11.1 - Понятие системы и системного анализа при проектировании.
11.2 - Задачи обеспечения агротехнических требований.
11.3 - Структурно-параметрический синтез рабочих органов сельскохозяйственных машин при проектировании.
11.4 - Построение функциональных схем.
Схемы в зависимости от основного назначения подразделяют на следующие типы:
- структурные;
- функциональные;
- принципиальные (полные);
- соединений (монтажные);
- подключения;
- общие;
- расположения;
- объединенные.
Примечание. Наименования типов схем, указанные в скобках, устанавливают для электрических схем энергетических сооружений.
Наименование и код схем определяют их видом и типом.
Наименование схемы комбинированной определяют комбинированными видами схем и типов схем.
Наименование схемы объединенной определяется ее видом и типом.
Код схемы должен состоять из буквенной части, определяющей вид схемы, и цифровой части, определяющей тип схемы.
Виды схем обозначают буквами:
- электрические – Э;
- гидравлические – Г;
- пневматические – П;
- газовые (кроме пневматических) – Х;
- кинематические – К;
- вакуумные – В;
- оптические – Л;
- энергетические – Р;
- деления – Е;
- комбинированные – С.
Типы схем обозначают цифрами:
- структурные – 1;
- функциональные – 2;
- принципиальные (полные) – 3;
- соединений (монтажные) – 4;
- подключения – 5;
- общие – 6;
- расположения – 7;
- объединенные – 0.
Например, схема функциональная: (шифр изделия) 2; схема кинематическая общая: шифр изделия К6; схема кинематическая принципиальная, шифр изделия К3; схема принципиальная: шифр изделия 3.
Функциональная схема (ФС) проектируемой СХМ (ГОСТ 2.701-84) определяет обоснованную систему частных технологических операций и технических средств их реализующих, и их взаимосвязи, определяющие рациональное выполнение заданного технологического процесса при известных ограничениях его показателей (агропоказатели).
ФС разъясняет технологические операции, процессы в проектируемой СХМ или агрегате, определяет вид (или вариант) технического средства выполняющего частную операцию (например, пневмосепарация), или их подсистему (например, решетный стан ВР30М, включающий четыре частные операции), и их основные параметры (размеры, кинематические параметры), определяет изменение технологических свойств обрабатываемого материала после выполнение каждой операции и всей СХМ или агрегата.
В результате ее разработки получают данные о вариантах рабочих органов, с помощью которых целесообразно осуществлять технологический процесс проектируемой СХМ, о их параметрах и режимах работы, о взаимном их расположении и последовательности осуществления обработки сельскохозяйственного материала.
Исходными данными для построения ФС служат исходные технологические свойства обрабатываемого материала и свойства, которые необходимо ему придать в процессе обработки на проектируемой СХМ.
Этот процесс перевода материала из одного состояния в другое зависит от наличия и возможностей рабочих органов, последовательно и в совокупности осуществляющих его.
Наличие рабочих органов, в которых заложены различные методы и принципы воздействия на материал, различная степень концентрации обработки, дает некоторое количество вариантов функциональной схемы проектируемой машины.
Для ориентировочного подхода к созданию вариантов в практике за базу выбирают одну из машин-аналогов раннего периода выполнения механизированных сельскохозяйственных процессов, а все последующие варианты машин рассматривают как процесс совершенствования конструкции.
Анализ их достоинств и недостатков приводит к синтезу новых вариантов схемы.
Однако полученные варианты, обеспечивающие одинаковое качество работы, обусловленное агро- и зоопоказателями, не являются равноценными, так как техническое задание накладывает целый ряд ограничений по материалоемкости, технологичности, надежности и долговечности, технике безопасности, эстетике и эргономике, экономике и т.д.
При оценке вариантов и выборе рациональной схемы эти ограничения должны быть учтены.
В результате расчета и построения схемы получают данные о размерах рабочих органов, режимах их работы и функциональных связях между ними.
Условием их обоснования является обеспечение заданных уровней показателей назначения, как правило, каждый рабочий орган обеспечивает достижение целого ряда значений агро- и зоопоказателей.
Обоснование ФС – творческий процесс проектирования, включающий современные методы моделирования вариантов с последующей их параметрической и структурной оптимизацией (параметрический и структурный синтез объекта проектирования) с использованием методологии теории исследования операций и системы автоматизированного проектирования (САПР).
ФС предназначена для изучения принципов функционирования СХМ, регулировки, контроля выполнения технологического процесса.
Утвержденная ФС является основой для разработки принципиальной и кинематической схем проектируемой СХМ или агрегата.
Построение ФС – процесс технического отображения обоснованной схемы с учетом требований стандартов (ГОСТ 2.701-84). ФС – неотъемлемая часть графической технической документации на проектируемый технический объект, разрабатываемый на стадиях технического проекта.
11.1. Понятие системы и системного анализа при проектировании
Проектирование (от латинского projectus – брошенный вперед) – процесс создания проекта-прототипа, прообраза предлагаемого или возможного объекта, состояния. В процессе проектирования получают данные о структуре и функционировании систем, подсистем и их элементов, удовлетворяющих критериям проектирования (доход, приведенные затраты в эксплуатации, производительность, показатели, назначения, надежность, долговечность и т.д.) [26].
Практическая реализация целей и задач проектирования может происходить в рамках САПР или с использованием аналоговых принципов (см. п.11.3.9).
Возможность проектирования сельскохозяйственных машин, агрегатов и других сложных объектов обусловлена использованием ряда принципов, основными из которых являются представление объекта проектирования в виде систем, декомпозиция и иерархичность описания объектов, многоэтапность и итерационность проектирования, типизация и унификация проектных решений и средств проектирования.
В общем случае система представляет собой целостный комплекс взаимосвязанных элементов, который имеет определенную структуру и взаимодействует с некоторой средой [23].
Системы изучаются в рамках общей и абстрактной теории систем.
Общая теория систем (ОТС) – научное направление, предметом которого является разработка совокупности философских, методологических, конструктивно-научных и прикладных проблем анализа и синтеза сложных систем произвольной природы. ОТС представляет собой область научных знаний, позволяющих изучать поведение, в том числе и целенаправленное, систем любой сложности и любого назначения.
Абстрактная теория систем (АТС) является специфичной для количественного исследования систем. Поскольку математических моделей может быть как угодно много и все они определяются принятым уровнем абстрагирования, то не может быть только одной формулировки для понятия «система», определение его в зависимости от принятого уровня абстрагирования является различным. Рассмотрение задач на одном определенном уровне абстракции позволяет решать определенную группу вопросов. Принято считать, что реальные системы неисчерпаемы в своих свойствах, и для познания действительности необходимо использовать те или иные уровни абстрагирования. Наиболее пригодными являются следующие уровни абстрактного описания систем: символический или лингвистический; теоретико-множественный; абстрактно-алгебраический; логико-математический; теоретико-информационный; динамический; эвристический.
При разработке систем прибегают к специальному приему описания систем: структурному (анализу внутреннего устройства) и функциональному (анализу взаимодействий со средой и между частями изделия) (рис.11.1, 11.2).
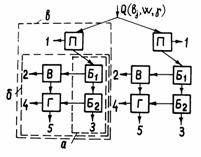
Рис.11.1. Воздушно-решетная зерноочистительная машина, представленная в виде системы (и подсистем) функционально связанных элементов: П – пневмосепаратор; , , В, Г – решета в двухъярусном решетном стане; 1 – легкие отходы; 2 и 3 – мелкие и крупные сорные отходы; 4 – фуражные отходы; 5 – очищенное зерно; а, б, в – выделенные подсистемы |
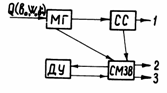
Рис.11.2. Молотилка зернокомбайна, представленная в виде функционально связанных подсистем: МГ – молотильная группа; СС – соломосепаратор; ДУ – домолачивающее устройство; СМЗВ сепаратор мелкого зернового вороха; 1 – фракция выделяемой соломы; 2 – фракция крупных и легких отходов; 3 – очищенное зерно |
При описании систем выделяют ее элементы [14]; это части или компоненты системы (например, отдельные решета
,
, В, Г и др. в воздушнорешетных машинах с двухъярусным решетным станом (см. рис.11.1); признаки, характеризующие свойства элементов системы (например, решета в решетных станах – размеры решетных полотен, форма и размеры их отверстий, кинематические параметры их движений) и связи между элементами системы и их признаками. В указанном примере (см. рис.11.1) связи между элементами системы (превмосепараторами и решетным станом, между решетами в решетном стане) определяются величиной и технологическими свойствами зерновых или зерносоломистых (см. рис.11.2) фракций, перемещаемых от предыдущего рабочего элемента к последующему (на схемах эти связи указаны линиями со стрелками). Два и более элементов системы, выполняющих законченную частную функциональную операцию, характеристики которой важны для анализа всей системы, могут быть выделены в подсистемы. Например, на рис.11.1 - решета
и
, образующие два последовательных решета для выполнения частной законченной технологической операции по выделению из зернового материала крупных примесей; решетный стан, включающий все решета; пневмосепараторы. В молотилке зерноуборочного комбайна (см. рис.11.2) в качестве подсистем можно выделить: молотильную группу, состоящую из молотильного барабана, подбарабанья и отбойного битера; соломотряса, состоящего, например, из группы параллельно работающих клавиш соломотряса; сепаратора мелкого зернового вороха и домолачивающего устройства.
Связи между признаками элементов или частей (подсистем, состоящих из двух или более элементов системы) могут быть выражены через показатели функционирования системы, величины которых зависят не только от функциональной связи элементов или частей системы, но и от их признаков (размеров отверстий решет, размеров решетных полотен и др.).
Связи объединяют систему в единое целое. По существу, только наличие многих видов связей (структурных, функциональных, логических, случайных и т.д.) делают понятие системы полезным.
Ни для одного множества рассматриваемых элементов нельзя утверждать, что в нем не существует связей; например, в случае любой физической системы за связи всегда можно принять расстояния между элементами этой системы.
Важной частью является вход системы, являющейся комплексным понятием. Во-первых, он субстанция, которая поступает в систему и подвергается определенным преобразованиям, изменяется при выполнении рассматриваемого процесса; во-вторых, вход – внешняя среда или совокупность факторов и явлений, воздействующих на рассматриваемую систему. У входа различают виды и компоненты. Рассмотрим три основных вида входа:
1) вход – результат предшествующего процесса, последовательно связанного с данным (например, подача
и технологические свойства зернового материала, полученные в результате функционирования зернокомбайна и поступающие для очистки в воздушно-решетную машину, содержание
-х компонентов
в зерновом материале, влажность
и плотность
зернового материала (см. рис.11.1) или подача
и соответствующие технологические свойства хлебной массы
,
,
, поступающей в молотилку зернокомбайна (см. рис.11.2) после жатки);
2) вход – результат процесса того же комплекса, который вновь вводится в него через обратную связь (например, дополнительная подача мелкого зернового вороха на его сепараторы мелкого зернового вороха из домолачивающего устройства (ДУ) (см. рис.11.2);
3) к понятию входа системы относятся и установленные способы ее функционирования (например, программы управления подачи хлебной массы в молотилку зернокомбайна).
Процесс переводит вход и выход и является процессом функционирования рассматриваемой системы (например, процесс очистки зерна от сорных и зерновых примесей). Выход является результатом функционирования рассматриваемой системы и относится либо к получению полезного результата очистки зернового материала, производительности зернокомбайна, либо к сопутствующим результатам, не дающим положительного эффекта (запыленность среды, вибрация машин и др.).
Структурное описание системы. Для структурного описания системы рекомендуется применять следующие четыре множества [26]:
,
где
- множество состава и свойств
-х элементов, каждый из которых не может быть описан структурой;
- множество назначений и характеров связей;
- множество устойчивости структуры;
- множество построений структуры.
Все множества принимаются конечными, и среди них различают следующее:
1. Во множестве элементов
: состав – гомогенный (содержащий однотипные элементы), гетерогенный (содержащий разнородные элементы), смешанный; свойства элементов – информационные, материальные, энергетические.
2. Во множестве
: назначение связей – информационные, материальные, энергетические; характер связей – прямые, обратные.
3. Во множестве
устойчивости структуры: детерминированная, вероятностная (стохастическая).
4. Во множестве построения
: иерархические, многосвязные комплексы (последовательные, параллельные, смешанные). Перечисленные комплексы представляют совокупность двух и более элементов (рис.11.3).
Элемент комплекса (системы) – его часть (базовый элемент), у которой теоретически или экспериментально можно определить вход и выход и установить зависимость выхода от входа, определяемую природой элемента. Элементы делятся на одномерные и многомерные.
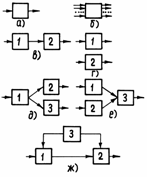
Рис.11.3. Виды комплексов и их элементы: а – одномерный элемент; б – многомерный элемент; в-ж – комплексы; в – последовательный; г – параллельный; д – расходящийся; е – сходящийся; ж - замкнутый
Одномерный элемент – элемент, вход и выход которого представляют собой скалярные величины (величины, характеризующие один показатель, например, подача зернового материала) (см. рис.11.3,а).
Многомерный элемент – элемент, вход и выход которого описываются совокупностью независимых показателей, являющихся аргументами вектора входных воздействий (например, подача зернового материала, его влажность, содержание сорных и зерновых компонентов и т.д.) (см. рис.11.3,б).
При изучении систем вводится понятие сложной системы.
Рассмотрение изучаемого объекта как системы, состоящей из взаимодействующих элементов, построение математической модели и исследование его свойств методом моделирования составляет сущность системного подхода, а совокупность методов и приемов исследования входит в арсенал самостоятельного научного направления – системного анализа.
11.1.1. Иерархические уровни описания проектируемых объектов
Разделение описаний по степени детализации отображаемых свойств и характеристик объекта лежит в основе блочно-иерархического подхода к проектированию и приводит к появлению иерархических уровней (уровней абстрагирования) в представлениях о проектируемом объекте.
На каждом иерархическом уровне используются свои понятия системы и элементов. На уровне 1 (верхнем уровне) подлежащий проектированию сложный объект
(рис.11.4) рассматривается как система
из
взаимосвязанных и взаимодействующих элементов
. Каждый из элементов в описании уровня 1 представляет собой подсистему
на уровне 2. Элементами подсистемы
являются объекты
(
- количество элементов в описании подсистемы
,
,
). Как правило, выделение элементов
происходит по функциональному признаку. Подобное разделение может продолжаться вплоть до получения на некотором уровне элементов, описание которых дальнейшему делению не подлежит (базовые элементы).
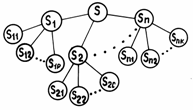
Рис.11.4. Схема иерархического
описания объекта проектирования |
Таким образом, принцип иерархичности означает структурирование представлений об объектах проектирования по степени детальности описаний, а принцип декомпозиции (блочности) – разбиение представлений каждого уровня на ряд составных частей (блоков) с возможностью раздельного (поблочного) проектирования объектов
на уровне 1, объектов
- на уровне 2 и т.д.
Пример. В машиностроении базовые элементы представлены деталями: винт, шпонка, вал, зубчатое колесо, решетное полотно и др. Детали рассматриваются как элементы, фигурирующие в описаниях низшего иерархического уровня, на котором системами являются сборочные единицы (редуктор, решетный стан, молотильный барабан и др.). Иногда базовыми элементами таких систем могут быть не только детали, но и –объекты, состоящие из многих деталей и получаемые на данном предприятии как законченные комплектующие изделия (например, подшипники качения, электродвигатели и т.п.). Сборочные единицы являются элементами систем следующего иерархического уровня (например, зерноочистительная машины и др.), которые, в свою очередь, могут быть элементами более высокого уровня (например, отделение очистки зерноочистительного агрегата, куда входит несколько различных машин).
11.1.2. Классификация типовых процедур проектирования
Проектная процедура называется типовой, если она предназначена для многократного применения при проектировании многих типов объектов.
Различают проектные процедуры анализа и синтеза. Синтез заключается в создании описания объекта, а анализ – в определении свойств и исследовании работоспособности объекта по его описанию, т.е. при синтезе создаются, а при анализе оцениваются проекты объектов.
Процедуры анализа делятся на процедуры одно- и многовариантного анализа. При одновариантном анализе заданы значения внутренних параметров. Требуется определить значение выходных параметров объекта. Многовариантный анализ заключается в исследовании свойств объекта в некоторой области пространства внутренних параметров. Такой анализ требует многократного решения систем уравнений – математической модели, описывающей объект (многократного выполнения одновариантного анализа).
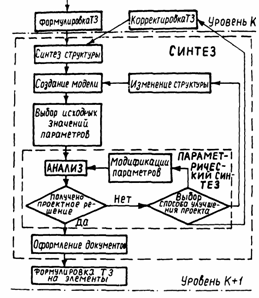
Рис.11.5. Схема процесса проектирования |
Процедуры делятся на процедуры структурного и параметрического синтеза. Целью структурного синтеза является определение структуры объекта – перечня типов элементов, составляющих объект, и способа связи элементов между собой в составе объекта. Параметрический синтез заключается в определении числовых значений параметров элементов при заданных структуре и условиях выполнения агропоказателей на выходные показатели объекта, т.е. при параметрическом синтезе нужно найти точку или область в пространстве внутренних параметров, в которых выполняются те или иные условия (обычно технические, агро- или зоотребования).
Типичная последовательность проектных процедур на одном из этапов нисходящего проектирования представлена на рис.11.5.
На предыдущем этапе решались задачи
-го иерархического уровня, одним из результатов решения этих задач при нисходящем проектировании является формулировка ТЗ (технического задания) на проектирование систем
-го рассматриваемого уровня.
Если решение задач высоких иерархических уровней предшествует решению задач более низких иерархических уровней, то проектирование называют нисходящим. Если сначала выполняются этапы, связанные с низшими иерархическими уровнями, проектирование называют восходящим. У каждого из этих двух видов проектирования имеются преимущества и недостатки.
Проектирование системы начинается с синтеза исходного варианта структуры. Для оценки этого варианта создается модель: математическая при автоматизированном проектировании; экспериментальная (физическая) или стенд – при неавтоматизированном проектировании. После выбора исходных значений параметров элементов выполняется анализ варианта, по результатам которого становится возможной его оценка. Обычно оценка заключается в проверке выполнения требований ТЗ. Если ТЗ выполняются, то полученное проектное решение принимается, система
-го уровня описывается в принятой форме и формулируется ТЗ на проектирование элементов данного уровня (так называемых систем следующего уровня). Если же полученное проектное решение неудовлетворительно, выбирается один из возможных путей улучшения проекта.
Обычно проще всего осуществить изменение числовых значений параметров элементов, составляющих аргументы вектора
управляющих воздействий (например, частоту колебаний решетного стана, форму и размеры отверстий решет и т.п.).
Совокупность процедур модификации
, анализа и оценки результатов анализа представляет собой процедуру параметрического синтеза. Если модификации
целенаправлены и подчинены стратегии поиска наилучшего значения некоторого показателя качества, то процедура параметрического синтеза является процедурой оптимизации. Возможно, что путем параметрического синтеза не удастся добиться приемлемой степени выполнения требований ТЗ. Тогда используют другой путь, связанный с модификациями структуры проектируемого объекта.
Новый вариант структуры синтезируется, и для него повторяются процедуры формирования модели и параметрического синтеза. Если не удастся получить приемлемое проектное решение и на этом пути, то возникает вопрос о корректировке ТЗ, сформулированного на предыдущем этапе проектирования. Такая корректировка может потребовать повторного выполнения ряда процедур
-го иерархического уровня, что обусловливает итерационный характер проектирования.
По характеру и степени участия человека и использования ЭВМ при выполнении работ проектирования различают несколько режимов.
Автоматический режим имеет место при выполнении проектирования по формальным алгоритмам на ЭВМ без вмешательства человека в ход решения.
Ручной (неавтоматический) режим характеризует выполнение проектирования без помощи ЭВМ.
Диалоговый (интерактивный) режим является более совершенным режимом. При нем все процедуры выполняются с помощью ЭВМ, а участие человека проявляется в оперативной оценке результатов проектных процедур или операций, в выборе предложений и корректировке хода проектирования. Если инициатором диалога является человек, которому представлена возможность в любой момент времени прервать автоматизированное вычисление на ЭВМ, то диалог называется активным. Если прерывание вычислений происходит по командам выполняемой ЭВМ программы в определенные, заранее предусмотренные моменты, т.е. проектировщик не может выступать как инициатор диалога, то такой диалог называют пассивным.
Развитие САПР происходит в направлении повышения степени автоматизации проектирования. Однако работа в режиме диалога в САПР остается необходимой, так как полностью процесс проектирования сложных систем формализовать не удается и участие проектировщика в ряде случаев позволяет ускорить принятие решений.
11.1.3. Математическое обеспечение автоматизированного проектирования (АП)
Математическое обеспечение АП включает в себя математические модели объектов проектирования, методы и алгоритм выполнения проектных процедур [26].
Математическая модель – это совокупность математических объектов (чисел, символов, множеств и т.д.) и связей между ними, отражающая важнейшие для исследователя свойства изучаемого или проектируемого объекта.
К математическому моделированию в технике прибегают в тех случаях, когда опыта и интуиции проектировщика недостаточно для принятия решения, а также при решении задач, требующих больших объемов вычислений.
Как известно, в технике широко применяется и другой вид моделирования – физическое макетирование объектов в уменьшенном или упрощенном виде. Как физическое, так и математическое моделирование имеют свои преимущества и недостатки. Преимуществами математического моделирования являются отсутствие затрат на изготовление физических макетов, возможность проведения практически неограниченного числа экспериментов, в том числе на критических режимах, которые привели бы к разрушению физического макета. Вместе с тем в ряде случаев затраты на создание адекватной математической модели могут превосходить затраты на макетирование, а достоверность результатов математического моделирования часто зависит от принимаемых допущений и неизвестных коэффициентов математической модели.
Математические модели (ММ) служат для описания свойств объектов в процедурах АП. К ММ предъявляются требования универсальности, адекватности, точности и экономичности.
Степень универсальности ММ характеризует полноту отображения в ММ свойств реального объекта. ММ отражает лишь некоторые свойства объекта. Так, большинство ММ, используемых при функциональном проектировании, предназначены для отображения протекающих в объекте физических (например, полного выделения отдельных компонентов из зернового материала в решетном стане зерноочистительной машины) или информационных процессов, при этом не требуется, чтобы ММ описывала такие свойства объекта, как геометрическая форма составляющих его элементов (например, механическая прочность каркаса решетного стана и др.).
Точность ММ оценивается степенью совпадения значений параметров реального объекта и значений тех же параметров, рассчитанных с помощью оцениваемой ММ.
Адекватность ММ – способность отображать свойства объекта с погрешностью не выше заданной.
Экономичность ММ характеризуется затратами вычислительных ресурсов, т.е. затратами машинного времени и объемом памяти ЭВМ.
Основные признаки классификации и типы ММ, применяемые в САПР, приведены в табл. 11.1.
Таблица 11.1
Классификация математических моделей
Признаки классификации |
Математические модели |
Характер отображаемых свойств
объекта |
Структурные, функциональные |
Принадлежность к иерархическому уровню |
Микроуровня, макроуровня, метауровня |
Степень детализации описания внутри одного уровня |
Полные, макромодели |
Способ представления свойств объекта |
Аналитические, алгоритмические,
имитационные |
Способ получения модели |
Теоретические, эмпирические |
11.2. Задачи обеспечения агротехнических требований
Агротехнические требования обеспечиваются при выполнении механизированных технологических сельскохозяйственных процессов созданием функциональной структуры машин, параметрами и режимами их работы. Эта группа требований определяет основное назначение машины. Напомним из теории исследования операции, что система может считаться функционально пригодной, если она выполняет свое назначение. Следует также иметь в виду, что все другие группы требований могут быть обеспечены методами, общими для отраслей машиностроения, а эта группа требует специальных методов, присущих только сельскохозяйственному машиностроению.
Очевидно, что в этом плане функциональная структура СХМ при проектировании является первоначальной. Критериями ее проектирования являются показатели качества работы, содержащиеся в техническом задании. Для создания функциональной структуры рассматриваются и последовательно решаются задачи:
1. Синтез вариантов рабочих технологических операций, их систем, выполняемых рабочими органами и всей проектируемой СХМ.
2. Моделирование вариантов рабочих технологических операций и их систем, выполняемых рабочими органами и всей проектируемой СХМ.
3. Параметрический и структурный синтез систем технологических операций, выполняющих заданный технологический процесс в проектируемой СХМ при выполнении всех заданных агро- или зоотребований.
Для решения этих задач необходимо рассмотреть общие подходы и методы воздействия на обрабатываемые материалы.
Осуществление процессов связано с необходимостью выбора метода воздействия на среду, материал, объект.
Целью создания процесса является повышение эффективности его функционирования по отношению к реально существующим процессам при условии выполнения требований по качеству, записанных в техническом задании в виде агротребований, которые имеют количественное выражение.
Рассматривая механические системы, следует отметить, что в них для организации процессов используются законы механики. Они должны быть положены в основу моделирования процессов. Ранее отмечалось, что в процессе проектирования создается нечто, чего не существует и что является продуктом деятельности человеческого мозга. Не на всех стадиях проектирования имеется возможность экспериментального исследования проектируемой системы из-за ее физического отсутствия. Поэтому считаем необходимым основное внимание уделить ранним стадиям проектирования, так как сформированная машина в виде опытного образца доступна для экспериментальных исследований.
Для моделирования процессов на ранних стадиях проектирования обычно используют математические модели, получившие название в сельхозмашиностроении рациональных. В основе их лежат логика и законы механики. Анализ техники, применяемой в сельском хозяйстве, показывает, что в основе всех рабочих процессов воздействия на материалы, среды, объекты положены методы, реализуемые в технических устройствах: удар, растяжение, сжатие, сдвиг, скручивание.
В ряде случаев применяют комбинации этих методов. Однако при применении любого метода встает проблема создания потока, обеспечивающего требуемую производительность. Иногда это требование идет в ущерб качеству выполняемого процесса. Примером может служить процесс обмолота. В нем использован принцип удара по хлебной массе, что приводит как к разрушению связи зерна с колосом (его основное назначение), так и к дроблению зерна и перебиванию соломы. Последнее, кроме снижения качества, создает неблагоприятные условия для работы сепарирующих рабочих органов и приводит к большой энергоемкости процесса.
Использование в этом случае принципов скручивания, растяжения плодоножки требует новых технических решений для организации потока материала.
Направленность потока материала по отношению к движению рабочего органа обеспечивает надежность технологического процесса. В связи с этим в свое время родился термин «прямоточность», который отражал в себе важность совпадения направления потока материала и исполнительных элементов рабочего органа.
Возможность применения различных принципов ограничена возможностью осуществления движений рабочими органами. Их три вида: поступательное, вращательное, колебательное.
Следует отметить, что технологическая операция определяет характер воздействия на материал, среду, объект. Конструктор должен поставить в соответствие ему метод, учитывая в первую очередь возможность реализации его в техническом устройстве, называемом рабочим органом. При этом приходится учитывать целый ряд ограничений, вытекающих из технического задания: технологичность, надежность и т.п., но в первую очередь те, которые обеспечивают заданные показатели назначения проектируемой СХМ.
Например, льномолотилка должна иметь устройство для разрушения коробочек. Если исходить из перечисленных принципов, то в данном случае применимы сдвиг и удар. В первом случае можно использовать вальцы, имеющие различные скорости при контакте с ворохом. Качество плющения коробочек зависит от толщины слоя вороха, т.е. от захватывающей способности вальцев. Это приводит к ограничению производительности. Поэтому для получения большой производительности в машинах по разделыванию вороха льна используют бильный барабан. Из этого примера следует, что применяемый метод воздействия на материалы, среды, объекты предопределяет тип рабочего органа для выполнения рабочего процесса. Следует отметить, что при проектировании машин применение метода воздействия на объект обработки хотя и связано с созданием определенного напряженно-деформационного состояния, однако интерес представляют факторы, обеспечивающие это состояние. К ним относятся геометрические и кинематические характеристики процесса, тождественные характеристикам рабочих органов. Геометрические и кинематические характеристики являются для процесса управляющими факторами и составляют предмет определения при разработке функциональной схемы. Современный путь их определения заключается в моделировании и структурно-параметрической оптимизации объекта проектирования.
11.3. Структурно-параметрический синтез рабочих органов сельскохозяйственных машин при проектировании
При параметрической и структурной оптимизации ФС на первом этапе необходимо выбрать существующие (принцип унификации) или обосновать новые рабочие органы, реализующие одну или подсистему вариантов частных технологических операций, необходимых для выполнения заданного технологического процесса проектируемой СХМ.
Для системного анализа и синтеза, определяющих рациональные подсистемы операций и рабочих органов, их реализующих, необходимо построить математические модели, описывающие эти операции, провести их многомерный анализ и, если эти операции последние в системе операций, формирующих СХМ, осуществить параметрический синтез этих рабочих органов.
Системность анализа и параметрического синтеза (для последних операций в системе), операций и рабочего органа, ее реализующего, определится количеством, качеством обрабатываемого материала на предыдущей операции в системе и характеристиками его подачи на исследуемый рабочий орган (закономерности поступления, потока материала по времени, по ширине).
Рассмотрим для примера методы структурной и параметрической оптимизации базовых элементов и рабочих органов воздушно-решетных зерноочистительных машин.
11.4. Построение функциональных схем
Результаты, полученные при решении задач по обоснованию функциональной схемы являются основанием для ее построения. Методы выполнения схем изложены в ГОСТ 2.701-84.
Для функциональных схем изображения элементов машин не установлены стандартами. Обычно схема изображается на основе схематического разреза с внешними очертаниями машины, внутри которого даются упрощенные изображения каждого элемента.
Построение функциональной схемы выполняется без соблюдения масштаба, но с приближенным учетом соотношений между элементами.
На функциональной схеме учитывают и показывают приближенно пространственное расположение составных частей и источника движения.
При выполнении схем применяют условные графические обозначения, установленные в стандартах, прямоугольники, упрощенные внешние очертания и нестандартные условные обозначения. Последнее наиболее распространено в функциональных схемах СХМ, поскольку имеется очень большое разнообразие элементов и обрабатываемых материалов и их комбинаций. Нестандартные условные графические обозначения, применяемые в функциональных схемах СХМ, упрощенно отражают контуры рабочего или вспомогательного органа, элемента или составной части. При изображении обычно следуют установившейся в отрасли практике.
На функциональной схеме должны быть изображены:
- Все рабочие органы в последовательности выполняемого технологического процесса.
- Часть функционально вспомогательных элементов, например рама, опорные колеса, двигатель, элементы и величины регулировок.
- Обрабатываемый материал. Для простых процессов обрабатываемый материала показывается условными обозначениями, отражающими вид материала и изменение его технологических свойств после выполнения соответствующих операций.
Для показа потоков материалов с несколькими компонентами удобно использовать стрелочные обозначения (рис.11.58).
Если это не загромождает чертеж, предпочтительно сочетание двух видов условных обозначений, первый дает информацию о перемещении различных компонентов (например, крупные, мелкие примеси, зерно), второй точно указывает направление движения различных фракций обрабатываемого материала (см. рис.11.58). Функциональную схему рекомендуется выполнять не менее чем в двух проекциях для пространственного представления о машине и ее рабочих органах.
На функциональной схеме должны быть указаны:
1. Геометрические, кинематические и при необходимости динамические параметры рабочих органов и машины, которые обеспечивают выполнение технологического процесса.
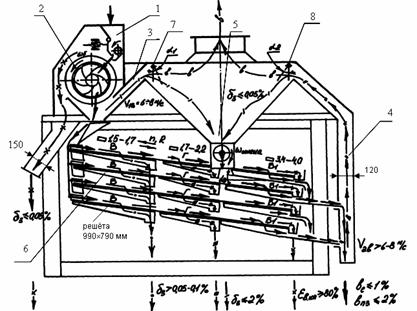
Рис.11.58. Очиститель зерна стационарный ОЗС-50/25. Схема функциональная: 1 -камера приемная; 2-скельператор барабанный; 3,4-каналы аспирационные; 5 - камера осадочная; 6 - 4-ярусный трехрешетный модуль; 7,8 – заслонки для изменения скорости воздушного потока в пневмосистемах; δз- потери зерна; εв.кп- полнота выделения крупных примесей; вс- содержание сорных примесей; впз- содержание зерновых примесей; V1В , V2В - скорость воздушного потока. Условные обозначения:
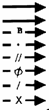
|
ввод обрабатываемого материала;
основной поток зернового материала;
воздушный поток;
подсев;
легкие примеси с воздухом;
фураж;
легкие примеси;
крупные примеси
|
2. Показатели, характеризующие обрабатываемый материал, а в сложных процессах связанных со смешиванием, сепарацией, сортированием и др., все компоненты обрабатываемых материалов на каждой стадии изменения их состояния, т.е. до и после каждого рабочего органа.
3. Выходные характеристики обрабатываемого материала должны соответствовать агротехническим требованиям. Характеристики или показатели качества обрабатываемых материалов выражаются в процентах или ко всему входящему материалу (вход 100%) или входу каждого компонента. В любом случае при расчете должно соблюдаться равенство всех входов и всех выходов.
Используя методологию САПР «Проектирование функциональной схемы и структуры воздушно-решетной зерноочистительной машины» и общие требования к построению ФС, можно обосновать и построить ФС универсальной воздушно-решетной машины (см. рис.11.58) производительностью:
предварительная очистка зерна…………….. - 50 т/ч;
первичная очистка зерна ……………………….- 25 т/ч;
вторичная (семенная) очистка зерна………- 10 т/ч.