.
Если известна кривая усталостной прочности детали, то можно провести испытания по усеченному режиму, опуская те составляющие спектра нагрузки, которые вызывают напряжения, не превышающие 40% от реального предела выносливости.
Если известны пределы чувствительности параметров износа кинематической пары (удельное давление, скорость скольжения), то можно провести испытания по усеченному режиму, опуская те составляющие спектра нагрузки, которые не превышают 10-15% от допустимого уровня нагрузки при длительности процесса, составляющей не более 25% от общего времени эксплуатации.
Проверка выбранных режимов. При разработке новых режимов стандартных ресурсных испытаний важно проверить правильность развития повреждений и отказов в исследуемом объекте. Поэтому на первой стадии внедрения новых испытаний рекомендуется провести поисковые опыты в виде одной или нескольких повторностей, позволяющих оценить правильность выбранных режимов с использованием соответствующих измерительных средств и приборов (например, тензометрирования).
При проведении уже отработанных режимов стендовых испытаний необходимо также ввести контроль происходящих процессов разрушения. При фиксации только моментов отказов теряется большой объем ценной информации, а в некоторых случаях можно сделать даже ошибочные заключения.
Важное значение для оценки правильности выбранных режимов стендовых испытаний является также изучение видов повреждений и отказов, полученных после окончания испытаний.
14.4. Оценка показателей назначения
Сравнительные стендовые испытания двухъярусных четырехрешетных и одноярусных трехрешетных модулей. Сравнительные стендовые испытания решетных модулей (см. рис.11.28) в режиме предварительной очистки зерна пшеницы проведены на специальной установке в лаборатории сепарации ДГТУ.
Исходный зерновой материал: пшеница «Северодонская», влажность 14%, содержание дробленых половинок зерна 1,43%, щуплого зерна 9,35%, семян сорняков 0,96%, мелких сорных примесей 0,37%, крупных сорных примесей 1,83%, дробленой соломки 0,35%.
Классический двухъярусный решетный модуль оснащался решетными полотнами длиной каждое 990 мм, а одноярусный трехрешетный - решетными полотнами длиной каждое 790 мм. При этом решето N1 – с рабочим размером продолговатых отверстий □3,2 мм, N2 - □4,0 мм, N5 - Æ2,5 мм, N6 - Æ2,5 мм. Решета одноярусного трехрешетного модуля: решето N5 - Æ2,5 мм, решето N1 - □3,2 мм, решето N2 - □4,0 мм.
Кинематические параметры решетных модулей одинаковы и постоянны:
=7,17 с-1 (430 мин-1),
=80,
=8 мм.
Результаты стендовых испытаний, усредненные по трем повторностям, представлены на рис.14.11-14.14.
Выявлено, что при заданном интервале вариации подач
зернового материала (см. рис.14.11-14.14) агропоказатель
3% (содержание сорных примесей
в очищенном зерне) выполняется. Исходя из этого величина производительности сравниваемых решетных станов оценивалась по второму агропоказателю
0,05%.
Для этих условий (см. рис.14.11, 14.13) производительность одного двухъярусного решетного модуля 4,72 кг/(м×с) и одного трехрешетного модуля 5,12 кг/(м×с).
Прирост производительности одного трехрешетного модуля на 8,47% при одинаковых площадях зерновых решетах N1 и N2 определяется рациональной компоновкой трехрешетного модуля, при которой на подсевном решете N5 происходит процесс «сегрегации», улучшающий полноту просевания зерна на последующих решетах N1 и N2.
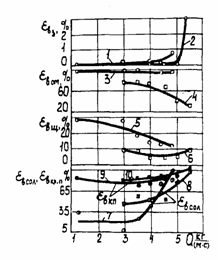
Рис.14.11. Зависимость полноты выделения
из зернового материала
-х компонентов от его подачи
и схемы решетных модулей в режиме предварительной очистки:
зерна пшеницы,
- мелких сорных примесей,
- щуплого зерна,
- дробленой соломки,
- крупных сорных примесей; 1, 3, 5, 7, 9 – один двухъярусный решетный модуль; 2, 4, 6, 8, 10 – один трехрешетный модуль
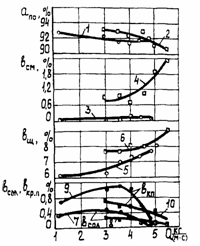
Рис.14.12. Зависимость содержания
-х компонентов в очищенном зерне от подачи
зернового материала и схемы решетного модуля в режиме предварительной очистки зерна пшеницы:
- мелких сорных примесей,
- щуплого зерна,
- дробленой соломки,
- крупных примесей,
- чистота зерна; 1, 3, 5, 7, 9 – один двухъярусный решетный модуль; 2, 4, 6, 8, 10 – один трехрешетный модуль
Например, при постоянной подаче 3,5 кг/(м×с) зернового материала на сравниваемые решетные модули полнота выделения из него: мелких сорных примесей на одном двухъярусном решетном модуле
=79% на одном трехрешетном -
=68% (снижение на 13,92% за счет уменьшенной в 2,5 раза площади подсевного решета); щуплого зерна на двухъярусном решетном модуле
=20%, на одном трехрешетном -
=6,66% (снижение в 3 раза, что, несомненно, положительно, так как уменьшает выход фуражных отходов в сорные отходы); соломистых примесей на двухъярусном модуле
=23%, на одном трехрешетном
=47% (рост в 2,04 раза); крупных примесей на двухъярусном модуле 75,5%, на одном трехрешетном -
=81,5% (рост на 7,95%).
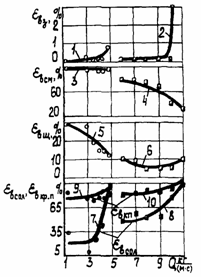
Рис.14.13. Зависимость полноты выделения
из зернового материала
-х компонентов от его подачи
и схемы решетных модулей в режиме предварительной очистки:
- зерна пшеницы,
- мелких сорных примесей,
- щуплого зерна,
- дробленой соломки,
- крупных сорных примесей, 1, 3, 5, 7, 9 – один двухъярусный решетный модуль; 2, 4, 6, 8, 10 – два трехрешетных модуля
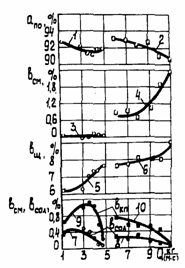
Рис.14.14. Зависимость содержания
-х компонентов в очищенном зерне от подачи
зернового материала и схемы решетных модулей в режиме предварительной очистки:
- мелких сорных примесей,
- щуплого зерна,
- дробленой соломки,
- крупных сорных примесей,
- чистота зерна; 1, 3, 5, 7, 9 – один двухъярусный решетный модуль; 2, 4, 6, 8, 10 – два трехрешетных модуля
Причиной роста полноты выделения из зернового материала на трехрешетном модуле соломистых и крупных сорных примесей следует считать рациональную компоновку решет в ярусе: на первом подсевном решете активно протекают внутрислоевые процессы, обеспечивающие всплывание в зерновом слое компонентов с малой плотностью и высокими коэффициентами внутреннего трения, что подготавливает зерновой материал к сепарации на решетах N1 и N2 (см. рис.11.28).
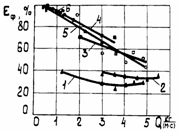
Рис.14.15. Изменение величины критерия эффективности сепарации
зерна пшеницы на решетных модулях от подачи
зернового материала, схемы решетного модуля и вида очистки зерна: предварительная очистка двухъярусным (1) и одним одноярусным трехрешетным (2) модулем; первичная очистка двухъярусным (3) и одним одноярусным (4) модулем; семенная очистка двухъярусным (5) и одним одноярусным трехрешетным (6) модулем
Рост эффективности сепарации в режиме предварительной очистки зерна пшеницы одноярусным трехрешетным модулем показан и значительным увеличением критерия
эффективности сепарации (рис.14.15).
Производительность МПО, ос-нащенных двумя классическими двухъярусными решетными модулями для условий эксперимента при их ширине 990 мм – 32,62 т/ч (общая площадь решет в модуле – 7,84 м2). При использовании в МПО двух трехрешетных одноярусных модулей – 36,86 т/ч (прирост производительности на 12,99%); общая площадь решет в ярусе 4,69 м2). При использовании четырех трехрешетных ярусов – 70,77 т/ч (прирост в 2,17 раз; общая площадь решет в ярусе 9,38 м2).
Оценены показатели сепарации (см. рис.14.16, 14.17) сравниваемых решетных модулей в режиме первичной (продовольственной) очистки исходного зернового материала.
Проведен анализ величин удельной просеваемости зерна через решета с продолговатыми отверстиями и заданное количество и качество выходных фракций при первичной очистке зерна пшеницы. Выявлено, что для проведенных испытаний содержание в очищенном зерне сорных примесей для обеих схем решетных модулей удовлетворяет агротребованиям
.
Оценка производительности одного двухъярусного и одного одноярусного трехрешетного модуля проведена по условиям выполнения агротребований на потерю зерна пшеницы сходом с зерновых решет (см. рис.11.28, решето N2)
и на содержание в очищенном зерне зерновых примесей
.
Установлено, что для заданных агротребований производительность одного двухъярусного решетного модуля 1,84 кг/(м×с) (6,62 т/ч), одного и двух трехрешетных модулей соответственно – 1,62 кг/(м×с) (5,87 т/(м×ч)) и 3,25 кг/(м×с) (11,7 т/(м×ч)).
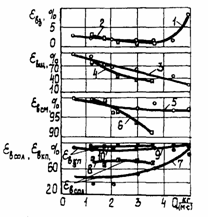
Рис.14.16. Зависимость полноты выделения
из зернового материала
-х компонентов от его подачи
и схемы решетных модулей в режиме очистки зерна пшеницы продовольственного назначения:
- зерна пшеницы,
- мелких сорных примесей,
- щуплого зерна,
- дробленой соломки,
- крупных сорных примесей; 1, 3, 5, 7, 9 – один двухъярусный решетный модуль; 2, 4, 6, 8, 10 – один трехрешетный одноярусный модуль
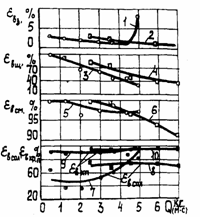
Рис.14.17. Зависимость полноты выделения
из зернового материала
-х компонентов от его подачи
и схемы решетных модулей в режиме очистки зерна пшеницы продовольственного назначения:
- зерна пшеницы,
- мелких сорных примесей,
- щуплого зерна,
- дробленой соломки,
- крупных сорных примесей; 1, 3, 5, 7, 9 – один двухъярусный решетный модуль; 2, 4, 6, 8, 10 – два трехрешетных одноярусных модуля
Для такой производительности чистота зерна, очищенного одним двухъярусным решетным модулем, 97,4%, двумя трехрешетными модулями – 98% (прирост на 0,62%). Содержание в зерне, очищенном двухъярусном решетным модулем, соломистых примесей 0,306%, крупных примесей – 0,40%, а в зерне, очищенном двумя трехрешетными модулями, соответственно 0,150% (снижение в 2,4 раза) и 0,203% (снижение в 2 раза).
При одинаковой подаче зернового материала
-3 кг/(м×с) на один двухъярусный решетный модуль и на два трехрешетных модуля чистота очищенного ими зерна пшеницы соответственно 95,6% и 98,2% (рост на 2,72%), содержание в очищенном зерне щуплого зерна соответственно 3,6% и 1,73% (снижение в 2,8 раз), соломистых примесей соответственно 0,207% и 0,150% (снижение в 1,36 раз), крупных сорных примесей 0,39% и 0,203% (снижение в 1,92 раза).
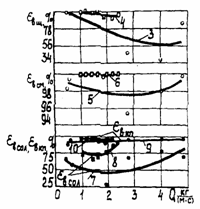
Рис.14.18. Зависимость полноты выделения
из зернового материала
-х компонентов от его подачи
и схемы решетных модулей в режиме семенной очистки зерна пшеницы:
- зерна пшеницы,
- мелких сорных примесей,
- щуплого зерна,
- дробленой соломки,
- крупных сорных примесей, 1, 3, 5, 7, 9 – один двухъярусный решетный модуль; 2, 4, 6, 8, 10 – два трехрешетных одноярусных модуля
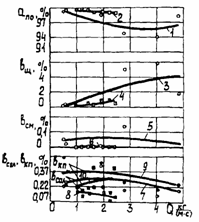
Рис.14.19. Зависимость содержания
-х компонентов в очищенном зерне от подачи
зернового материала и схемы решетных модулей в режиме семенной очистки зерна пшеницы:
- мелких сорных примесей,
- щуплого зерна,
- дробленой соломки,
- крупных примесей,
- семян пшеницы (чистота зерна); 1, 3, 5, 7, 9 – один двухъярусный решетный модуль; 2, 4, 6, 8, 10 – два трехрешетных одноярусных модуля
Анализ результатов параметрической оптимизации решетных модулей (см. гл.11) с учетом требований к выходным фракциям позволил выбрать рациональные параметры решет в трехрешетном одноярусном решетном модуле применительно к зерноочистительным машинам семенной очистки зерна: решето N5 - □1,7 мм; решето N6 - □2,2 мм; решето N2 - □3,2 мм (см. рис.11.28); длина каждого решета в ярусе 790 мм.
Двухъярусный решетный модуль оснащался решетными полотнами длиной каждое 990 мм с рабочими размерами отверстий: решето N1 - □3,0 мм, N2- □3,4 мм, N5 - □2,0 мм, N6 - □2,2 мм. Кинематические параметры сравниваемых модулей постоянны:
=60,
=8 мм,
=7,17 с-1 (430 мин-1).
Исходный зерновой материал: пшеница «Северодонская», влажность
=14%, содержание щуплого зерна 8%, сора мелкого 2,0%, дробленной соломки 0,5%, крупных сорных примесей 4%. Результаты стендовых испытаний, усредненные по трем повторностям, представлены на рис.14.18; 14.19 (чистота зерна
без учета половинок зерна).
Выявлено, что для выполнения агропоказателя по чистоте очищенного зерна производительность одного классического двухъярусного решетного модуля
=1,08 кг/(м×с) (3,88 т/(м×ч), а одного трехрешетного одноярусного модуля
=1,22 кг/(м×с) (4,392 т/(м×ч), прирост производительности на 12,96%.
Установлено, что при равной подаче зернового материала, например
=1 кг/(м×с), чистота зерна, очищенного одним трехрешетным модулем 99%, а двухярусным модулем 98,2%, при этом содержание в зерне, очищенном трехрешетным модулем, соломистых примесей меньше, чем у эталона в 2,07 раза (соответственно 0,13% и 0,27%), крупных сорных примесей – в 1,28 раз (соответственно 0,29% и 0,37%).
Рост эффективности семенной очистки зерна пшеницы на одноярусном трехрешетном модуле определен и величиной критерия эффективности (см. рис.14.15).
Производительность зерноочистительной машины с двумя двухъярусными решетными модулями 2,16 кг/(м×с) (7,77 т/(м×ч), а с четырьмя трехрешетными модулями – 4,88 кг/(м×с) (17,56 т/(м×ч).
Результаты проведенных стендовых исследований:
1. Установлена технологическая эффективность использования одноярусных трехрешетных модулей в зерноочистительных машинах и агрегатах.
2. Определено, что использование двух одноярусных трехрешетных модулей по сравнению с серийным двухъярусным четырехрешетным модулем повышает в 2,17 раз производительность предварительной, в 1,77 раз первичной (базисные кондиции продовольственного назначения) и в 2,25 раз семенной очистки зернового материала за счет рациональной компоновки решет, соотношения площадей подсевных и зерновых решет, тонкослойной сепарации и обеспечения условий для активного процесса расслоения фракций в зерновом слое.