Лекция 11. Очистка воздуха от пыли
11.1. Измерение запыленности воздуха
Запыленность воздуха может быть определена прямыми способами
(весовым и количественным) и косвенными (фотометрическим, электростатическим
и др).
Запыленность воздуха измеряют в рабочем помещении, внутри
воздуховодов, в оборудовании и в фильтрах и циклонах для выявления
взрывоопасных концентраций.
Наибольшее распространение как наиболее простой и падежный
получил весовой способ с определением количества пыли в мг, приходящейся на 1м3 воздуха. На рис. 26
представлена схема установки для измерения запыленности воздуха весовым
способом. При определении запыленности воздуха применяют специальные патроны с
круглыми фильтрами из синтетических материалов типа АФА-ВП-10 и АФА-ВП-18
(аналитические фильтры аэрозольные весовые перхлорвиниловые Петрянова площадью 10 и 18 см2).
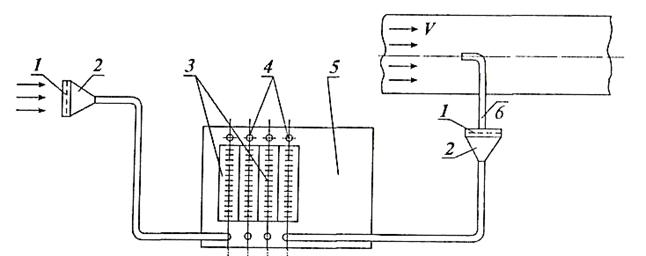
Рис. 26. Схема установки для измерения запыленности воздуха
I - фильтр, 2 - патрон, 3 - ротаметры, 4 - регуляторы расхода
воздуха, 5 - ротационная воздуходувка, 6 -трубка для забора запыленного воздуха.
При отсутствии фильтров применяют аллонж с ватным фильтром:
стеклянный цилиндр диаметром 20 мм и длиной 100 мм, заканчивающийся конусами с
патрубками диаметром 8... 12мм для присоединения резиновых трубок.
Цилиндр на длине 40мм заполнен равномерным слоем стекловаты так, чтобы
сопротивление слоя было не менее 4000 Па при расходе воздуха 10 л/мин.
Пылезаборную трубку устанавливают в воздуховоде так же, как и пнев-мометрическую,
и отбирают пробы в тех же точках, где измеряют динамическое давление.
Пылезаборная трубка имеет шлифованный внутренний диаметр 4...6мм.
Для более точных замеров концентрации пыли в воздуховодах необходимо
соблюдать условие изокинетичности потоков, а также отбирать пробы. Не менее чем
в 6 точках по двум взаимно перпендикулярным направлениям. Сечения для отбора
проб следует брать на выравненных потоках на прямых участках, исключая влияние
завихрений и сил тяжести.
Условие изокинетичности потоков заключается в том, что скорость воздуха в пылезаборной трубке должна быть равна
скорости воздуха в воздуховоде.
Скорость воздуха в отверстии
пылезаборной трубки регулируют изменением расхода q л/мин, просасываемого через фильтр
ротационной воздуходувной машиной, вращением регулятора, наблюдая по шкале
ротаметра. Объемы просасываемого запыленного воздуха принимают в зависимости от предполагаемой концентрации пыли
следующими: < 2 мг/м3; 2... 10; 10...20; 20...50; 50...
150 мг/м3; > 150 мг/м3 — соответственно объемы в л:
1000; 500; 400; 300; 200 и 100...50 л.
Запыленность воздуха в мг/м3
определяется по формуле:
, (45)
где А1 и А2 — соответственно
массы фильтра или аллонжа до и после опыта, мг;
q л/мин — расход воздуха по ротаметру; t мин — время отбора пробы.
Минимальное и максимальное время отбора пробы определяется по
формулам:
,
где Amin - минимальная привеска фильтра (Amin - 1 мг);
- предполагаемая
запыленность (мг/м3)
,
где Атлх - максимальная привеска пыли в
фильтре (для фильтров АФА-ВП-18 Атлх
= 50 мг; для АФА-ВП-10 - 25 мг).
Фотометрический способ определения запыленности воздуха основан на
принципе измерения величины ослабления светового потока, проходящего через
слой запыленного воздуха.
Фотопылемеры Ф-1 и Ф-2 предназначены для контроля запыленности воздуха в угольных шахтах и деревообрабатывающих
цехах. Принцип действия заключается в том, что луч света проходит через
слой запыленного воздуха, отражается от зеркала и сконцентрированным пучком
попадает на фотосопротивлепие.
Электростатические пылемеры основаны на способности частиц
пыли приобретать и сохранять электрические заряды. Электрические заряды,
полученные в результате трения частиц о плоскость электростатического датчика,
установленного неподвижно в воздуховоде, воздействуют на электронно-релейпую
схему и преобразуются в показания прибора. Недостаток этого способа — низкая
точность измерения запыленности.
11.2. Основные показатели работы пылеотделительных
устройств
К основным показателям работы любого пылеотделителыюго устройства
относятся: эффективность пылезадержания, аэродинамическое сопротивление и
пылеемкость.
По размеру частиц различают мелкую (до 10 мкм), среднюю (до
200 мкм), и крупную (> 200 мкм) пыль.
Физико-механические свойства пыли (плотность, влажность,
смачиваемость, гигроскопичность) в сочетании с размерами частиц являются основанием
для подбора или разработки конструкции пылеуловителя.
Тип пылеуловителя выбирается в зависимости от степени
очистки, требуемой по условиям производства.
1.Качество очистки воздуха (газа) от взвешенных твердых
пылевидных частиц определяют по процентному отношению концентрации пыли до и
после очистки. Эффективность работы пылеотделителя (пылезадержания)
рассчитывается по формуле:
, (46)
где и — соответственно
концентрации взвешенных частиц до и после очистки, мг/м3.
2.Вторым показателем работы пылеотделительного устройства
является аэродинамическое сопротивление. В аспирационных системах пылетодели-тели
и фильтры являются элементами сети. На преодоление сопротивления проходу
воздуха через них затрачивается значительная часть располагаемого давления
вентилятора.
Чрезмерное высокое сопротивление пылеотделителя может
являться следствием его неправильного выбора или его засорения, что нарушает
эффективность работы системы в целом. Для всех пылеотделительных устройств
сопротивление (потеря давления) зависит от расхода воздуха (газа) и
определяется выражением:
,
где Кп — коэффициент
пропорциональности;
п — показатель, отражающий конструктивные особенности
пылеотделителя (п = 1,5...2,0);
Q - расход воздуха.
У многих пылеотделителей (например, инерционных, электрофильтров,
акустических пылеотделителей) при неизменном расходе воздуха сопротивление в
процессе работы остается постоянным.
Однако у большинства фильтров контактного действия сопротивление в
процессе работы растет и может в два раза превысить начальное вследствие
оседания пыли.
3. Под пылеемкостыо понимается масса пыли, которую пылеотделитель
(фильтр) способен поглотить в процессе непрерывной работы, сохраняя в
допустимых пределах величины эффективности пылезадержания и аэродинамического
сопротивления. После того как количество пыли достигло значения предельной
пылеемкости, необходимо: опорожнить пылесборник;
произвести промывку, встряхивание или продувку фильтрующего слоя; заменить
фильтрующие элементы. В общем случае показатель предельной пылеемкости должен
быть учтен при выборе фильтра.
11.3. Классификация и основные типы пылеотделительных устройств
По принципу действия существующие пылеотделительные
устройства можно классифицировать по следующим группам:
—инерционные, или центробежные, циклоны, в которых выделение
взвешенных частиц пыли происходит за счет сил инерции при резком изменении
направления движения воздушного потока;
—пылеотделительные камеры, работающие
на принципе осаждения частиц пыли, имеющих значительную массу, т. е. за счет
сил тяжести;
—пылеотделители, работающие на
принципе улавливания частиц пыли, смачиваемых водой;
—матерчатые фильтры, удерживающие
частицы пыли, размер которых превышает размер пор хлопчатобумажной ткани;
—электроочистительные установки,
работающие на принципе иониза-. ции молекул газа и зарядки взвешенных частиц в
электрическом поле постоянного тока.
Тип пылеуловителя выбирается в зависимости от степени очистки, требуемой по условиям производства. Как упоминалось
ранее, качество очистки воздуха от
взвешенных твердых частиц материала определяется по процентному
отношению концентрации пыли до и после очистки.
На мукомольных, крупяных и комбикормовых заводах нашли широкое применение
инерционные центробежные пылеотделители (циклоны) и матерчатые рукавные
фильтры. Кроме того, в системах с рециркуляцией воздуха применяются мокрые
фильтры с водяной завесой.
Циклоны — наиболее простые, надежные и сравнительно дешевые
пылеулавливающие устройства. Корпус циклона состоит из цилиндрической и
конусной частей. Запыленный воздух поступает по входному патрубку в верхнюю часть цилиндра. Входной
патрубок расположен по касательной к цилиндру и с небольшим уклоном книзу для
придания потоку вращательного движения с направлением вниз (см. рис. 27).
Циклоны работают на принципе
выделения частиц пыли в поле центробежных сил. Эффективность работы циклона пропорциональна
величине центробежной силы, действующей на частицы пыли диаметром d4 во вращательном движении.
,
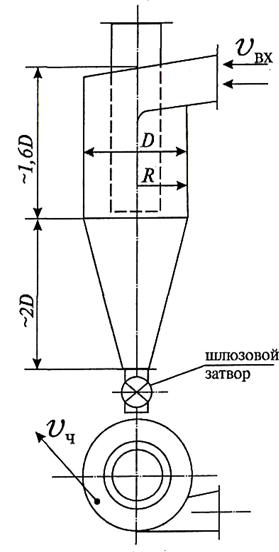
Рис.27 Схема
циклона
где — плотность материала частицы;
Vч— окружная
скорость частицы;
— масса частицы.
Чем меньше диаметр частицы и , тем больше должна быть скорость вихревого потока для
получения той же центробежной силы.
При сохранении свойств частицы
увеличение скорости движения и уменьшение радиуса циклона повышает
эффективность работы циклона, однако повышает и его аэродинамическое
сопротивление:
(47)
где — скорость воздуха во
входном патрубке, пропорционально квадрату скорости входа воздуха в циклон. К
тому же при > 20 м/с ухудшается
эффективность пылезадержания циклона в связи с отрывом частиц от стенки. Для
повышения эффективности работы циклонов уменьшают их диаметры, а
соответствующую нагрузку по производительности получают увеличением количества
одновременно работающих циклонов с установкой их в батарею.
Циклоны подбирают по заданной
производительности по воздуху с проверкой расчетом - , которая должна быть в пределах 15...18 м/с. Степень очистки
циклонов может достигать 99,5%. Циклоны устанавливают на всасывающей и напорной
линиях сети. Промышленность выпускает большую гамму одиночных и батарейных
циклонов типа ЦОЛ, БЦ, ОТИ, ЧБЦШ и др., данные о которых приводятся в
справочной литературе.
Лекция
14. Рукавные фильтры. Схема,
методы очистки ткани.
Устройство
всасывающих фильтров.
Всасывающий
фильтр состоит из следующих
основные частей: корпуса (шкафа)
прямоугольной или цилиндрической формы, фильтровальных рукавов диаметром
120...200 мм, длиной 1 800...2 000 мм, устройства для очистки
фильтровальных рукавов от осажденной на них пыли и устройства для удаления
осажденной пыли.
По способу очистки
фильтровальных рукавов фильтры бывают: с двойной очисткой; встряхиванием и с
обратной продувкой атмосферным воздухом (фильтры ФВ и Г4-1БФМ); с одинарной
очисткой: с обратной продувкой рукавов атмосферным воздухом (те же марки), с
обратной продувкой рукавов воздухом от вентилятора высокого давления и обратной
импульсной продувкой рукавов сжатым воздухом от компрессора (фильтры РЦИ и
РЦИЭ).
Схемы очистки воздуха от
пыли во всасывающих фильтрах показаны на рис. 28. В фильтре с продувкой рукавов
атмосферным воздухом (рис,28,а - слева) запыленный воздух поступает внутрь
рукавов через конусный сборник для пыли, очищается, входит в шкаф фильтра и
уносится в аспирационную сеть вентилятором через клапанную коробку.
Во время очистки рукавов
секция фильтра отключается от вентилятора, открывается продувочное отверстие и
атмосферный воздух продувает ткань снаружи вовнутрь, очищая её от пыли (рис. 28,6 - справа).
Подсос в фильтрах
шкафного типа, включая приток воздуха на продувку рукавов, не должен превышать
15 %.

Сжатый
воздух
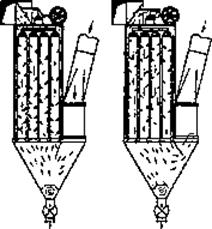
а
Рис. 28. Схемы работы фильтра
РЦИ (РЦИЭ):
а
- фильтр со встряхивающим механизмом и однократной продувкой атмосферным воздухом
(слева рабочий режим, справа - момент
очистки ткани);
б - фильтр с импульсной продувкой рукавов
сжатым воздухом;
1 – камера запыленного воздуха; 2-рукав;
3 - конус; 4 - входной патрубок; 5 - клапан; 6 - сопло; 7 - выходной патрубок; 8 -камера очищенного воздуха;
9 - труба Вентури; 10-
камера сжатого воздуха; 11-решетка
В фильтрах
Г4-1БФМ предусмотрена очистка ткани путем встряхивания рукавов и обратной
продувки атмосферным воздухом.
Всасывающий фильтр Г4-1БФМ показан на рис. 29, а
техническая характеристика фильтров дана
табл. 4.
Этот фильтр отличается
конструкцией продувочно-встряхивающего механизма, в нем применен эксцентриково - храповый механизм;
сборный конус для пыли имеет три шнека вместо двух, что устраняет
сводообразование и подпор пыли; привод распределительного вала 18 осуществлен эксцентриковым и
храповым механизмами; вместо трех встряхивающих кулачков применен один кулачок.
Техническая характеристика
всасывающих фильтров Г4-1БФМ. Таблица 4
Фильтр
|
Число
секций
|
Фильтрую-щая пло-щадь, м2
|
Число рука-вов
|
Размеры фильтра, мм
|
Масса, кг
|
А
|
Б
|
В
|
Г
|
Д
|
Е
|
Г4-1БФМ-30
|
2
|
30
|
36
|
1670
|
1205
|
1034
|
300
|
400
|
1215
|
1100
|
Г4-1БФМ-45
|
3
|
45
|
54
|
2200
|
1720
|
1550
|
350
|
500
|
1730
|
1400
|
Г4-1БФМ-60
|
4
|
60
|
72
|
2700
|
2240
|
2070
|
400
|
560
|
2245
|
1650
|
Г4-1БФМ-90
|
6
|
90
|
108
|
3750
|
3275
|
3104
|
450
|
710
|
3170
|
2220
|
В каждом фильтре
применено два одинаковых электродвигателя (мощностью 0,55 кВт и частотой
вращения n=1370 об/мин). Один электродвигатель используется
для привода продувочно - встряхивающего механизма, второй — шлюзового затвора.
Допустимое разрежение внутри фильтра не более 3000 Па. Продолжительность встряхивания
и продувки рукавов каждой секции 12...15с вместо 30с в фильтре ФВ, высота
подъема рукавов при встряхивании 40мм. Число ударов встряхивающего механизма за
цикл продувки семь. Интервал между циклами продувки и встряхивания 3...4 мин.
Рукавные встряхивающиеся тканевые
фильтры применяются для улавливания как тонких, так и грубых фракций пыли. Они
обладают достаточно высокой эффективностью пылезадержания (до 99,8%). К.
недостаткам этих фильтров относят сложность конструкции, громоздкость,
необходимость высококвалифицированного обслуживания.
На мукомольных заводах в основном
применяются фильтры типа ГЧ-1БФМ-30; 45; 60; 90 (цифра — суммарная площадь
фильтрующей поверхности в м2).
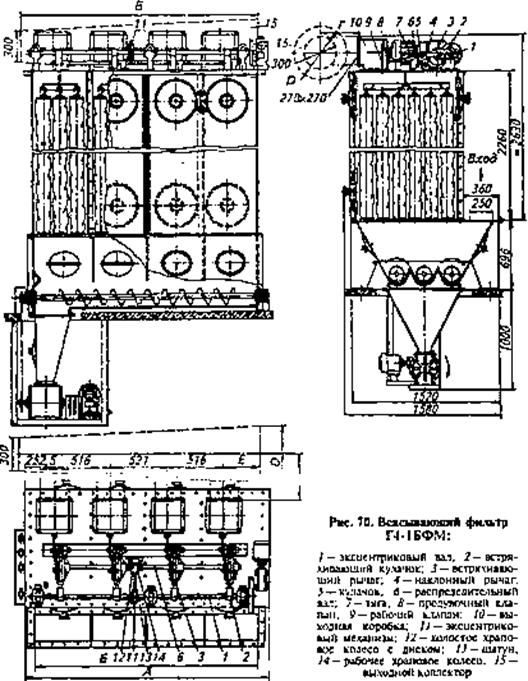
Рис.29
Всасывающий фильтр Г4-1БФМ
1-эксцентриковый
вал, 2-встряхивающий кулачок, 3-рычаг, 4- наклонный рычаг, 5- кулачок, 6-
распределительный вал, 7- тяга. 8- продувочный клапан, 9-рабочий
клапан,10-выходная коробка, 11- эксцентриковый механизм, 12-храповое колесо с
диском, 13- шатун, 14-рабочее храповое колесо, 15- выходной коллектор.
Фильтрующим элементом таких фильтров
является матерчатый рукав диаметром 135 мм и длиной 2090 мм, изготовленный из фильтрующей ткани.
Рабочее разрежение в корпусе фильтра допускается до 10000Па из условия
прочности конструкции. В качестве фильтрующей ткани используется «сукно № 2» с
шерстяным утком и хлопчатобумажной или льняной основой. Такими же фильтрующими
способностями обладают хлопчатобумажные ткани типа вельветона и замши
спортивной. Они достаточно плотны, имеют хороший начес (ворс). Кроме того,
может применяться синтетическое волокно лавсан и др.
Воздушная рабочая нагрузка на ткани
выбирается такой, чтобы предельная условная пылевая нагрузка для чистошерстяных
тканей и тканей из синте-тических волокон не превышала 1500 г/м2 •
ч; для «сукна № 2» - 1000 г/м2
• ч; для хлопчатобумажных тканей - 750 г/м2 • ч (например, если
начальная запыленность воздуха составляет- 15 г/м3, то удельная
воздушная нагрузка ( для «сукна № 2» будет равна:
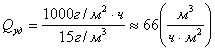
Для фильтров с продувкой фильтрующей ткани
атмосферным воздухом = 90...120 м3/ч
• м2; при импульсной продувке
сжатым воздухом = 400 м3/ч
• м2.
Обладая высокой эффективностью
очистки воздуха, рукавные фильтры быстро засоряются и для длительной стабильной
работы требуют специальных устройств для
систематической регенерации фильтрующего
слоя. Регенерация осуществляется встряхиванием рукавов и обратной продувкой
ткани атмосферным или сжатым воздухом.
Фильтрующие рукава в рукавных
фильтрах могут работать по следующим схемам: подача запыленного воздуха внутрь
рукава; подача запыленного воздуха снаружи.
На рис. 30 представлена схема фильтра
с подачей воздуха внутрь рукава с обратной продувкой атмосферным воздухом.
Ворсистую фильтрующую ткань от
осевшей пыли очищают обратной продувкой воздуха и периодическим встряхиванием
рукавов. Расход воздуха на обратную продувку составляет 10... 15 % от общего
количества воздуха, поступающего в фильтр.
Для вывода пыли из фильтра применяют
шнеки и шлюзовые затворы. Аэродинамическое сопротивление фильтров зависит от
удельной воздушной нагрузки на ткань, которую выбирают в зависимости от
технологических машин, обслуживаемых аспирационной сетью. На рис. 31
представлен график для определения сопротивления фильтра по удельной воздушной
нагрузке.
Рекомендуемая удельная воздушная
нагрузка для матерчатых фильтров типа ГЧ-1БФМ: при двухступенчатой очистке -
120... 150 м3/час*м2; при одноступенчатой
- 75...90 м3/час•м2.
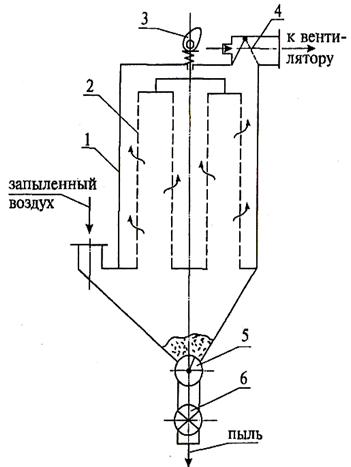
Рис. 30 Схема рукавного фильтра
1- корпус, 2- рукав, 3- кулачок, 4-перекидной клапан,
5- шнек, 6- затвор
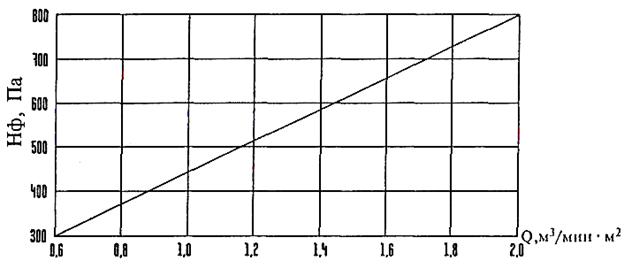
Рис.31
Зависимость сопротивления фильтра Н ф , от
воздушной
нагрузки на 1м2 ткани фильтра.
Лекция 15. Расчеты по
подбору фильтра.
По фактическому расходу воздуха и допустимой удельной
нагрузке определяют
расчетную площадь фильтрующей поверхности
По из справочника
подбирают фильтр с поверхностью равной или ближайшей к расчетной . Далее определяют действительную нагрузку на ткань , по которой определяют сопротивление фильтра по графикам или
номограммам.
На мукомольных, крупяных и
комбикормовых заводах при проектировании вентиляции и воздушного отопления
допускается использовать рециркуляцию воздуха, отработавшего в аспирационных и
пневмотраспортных сетях. Для этого воздух очищает до запыленности, не
превышающей 30% ПДК в рабочей зоне. В таких системах нашла применение мокрая
пылеочистка.
Увлажнение пылевых частиц, а также
смачивание поверхностей, предназначенных для улавливания и отведения пыли,
значительно повышает эффективность пылеотделителей при задержании мелкой пыли.
Применение жидкости облегчает задачу удаления задержанной пыли и устраняет опасность
воспламенения и взрыва. К недостаткам мокрых пылеотделителей можно отнести
сложность конструкции, расход воды за счет испарения и уноса, увлажнение
воздуха.
Сущность способа мокрой (влажной)
очистки воздуха от пыли заключается в том, что запыленный воздух пропускается
через завесу распыленной воды. Эффект распыления в данном случае достигается
форсунками, вращающимися лопастными колесами или гидродинамическим
взаимодействием потока воздуха и воды.
На практике для мокрой пылеочистки
воздуха применяются фильтры типов ФАМ, У1-БФА и др., промышленные кондиционеры
типа КТ и установки с гидродинамическим распылом воды типа «Омикрон». |