5. СИСТЕМЫ АВТОМАТИЧЕСКОГО КОНТРОЛЯ В ГАП
5.1. Самонастраивающаяся система активного контроля (САСАК)
Выбор принципа построения самонастраивающихся систем предопределяется требуемой точностью, доминирующим влиянием определенных факторов, экономичной самостоятельностью, условиями работы и т.д. Несмотря на разнообразие конструктивных схем САСАК возможно выделить общие закономерности формирования подналадочного (поднастроечного) воздействия: компенсирующего смещение настройки металлорежущих станков. Формирование подналадочного (поднастроечного) импульса рассмотрим на примере двухступенчатой САК, представляющую собой синтез прибора активного контроля в процессе обработки, и подналадчика [4, 5]. Структурная схема автоподнастроечной системы (рис. 54) включает в себя измерительное устройство ИУ статистический анализатор СА исполнительный механизм поднастройщика ИМП прибора контроля в процессе обработки.
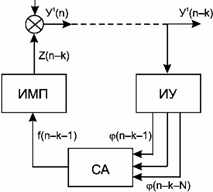
Рис. 54. Структурная схема автоподнастройщика
При регулировании размерного параметра отклонение Y'(n) контролируемого размера n-й детали можно представить в виде
Y'(n) = Y (n) + Z (n – k) (69)
где Z(n – k) – регулирующее воздействие механизма поднастройки (ИМП) в момент (n – k); k – число деталей, расположенных между позициями обработки и измерения.
Величина Y(n) может быть изменена только после окончания процесса обработки n-й детали. Поэтому процесс стабилизации контролируемого параметра около номинального значения заключается в оценке ожидаемого значения отклонения Y'(n) на основании измеренных Y'(n – k – 1)…… Y'(n – k – N) (N - число деталей в скользящей выборке) и введения регулирующего воздействия Z(n – k), направленного в сторону уменьшения ожидаемого Y'(n). Этот процесс происходит следующим образом. На ИУ поднастройшика, расположенное вне зоны обработки, поступают выборки деталей, сошедших со станка. Число дед алей в выборке ичановлено оптимальное N = 6 [8]. Система работает по скользящей медиане. По результатам измерения деталей СА выдает соответствующую команду ИМП. Работа СА может быть описана следующим образом [7,5,12]. Внутри поля допустимых отклонений контролируемого параметра Y'(n) устанавливаются зоны допустимых положений центра группирования. На выходе ИУ формируется информация Y(n) о величине отклонения медианы выборки от заданного номинала и о ее принадлежности определенной зоне допустимых значении центра группирования. Некоторые определенные значения сигнальных границ (+h,–h) определяют границы этих зон (+1,0,-1). При необходимости число зон может быть большим. В связи с чтим СА различают три состояния центра группирования: положения внутри 0-й зоны и выходы за ее положительную и отрицательную границы.
Вся полученная информация обрабатывается в СА по определенному алгоритму и после окончания измерения (n - k - 1) детали появляется сигнал f(n - k - 1), который может иметь один из трех уровней: О, А+. А-. Сигнал f(n - k - 1) поступает на ИМП, который осуществляет смешение настройки процесса на соответствующую величину. Если процесс не нуждается в поднастройке, появляется сигнал f(n - k - 1)=0.
В том случае Z(n - k) = Z(n - k - 1). Выход N/2 деталей выборки за одну из установленных границ –h или +h вызывает один импульс поднастройки. Тогда
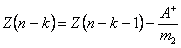
или
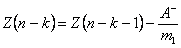
где m1(m2) - время переходного процесса поднастройки, шт. обработанных деталей,
А (А + ) - абсолютная величина отрицательного (положительного) импульса поднастройки.
Корректирующие воздействие ИМП
(71)
где – число отрицательных и положительных импульсов поднастройки, произведенных до момента j = n- k - 1. Сигнал f(j) является некоторой функцией φ(j), которая обозначает зоны и расположения отклонений j -ой детали
(72)
и по принятому алгоритму системы подается на поднастройку процесса, если любые N/2 детали выборки выходят за соответствующие границы зон
(73)
Неточность корректирующего воздействия ИМП будет обусловливать смещение центра группирования У0'(n)
(74)
Для полной компенсации функциональных погрешностей процесса величина импульса поднастройки при выборочном методе должна удовлетворять условию Na < А. Для выполнения этого условия диапазон возможных значений должен ограничиваться
(n = 1,2,...) (75)
где и определяются параметрами системы поднастройки.
Число возможных положений центров группирования в данной системе составляет

где a и σ – параметры, характеризующие процесс обработки; величину функциональной погрешности, приходящуюся на одну деталь и среднее квадратическое отклонение соответственно; С1 и С2 – параметры, характеризующие систему: коэффициенты рассогласования между Y0'(n) и границами ±h; b – наибольший общий делитель a и A.
Координата любого из р возможных положений центров группирования определяется величиной
(76)
где μ = (1,2,...,p) – порядковый номер положения центра группирования.
Определение закона распределения Y'(n) при n® ¥ можно осуществить по методике, изложенной в [19]. Состояние системы в момент времени n определяется двухмерным вектором r с компонентами Y0'(n) и t(n), где t(n) – время с момента последней поднастройки до момента n. Если последняя поднастройка произошла после k-ой детали, то t(n) = n – k при n – k < N + 1 и t(n) = N + 1 при n – k ³ N + 1. Из состояния и Т >N, характеризующегося моментом n, система в n+1 момент может перейти в одно из трех состояний:
(77)
При этом и никаких других состояний, кроме указанных в (77), быть не может. Согласно (77) вероятность перехода системы из одного состояния в другие Ri(μ), (i = 0, +1, –1) может быть представлена в виде явной функции от μ, не зависящей от номера детали n. Следовательно, процесс изменения состояний системы образует простую однородную цепь Маркова с конечным числом состояний и дискретным временем [19]. Процесс перехода системы из одного состояния в другое зависит от параметров исходного процесса обработки (a и σ), от величины подналадочного импульса А и установленных сигнальных границ ±h.
Величина среднего квадрата регулируемого размера Y'(n) определяется как [14]
(78)
где F(Y') – предельный закон распределения этого размера.
(79)
Здесь Pμ (μ = 1, …, p) вероятность нахождения центра группирования в точке с координатой Y'(μ).
После окончания процесса автоподнастройки ИУ и СА выключаются до прихода на ИУ детали с номером (п + m1,(2)) – 1). В противном случае неизбежно формирование ложных импульсов поднастройки, поскольку регулирующее воздействие Z(n – k) уменьшит ожидаемое значение отклонения регулируемого параметра Y на величину A–(+) только у деталей с номерами n' ³ n + m1,(2) – 1. Если после измерения (n – k – 1)-й детали СА выдал сигнал на поднастройку, то результаты измерения выборки, хранящиеся в СА, стираются и следующая выборка будет формироваться заново. Если же сигнал f(n – k – 1) = 0, то следующая выборка формируется путем замены (n – k – N)-й детали деталью с номером (n – k) и т.д. Частным случаем рассмотренного выше метода формирования импульса поднастройки является способ формирования при N=1, называемый подналадкой (поднастройкой) по одной детали, В этом случае первое же измерение, оказавшееся за пределами нулевой зоны, должно сопровождаться процессом поднастройки.
Определение оптимальных параметров САСАК, обеспечивающих минимальную погрешность обработки, можно осуществить методом математического моделирования на ЭЦВМ. Из рассмотренного принципа работы САСАК следует, что для построения алгоритма, моделирующего процесс автоматической поднастройки со случайным характером смещения уровня размерной настройки системы СПИД, требуются арифметические, логические и служебные операторы. На рис. 55 приведена блок-схема одного из возможных моделирующих алгоритмов [12].
Скачать блок - схему моделирующего алгоритма (Рис.55.)
Алгоритм состоит из пяти основных частей. Первая часть (операторы 1-9) обеспечивает формирование и хранение в памяти реализации исходного технологического процесса (без регулирования). Вторая часть (операторы 10-32) имитирует процесс обработки деталей между поднастройками. Третья часть (операторы 33 – 39) моделирует процесс регулирования размеров при отрицательной поднастройке. Четвертая часть (операторы 40-46) имитирует процесс регулирования размеров при положительной поднастройке.
Наконец, пятая часть (47-53) обеспечивает обработку результатов статистического моделирования и управления самим процессом моделирования (цикличность по А1 и вариантам n). При описании работы подалгоритмов приняты следующие обозначения: буквами f, Ф и К обозначены служебные операторы, выполняющие соответствующие функции, А – арифметические и Р – логические; индекс при букве соответствует номеру оператора на блок-схеме.
Оператор F1 обеспечивает формирование варианта n1 реализации случайного процесса обработки с автоматической поднастройкой, имеющего заданное сочетание параметров согласно оптимальной настройки моделирования. Затем управление передается оператору F2, который определяет величину импульса поднастройки Аi для данного процесса. Для осуществления поднастройки должно выполняться условие (принято ) Поэтому варианты значений Аi определялись по формуле

где Di=1.0; 1,1; 1,5; 2,0; 3,0; 6,0; 9,0
Оператор Ф3 формирует реализации стационарного случайного процесса смещений уровня размерной настройки системы СПИД .Здесь и далее Тn – максимальная протяженность реализации случайной размерной функции. Закон изменения задается соответствующим видом ее корреляционной функции Оператор Р4 проверяет условие . При выполнении этого условия, свидетельствующего о том, что формирование стационарной последовательности еще не закончено, управление по стрелке с индексом 1 возвращается к оператору Ф3, если условие не выполнено, т.е. сформированы, то управление по стрелке с индексом 0 передается оператору А5, который определяет текущий номер t2 и производит выборку соответствующего из совокупности Оператор Ф6 формирует реализацию случайной некоррелированной последовательности , представляющую собой дискретную реализацию с дисперсией . Оператор далее моделирует реализацию неслучайной функции , закон изменения которой известен. После этого оператор производит вычисление и хранение в памяти ЭЦВМ реализации случайной размерной функции
(80)
Наконец, оператор проверяет условие < . При выполнении этого условия управление по стрелке с индексом l передается оператору , и цикл формирования реализации повторяется. Если условие не выполнено, что соответствует окончанию формирования всей реализации случайной размерной функции протяженностью деталей, то управление по стрелке с индексом 0 передается оператору .
С оператора начинается работа второй части алгоритма. Оператор определяет момент времени - начало очередного цикла автоподнастройщика (после окончания последней поднастройки) и величину - регулирующее воздействие ИМП на данный момент времени. Далее оператор определяет номер r' (r' = 1,2,...) цикла обработки деталей после окончания последней подналадки, вычисляет номер очередной "обрабатываемой" детали ( + r'), производит выборку соответствующего из совокупности , вычисление и запоминание реализации итогового стационарного случайного процесса
(81)
Затем оператор проверяет условие . При выполнении этого условия по стрелке с индексом 1 передается оператору , проверяющему условие r' < k-1. Если последнее условие выполнено, т.е. детали с "исправленными" последней поднастройкой размерами еще не поступали на ИУ, то управление по стрелке с индексом 1 передается оператору . При r' = k-1 оператор по стрелке с индексом 0 дает разрешение оператору на начало цикла "измерения". Оператор определяет номер j (j =0,1,2,...) цикла "обработки" деталей после окончания последней "поднастройки", вычисляет номер ( очередной детали, поступающей на позицию измерения, производит выборку соответствующего из имеющейся на данный момент времени совокупности У'(t). После этого оператор проверяет условие , т.е. сравнивает отклонение "обработанной детали" со значением верхней границы +h измерительного устройства. При выполнении этого условия управление по стрелке с индексом 1 передается оператору , формирующему сигнал . Если это условие не выполняется, т.е. размер "измеряемой детали" не вышел за верхнюю сигнальную границу, управление по стрелке с индексом 0 передается оператору , формирующему сигнал . Соответствующий оператор , или , передает управление оператору ,, который записывает поступающий сигнал 1 или 0 в заданном порядке в ячейки , т.е. имитирует формирование скользящей выборки СА. Далее оператор , вычисляет величину сигнала , определяя количество деталей в выборке N, размеры которых вышли за верхнюю контрольную границу +h. Затем оператор проверяет условие . Если это условие выполняется, то управление по сделке с индексом 1 передается оператору , формирующему сигнал , т.е. "поднастройка "0". Этим дается разрешение оператору на управление путем проверки условия < (-h), что соответствует сравнению отклонения размера "измеряемой детали" со значением нижней сигнальной границы -h измерительного устройства. При выполнении этого условия управление по стрелке с индексом 1 передается оператору , формирующему сигнал ; при невыполнении условия управления по стрелке с индексом 0 передается оператору , формирующему сигнал . Соответствующий оператор дли передает управление оператору . Последний записывает поступающий сигнал 1 или 0 в заданном порядке в ячейки , имитируя формирование скользящей выборки статистического анализатора автоподналадчика.
Далее оператор вычисляет величину сигнала , т.е. определяет количество деталей в выборке N, размеры которых вышли за нижний контрольный предел (-h). Затем оператор проверяет условие . При выполнении этого условия управление по стрелке с индексом 1 передается оператору , формирующему сигнал , далее оператору , формирующему сигнал , и, наконец, оператору . Оператор определяет номер "детали", "обрабатываемой" в данный момент, производит выборку соответствующего из совокупности , вычисление и запоминание .
(82)
Затем оператор проверяет условие < . При выполнении этого условия управление по стрелке с индексом 1 передается оператору , разрешающему переход к очередному циклу "изменения" и "обработки" деталей. В этом случае управление передается оператору , и описанный цикл повторяется.Возвратимся к оператору . При невыполнении условия управление по стрелке с индексом 0 передается оператору , формирующему сигнал т.е. команду "подналадка “ “ и далее оператору счетчика числа отрицательных подналадок. Затем оператор определяет номер d' (d'=0,1,...) шага проходящей подналадки " ", вычисляет и запоминает величину регулирующего воздействия автоподналадчика в данный момент времени
(83)
После этого оператор  вычисляет номер  детали, "обрабатываемой" в данный момент, производит выборку соответствующего Y(t3) из совокупности Y(t2), вычисление и запоминание величины Y'(t4) и передает управление оператору P37. Оператор Р37 проверяет условие t4 < Тп. При выполнении этого условия управление по стрелке с индексом l передается оператору Р38. Оператор Р 38 проверяет условие d' = m - 1, т.е. проверяет, закончена ли производящаяся под yал fдка; если подналадка не закончена, то по стрелке с индексом l передается оператору команда на следующий шаг подналадки. Если d' = m - 1, т.е. подналадка окончена, то по стрелке с индексом 0 управление будет передано оператору F39. Оператор F39 формирует сигналы  и  , передает управление оператору A10, начинающему новый цикл обработки с подналадкой.Возвратимся теперь к оператору Р27. При невыполнении условия  , т.е. при выходе  деталей скользящей выборки за нижний предел, управление по стрелке с индексом 0 передается F40, формирующему сигнал  (команда на положительную подналадку). Далее оператор К41 прибавляет единицу к имеющемуся числу n(2) положительных подналадок и передает управление оператору А42. Оператор А42 определяет номер d' (d' = 0,1, ...) шага проходящей подналадки А+ вычисляет и запоминает величину регулирующего воздействия автоподналадчика , в данный момент
 (84)
Затем оператор А43 вычисляет номер t4 (t4 =t3 + d') "детали ", "обрабатываемой" в данный момент времени, производит выборку соответствующего Y(t4) из совокупности Y(t2) вычисляет и запоминает величину Y'(t4):
 (85)
После этого оператор Р44 проверяет условие t4 <Тп. При выполнении этого условия управление по стрелке с индексом 1 передается оператору Р45, проверяющему условие d' <m-1. Если последнее условие выполнено, то управление по стрелке с индексом 1 передается оператору А42. Если d' = m - 1, т.е. последняя подналадка закончена, то управление по стрелке с индексом 0 передается оператору F46. Оператор F46 формирует сигнал  и  и передает управление оператору A10, который начинает новый цикл обработки и подналадки.
Возвратимся к операторам Р12,Р31,Р37 и Р44. При невыполнении условий, проверяемых перечисленными логическими операторами, управление от них по стрелке с индексом 0 передается оператору Р47. Оператор Р47 производит математическую обработку итогового стационарного случайного процесса Yr(t), вычисляет его параметры:
математическое ожидание M[Y']
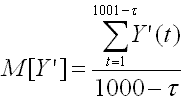 (86)
дисперсию D[Y']
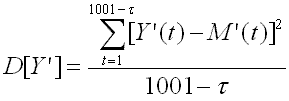 (87)
среднеквадратическое отклонение σ1[Y']
 (88)
средний квадрат отклонения M[(Y')2]
 (89)
корреляционную функцию KY'(τ)
(90)
Затем оператор А48 выдает на печать результаты обработки и передает управление оператору F49 который осуществляет переход к следующему значению величины подналадочного импульса Аi . Далее оператор Р50 проверяет условие i < 7. При выполнении этого условия управление по стрелке с индексом 1 передается оператору F7 и начинается моделирование этого же процесса обработки с новым значением величины подналадочного импульса. При невыполнении условия i < 7, т.е. при переборке всех значении Аi управление по стрелке с индексом 0 передается оператору F51, формирующему команду на переход к очередному варианту п1 технологического процесса. Затем оператор Р52 проверяет условие n1 < 25. При выполнении этого условия управление по стрелке с индексом 1 передается оператору F], формирующему очередное сочетание параметров исходного технологического процесса. При невыполнении условия n1 < 25, т.е. при переработке всех 25 вариантов запланированных производственных процессов, управление по стрелке с индексом 0 передается алгоритму Я53. Оператор Я53 выдает команду на окончание моделирования.
Модификации описанного алгоритма могут быть использованы при моделировании различных методов подналадки.
Применение метода математического моделирования на ЭЦВМ технологических процессов с автоподнастройкой позволяет повысить объективность выводов и точность вычислений при расчете оптимальных параметров автоподналадчиков для регулирования конкретных технологических процессов и существенно снизить трудоемкость этих расчетов.
5.2. Повышение информативности и точности контроля процесса обработки с помощью САК с жесткой настройкой
Точность собственной САК обусловлена процессами, происходящими в измерительном механизме (ИМ), отчетно-командном устройстве (ОКУ) и исполнительных цепях системы СПИД. Отсчетно-командное устройство при этом обеспечивает управление процессом обработки через главную обратную связь. Время срабатывания ОКУ, инерционность исполнительных и рабочих органов системы СПИД, их чувствительность влияют на величину "перебега" шлифовального круга, увеличивая рассеяние размеров обрабатываемых деталей [12]. Величина "перебега" зависит также от изменения режущей способности шлифовального круга.
Рассмотрим формирование радиус-вектора R(t) обрабатываемой детали (рис.56).
Для количественной оценки формирования радиуса R(t) детали достаточно рассмотреть систему с; одной степенью свободы, так как обрабатываемая деталь и шлифовальный круг фиксированы в осях вращения. Взаимодействие шлифовального круга и обрабатываемой детали описывается дифференциальным уравнением второго порядка
 (91)
где m - приведенная масса детали; р1 - коэффициент успокоения горизонтальных колебаний детали; с1 - поступательная жесткость системы "деталь-центры" в направлении врезной подачи (рис.56,а).
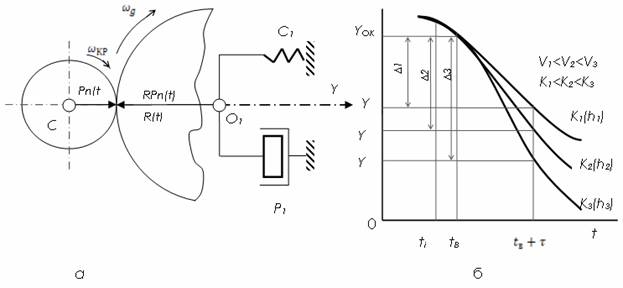
Рис.56. Схема взаимодействия шлифовального круга с обрабатываемой деталью: а - формирование радиус-вектора обрабатываемой детали; б - типовая зависимость величины "перебега" от режущей способности шлифовального круга
При прецизионном шлифовании для получения заданного значения функции R(t) с минимальными погрешностями размера и формы применяются циклы с выхаживанием. Решение (91) для периода выхаживания имеет вид
Здесь R - значение Y(tB) в момент времени tB (начало выживания); Ej, Nj - амплитуды простых гармоник сечения детали и колебания оси детали относительно ее среднего положения, не приводящих к снятию стружки; Dl, D2 - амплитуды свободных колебаний; λ - частота собственных колебаний; ωj - частота вынужденных колебаний; f - коэффициент затухания собственных колебаний Pn(t) - коэффициент затухания нормальной составляющей силы резания при выживании [1]
(93)
где hc - коэффициент затухания, обусловленный жесткостью системы СПИД; р- коэффициент пропорциональности; Кр - коэффициент режущей способности шлифовального круга, равный отношению скорости съема припуска к нормальной составляющей силы резания.
Поскольку в выражении (92) f >>h, то первый член функции Y(t) быстро убывает и при сколь-нибудь длительном выхаживании следует принимать во внимание только второй член. Процесс выхаживания уменьшает натяг в системе "деталь-центры-круг" до минимума. По мере уменьшения натяга динамические параметры системы будут все более приближаться к параметрам упругой системы станка на холостом ходу.
Съем припуска с детали начинается при достижении в системе некоторого критического натяга Рк, являющегося функцией режущей способности круга. На величину Рк влияют также силовые δp(t) и тепловые δT(t) деформации системы СПИД, ведущие к перераспределению усилий в системе "деталь-центры-круг".
Однако, можно считать, что влияния δp(t) и δT(t), приводящие к изменению протяженности звеньев размерной цепи станка и, как следствие, к изменению толщины снимаемого слоя с обрабатываемой детали, сказываются и на изменение коэффициента режущей способности шлифовального круга. Поэтому можно принять изменение величины за интегральную оценку влияния на процесс шлифования и других факторов, в частности, δp(t) и δT(t), т.е.
Pk(t) = P[Kp(t)] (94)
причем чем больше коэффициент Кр, тем меньше значение Рк.
Съем припуска с детали прекращается при величине натяга, соответствующего некоторому значению Рк, при котором в зоне контакта детали и шлифовального круга происходят только процессы трения и скобления вследствие перехода от микрорезания к пластическому и далее к упругому и пластическому контакту. В результате ухудшается качество поверхности и могут возникнуть автоколебания, еще более искажающие рельеф детали. Следовательно, пропроцесс шлифования должен быть прекращён при натяге P0, несколько большим Рk, т.е.
, (95)
где . Здесь - критическое значение натяга перед очередной правкой круга, т.е. при минимальном значении Kp.
При шлифовании в двухступенчатом цикле с выхаживанием [18] с применением САК врезная подача согласно (92) прекращается при достижении определённого размера R и далее съём припуска происходит под действием созданного в системе СПИД натяга. Форма соответствующей экспоненты определяется величиной коэффициента затухания h , а её наклон к оси абсцисс в момент начала выхаживания – скоростью съёма припуска V , которая в общем случае не стабильна; она изменяется под влиянием случайных факторов и флуктуаций режущей способности круга. Инерционность системы СПИД при шлифовании с САК характеризуется временем «выбега» τ , т.е. временем между подачей сигнала на овод круга и фактическим началом отвода. Поэтому стабильность размеров партии деталей обеспечивается при условии выдачи окончательной команды САК при одном и том же значении скорости съёма припуска (рис.56,б). Величина «перебега» в этом случае будет зависеть только от изменения режущей способности круга.
Аналитическое выражение алгоритма управления точностью обработки с помощью САК можно установить путём анализа зависимости величины «перебега» от режущей способности шлифовального круга (рис.56,б).
Форма экспоненты кривых зависит от режущей способности шлифовального круга , а их наклон к оси абсцисс – скоростью съёма припуска . Экспоненциальный закон съёма припуска при выхаживании определяется функцией
, (96)
где R – значение функции Y(t) в момент начала выхаживания, который характеризуется временем .
Покажем, каким должен быть уровень срабатывания предварительной команды САК для достижения заданного значения размера при постоянной скорости съёма припуска независимо от величины скорости съёма припуска в период его установившегося съёма
,
. (97)
Из (97) путём простых преобразований получим
;
и (98)
Алгоритм формирования предварительной команды для i-го цикла согласно (98) запишется в виде
(99)
Здесь – уровень срабатывания окончательной команды (ОК) в (i-1)-м цикле; - скорость съёма припуска в i-м цикле в период врезания; - скорость съёма припуска в момент выдачи окончательной команды в (i-1)-м цикле.
С учётом влияния формы экспоненты, поскольку

и, следовательно, получим алгоритм формирования предварительной команды (ПК)
(100)
где - коэффициент режущей способности круга в i-м цикле (практически ); – значение натяга в момент выдачи окончательной команды в (i-1)-м цикле.
Выражение (100) представляет собой алгоритм формирования ПК САК, обеспечивающий достижение уровня срабатывания ОК при определенной и постоянной скорости снятия припуска независимо от её вариаций в период врезания и изменения режущей способности круга. Синтезируем алгоритм формирования ОК САК, компенсирующий влияние изменения режущей способности шлифовального круга на величину «перебега» ∆. Из графика (56,б) следует, что
и ,
т.е. . (101)
Разложив функцию - в ряд Маклорена и, ограничиваясь двумя первыми членами ряда, получим . Величина перебега в i-м цикле определится из выражения
(102)
В выражении (102) h=var, τ=const, что позволяет осуществить контроль величины h(t), зная функцию Y(t). Действительно, так как
и , а , ,
то (103)
Выполнить соотношение (103) можно, управляя параметром . Из (103) , откуда .
Следовательно,
, (104)
где - скорость съёма припуска в момент выдачи ОК в 1-ом цикле после правки. Окончательно алгоритм управления шлифованием с помощью САК может быть представлен в виде
(105)
Реализация алгоритма (105) позволяет корректировать уровень срабатывания ПК таким образом, чтобы достигнуть заданного значения размера обрабатываемой детали при постоянной скорости съёма припуска независимо от изменения режущей способности шлифовального круга и вариаций величины врезной подачи шлифовальной бабки; корректировка уровня срабатывания ОК сводит к минимуму влияние режущей способности круга на величину "перебега". Преимуществом приведенного в (105) алгоритма является возможность его реализации на базе серийного двухкомандного устройства активного контроля, снабженного измерителем нормальной составляющей силы резания (ИСР) и блоками корректировки уровней срабатывания предварительной (КПК) и окончательной (КОК) команд, которыми управляет мини-ЭВМ, вычисляющая значения и (рис.57,а). Схема вычисления алгоритма (105) представлена на рис. 57,б.
Величина съема припуска контролируется измерительным наконечником ИМ САК, который кроме информации о размере обрабатываемой детали воспринимает возмущения, обусловленные взаимодействием узлов и рабочих процессов динамической системы станка. Этот массив информации отображается на работе ИМ в виде монотонных и колебательных перемещений наконечника и может быть представлен в виде вектора В(t)=В{b1(t),b2(t),b3(t)} динамического состояния измерительного наконечника. Вектор В(t) характеризуется постоянной b1, монотонной b2(t) и многочастотной b3(t) составляющими.
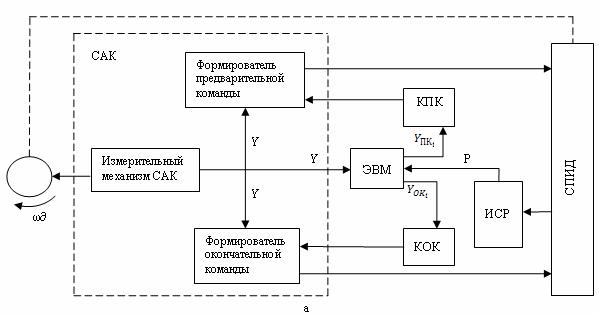
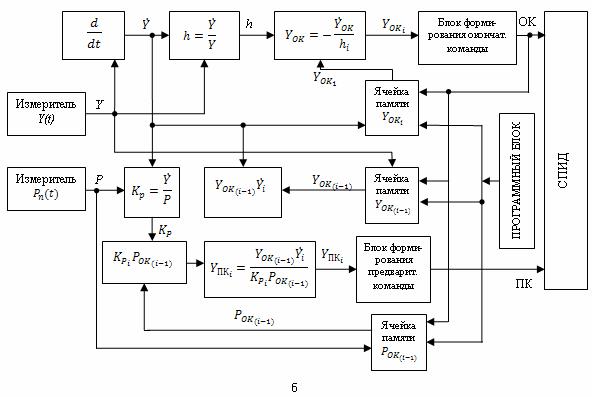
Рис.57. Реализация оптимального алгоритма управления шлифованием: а – структура САК с реализацией оптимального алгоритма управления шлифованием; б – схема вычисления оптимального алгоритма управления
, (106)
где b1 = R0 – исходное значение контролируемого параметра (радиус заготовки);
b2(t) = R(t)t – монотонная составляющая вектора В(t), пропорциональная скорости R(t) съема припуска;
– многочастотная составляющая вектора, обусловленная воздействием микронеровностей поверхности контролируемой детали, рабочими процессами и внешними воздействиями на упругую систему станка. Монотонная составляющая вектора В(t) зависит от величины натяга в системе "круг-деталь", режущей способности шлифовального круга, режима обработки и физико-химических свойств заготовки. Многочастотную составляющую вектора В(t) определяют рельеф контролируемой поверхности, линейная скорость вращения детали, сила резания, режущая способность шлифовального круга, вибрации детали и друге параметры рабочих процессов и внешних воздействий в динамической системе станка. Поэтому анализ составляющих вектора В(t) может дать обширную информацию о характере процесса формообразования.
5.3. Автоматический контроль на станках с ЧПУ
В настоящее время вопросы повышения точности и производительности на станках с ЧПУ решаются двумя путями [3].
Первый путь – что конструирование следящих приводов высокой точности. В применении к станкам с ЧПУ этот путь приводит к уменьшению погрешности на контуре та счет уменьшения погрешностей вдоль каждой из координат станка. Указанный путь не учитывает, что отдельные координаты движения рабочего узла станка с ЧПУ связаны между собой функционально или, в общем случае, корреляционно, например, через систему управления, процессы трения и деформации в системе и технологические процессы. Если этими связями пренебречь, то структурная схема многокоординатного привода станка с ЧПУ разобьется на отдельные одномерные следящие приводы, число которых будет равно числу управляющих координат. Методы построения одномерных следящих приводов высокой точности хорошо известны и широко освещены в литературе. Эти методы включают в себя выбор быстродействующей части привода (усилитель мощности, двигатель, редуктор) и синтез цепей управления, позволяющих полностью реализовать быстродействие силовой части привода (последовательно корректирующие устройства, местные обратные связи и т.д.).
Выбор достаточно быстродействующей силовой части привода является необходимым условием для воспроизведения тех скоростей и ускорений, которые заданы в программе. Одновременно очень важно обеспечить плавность движения исполнительных узлов станка с ЧПУ на малых так называемых "ползучих" скоростях. В настоящее время не существует хорошей методики выбора силовой части привода с учетом, как наибольшего быстродействия, так и плавности движения на "ползучих" скоростях. При синтезе цепей управления нужно стремиться по возможности полностью реализовать те динамические свойства силовой части привода, которыми она обладает. Неправильно выбранные коэффициенты усиления по скорости, ускорению и моменту, а также корректирующие цепи могут снести к минимуму достоинства силовой части привода.
Из теории автоматического регулирования известно, что установившиеся составляющие погрешностей следящего привода зависят от коэффициентов усиления (по скорости, по ускорению, по момент и т.д.), а переходные составляющие - от частоты среза ЛАЧХ (логарифмическая амплитудочастотная характеристика) разомкнутого следящего привода или от величины собственной частоты замкнутого привода. Но увеличение коэффициентов усиления и частоты среза ЛАЧХ сопровождается ухудшением условий устойчивости замкнутого следящего привода. Поэтому синтез систем управления высокоточных следящих приводов, работающих с большими ускорениями, является сложным вопросом с неоднозначным решением.
Второй путь - это разработка таких методов получения программ для станков и автоматов с ЧПУ, которые позволили бы повысить производительность обработки путем использования форсированных режимов, поскольку погрешность обработки выходит за допускаемые пределы гораздо раньше, чем используются предельные динамические возможности привода. Точность обработки пытаются повысить за счет учета особенностей привода с ЧПУ. Такие методы получения программ для станков с ЧПУ достаточно известны. Они включают изменение масштаба времени программы, подыскание программы и некоторые другие методы, не обеспечивающие достаточно высокую точность обработки вследствие случайного влияния различных факторов.
Метод изменения масштаба времени программы заключается в замедлении скоростей обработки детали для снижения динамических погрешностей, поскольку они уменьшаются с понижением скоростей и ускорений. Масштаб времени программы обычно изменяется в зависимости от особенностей технологической программы и с учетом динамических свойств привода.
Автоматическое изменение темпа выдачи программы в зависимости от погрешности слежения уменьшает установившиеся составляющие погрешности, но не уменьшает, а даже увеличивает ее переходные составляющие. Поэтому, чтобы использовать этот метод, нужно синтезировать следящие приводы с малыми переходными составляющими погрешности, либо снижать скорости обработки при составлении технологической программы в местах резких искривлений траектории режущего инструмента. Данный метод не обеспечивает также необходимую точность обработки.
Случайный характер таких определяющих точность обработки факторов, как износ режущего инструмента, тепловые и силовые деформации системы СПИД, затрудняет их компенсацию путем предварительной настройки станка методом предыскажения программы или заданием законов изменения этих факторов в качестве исходных данных для работы системы программного управления.
Новый метод повышения точности и производительности обработки на станках с ЧПУ основан на использовании активного контроля для внесения коррекции в программы станков с ЧПУ. Разработка этого метода стала возможной благодаря развитию в последнее время систем автоматизированного проектирования (САПР) и в первую очередь САПР, имеющих возможность выпускать управляющие ленты для станков с ЧПУ. Суть этого метода заключается в том, что после обработки деталь на той же позиции, т.е. при совмещении технологической и измерительной баз, измеряется при помощи индуктивной (для деталей сложной формы) или оптической (для печатных плат) измерительных систем, и по результатам измерений вносится коррекция в технологическую программу станков с ЧПУ с помощью контрольной программы. Обратную размерную связь между станком с ЧПУ и системой автоматизированного проектирование реализует контрольная программа. Благодаря этой обратной связи появляется возможность рассматривать выше названные САПР и станки с ЧПУ как звенья одной цепи – цепи полной автоматизации получения готовой продукции: от проектирования до изготовления (рис.58). Наличие в станках с ЧПУ контрольной программы представляет собой реализацию главной обратной связи.
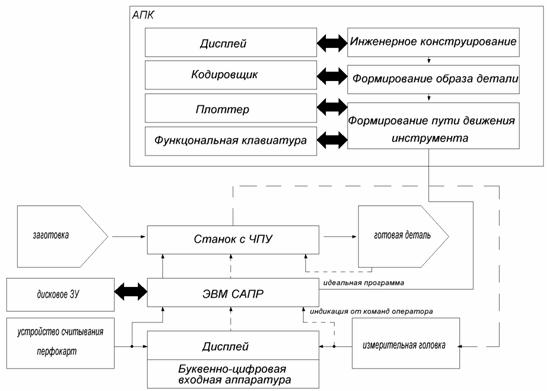
Рис.58. Типовая структурная схема проектирования и изготовления сложных деталей с применением САПР контрольной программы: АПК – автоматизированный проектный комплекс; Плоттер – прецизионный графопостроитель; ЗУ – запоминающее устройство
Использование контрольной программы на станках с ЧПУ позволяет совместить в них функции, присущие как станкам, так и контрольно-измерительным машинам (КИМ).
Таким образом, активный контроль для внесения коррекции в программы станков с ЧПУ, реализуемый при помощи контрольной программы и контрольно-измерительных головок, является универсальным способом повышения точности и производительности обработки деталей сложной формы на станках с ЧПУ.
В связи с введением понятия контрольная программа для станка с ЧПУ, которая воспроизводит с малыми скоростями и ускорениями с необходимой точностью заданный контур детали, возникают вопросы, как её рассчитать и как часто она должна включаться. Для ответа на эти вопросы сначала установим взаимосвязь между контрольной и технологической программами.
При сопоставлении технологической программы для плоских деталей сложной формы на перфоленте или магнитной ленте фиксируют: исходное положение инструмента и заготовки, режимы резания (выбирают на основании стойкости инструмента и материала заготовки), перемещения стола станка , (описывают точные геометрические формы готовой детали). Обозначим весь этот массив информации через {A}.
В процессе многократного воспроизведения массива информации {A} могут происходить следующие изменения, которые не учтены в этом массиве: изменение температуры окружающей среды; износ режущего инструмента и, как следствие, увеличение силы резания, т.е. увеличение силовой деформации системы СПИД; нагрев системы СПИД; изменение напряжения и силы тока в сети, к которой подключён станок с ЧПУ; изменение припуска на обработку (вызывает изменение силы резания при обработке группы деталей); старение элементов (как электрических, так и механических при длительной работе станка).
Кроме того любой станок с ЧПУ обладает передаточной функцией W(p) и, соответственно, воспроизводит массив информации {A} с некоторым искажением.
Эти искажения в первую очередь объясняются наличием двух погрешностей привода:
- установившейся погрешности привода (рис.59)
, (107)
где - коэффициент погрешностей; - входная величина;
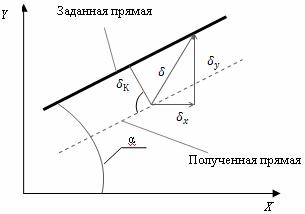
Рис.59. Погрешности при воспроизведении прямой линии: - векторная погрешность; и - погрешности по соответствующим координатам; - погрешность на контуре
- переходной погрешности привода , вызванную перерегулированием в приводе (рис.60).
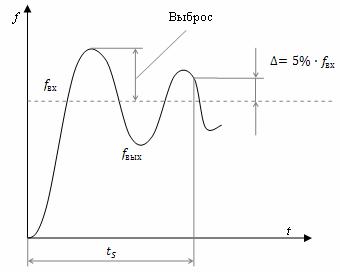
Рис.60. К определению длительности переходного процесса: tS - длительность переходного процесса
Все вышеперечисленные фактора приводят к тому, что контур готовой детали отличается от заданной геометрической формы на величину погрешности на контуре (рис.61).
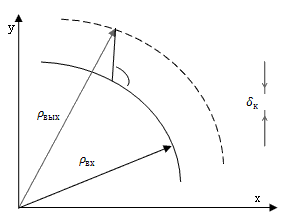
Рис.61. К оценке погрешности на контуре: - радиус-вектор точки, принадлежащей заданному контуру и наименее удалённый от точки, являющейся концом радиус-вектора на полученном контуре
В контрольную программу, состоящую из массива информации {B}, входят: исходное состояние контрольно-измерительной головки и обработанной детали, перемещения стола станка , , скорости и ускорения этих перемещений. Причём скорость и ускорение, а также величину перемещения контрольно-измерительной головки для каждого типового участка профиля детали выбирают на основании учёта передаточной функции привода так, чтобы погрешность на контуре для этого участка профиля детали была заведомо меньше допустимой погрешности воспроизведения этого участка профиля, т.е. чтобы выполнялось следующее неравенство:
(108)
При составлении контрольной программы можно использовать как переменный масштаб времени программы, так и дополнительные сигналы коррекции, а именно низшие производные от исходной технологической программы, если для составления контрольной программы используется ЭВМ. Если станок с ЧПУ работает совместно с системой автоматизированного проектирования, то для составления контрольной программы используют результаты математического моделирования работы привода станка с ЧПУ.
При воспроизведении массива информации {B} на станке с ЧПУ могут происходить следующие изменения: изменение температуры окружающей среды (кратковременное, так как контрольная программа включается на станке с ЧПУ один раз, а время её отработки мало по сравнению со временем обработки небольшой партии деталей); изменение напряжения и тока в сети.
Массив информации {B} контрольной программы привод станка воспроизведёт так, что на выходе будет получен контур детали, для которого выполняется неравенство (108).
Сравнивая измерения, которые могут происходить при воспроизведении массивов информации {A} и {B} можно заметить, что контрольная программа позволяет компенсировать погрешности при обработке детали, вызванные изменением каких-либо параметров следящего привода (увеличение люфта, износ и затупление режущего инструмента, погрешность от тепловых и силовых деформаций системы СПИД), изменением внешних условий (повышение температуры окружающей среды, увеличение влажности и т.д.). Как всякая подналадочная система, контрольная программа позволяет компенсировать только медленно изменяющиеся функциональные (коррелированные) погрешности и не компенсирует собственно случайные погрешности (высокочастотные составляющие погрешности обработки). Однако, как показывают исследования, влияния различных составных частей погрешности обработки на станке с ЧПУ, удельный вес некомпенсируемых собственно случайных погрешностей обработки весьма невелик (меньше 10%). Таков же примерно удельный вес и погрешностей измерения при помощи контрольно-измерительной головки, перемещаемой по контрольной программе, в общем объёме суммарной погрешности обработки.
Кроме сказанного выше, контрольная программа позволяет учесть динамические погрешности слежения в приводе станка с ЧПУ при обработке первой детали и при помощи различных технических решений снизить их в приводе при обработке следующих деталей.
Основываясь на вышеприведённых рассуждениях и используя теорию подналадочных систем, при рассмотрении взаимосвязи контрольной и технологической программ надо различать две задачи, которые решает контрольная программа.
Первая задача: после обработки первой пробной детали контрольная программа позволяет устранить погрешности в местах резких искривлений траектории движения режущего инструмента, установившейся погрешности слежения, деформация системы СПИД и т.д. Результатом решения этой задачи является получение усовершенствованной технологической программы.
Вторая задача: в процессе обработки большой партии деталей контрольная программа выполняет функцию обычной подналадочной системы, которая периодически осуществляет коррекцию технологической программы станков с ЧПУ.
Однако на станках с ЧПУ (при мелкосерийном производстве) обычно обрабатывают небольшие партии деталей, поэтому достаточно одной поднастройки станка в процессе обработки всей партии деталей, и контрольной программе обычно не приходится решать вторую задачу.
Для точного расчета контрольной программы нужно установить зависимость погрешности воспроизведения заданного контура детали от скорости и ускорения перемещения контрольно-измерительной головки для данного типа привода станка с ЧПУ и приводов других видов.
Для станков с ЧПУ нужно различать как статическую, так и динамическую точности, которые соответственно определяются погрешностями статической и динамической настройки станка.
Суммарная погрешность обработки детали определяется как погрешностью статической настройки , так и погрешностью динамической настройки станка, т.е.
(109)
Погрешность статической настройки станка с ЧПУ складывается из нескольких составляющих. Основные из них: а) погрешность датчика положения; б) погрешность, связанная с зазором в кинематической цепи между датчиком положения и управляемым органом станка; в) погрешность, вызванная действием статического момента нагрузки при трогании (усилия трения в направляющих, усилия резания).
Погрешность динамической настройки станка с ЧПУ будет определяться следующими основными составляющими: а) скоростной ошибкой слежения; б) ошибкой слежения, обусловленной ускорением; в) ошибками, обусловленными более высокими производными входного воздействия; г) моментной ошибкой слежения; д) ошибками слежения, вызываемыми скачками воздействия или его производных.
При этом уравнение (109) не нужно понимать как простое алгебраическое суммирование погрешности статической и динамической настройки станка, так как последние в свою очередь характеризуются соответственно математическими ожиданиями:
,

и средними квадратичными отклонениями:
,

относительно математических ожиданий.
Для станков с ЧПУ, работающих в режиме слежения при фиксированных значениях сигнала программы, контрольную программу целесообразно использовать в приводах, работающих с высокой производительностью. Например, сверлильный станок с ЧПУ для сверления печатных плат имеет производительность 4 отверстия в секунду. Если привод работает в низкодинамическом режиме и время переключения кадров программы достаточно, чтобы прекратился переходной процесс, обусловленный колебаниями ротора, то погрешность обработки детали будет определяться только статической точностью, и для повышения ее можно использовать специальные программы "доползания". В таком режиме обычно работают прециозные координатно-расточные станки.
Нужно отметить, что в настоящее время системы подналадки станков с ЧПУ, использующие для получения усовершенствованной технологической программы контрольную программу, можно применять на двухкоординатных приводах станков с ЧПУ. Применение таких подналадочных систем на трех- и многокоординатных приводов станков с ЧПУ сопряжено с большими технологическими трудностями. Это объясняется особенностями подналадки для двух-и трехкоординатных приводов станков с ЧПУ.
На рис.62 показан процесс подналадки для двухкоординатного привода. Заданная траектория движения режущего инструмента АВ и полученная при обработке плоской детали траектория движения режущего инструмента А'В' лежат в одной плоскости . В процессе контроля, когда двухкоордашатный привод станка с ЧПУ работает по контрольной программе, погрешности в приводе, обусловленные установившейся и переходной составляющими ошибками слежения, будут весьма малы по сравнению с погрешностями, обусловленными ошибками слежения при обработке детали. В результате этого будет измеряться не реальная погрешность на контуре δреал, а погрешность обработки δизм вдоль одной из координат станка. Если же деталь не обладает достаточной жесткостью в плоскости F0, то будут накладываться дополнительные погрешности, обусловленные нежесткостью системы СПИД (см. рис.62).
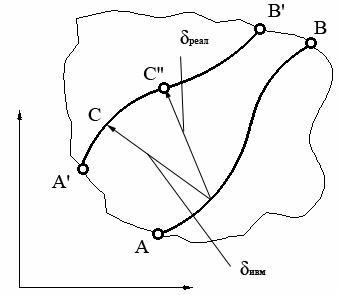
Рис.62. Особенности процесса подналадки для двухкоординатного привода станка с ЧПУ
Имея приближенную математическую модель шагового привода и зная формулы определения погрешностей на контуре, обусловленных установившимися и переходными ошибками слежения, при автоматизированном получении усовершенствованной технологической программы, погрешности измерения, обусловленные несовпадением точек С¢ и С¢¢ можно компенсировать по следующей схеме:
xконтр = xисх ± δ*,
где xконтр – перемещение по оси х для контрольной программы в процессе измерения погрешностей воспроизведения фрагмента; xисх – перемещение по оси х для исходной технологической программы в процессе воспроизведения фрагмента; С'С" = δ* – векторная ошибка в процессе воспроизведения типового фрагмента (рассчитывается по формуле определения погрешностей обработки на контуре).
На рис.63 приведены особенности подналадки для трехкоординатного привода. Поверхность F0 – расчетная; на ней располагаются все точки траектории фрезы, по которой она должна двигаться, чтобы трехмерная деталь получилась идеально точной. Но из-за нежесткости системы СПИД, силовых и температурных деформаций, из-за погрешностей в приводе, обусловленных установившимися и переходными составляющими ошибки слежения, поверхность детали в этой точке обработана так, как будто инструмент двигался по траектории А'В', расположенной на некоторой поверхности F1. В процессе контроля (работает контрольная программа) измерительные усилия ничтожно малы по сравнению с силами резания, а также малы погрешности привода, обусловленные установившимися и переходными составляющими ошибки слежения. В результате этого центр щупа измерительного устройства (диаметр и форма участка щупа, двигающегося по изделию, совпадает с размерами фрезы) будет двигаться по линии А"В", регистрируя погрешности обработки АВ (δизм ) в направлении оси коррекции у. В этом случае наиболее точной будет такая величина поправки, в результате действия которой траектория движения фрезы А"В" при обработке следующей заготовки окажется совмещенной с расчетной поверхностью F0. Даже, если можно было бы измерять непосредственно погрешность на контуре δk (причем вектор δk не лежит в одной плоскости с вектором δизм), все равно определение такой корректирующей поправки сопряжено со значительными трудностями прежде всего потому, что после введения корректирующей поправки изменится толщина снимаемого слоя, что в свою очередь, вызовет изменение деформации системы СПИД в процессе обработки нового изделия, и траектории движения фрезы А"В" не совместится с расчетной поверхностью F0. В силу указанных обстоятельств первую корректирующую поправку для трехкоординатного привода станка можно получить только приближенно.
/html/Files/5.2.files/image019.gif)
Рис. 63. Особенности процесса подналадки для трехкоординатного привода станка с ЧПУ
На автоматизированном проектном комплексе при интерактивном проектировании получают исходную технологическую программу из условия максимального быстродействия станка с ЧПУ и контрольную программу, соответствующую идеальному профилю детали. Для этого в устройстве обмена автоматизированного проектного комплекса записывают для типовых участков профиля деталей траекторию движения электромеханической измерительной головки (рис.65, 66) с присвоением соответствующих символов и коэффициентов коррекции скорости и ускорения для контрольной программы.
/html/Files/5.2.files/image020.gif)
Рис. 64. Процесс получения усовершенствованной технологической программы на комплексе АПК – станок с ЧПУ: КНМЛ 1,2,3 – кассетные накопители на магнитной ленте
/html/Files/5.2.files/image021.gif)
Рис.65. Принципиальная схема электромеханической измерительной головки: 1 – измерительный стержень с шариком; 2 – пружины стабилизации; 3 – катушки индуктивности; 4 – шаровая опора; d – диаметр измерительного шарика; 5 – встроенный электронный блок
/html/Files/5.2.files/image022.gif)
Рис.66. Схема измерений электромеханической измерительной головки: CH – величина натяга; 1 – профиль готовой детали; 2 – идеальный профиль детали; 3 – контрольное поле; 4 – контур контрольной программы; 5 – траектория движения измерительного стержня при прохождении прямого угла; 6 – измерительный шарик
При получении исходной технологической программы кодируют профиль детали с набором соответствующих символов коэффициентов коррекции погрешности. После получения исходной технологической программы включают на автоматизированном проектном комплексе режим редактирования "1" (рис.67), позволяющий, используя устройство обмена УО и технологическую программу, получить контрольную программу, которую потом применяют в контрольном режиме на станке с ЧПУ. Расчет коэффициентов коррекции скорости, ускорения и погрешности дня каждого типового участка профиля детали производят во время математического моделирования привода станка с ЧПУ на ЭВМ. Используя контрольную программу, режим редактирования «2» (рис.68), технологическую программу и первую обработанную деталь на автоматизированном проектном комплексе, получают усовершенствованную технологическую программу. Измерение погрешностей обработки производится установленной на станке с ЧПУ контрольно-измерительной головкой, управляемой контрольной программой. Процесс получения усовершенствованной технологической программы для координаты Х (аналогично для координаты у) происходит автоматически по следующему циклу:
где Хусов – перемещение по оси х в усовершенствованной технологической программе ;
Хисх – перемещение по оси х в исходной технологической программе, определяют по идеальной траектории движения режущего инструмента; ±Х – погрешность обработки первой детали, возникающая в результате использования исходной технологической программы; Хкорр - значение сигнала коррекции на входе привода станка с ЧПУ, если на выходе перемещение режущего инструмента равно 1 мм, определяют в результате моделирования привода станка с ЧПУ на ЭВМ.
/html/Files/5.2.files/image023.jpg)
Рис.67. Алгоритм программы редактирования “1” на АПК для получения контрольной программы: ФС – фотосчитывающее устройство; ПЛ - перфоратор
/html/Files/5.2.files/image024.jpg)
Рис.68. Алгоритм программы редактирования “2” на АПК для получения усовершенствованной технологической программы: п/п - подпрограмма
Если величина больше , где - погрешность на контуре, то в этом случае, кроме коррекции на величину перемещения по оси «Х» вносят коррекцию по скорости и ускорению через коэффициенты, которые также рассчитывают при моделировании привода станка с ЧПУ на ЭВМ.
|