Технология получения продукции сельского хозяйства, помимо операций по возделыванию и уборке сельскохозяйственных культур, включает операции доставки, первичной переработки и хранения продукции. Поточные технологические линии (ПТЛ) формируются для уборочно-транспортных (уборка зерновых, закладка силоса и сенажа, сбор овощей и фруктов) и транспортно-распределительных (внесение удобрений, сев, защита растений) операций, а также при групповой организации сельскохозяйственных работ. Неправильная организация взаимодействия агрегатов приводит к снижению производительности всей ПТЛ, увеличению количества агрегатов в ПТЛ, повышению себестоимости продукции, неоправданным потерям урожая. Для эффективной организации взаимодействия, агрегаты должны обладать закладываемыми при проектировании высокими коммуникативными свойствами: малым временем передачи продукта между рабочими, транспортными и вспомогательными агрегатами и машинами; адаптивностью к агрегатам разного типа; лёгкостью маневрирования при подготовке передачи продукта; малой трудоёмкостью подготовительно заключительных операций при передаче продукта. Поэтому для создания эффективной техники конструктору необходимо владеть вопросами организации эффективного взаимодействия агрегатов в ПТЛ [45].
6.1. Взаимодействие агрегатов при групповой форме организации работ
Групповой называется организация работ, при которой на одном поле, в одном загоне работает несколько агрегатов.
Организуют групповую работу, прежде всего, на операцию с агросроком, который меньше выработки агрегата за это время на данном поле. Кроме того, дополнительными основаниями организации групповой работы агрегатов являются административно-организационные факторы: возможность оперативного маневрирования имеющимися мощностями; концентрация средств ремонта и обслуживания техники; концентрация средств организации питания, отдыха и бытового обслуживания; обеспечение эффективной работы не квалифицированных механизаторов, копирующих режимы работы наставника во главе группы.
Однако производительность группы будет меньше суммы расчётных производительностей отдельных агрегатов. Эта разница вызвана потерями времени работы агрегатов на взаимодействие в группе. Наиболее распространённая форма потери времени в группе – ожидание. Ожидание при последовательном заезде агрегатов в загон, ожидание в загоне при отказе впереди идущего агрегата, ожидание при технологическом обслуживании агрегатов и т.п.
Дополнительные потери времени на ожидание возникают при групповой организации работ разнотипных агрегатов. Такие агрегаты имеют различную оптимальную скорость в загоне, разное время маневрирования на разворотах, разную утомляемость механизаторов, разную периодичность обслуживания агрегатов.
При групповой организации работ, когда выполнение операции связано с непосредственным взаимодействием рабочих агрегатов с машинами обслуживания (разгрузка, загрузка, заправка), потери времени на ожидание tож будут обязательны, если время взаимодействия tвз рабочего агрегата и обслуживающей машины будет больше отношения времени рабочего цикла tраб агрегата к n – их количеству в группе.
. (6.1)
Время рабочего цикла tраб для уборочно-транспортных и транспортно-распределительных операций может быть рассчитано
, (6.2)
где Е (*) – целая часть от (*); W – вместимость бункера рабочей машины, м3; r - плотность вносимого или собираемого продукта, кг/м3; j - коэффициент заполнения бункера рабочей машины, для большинства сельхозмашин значение j колеблется от 0,7 до 0,9; В – ширина захвата агрегата, м; Vр – рабочая скорость агре- гата, км/ч; G - норма внесения или урожайность, кг/га; lгон – длина гона при работе агрегата, м; tпов - время, затрачиваемое агрегатом на повороты и развороты при работе в загоне, ч; tхх - время, затрачиваемое агрегатом на холостой пробег к обслуживающей машине, ч.
Время поворота tпов агрегата приближённо может быть рассчитано
, (6.3)
где Vпов – скорость маневрирования агрегата при поворотах, км/ч; К1 – коэффициент, равный 1,2 для агрегатов, приводимых от вала отбора мощности и 1,1 для прочих агрегатов.
Время холостого пробега tхх агрегата приближенно будет равно
, (6.4)
где Vхх - скорость агрегата на холостом ходу, км/ч; К2 – коэффициент, равный 1 для разбрасывателей удобрений и 1,5 для остальных агрегатов.
Время взаимодействия tвз рабочего агрегата и обслуживающей машины будет включать: время передачи продукта tппр; время подготовки к передаче tппр1; время завершения передачи tппр2. Время tппр, tппр1, tппр2, составляющие tвз, наряду с характеристиками совместимости являются основными параметрами коммуникабельности агрегата, закладываются конструктором при проектировании.
Очевидно, ограниченная коммуникабельность и низкая надёжность агрегатов способны свести на нет все преимущества групповой организации работ.
6.2. Прямоточная организация работы агрегатов на уборочно-транспортных и транспортно-распределительных операциях
Организация взаимодействия машинно-тракторных агрегатов и машин на транспортно-распределительных и уборочно-транспортных операциях, при которой на рабочие агрегаты (изменяющие потребительские свойства агрофона, продукта) возложены функции доставки рабочего материала «склад – поле», называется прямоточной организацией.
Сфера применения прямоточной организации взаимодействия агрегатов – операции с большим агросроком, для выполнения которых в парке хозяйства может быть сформировано избыточное количество агрегатов, и операции, у которых транспортирование занимает много меньше времени, чем работа на поле. Такую организацию, чаще других, применяют при внесении жидких органических удобрений под основную обработку почвы, при кормлении крупного рогатого скота измельчённой зелёной массой, смесями грубых и сочных кормов на открытых площадках прицепными и самоходными кормораздатчиками и раздатчиками-смесителями, при малообъёмном внесении химикатов. Схема организации взаимодействия агрегатов и машин при прямоточной организации работы ПТЛ приведена на рис. 6.1. Преимуществами такой организации является идеальное взаимодействие между транспортным и рабочим звеном потока. Недостатком – использование рабочих машин на транспортных операциях, существенно увеличивающее время цикла рабочей машины.
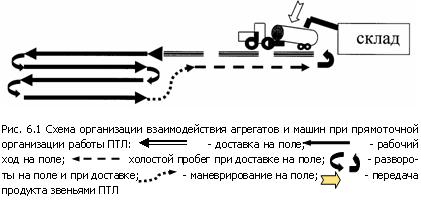
Прямоточная организация взаимодействия звеньев ПТЛ возможна в хозяйстве, когда
, (6.5)
где S – площадь культуры в хозяйстве, для обработки которой формируется ПТЛ, га; АС - агросрок на обработку культуры, дни; ТР – продолжительность работы агрегатов в день, ч; niпарк – количество машин i-го типа для выполнения операции в парке хозяйства; Wi – вместимость бункера машин i-го типа, м3; tiЦ – время цикла на этой операции агрегатов с машинами i-го типа, ч; ji – коэффициент заполнения бункера для машин i-го типа; tiСМ – коэффициент использования времени смены для агрегатов на базе машин i-го типа.
Время цикла tiц агрегатов с машинами i-го типа на этой операции будет
, (6.6)
где tiдст – время, затрачиваемое агрегатом на доставку материала «склад-поле», ч; – tiраб - время, затрачиваемое агрегатом на работу в загоне, ч; tiхх - время, затрачиваемое агрегатом на холостой переезд «поле – склад», ч; tiразв – время, затрачиваемое агрегатом на повороты и развороты, ч; tiман - время, затрачиваемое агрегатом i-го типа на маневрирование по полю, ч; tiвз – время, затрачиваемое агрегатом на загрузку (разгрузку) на складе, ч; tiож - время, затрачиваемое агрегатом на ожидание загрузки (разгрузки) у склада, ч.
Время tiдст, затрачиваемое агрегатом на доставку материала «склад-поле», может быть рассчитано
, (6.7)
где lдст - расстояние доставки материала «поле – склад», км; ViТР - средняя скорость агрегата i-го типа при транспортировании, км/ч.
Время tiраб, затрачиваемое агрегатом i-го типа на работу в загоне, может быть рассчитано
, (6.8)
где Viраб – скорость агрегата на поле при выполнении операции, км/ч.
Время tiхх, затрачиваемое агрегатом i-го типа на холостой переезд «поле – склад», может быть рассчитано
, (6.9)
где Viхх – скорость агрегата на холостом ходу при доставке материала «поле – склад», км/ч.
Время tiразв, затрачиваемое агрегатом на повороты и развороты на поле, может быть рассчитано
, (6.10)
где Viпов – скорость агрегата на холостом ходу при поворотах на поле, км/ч; К1 – коэффициент, описанный в п.6.1 , формула (6.3).
Время tiман, затрачиваемое агрегатом i-го типа на маневрирование по полю, может быть рассчитано
, (6.11)
где Viман – скорость агрегата на холостом ходу при переездах по по- лю, км/ч; К2 – коэффициент, описанный в п. 6.1 , формула (6.4).
Время tiвз, затрачиваемое агрегатом на загрузку (разгрузку) на складе, может быть рассчитано
, (6.12)
где Qi – производительность загрузки (разгрузки) агрегата, т/ч; К3 – коэффициент, учитывающий потери времени на подготовку и завершение загрузки (разгрузки) агрегата.
Условия возникновения времени tiож, затрачиваемого агрегатом на ожидание загрузки (разгрузки) у склада, и расчёты компонент этого времени были рассмотрены в п.6.1, зависимости (6.1) – (6.4).
Анализ приведенных зависимостей (6.5)-(6.12), описывающих закономерности прямоточной организации взаимодействия агрегатов ПТЛ, показывает, что для этой организации ПТЛ необходимо формировать агрегаты, включающие машины с большой вместимостью бункера, высокими транспортной скоростью и производительностью при погрузке (разгрузке).
6.3. Перегрузочная организация работы агрегатов на уборочно-транспортных и транспортно-распределительных операциях
Организация взаимодействия машинно-тракторных агрегатов и машин на транспортно-распределительных и уборочно-транспортных операциях, при которой рабочие машины загружаются (разгружаются) непосредственно на поле или на краю поля транспортными агрегатами, связывающими эту рабочую машину со складом, называется перегрузочной.
Сфера применения перегрузочной организации взаимодействия агрегатов в ПТЛ очень широка. Это операции с небольшим, ограниченным агросроком, большими площадями обработки, большими объёмами перевозки продукта. Из-за больших объёмов и коротких сроков работ, как правило, не бывает избыточного количества агрегатов в парке хозяйств. Перегрузочную организацию применяют при уборке зерновых, севе, внесении минеральных удобрений, защите растений и т.п.
Схема взаимодействия агрегатов в ПТЛ при перегрузочной организации уборочно-транспортных операций представлена на рис. 6.2.
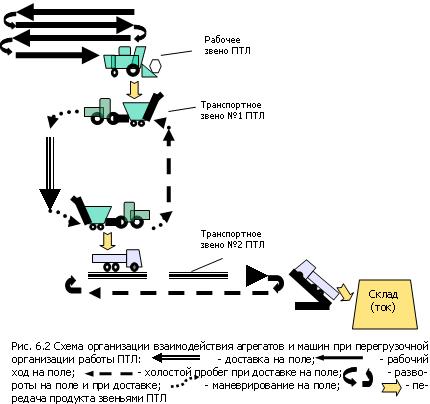
На приведенной схеме (см. рис.6.2) рабочее звено ПТЛ обеспечивает два последовательно работающих транспортных звена: транспортное звено №1 - передачу материала от рабочей машины на край поля; транспортное звено №2 - доставку материала «поле – склад». Вызвано это тем, что машины (агрегаты) транспортного звена №2 обладают высокой производительностью при доставке, но не могут выезжать на поле из-за экологических ограничений (превышение допустимого удельного давления на почву). Агрегаты (машины) транспортного звена №1 имеют меньшую производительность при доставке «поле – склад», но соответствуют экологическим нормам по удельному давлению. Совместная работа транспортных звеньев № 1 и № 2 обеспечивает наименьшие потери времени агрегатов рабочего звена ПТЛ. Преимуществом такой организации является возможность выполнения значительных объёмов работ при малом количестве рабочих машин в парке хозяйства. В сравнении с прямоточной организацией работ части времени цикла (tiдст, tiхх, а в нашем примере и tiман) от рабочих агрегатов передаются универсальным и специальным транспортным агрегатам (машинам).
К недостаткам перегрузочной организации работы ПТЛ относятся неизбежные потери времени агрегатами на ожидание взаимодействия (перегрузки). Для сокращения потерь времени рабочими агрегатами на ожидание взаимодействия создаётся избыточность агрегатов транспортных звеньев ПТЛ.
Перегрузочная организация взаимодействия агрегатов в ПТЛ на уборочно-транспортных и транспортно-распределительных операциях описывается уравнением «идеальной организации взаимодействия». Это уравнение устанавливает равенство произведений времени цикла на количество агрегатов для всех звеньев ПТЛ.
, (6.13)
где t1Ц, t2Ц,…, tiЦ – время цикла агрегатов соответственно в 1-м, 2-м, …, i–м звене ПТЛ, ч; N1, N2,…, Ni – количество агрегатов соответственно в 1-м, 2-м, …, i–м звене ПТЛ.
Время цикла t1Ц, t2Ц,…, tiЦ агрегатов в 1-м, 2-м, …, i–м звене ПТЛ существенно отличаются по структуре.
Время цикла t1Ц рабочего агрегата включает
t1Ц = t1раб + t1 разв + t1ман + t1вз + t1ож , (6.14)
где t1раб - время, затрачиваемое агрегатом на работу в загоне, ч; t1разв – время, затрачиваемое агрегатом на повороты и развороты в загоне, ч; t1ман - время, затрачиваемое рабочим агрегатом на маневрирование по полю, ч; t1вз – время, затрачиваемое агрегатом на перегрузку материала при взаимодействии с агрегатом транспортного звена, ч; t1ож - время, затрачиваемое агрегатом на ожидание перегрузки материала при взаимодействии с транспортным звеном, ч.
Значения времени t1раб, t1 разв, tiман, tiвз может быть рассчитано соответственно по зависимостям (6.8), (6.10), (6.11), (6.12). Время tiож, затрачиваемое агрегатом на ожидание перегрузки материала при взаимодействии с транспортным звеном, возникает, если, вопреки (6.13)
, (6.15)
или (и)
. (6.16)
Время цикла t2Ц транспортного агрегата включает
t2Ц =t2дст + t2хх + t2ман+ t2вз1 + t2ож1 + t2вз3 + t2ож3 , (6.17)
где t2дст - время, затрачиваемое агрегатом 2-го звена на доставку материала «поле - склад», ч; t2хх - время, затрачиваемое агрегатом 2-го звена на
холостой переезд «склад –поле», ч; t2ман - время, затрачиваемое этим агрегатом на маневрирование по полю, ч; t2вз1 – время, затрачиваемое агрегатом на
перегрузку материала при взаимодействии с агрегатом рабочего (1-го) звена, ч; t2ож1 - время, затрачиваемое агрегатом на ожидание загрузки (разгрузки)
рабочим агрегатом (агрегатом 1-го звена) на поле, ч; t2вз3 – время, затрачиваемое агрегатом на перегрузку материала при взаимодействии с погрузочно-разгрузочными
средствами склада или следующего транспортного звена, ч; t2ож3 - время, затрачиваемое агрегатом на ожидание загрузки (разгрузки) у склада или взаимодействия со
следующим транспортным звеном, ч.
Значения времени t2дст , t2хх , t2ман, t2вз1 , t2 вз3 может быть рассчитано соответственно по зависимостям (6.7), (6.9), (6.11), (6.12). Время t2ож1 и t2ож2,
затрачиваемое агрегатом на ожидание перегрузки материала при взаимодействии с разгрузочно-погрузочными средствами склада или агрегатами следующего транспортного звена, возникает, если, как и для агрегатов рабочего звена, вопреки (6.13)
,
, (6.18)
или (и)
,
. (6.19)
Время цикла tiЦ погрузочно-разгрузочного агрегата, работающего на складе, будет включать
tiЦ = t i вз(i-1) + t i ож( i-1) , (6.20)
где t i вз(i-1) - время на взаимодействие с транспортным агрегатом i-1 –го звена, ч; t i ож(i-1) - время ожидания этого взаимодействия, ч.
Рассчитываются t i вз(i-1) и t i ож(i-1) аналогично таким же компонентам времени цикла t2Ц агрегатов транспортного звена (см. зависимости (6.12), (6.15), (6.16)).
Анализ зависимостей (6.13)-(6.20), описывающих закономерности перегрузочной организации взаимодействия агрегатов ПТЛ, показывает, что для этой организации необходимо формировать агрегаты, включающие машины с высокой коммуникабельностью, позволяющие производить перегрузку материала широкому кругу агрегатов различного типа и с высокой производительностью.
6.4. Перевалочная организация работы агрегатов на уборочно-транспортных и транспортно-распределительных операциях
Перевалочной называется организация взаимодействия машинно-тракторных агрегатов (МТА) и машин на уборочно-транспортных и транспортно-распределительных операциях, при которой для загрузки (разгрузки) рабочих машин на краю поля организуется временный склад-накопитель с погрузочно-разгрузочным звеном, а транспортное звено, связывающее временный склад-накопитель и постоянный (основной) склад хозяйства, работает независимо от рабочего звена, вне агросрока на выполнение операции.
Перевалочная организация взаимодействия МТА и машин на уборочно-транспортных и транспортно-распределительных операциях применяется при работе с материалами, допускающими временное хранение и перевалку без существенных потерь и ухудшения потребительских свойств. Это транспортно-распределительные операции при внесении твёрдых органических удобрений под основную обработку почвы по парам, внесении жидких комплексных удобрений, при крупнокапельной химической защите растений и т.п. Это уборочно-транспортные операции при уборке картофеля, свёклы, бахчевых и огородных культур, уборке незерновой части урожая злаковых, заготовке сена и т.п. Схема взаимодействия агрегатов в ПТЛ при перевалочной организации работ приведена на рис. 6.3. Для примера рассмотрена организация взаимодействия агрегатов при внесении твёрдых органических удобрений. В приведенном примере транспортное звено и рабочее звено ПТЛ обслуживаются разными погрузочно-разгрузочными звеньями. Циклы агрегатов в рабочих и транспортных звеньях не увязываются. Количество рабочих агрегатов, как и при прямоточной, и перегрузочной организациях определяется объёмами работ и агросроками, а количество транспортных – определяется допустимыми сроками хранения материалов на временном складе-накопителе.
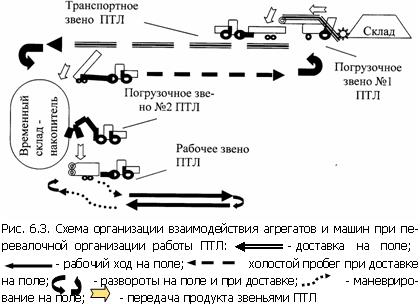
Перевалочная организация взаимодействия агрегатов и машин в ПТЛ подчиняется следующим закономерностям.
Для транспортного звена
, (6.21)
где tТРЦ, tЗАГЦ – время цикла агрегатов соответственно в транспортном и работающем с ним погрузочно-разгрузочном звене ПТЛ, ч; NТР, NЗАГ – количество агрегатов соответственно в транспортном и работающем с ним погрузочно-разгрузочном звене ПТЛ.
Время цикла tТРЦ, tЗАГЦ агрегатов соответственно в транспортном и работающем с ним погрузочно-разгрузочном звене ПТЛ рассчитывается аналогично времени цикла агрегатов транспортного и погрузочно-разгрузочного звена при перегрузочной организации работ (см. п.6.2).
Суммарная производительность агрегатов, привлекаемых к доставке продукта «поле – склад», должна соответствовать выражению
, (6.22)
где S – площадь культуры в хозяйстве, для обработки которой формируется ПТЛ, га; G - норма внесения или урожайность, кг/га; АХР - предельно-допустимый срок хранения материала на временном складе - накопителе, дни; ТР – продолжительность работы агрегатов в день, ч; ТРI – количество типов транспортных агрегатов, которое может быть сформировано в парке; nТРiпарк – количество транспортных агрегатов и машин i-го типа в парке хозяйства; WТРi – вместимость бункера транспортной машин i-го типа м3; tТРiЦ – время цикла транспортных агрегатов с машинами i-го типа, ч; jТРi – коэффициент заполнения бункера для транспортных машин i-го типа; tТРiСМ – коэффициент использования времени смены для транспортных агрегатов на базе машин i-го типа.
Для рабочего звена
, (6.23)
где tРАБЦ, tЗАГЦ – время цикла агрегатов соответственно в рабочем и обслуживающим его погрузочно-разгрузочном звене ПТЛ, ч; NРАБ, NЗАГ – количество агрегатов соответственно в рабочем и обслуживающим его погрузочно-разгрузочном звене ПТЛ.
Время цикла tРАБЦ, tЗАГЦ агрегатов соответственно в рабочем и обслуживающим его погрузочно-разгрузочном звене ПТЛ рассчитываются аналогично времени цикла агрегатов рабочего и погрузочно-разгрузочного звена при перегрузочной организации работ (см. п. 6.3).
Суммарная производительность агрегатов, привлекаемых в рабочее звено при перевалочной организации, должна соответствовать выражению
, (6.24)
где S – площадь культуры в хозяйстве, для обработки которой формируется ПТЛ, га; АС - агросрок на выполнение операции, дни; ТР – продолжительность работы агрегатов в день, ч; РАБI – количество типов рабочих агрегатов, которое может быть сформировано в парке; nРАБiпарк – количество рабочих агрегатов и машин i-го типа в парке хозяйства; WРАБi – вместимость бункера рабочей машин i-го типа м3; tРАБiЦ – время цикла рабочих агрегатов с машинами i-го типа, ч; jРАБi – коэффициент заполнения бункера для рабочих машин i-го типа; G - норма внесения или урожайность, кг/га; tРАБiСМ – коэффициент использования времени смены для рабочих агрегатов на базе машин i-го типа.
В целом перевалочная организация взаимодействия агрегатов и машин в ПТЛ экономичнее прямоточной и перегрузочной. Если позволяет рабочий материал, именно эта организация взаимодействия является предпочтительной. Для повышения эффективности ПТЛ при перевалочной организации работ, проектируемым агрегатам необходимо придавать функции самозагрузки, саморазгрузки. Придание этих функций рабочим и транспортным агрегатам не только снижают капитальные затраты, так как высвобождают агрегаты погрузочно-разгрузочных звеньев, но и повышают производительность, исключая время ожидания для транспортных и рабочих агрегатов.
6.5. Взаимовлияние параметров машинно-тракторных агрегатов в условиях поточно-технологических линий
Для иллюстрации взаимовлияния параметров МТА в условиях ПТЛ построим элементарную имитационную модель уборочно-транспортной операции. В качестве объекта моделирования возьмём ПТЛ уборки зерновых. Для доставки зерна и половы применена перегрузочная организация взаимодействия агрегатов, для соломы – перевалочная, и в данном примере рассматриваться не будет. Схема организации взаимодействия агрегатов приведена на рис. 6.4.
В ПТЛ входит звено комбайнов Дон-1500, выполняющих прямое комбайнирование со сбором половы в прицепную тележку 2ПТС-4. Для разгрузки бункеров комбайнов и доставки зерна на край поля использован транспортный агрегат из трактора Т-150К+ бункера - перегружателя Дон - 20НПП, для доставки зерна на ток - КамАЗ 5320 с прицепом ГКБ 8350. На току имеется разгрузчик автомобилей У15 - УРАГ. Для доставки половы к месту складирования использован транспортный агрегат из трактора МТЗ–80 + тележки 2ПТС-4.
Звено комбайнов убирает озимые урожайностью Gо 45 ц/га на поле в 100га (lгон = 1000 м). Отношение зерна к соломе - 1/1, доля половы и сбоины в соломе – 20% (урожайность по полове G1 = 9 ц/га). На поле сделаны обкосы для разворота комбайнов. Поле разделено прокосами на 4 делянки; расстояние от поля до тока lдст1 – 4 км по грунтовой дороге, расстояние до склада половы (фермы) , lдст2 - 8 км по грунтовой дороге.
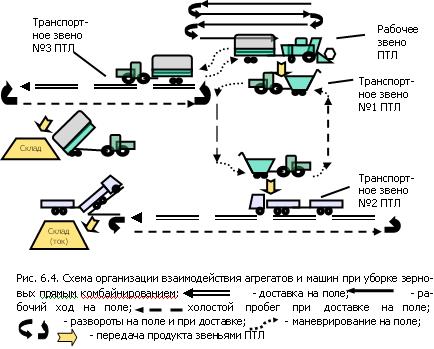
Основные параметры машин и агрегатов ПТЛ следующие.
Рабочее звено – комбайны Дон – 1500 + тележки 2ПТС-4: ширина захвата, Вр – 6м; скорость Vр при прямом комбайнировании – 6 км/ч; вместимость бункера Wр
– 4т зерна; разгрузка бункера tвз1– 1,5 мин; среднее время одного разворота агрегата комбайн + тележка в конце гона и переезда к следующему гону, tрз1 – 5 мин;
вместимость тележки – 40 м3, её грузоподъёмность Wт4 – 4 т; время замены заполненной тележки порожней, tман1 – 7 мин.
Транспортное звено № 1 сформировано из агрегатов - трактор Т-150 + бункер-перегружатель Дон – 20 НПП: вместимость Wт2 бункера перегружателя - 8
т; скорость транспортирования V тр2 – 3,5 км/ч; скорость холостого хода V хх2 – 10 км/ч; время разгрузки, tвз2 – 3 мин.
Транспортное звено № 2 – автомобили с прицепом КамАЗ 5320 + ГКБ 8350: грузоподъёмность Wт3 – 16 т; средняя рабочая скорость по просёлку, V тр3 – 14
км/ч; скорость холостого хода V хх3 – 15км/ч; разгрузка, tвз3 – 10 мин.
Транспортное звено № 3 – агрегаты трактор МТЗ-80 + тележка 2ПТС-4: грузоподъёмность, Wт4 – 4т; средняя рабочая скорость V тр4 – 10 км/ч; скорость
холостого хода V хх3 – 12 км/ч; смена тележки у комбайна, tман1 º tман4 – 7 мин; саморазгрузка у склада, tвз4 – 6 мин.
Для определения количества агрегатов в звеньях ПТЛ рассчитаем время цикла tЦ для агрегатов этих звеньев.
1. Расчёт времени цикла комбайна включает:
- путь заполнения бункера Wр комбайна вместимостью 4т
м;
- время заполнения бункера
мин;
- время на переезды и повороты
мин.
Таким образом, время цикла tЦ 1P рабочего агрегата до разгрузки бункера, без учёта возможного времени ожидания, будет
мин.
После выполнения 5-ти рабочих циклов заполнится тележка половой и будет заменена порожней. Общий tЦ 1 цикл работы агрегата составит
мин.
Технологическая производительность QТ агрегата в рабочем звене, без учёта времени возможного ожидания, составит:
кг/час.
Общая производительность ПТЛ - около 21 т/ч.
2. Расчёт времени цикла бункера-перегружателя включает:
- маневрирование к комбайну №1 – tМАН2-1 = 1,5 мин;
- разгрузку комбайна №1 - tВЗ 1-2 =1,5 мин;
- маневрирование к комбайну №2 – tМАН2-1 = 1,5 мин;
- разгрузку комбайна №2 - tВЗ 1-2 =1,5 мин;
- доставку зерна на край поля, tдст 2 , при среднем расстоянии доставки lдст0 – 500 м
мин;
- разгрузку бункера в автомобиль - tВЗ 2-3 = 3 мин;
- холостой пробег бункера-перегружателя - tхх 2,
мин.
Время работы tЦ 2р бункера-перегружателя, без учёта ожидания, составит
tЦ 2р =2 tМАН2-1 + 2 tВЗ 1-2 + tдст 2 + tВЗ 2-3 + tхх 2 = 20,5 мин.
Таким образом, время tож 2 бункера перегружателя будет 1 мин, общий цикл tЦ 2 будет 21,5 мин., а у комбайна №2 смещение по времени – 3мин. В общем случае это не ожидание.
3. Расчёт времени цикла tЦ3 автомобиля Камаз - 5920 с прицепом ГКБ – 8350 включает:
- время разгрузки бункера в автомобиль - tВЗ 2-3 = 3 мин;
- время ожидания tож 3 автомобилем очередного подхода бункера перегружателя, при tЦ 2 = 21,5 мин, составит tЦ 2 - tВЗ 2-3=18,5 мин;
- время разгрузки бункера в прицеп - tВЗ 2-3 = 3 мин;
- время доставки зерна на ток, tдст 3 , при среднем расстоянии доставки lдст1 – 4 км,
мин;
- время разгрузки автомобиля и прицепа на току - tВЗ3-3=10 мин;
- время tхх 3 холостого пробега автомобиля от тока на край поля
мин.
Время работы tЦ3р автомобиля с прицепом, без учёта ожидания после возвращения на край поля, составит
tЦ3р =2 tВЗ2-3 + tож3 + tдст3 + tВЗ3-3 + tхх3 = 68 мин.
4. Расчёт времени цикла tЦ4 агрегата трактора МТЗ - 80 с тележкой 2ПТС4 включает:
- время подачи тележки от края поля к комбайну, tман4-1 =3 мин;
- время смены тележки у комбайна, tман1 º tман4 – 7 мин;
- время доставки половы, tдст 4 , при среднем расстоянии доставки lдст2 – 8 км,
мин;
- время саморазгрузка у склада, tвз4 – 6 мин;
- время tхх4 холостого пробега трактора с тележкой от тока на край поля
мин.
Время работы tЦ 4р трактора с прицепом, без учёта ожидания после возвращения на край поля, составит
tЦ 4р = tман4-1 + tман4 + tдст 4 + tВЗ 4 + tхх 4 = 104 мин.
Необходимое количество агрегатов из трактора с бункером - перегружателем, автомобилей с прицепом и агрегатов из трактора и прицепной тележки для эффективной работы звена из 2-х комбайнов Дон – 1500, формально, можно рассчитать
,
где j – порядковый номер звена в ПТЛ.
Однако и детерминированные, смещённые оценки показателей ПТЛ широко используют в практике проектирования для получения сравнительных оценок эффективности машин и агрегатов.