2. ПРИНЦИПЫ ПОСТРОЕНИЯ ОСНОВНЫХ ЦЕПЕЙ САК ГАП
2.1. Цели и задачи системы автоматического контроля
2.2. Метрологическое обеспечение ГАП
2.3. Техническая база САК ГАП
2.4. Нормативная база САК ГАП
2.5. Принципы построения измерительной и транспортирующей цепей
2.1. Цели и задачи системы автоматического контроля
Система автоматического контроля (САК) гибкого автоматизированного производства (ГАП) является его важнейшим звеном. Она решает следующие задачи:
- получение и представление информации о свойствах, техническом состоянии и пространственном расположении контролируемых объектов, а также о состоянии технологической среды;
- сравнение фактических знаний параметров с заданными;
- передача информации о рассогласованиях для принятия решений на различных уровнях управления ГАП;
- получение и представление информации об исполнении функций.
Различные уровни управления ГАП решают свои, свойственные им, задачи. Типовая структура САК ГАП, представленная на рис. 9, имеет три уровня [10]. Верхний уровень обеспечивает общий контроль совокупности автоматических ячеек (АЯ) для координации их взаимодействия и решения задач по получению, обработки и обобщению информации, поступающей с нижестоящего уровня (от АЯ); контролю объема и качества продукции; контролю над исполнением операций, выполняемых АЯ; самоконтролем и контролем функционирования нижестоящего уровня. Средний уровень осуществляет контроль АЯ и представление на верхний уровень обобщенной информации о свойствах, техническом состоянии и пространственном расположении контролируемых объектов и составах частей ячейки. На этом уровне решаются задачи получения и обработки информации о контролируемых параметрах объекта, параметрах функционирования ячейки и ее элементов, параметрах технологической среды, контроля качества изготовления объекта обработки на элементарных автоматизированных системах (ЭАС), входящих в ячейку; самоконтроля и контроля функционирования нижестоящего уровня. Нижний уровень обеспечивает контроль объектов обработки, технического состояния и пространственного расположения составных частей ЭАС (станка с числовым программным управлением, робота загрузки, автоматического средства контроля). На этом уровне САК решает такие задачи, как получение и обработка информации о контролируемых параметрах и функциях объекта обработки и составных частей ЭАС, передала информации на средний уровень; контроль над исполнением переходов; контроль функционирования составных частей ЭАС; представление информации в систему технического обслуживания для прогнозирования постепенных отказов инструмента и оборудования.
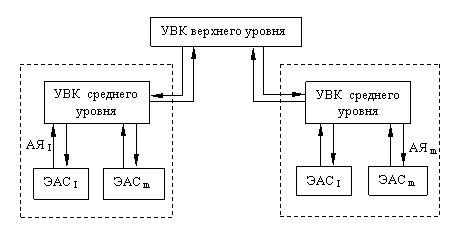
Рис. 9. Типовая структура САК ГАП
На всех уровнях САК должна обеспечивать возможность автоматической перестройки средств контроля в пределах заданной номенклатуры контролируемых объектов, полноту и достоверность контроля, надежность средств контроля, соответствие динамических характеристик САК динамическим свойствам контролируемых объектов.
Сформулированные цели и задачи САК позволяют установить объекты и средства контроля для каждого уровня. Так, объектом контроля верхнего уровня является совокупность АЯ и рабочее место оператора, а средством контроля – управляющий вычислительный комплекс (УВК) на базе мини-ЭВМ. Объектом контроля среднего уровня служит автоматизированная система, состоящая из совокупности ЭАС, а средством контроля – УВК на базе микро-ЭВМ. УВК состоит из ЭВМ, средств сопряжения с удаленными терминалами и локальной сетью ЭВМ, средств повышения надежности функционирования и т.д.
Более подробно рассмотрим объект и средство контроля нижнего уровня, так как именно на этом уровне различные средства автоматического контроля, в том числе и подналадчики, находят наибольшее применение. Объектом контроля нижнего уровня являются составные части ЭАС (рис. 10): управляющий орган (УО), передаточное звено (ПЗ), исполнительный орган (ИО), объект обработки (ОО). Средства контроля (СК) на нижнем уровне за состоянием составных частей ЭАС и технологической среды (ТС) определяются спецификой компонентов ЭАС. Средства управления ЭАС строятся на базе микро-ЭВМ или микропроцессоров и содержат дополнительно к ранее перечисленному составу УВК средства сопряжения с датчиками и исполнительными механизмами. Объекты и средства контроля ЭАС образуют соответствующие подсистемы автоматического контроля. Основная задача построения САК заключается в распределении функций контроля между уровнями и в оптимизации состава средств контроля на нижнем уровне. При этом следует стремиться к тому, чтобы на нижнем уровне САК обеспечивалась максимально возможная автономность управления по результатам контроля.
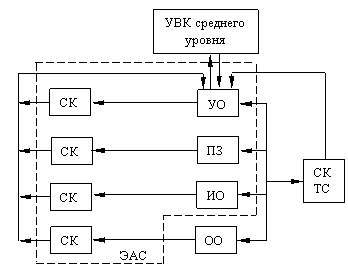
Рис. 10. Структура системы контроля ЭАС
Объем контроля распределяется между средством обработки и объектом обработки в ЭАС, с одной стороны, и между взаимодействующим по объекту обработки ЭАС, с другой (рис. 11). Например, объект обработки можно контролировать путем измерения как его параметров (размеров и формы деталей, их твердости, массы и т.д.), так и параметров средства обработки (износа инструмента, положения исполнительного органа станка и т.д.) Возможны и комбинированные средства контроля, построенные на синтезе приборов активного контроля в процессе обработки и подналадчиков. Функции контроля качества продукции на нижнем уровне осуществляются по той из нижеследующих программ, которая в наибольшей степени соответствует целям и возможностям конкретного производства [18].
1. Программа активного контроля в зоне обработки детали пользует автоматическое управление размером и формой в поперечном и продольном сечениях обрабатываемой детали.
2. Программа статистического контроля обеспечивает управление уровнем настройки обрабатывающего оборудования по результатам контроля партии или выборки из партии на рабочем месте или контрольной ячейке. На основании обработки размерной информации о детали в выборке выдается одна из управляющих программ: норма, брак, подналадка "+", подналадка "-", потеря точности. Объем выборки и периодичность взятия измерительной информации рассчитывается в УВК по каждому станку в зависимости от точностных характеристик процесса обработки.
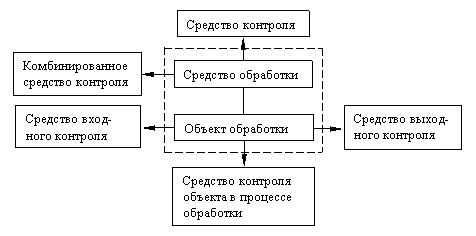
Рис. 11. Распределение объема контроля между средством и объектом обработки
3. Программа приемочного контроля имеет два варианта: полный (100%-ный) и выборочный. В первом варианте программой предусматривается автоматическая проверка основных результатов и автоматическая выдача сертификата о годности продукции, во втором – сбор информации со всех контрольных операций в технологическом процессе изготовления о качестве деталей в партии и определение уровня контроля (размер выборки). При контроле последующей партии объем выработки корректируется по результатам контроля предыдущей выборки и сопоставления информации с контрольных операций при изготовлении партий. В результате устанавливается один из трех режимов контроля: усиленный, нормальный, ослабленный. Объем программного обеспечения (ПО) САК колеблется в широких пределах в зависимости от объема и вида контроля, выбранного для конкретного производства. Для механической обработки ПО, например, может составлять от 10 до 500 Кбайт вместе с нормативно-справочными массивами, в том числе ПО программ пользователя от 5 до 200 Кбайт.
2.2. Метрологическое обеспечение ГАП
Для обеспечения гибкости производства от САК требуется гибкость не только в эксплуатационном плане (быстрая автоматическая перестройка на изготовление новой продукции), но и в метрологическом.
Вследствие того, что компоненты ГАП применяются при разнообразных технологиях производства, внешних воздействующих факторах, сочетаниях технических средств, возникает целесообразность в отказе от интегральной характеристики точности конкретного технического средства (например, основная и дополнительная погрешность средства измерения) и в переходе к дифференциальным составляющим (составляющие дополнительной погрешности по отдельным влияющим величинам). Суммарная погрешность в этом случае рассчитывается на этапе эскизного (технического) проекта после предварительного выбора всех технических средств ГАП. Это приводит к тому, что для решения задач метрологического обслуживания ГАП особое значение приобретает разработка методов расчета суммарных погрешностей измерения и контроля [10].
С метрологических позиций для ГАП характерны следующие особенности:
- распределенность технических средств системы в пространстве, что приводит к различным условиям эксплуатации;
- наличие каналов связи и, как следствие, большая подверженность воздействию разного рода помех;
- многофункциональность и многоканальность, обусловливающие необходимость в измерительных коммутаторах, промежуточных преобразователях, взаимное слияние каналов;
- изменчивость, гибкость структуры, возможность перестройки развития, наращивание системы в процессе эксплуатации;
- связь с органами управления и регулирования, а также с вычислительной техникой;
- преимущественная работа в динамическом режиме;
- длительное, непрерывное функционирование, невозможность полностью отключить систему для осуществления профилактики(проверки) ее в целом, а иногда и отдельных устройств, например, датчиков, без остановки технологического процесса производства. Оптимизация выбора нормируемых метрологических характеристик, способов их нормирования и методов контроля должна проводиться на основе минимизации потерь от завышения (занижения) требований и затрат при эксплуатации. Система обеспечения единства и достоверности контроля в ГАП представлена на рис. 12.
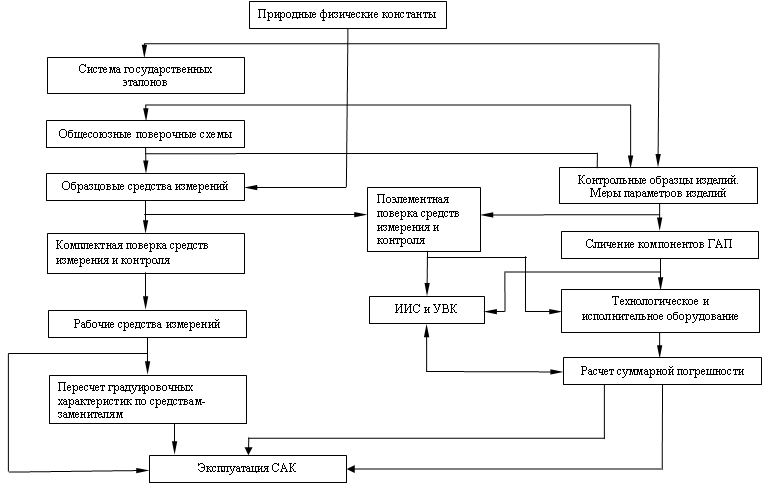
Рис. 12. Система обеспечения единства и достоверности контроля в ГАП
Нормируемые метрологические и точностные характеристики компонентов ГАП должны обеспечивать возможность определения погрешности результата измерения и контроля и точности выдачи управляющих воздействий с требуемой степенью достоверности при комплектной поверке (метрологической аттестации) ГАП в целом, а также достоверной оценки метрологических и точностных характеристик ГАП расчетным путем (по характеристикам технических средств, входящих в ГАП) с учетом конкретных условий эксплуатации ГАП. Кроме этого, нормируемые метрологические характеристики предусматривают экспериментальную проверку и контроль соответствия ГАП требованиям при выпуске их из производства и в процессе эксплуатации, а также выбор отдельных технических средств при компоновке ГАП, исходя из общих требований к контролю и распределению контроля по уровням и компонентам ГАП (рис.13).
Рис. 13. Структура метрологических и точных характеристик компонентов ГАП
Принципиально можно использовать три метода обеспечения единства и достоверности контрольно-измерительной информации в ГАП: 1) комплектную проверку средств измерения и контроля (комплектную аттестацию ГАП в целом и его компонентов); 2) поэлементную проверку средств измерения и контроля (поэлементную аттестацию компонентов ГАП); 3) сличение компонентов ГАП.
Первый метод применим для рабочих средств измерения и контроля (в том числе встраиваемых в оборудование), в первую очередь для измерительных преобразователей (датчиков). В случае поблочной (поэлементной) проверке установка (компонент в целом) расчленяется на автономные блоки, для каждого из которых устанавливаются нормируемые метрологические характеристики и способ их определения. Причем для автономного блока погрешность выявляется либо расчетным путем, либо путем проверки его в соответствии с общесоюзной поверочной схемой. При этом способе основной задачей является выбор достоверной модели представления информации и погрешности. Расчет погрешности должен основываться на реализации математически строгого подхода с проведением сложных экспериментов и расчетных работ, как при создании установки, так и при ее изготовлении и испытании. Информационная часть современных приборов чаще всего создается на базе математического обеспечения с привлечением ЭВМ, что вносит дополнительную алгоритмическую погрешность вследствие неполноты учета особенностей измерительного процесса (нелинейности, динамических особенностей измерительного тракта и т.д.). В силу отмеченных трудностей теоретический подход к определению фактической погрешности блока достаточно сложен и не всегда удобен для практического использования.
При втором способе предусматривается метрологическая аттестация и поверка автономных блоков приборов по иерархической схеме. Для некоторых из них существуют общесоюзные поверочные схемы. В противном случае необходимо создавать локальные поверочные схемы, содержание и состав которых регламентированы ГОСТ 8.061-73. При этом сходное образцовое средство, стоящее во главе поверочной схемы, градуируется косвенными методами, причем допускается как разработка такого средства, так и его заимствование из других поверочных схем. Завышающим этапом аттестации и поверки при использовании поблочного метода является расчет суммарной погрешности измерения, методы определения которой пока еще разработаны недостаточно. Поэтому для сокращения времени на поверку при разработке ГАП предусматривается широкое использование встраиваемых средств поверки, комплектных передвижных образцовых средств (в том числе автоматических, устанавливаемых на транспортном роботе), обеспечивающих поверку на рабочих местах.
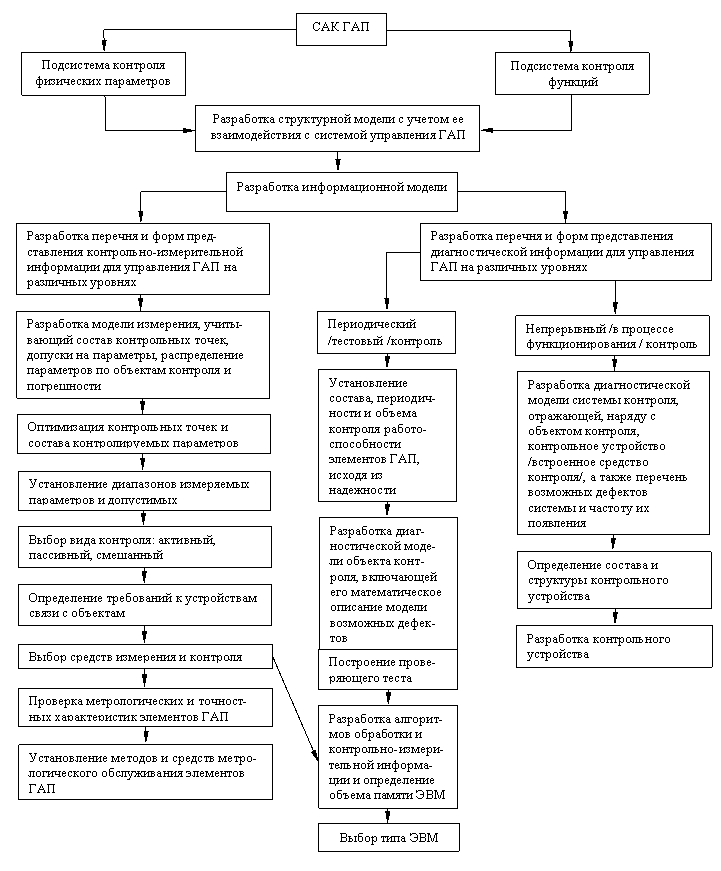
Рис. 14. Последовательность и содержание работ по синтезу САК ГАП
Таким образом, в ГАП САК должна обеспечивать двоякую функцию: с одной стороны, гарантировать выпуск продукции с параметрами, лежащими в пределах, установленных государственными стандартами, а с другой - функционирование рабочих средств измерения с заданными метрологическими характеристиками в течение длительного времени. Иначе говоря, речь идет о необходимости проведения работ по синтезу САК ГАП, последовательность и содержание которых представлены на рис. 14. В процессе функционирования достоверность контрольно-измерительной информации обеспечивается системой контроля работоспособности всех элементов ГАП встроенными средствами контроля, а также периодической поверкой средств измерений и периодической метрологической аттестацией вычислительной техники, технологического и испытательного оборудования.
2.3. Техническая база САК ГАП
Технической базой для создания автоматических систем контроля в промышленности является Государственная система промышленных приборов и средств автоматизации (ГСП). В настоящее время ГСП охватывает лишь часть необходимых для измерения величин, но она постоянно совершенствуется как по номенклатуре и техническим характеристикам, так и по углублению уровня унификации и обеспечению всех видов совместимости [11]. В основу построения и развития ГСП положены следующие принципы:
- возможность сведения многообразия функций автоматического контроля, регулирования и управления к ограниченному числу типовых функций;
- минимизация номенклатуры технических средств при условии максимального удовлетворения потребности народного хозяйства на основе агрегатных комплексов технических устройств и параметрических рядов приборов;
- построение технических средств (приборов и устройств) на основе типовых унифицированных блоков и модулей;
- агрегатное построение сложных систем управления на основе унифицированных приборов и устройств;
- совместимость приборов и устройств ГСП при работе (на основе конструктивной, информационной и метрологической совместимости).
Структурная схема ГСП представлена на рис. 15. Более подробно остановимся на средствах локального контроля и регулирования, поскольку именно они с помощью первичных измерительных преобразователей (датчиков) и приборов получают информацию о состоянии технологического процесса и через систему обратной связи воздействуют на него. Наибольшее распространение в системах локального контроля и регулирования получили датчики положения, давления, изображения, скорости, а также контрольно-измерительные машины (КИМ).
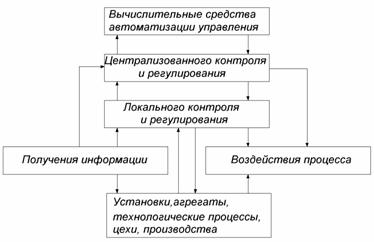
Рис.15. Структурная схема ГСП
Датчики положения осуществляют контроль размеров и формы заготовок изделия, положения рабочих органов оборудования роботов и др. Для контроля размеров и формы заготовки и изделия наибольшее применение нашли датчики касания с измерительными щупами в виде как одиночного щупа, обеспечивающего контроль по одной координате, так и трехкоординатных измерительных головок или головок со сменными щупами для контроля сложнопрофильных изделий. Из зарубежных фирм, разрабатывающих и выпускающих измерительные щупы и головки, наиболее известны итальянские - ДЕА, "Марпос", "Оливетти", японская – «Хитачи», германские - "Маузерверке" и "Оптон" и др. Например, фирма "Марпос" выпускает три разновидности щуповых головок: "Фенар", "Динар" и "Дирак", погрешность измерения которых не превышает ±0,5 мкм в течение рабочего дня, точность включения команд ±0,1 мкм, время приведения к нулю - не более 1 минуты. Для измерения перемещений подвижных частей станков с числовым программным управлением (ЧПУ) широко применяются линейные и угловые индуктосины фирмы "Оливетти", представляющие синусно-косинусный бесконтактный преобразователь. По лицензии этой фирмы Ленинградский электромеханический завод выпускает два типа измерителей для линейных (ПИЛП1-А2) и круговых (ПИКП 1-АЗ) перемещений. Распространение получают датчики с кодовыми дисками и фотоэлектрической системой преобразования информации. Входным воздействием является угол, выходным - код Грея, преобразуемый в дальнейшем в двоичный код для обеспечения совместимости с ЭВМ. В последнее время ведутся работы по использованию фотоэлектронных датчиков на приборах с зарядовой связью [11]. Оригинальный метод получения трехмерных цифровых изображений разработан на основе тактильного датчика. Эти датчики и алгоритмы обработки тактильной информации на ЭВМ применяются в измерительных роботах с сенсорной обратной связью. В качестве датчика используются щупы, используемые в измерительной головке МВ-1 английской фирмы "Рейнишо". Обработку тактильных данных можно разделить на две операции: получение контуров компоновки объекта и связывание этих контуров в последовательное структурное описание.
В качестве датчиков давлений (усилий, деформации) применяются встречно-штыревые преобразователи, напыляемые на поверхность пьезокристалла или пъезопленки. Они основаны на использовании зависимости частоты и скорости распространения поверхностных акустических волн от деформации упругого элемента.
Датчики изображения (распознавания) выдают информацию в виде оцифрованного изображения объекта контроля. В качестве датчика служит телекамера КТП-39, обеспечивающая 64 уровня квантования яркости и максимальный размер изображения 512x512 элементов [20] и серийно выпускаемая отечественной промышленностью. Фирма "Хитачи" использует видикон, представляющий собою передающую телевизионную трубку с фотоприводящей мишенью. Под действием света от объекта контроля на мишени образуется распределение зарядов (потенциальный рельеф), соответствующее изображению объекта. Считывание рельефа осуществляется электронным пучком.
Из последних разработок датчиков скорости следует отметить высокоскоростную и высокоточную японскую следящую головку «Аккдраттрейс», предназначенную для много операционных копировально-фрезерных станков.
Контроль качества продукции в ГАП осуществляется контрольно-измерительной ячейкой (ИЯ), основным элементом которой является контрольно-измерительная машина (КИМ)- На разработке и изготовлении КИМ специализируется германская фирма "Маузерверке"; поставляющая на международный рынок модели KMZ-S и KMZ-B, и итальянская фирма ДЕА, выпускающая машины "Омикрон", "Йота", "Сигма", "Эпсилон". Все эти КИМ имеют режима работы: ручной, автоматический и полуавтоматический и включены в общую информационно-измерительную систему (ИИС) ГАП, которая обеспечена соответствующими программами. На уровне локального контроля и регулирования в качестве операционной системы целесообразно использовать операционную систему реального времени (ОС РВ), которая обеспечивает управление разделяемыми ресурсами системы. Применительно к ОС РВ основными являются понятия задачи и раздела.
Задача представляет собой вычислительный процесс, потребности которого обслуживает операционная система. Задача состоит из одной или нескольких программ, скомпонованных в единый загрузочный модуль, называемый образом задачи. Основными атрибутами задачи являются раздел, признак выгружаемости на диск.
Раздел - это непрерывная область памяти, в которой размещается задача для выполнения. Атрибутами раздела являются имя, длина, база (фиксированный начальный адрес) и тип раздела.
Приоритет представляет собой число, отражающее конкурентоспособность задачи в борьбе за ресурсы системы.
Признак выгружаемости характеризуется возможностью временной выгрузки задачи на диск в том случае, когда более высокоприоритетной задаче требуется раздел, занятый данной задачей.
Для ОС РВ характерно такое понятие, как "важное событие", т.е. такое изменение состояния системы, которое заставляет управляющую программу заново оценивать возможность активной задачи занять центральный процессор. Важное событие возникает в результате следующих причин: при окончании операции ввода-вывода, завершении задачи, осуществлении директивы изменения приоритета задачи. Для организации ввода-вывода в ОС РВ предусмотрены драйверы внешних устройств. Драйвер выполняет следующие функции: принимает и обрабатывает прерывания устройства ввода-вывода, инициирует операции ввода-вывода, запрошенные управляющей программой, отменяет действующие операции ввода-вывода. ОС РВ включает набор драйверов стандартных устройств ввода-вывода. Однако имеется возможность разработки и включения в систему драйверов нестандартных устройств.
2.4. Нормативная база САК ГАП
Основные задачи метрологического обеспечения разработки, производства, испытаний и эксплуатации продукции регламентируется ГОСТ 1.25-76. Конкретизация этих направлений дана в стандартах Государственной системы обеспечения единства измерений (ГСИ), насчитывающей в настоящее время около 500 стандартов, которые классифицируются на основополагающие, регламентирующие нормируемые метрологические характеристики средств измерения, требования к различным категориям средств измерений, правила создания и утверждения средств измерений, стандарты государственных эталонов и государственных поверочных схем, стандарты методов и средств поверки, стандарты методов измерений. Группу основополагающих стандартов можно разбить на следующие подгруппы:
- терминологические стандарты;
- стандарты, устанавливающие основы метрологического обеспечения;
- стандарты общих требований к средствам измерений;
- стандарты общих требований к системам воспроизведения и передачи размеров единиц;
- стандарты общих требований к методам измерений и методам обработки результатов измерений.
К основополагающим стандартам для металлообработки следует отнести ГОСТ 8.050-73 (СТ СЭВ 1155-78) ТСИ. Нормальные условия выполнения линейных и угловых измерений" и ГОСТ 8.051-73 "ГСИ. Погрешности, допускаемые при измерении линейных размеров от 1 до 500 мм". Важным элементом унификации является обеспечение различного вида совместимости, которая в области аппаратурной реализации САК ГАП выливается в серьезную проблему из-за различных принципов формирования контрольно-измерительной информации (аналоговые, аналого-частотные, аналогово-цифровые) и динамических диапазонов изменения параметров и погрешностей измерения и контроля, а сама информация носит как параметрический функциональный, так и технико-экономический характер.
Виды совместимости и стандартизуемые для их реализации параметры приведены в табл. 1.
Таблица 1
Виды совместимости
Совместимости |
Стандартизуемый параметр,
обеспечивающий совместимость |
Основные
ГОСТы |
Функциональная |
Общие технические условия |
ГОСТ 13033-76
ГОСТ 13034-67
ГОСТ 13056-76 |
Информационная |
Входные и выходные сигналы |
ГОСТ 9895-69
ГОСТ 14853-69
ГОСТ12814-74
ГОСТ 9468-60
ГОСТ 26.016-81 |
Метрологические |
Нормируемые метрологические характеристики |
ГОСТ 8.009-72
ГОСТ 8.251-77
ГОСТ 8.256-77
ГОСТ 23222-78 |
Эксплуатационная |
Окружающие условия |
ГОСТ 17167-71
ГОСТ 17785-72
ГОСТ 17786-72 |
Надежность |
ГОСТ 13216-74
ГОСТ 15098-69
ГОСТ 20699-75 |
Энергетическая |
Параметры питания |
ГОСТ 10938-69 |
Конструктивная |
Присоединительные размеры |
ГОСТ 15579-70
ГОСТ166848-71
ГОСТ 20954-75 |
Унифицированные типовые
конструкции |
ГОСТ 2054-75 |
Эргономическая |
Эргономические показатели |
- |
Лингвистическая |
Отсутствует |
- |
К настоящему времени разработаны два государственных стандарта в области ИИС: на основные положения метрологического обеспечения (ГОСТ 8.437-81) и общие положения по поверке (ГОСТ 8.438-81).
ГОСТ 8.009-72 и 8.256-77 в части регламентации динамических характеристик аналого-цифровых преобразователей (АЦП), формы их представления и методы определения дополнены методическими указаниями РД-50-148-79 "Нормирование и определение динамических характеристик АЦП мгновенного электрического напряжения и тока". В них рекомендуется в качестве нормируемых динамических характеристик АЦП выбирать время преобразования TПР, время задержки ТЗ (время переходных процессов во входных устройствах), время цикла кодирования ТЦ, время установления выходного сигнала ТЗО (время задержки отсчета).
Первые три характеристики определяют максимальную продолжительность преобразования и необходимы для правильного применения АЦП в составе автоматизированных средств измерения, последняя - служит для оценки границ погрешности АЦП в динамическом режиме.
В методике МИ 222-80 "Расчет метрологических характеристик измерительных каналов информационно-измерительных систем но метрологическим характеристикам компонентов" даны формулы расчета ряда метрологических характеристик измерительных каналов для нормальных и рабочих условий эксплуатации ИИС в статическом и динамическом режимах: номинальной статической характеристики преобразования; характеристик систематической и случайной составляющих погрешностей; характеристик погрешности измерительного канала (для нормальных условий и статического режима эксплуатации); наибольших допускаемых отклонений метрологических характеристик измерительных каналов, вызванных изменениями внешних влияющих величин и неинформативных параметров входного сигнала (для рабочих условий и статического режима эксплуатации); динамической характеристики измерительного канала; характеристик случайной составляющей измерительного канала (для нормальных и рабочих условий и динамического режима эксплуатации).
Для нормирования и определения метрологических характеристик измерительных преобразователей, имеющих самостоятельное конструктивное исполнение, разработана методика РД 50-206-80 "Нормирование и определение метрологических характеристик измерительных преобразователей кода в постоянное напряжение и ток". Эта методика устанавливает комплекс нормируемых метрологических характеристик, форму их представления и методы экспериментального определения. Одна из проблем в области метрологического обеспечения ИИС - разработка методов определения погрешностей результатов вычислений с помощью вычислительных средств, входящих ИИС. Для определения структур ИИС, блоки которых описываются линейными стационарными операторами, создана методика аналитического расчета ИИС по метрологическим характеристикам ее блоков. Для ИИС, содержащих нелинейные блоки, погрешность которых в ряде случаев невозможно рассчитать аналитически, могут быть применены методы имитационного моделирования.
2.5. Принципы построения измерительной и транспортирующей цепей
Место средств измерения (СИ) в производственной системе определяется технологическим процессом. Структурная схема одного из известных вариантов производственного процесса со встроенными средствами измерений (модулями CИI-СИП) приведена на рис. 16.
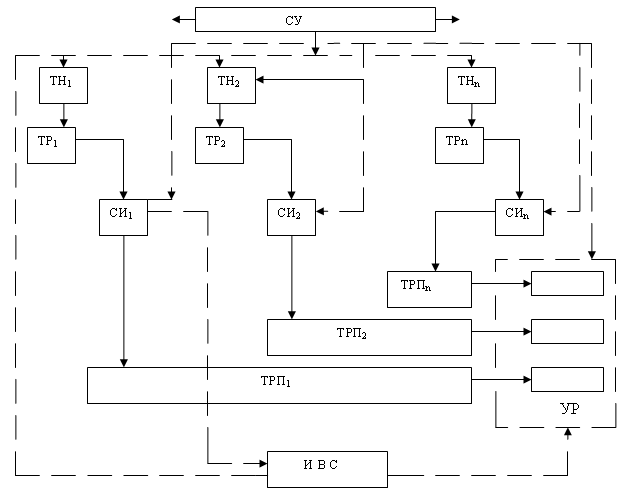
Рис.16. Структурная схема производственной системы
Детали, обрабатываемые на технологическом оборудовании ТН (модули THI-ТНП), транспортирующими устройствами ТР, которые могут содержать ориентирующие устройства и выполнены в виде роботов-манипуляторов, подавателей и транспортеров, подаются на модули СИI-СИП. Полученная с СИ информация направляется либо в информационно-вычислительную систему ИВС, либо в устройства реализации измерительной информации УР, которыми могут быть склад, технологическое оборудование дальнейшей обработки деталей, приемные устройства, ячейки или отсеки нахождения деталей заданных размеров и т.д. Информация, необходимая для корректировки технологического процесса, направляется на технологическое оборудование. На ИВС направляется информация о результатах измерения важнейших размеров.
Измерения детали подаются на транспортеры ТРПI-ТРПП, которые доставляют их к заданному адресату, т.е. к одному из устройств УР. В это же время к исполнительным органам УР из модулей CИI-СИП или ИВС должна поступать соответствующая информация, воздействующая на элементы, которые распределяют детали по заданным адресам.
Алгоритм работы производственной системы и его измерение, последовательность операций, моменты опроса и передача информации с одного блока на другой задаются и осуществляются системами управления СУ/8/.
Производственные системы могут содержать анализаторы, осуществляющие обработку результатов измерений, а также определяющие частоту и объем выборки измеряемых деталей и способ обработки измерительной информации.
В зависимости от построения производственного процесса количество, номенклатура и соподчиненность различных устройств и модулей могут изменяться. Например, детали можно снимать с технологического оборудования и устанавливать на СИ вручную оператором; на одно СИ можно подавать детали от нескольких технологических модулей; к устройству реализации измерительной информации от средств измерений детали могут подаваться индивидуальными манипуляторами; информационно-вычислительная система может отсутствовать, а вычислительные операции выполняться СИ; производственная система может быть снабжена гибким контрольным модулем, на который подаются детали от технологического оборудования.
Обобщенная структурная схема автоматического СИ приведена на рис.17.Схема составлена из функциональных блоков, выполняющих определенную задачу.
Из загрузочного устройства 1 детали поступают в накопитель 2, а затем транспортирующим устройством 3 подаются на измерительную станцию 4, где формируется измерительная информация.
Измерительным преобразователем 6, вмонтированным в станцию, информация преобразуется в электрические сигналы, которые через усилительно-преобразующие устройства 7 и аналого-цифровой преобразователь 9 поступают в пороговое устройство 10, последнее формирует сигналы о принадлежности детали к определенной группе или о выполнении логической операции (например, "брак", "годный ","номер сортировочной группы", "переключить подачу", на дальнейшую обработку"). От порогового устройства через запоминающее устройство 11 информация поступает на устройство 12 реализаций измерительной информации, т.е. цифровое табло, дисплей, светофорное табло, печатающую машину или дополнительный орган приемного устройства 13, куда транспортирующее ,устройство 5 должно к этому времени доставить измеренную деталь. Электроснабжение всех электрических элементов осуществляется блоком 8.
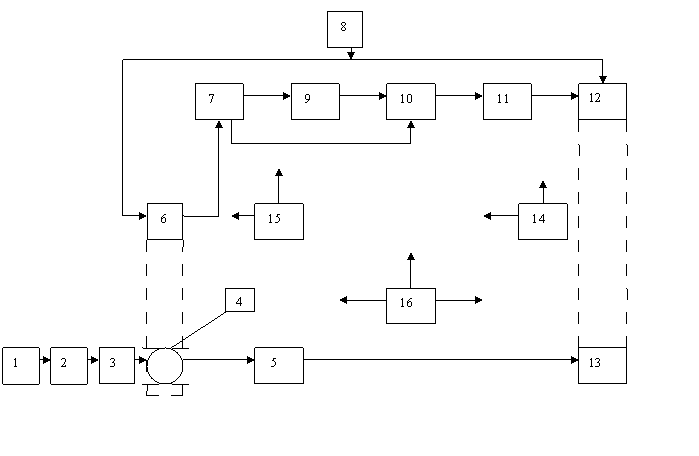
Рис.17. Обобщенная структурная схема автоматического средства
Алгоритм работы и установку диапазонов измерений задает программное устройство 15; последовательностью временных операций управляет командное устройство 16. На любом участке передачи информации или перемещения детали могу быть вмонтированы корректирующие устройства 14, осуществляющие обратную связь, компенсирующие погрешности или приводящие к норме работу СИ.
В зависимости от конструкции и назначения СИ часть функциональных блоков может либо отсутствовать, либо находиться в другой соподчиненности. Каждый блок можно представить в виде структурной схемы, состоящей из элементарных ячеек, которые выполняют определенную функциональную задачу. Структурные схемы функциональных блоков (узлов) рассмотрены в соответствующих главах книги.
Из структурных схем, представленных на рис. 16 и 17, следует, что как в производственных системах со встроенными СИ, так и в СИ, можно выделить транспортирующую цепь, измерительную и цепи управления, которые определяют два основных аспекта конструирования и эксплуатации СИ - производительность и точность.
До измерительной станции располагается только транспортирующая цепь, после измерительной станции параллельно существуют две цепи: измерительная и транспортирующая; цепи управления могут быть расположены на любом участке транспортирующей или измерительной цепи.
Основной операцией производственной системы является обработка детали на технологическом оборудовании. Основная операция СИ - контроль и измерение детали. Наиболее эффективными (с точки зрения производительности) следует признать системы или средства, в которых непрерывно и с наименьшим временем осуществляется основная операция, а все остальные операции, называемые вспомогательными, совмещены с основной операцией и не превышают времени осуществления основной операции.
Анализ соотношения между временем основной операции и периодами цикла работы отдельных блоков и устройств дает возможность повышать производительность СИ и выбирать оптимальную конструкцию [25,26].
Вспомогательные операции могут осуществляться последовательно с основной, а также параллельно и независимо от нее. В связи с этим можно выделить период Т1 цикла, в котором последовательно присутствует основная операция Т2, где основная операция отсутствует. Тогда:
Т1 = t0 + Σ tХП , T2 = Σ tX , (2)
где Σ tХП - сумма времен, не совмещенных с основной из вспомогательных операций;
Σ tX - сумма времен совмещенных с основной из вспомогательных операций.
Отношение суммы времени вспомогательных операций ко времени основной операции назовем коэффициентами производительности; они определяются по формулам:
KП= Σ tХП / t0 (3)
Решая совместно уравнения (2) и (3), получим:
T1 = (KП+1)t0,, T2 = KС t0. (4)
Период цикла Т блока, устройства, средства или отдельных участков цепей будет определяться наибольшим из периодов:
(5)
Чем меньше коэффициенты КП, КС и t0, тем эффективнее с точки зрения производительности отдельные устройства и средства .Коэффициент KП всегда больше 0, расчетное значение коэффициента KС может быть меньше 1, однако в реальной конструкции : КС≥1. При KП → 0 Т1→ t0, при КC→ 1 T2→t0.
Производительность будет полностью определяться основной операцией при КП=0, КС ≤, 1. Анализ уравнений (2) - (5) показывает, то повышение производительности может быть достигнуто за счет уменьшения коэффициентов КП и КС , т.е. за счет интенсификации отдельных операций и путем их совмещения. Интенсификация операций, как правило, приводит к уменьшению надежности работы. Поэтому при проектировании СИ для повышения производительности измерения и контроля целесообразно стремиться к совмещению операций: например, контроль последующей детали осуществлять во время обработки предыдущей детали, применяя два последовательно работающих робота-манипулятора; встраивать измерительную станцию в транспортирующее устройство; производить измерение деталей без остановки ее на позиции измерения; применять запоминающие устройства, которые позволяют запоминать измерительную информацию, освобождая станцию для измерения последующих деталей до ее доставки к адресату, и перемещать одновременно сигналы о результатах измерения ряда последовательно измеренных деталей; измерять одновременно несколько размеров.
Для анализа производительности СИ часть структурной схемы от измерительной станции до устройства реализации измерительной информации рационально представить как систему синхронного перемещения измеренной детали и носителей измерительной информации о ней, что предусматривает согласованность движения детали и передачи носителей измерительной информации. Неоправданно доставить деталь к приемной ячейке и не подать к этому времени на исполнительный орган измерительную информацию. Рассогласованность этих операций приводит к снижению производительности СИ.
Рассогласование движения детали и передачи измерительной информации о ней определяется отклонением скорости перемещения детали от расчетной, а также задержкой в передаче измерительной информации, обусловленной временем переходных процессов в отдельных блоках измерительной цепи. На конечном участке передачи измерительной информации время рассогласования tPC многих случаях достигает значительных величин, соизмеряемых с периодом цикла, который в этом случае определяется по формуле
T = TP+tPC,
где ТP -расчетное время периода цикла.
Если время преобразования измерительной информации и временные транспортные операции соответствуют расчетным значениям, то величина tPC может быть рассчитана и учтена при проектировании сдвигом lС измерительной станции, приемных позиций, записывающих и считывающих устройств измерительной цепи на расчетную величину, а также может быть скомпенсирована введением в конструкцию регулировочных элементов.
Величина сдвига lC определяется по формуле
,
где V - скорость перемещения измеренной детали.
Если длительность транспортных операций и преобразования измерительной информации зависит от ряда трудно учитываемых факторов, то время рассогласования определяется по формуле
TPC=KЗ tРВ ,
где К3 - коэффициент запаса; tРВ - расчетное время рассогласования.
Значение коэффициента запаса в некоторых случаях может колебаться в широких, пределах. Для транспортных операций оно зависит от условий перемещения и ориентации деталей, от типа, массы, формы и размеров детали, от степени ее очистки, от колебания скорости транспортирующих органов; для операций, связанных с перемещением измерительной информации, - от вариации переходных процессов. Непостоянство времени транспортных операций и вариация переходных процессов приводят к колебанию δtРС. Величина δtРС в общем случае может быть определена по формуле
δtРС =
где δitРС - колебание времени рассогласования на отдельных этапах движения детали и носителей измерительной информации.
Величину δtРС невозможно скомпенсировать. Поэтому сигнал измерительной информации на исполнительный орган приемного устройства должен быть подан раньше прихода детали на время, равное δtРС. что приводит к увеличению периода цикла, который в этом случае определяется формулой
T=TP+tPC+ δtРС
Для уменьшения времен tPC и δtРС, а следовательно и повышения производительности необходимо обеспечить ряд условий.
1. Число блоков в транспортирующей и измерительной цепях должно быть минимальным; для этого рационально совмещать транспортирующие, измерительные и исполнительные устройства. Процесс перекладывания деталей с одного устройства на другое по пути их следования нужно сокращать, так как при этом снижается Производительность измерения; число функциональных узлов сводить к минимуму, используя носителем информации измеренную деталь. Однако идея намагничивания ферромагнитных деталей с различной степенью намагниченности, пока не нашла практического применения. Большое преимущество имеют механические средства с клиновыми калибрами, особенно с гипоциклоидной подачей деталей. Однако механические системы не обладают универсальностью, достаточной точностью и надежностью, вследствие чего они имеют ограниченное применение [26].
2. Подлежащие изменению детали должны быть очищены, просушены и размагничены. Западание и выпадение цилиндрических деталей должно происходить при их ориентации по диаметру [24].
3. В транспортирующей цепи должны применяться устройства, временные операции которых могут быть точно определены аналитически. Этому условию в наибольшей степени отвечают устройства с принудительным перемещением деталей, в меньшей степени с перемещением деталей под действием собственной массы.
4. Измерительная цепь должна состоять из быстродействующих блоков, переходные процессы в которых обладают незначительной вариацией.
5. Между транспортирующими органами различных устройств должны существовать простые, замкнутые и точные кинематические связи.
На любом участке, в любом блоке измерительной цепи может возникнуть погрешность, которая вносит свой вклад в погрешность результата измерения. Наиболее характерными с точки зрения специфики образования и проявления погрешностей являются зоны: формирования измерительной информации, передачи измерительной информации механическими элементами, преобразования перемещений в электрический сигнал, преобразования аналогового сигнала в цифровой, формирования сигналов в пороговых устройствах, передачи дискретных сигналов, реализации измерительной информации.
Формирование информации осуществляется на входе измерительной цепи в измерительной станции СИ. Источником информации является деталь, на которой заданы размеры d, подлежащие измерению. Однако чувствительный элемент из-за погрешности базирования детали, контактных деформаций, неточности выполнения базирующих и чувствительных элементов, ошибочности идеологии измерения, загрязненности поверхности может воспринимать размер d1 , отличный от заданного размера d. Разность между заданным размером d и воспринимаемым чувствительным элементом размером d1 приводит к погрешности ΔВ1 = d – d1 Погрешность ΔВ1 во многом зависит от конфигурации, размеров, поверхностной твердости и шероховатости измеряемой поверхности.
Перед началом работы производится настройка средств измерений. Исходная настройка с помощью настроечных элементов, являющихся неотъемлемой частью конструкции СИ, производится по образцовым деталям, установочной мере или исходному элементу СИ (например, путем совмещения указателя с нулевым штрихом шкалы). Регулировочные элементы входят в цепи управления, и с помощью их оператор производит поиск исходного уровня, который определяет начальную точку градуировачнной характеристики. При этом возникают следующие погрешности: ΔВ2, определяемые погрешностью аттестации образцовых деталей или исходных цементов и, ΔВ3 определяемые погрешностью регулировочных элементов. Погрешности настройки особенно велики в зоне формирования измерительной информации, но они могут возникнуть на любом участке измерительной цепи.
Помимо размера, подлежащего измерению, который является информативным параметром, чувствительным элементом могут восприниматься неинформативные параметры: вибрации, колебания температуры и т.д., вносящие погрешности ΔВ4, обусловленные в основном воздействием влияющих величин ΔВЛ .
Таким образом, при формировании измерительной информации на вход измерительной цепи подается сигнал с погрешностями: ΔВ1, источником которой является измеряемая деталь, базирующие и чувствительные элементы; ΔВ2 и ΔВ3, определяемые погрешностями настройки, и ΔВ4, зависящая в основном от условий измерения. Конструкция СИ должна обеспечивать минимизацию погрешность формирования измерительной информации: например, оптимальную форму базирующих и измерительных поверхностей и их взаимное расположение, выбор оптимального измерительного усилия его колебания, высокую точность регулировочных элементов, правильный выбор материалов и взаимного расположения деталей измерительной станции.
Воспринимаемый чувствительным элементом размер может быть постоянным по времени x(t) = d или быть функцией времени d =φ(t).
Размер изменяется во времени при измерении поверхностей, перемещающихся относительно чувствительного элемента (например измерение зубчатых колес, формы и шероховатости поверхности).
Изменение размера во времени, как правило, имеет форму периодического или негармонического колебания.
При периодическом гармоническом изменении размера входной измерительный сигнал описывается уравнением ,где dm - максимальный размер; - круговая частота, причем Т – период изменения размера. При периодическом негармоническом колебании входной сигнал может быть с любой степенью точности Представлен в виде ряда Фурье в действительной или комплексной форме [13,30].
Для большинства задач измерений входной сигнал можно представить постоянным по времени, так как в конструкцию СИ вводятся устройства, фиксирующие измерительную информацию, либо после успокоения положения детали на измерительной станции, либо после достижения деталью заданного сечения при ее движении относительно чувствительного элемента.
Измерительная цепь оси состоит из блоков, последовательно преобразующих сигнал измерительной информации, принятый чувствительным элементом. Для каждого предыдущего блока, в то время как входной сигнал, воспринимаемый чувствительным элементом первого блока, является функцией измеряемого размера d (рис.18).

Рис 18. Схема передачи сигналов измерительной информации
Помимо этого на вход измерительной цепи и на элементы функциональных блоков воздействуют влияющие величины xВЛ, вызывая как смещение исходной настройки, так и искажение функций преобразования измерительной информации. Во внешних цепях и внутри блоков возникают низкочастотные, высокочастотные и импульсивные помехи хn, воздействующие на входной сигнал как возмущающие величины.
Передачу измерительной информации с одного блока на другой стремятся осуществить при установившемся значении входного сигнала. Поэтому для анализа погрешности, в первую очередь, важны характеристики. Определяющие функциональные связи между выходным сигналом и измеряемым размером или выходным и входными сигналами отдельного блока в статическом режиме.
На основании вышеизложенного статические функции преобразования отдельных блоков можно записать в виде уравнений:



а измерительные статистические функции – в виде уравнений:


причем последняя измерительная функция является градуировочной характеристикой.
Влияющие величины хВЛ, помехи хП ( как и погрешности формирования размера) являются вредными величинами, искажающими результат измерения, вызывая обратимое и необратимое воздействия. Например, изменение температуры может вызывать дрейф настройки, которая может вернуться к исходному уровню, а может воздействовать на припои. Приводя к необратимым воздействиям в других элементах механических цепей и структурных элементах электрических цепей. Поэтому должны быть приняты меры к уменьшению и исключению величин. Искажающих результат измерения. В некоторых случаях для учета погрешности и принятия мер по их устранению рационально определить зависимость выходного сигнала от влияющих величин и помех, т.е. ,
В реальных условиях работы определяют зависимость выходного сигнала от измеряемого размера или входного сигнала без учета отрицательных факторов. Влияющих на эти зависимости. При этом исключительно важное значение имеет анализ измерительных функций и градуировочной характеристики, так как большинство погрешностей приводятся ко входу измерительной цепи (рис.19).
В зоне передачи аналоговых сигналов измерительные статические характеристики непрерывны и являются либо случайной функцией, либо функцией случайных величин ( см. рис 19а). Незначительное изменение измеряемого размера или входного сигнала приводит к изменению выходного сигнала.
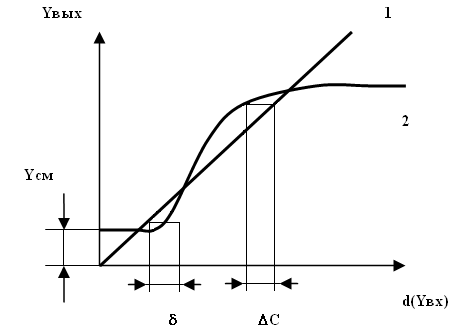
а)
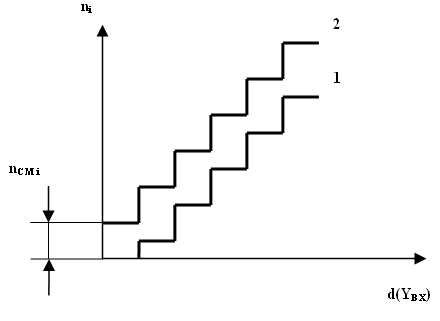
б)
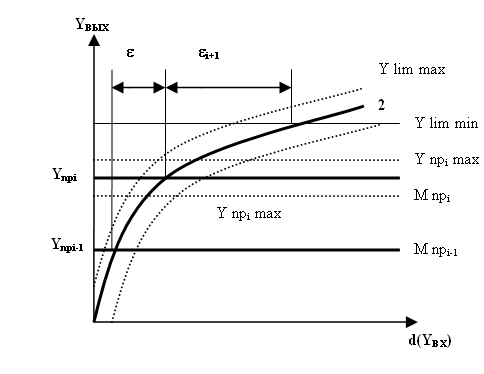
в)
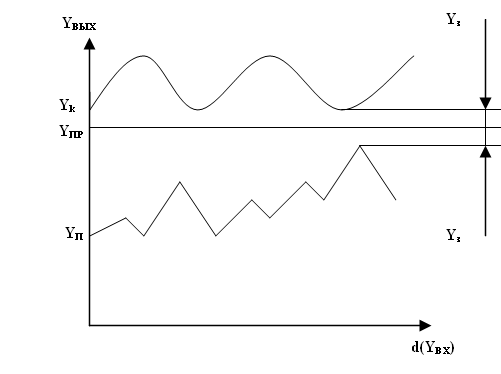
г)
Рис. 19. Градуировочные характеристики: а- непрерывные; б- дискретные; в- преобразование непрерывного сигнала в дискретный; г- создание зон запаса
При многократном определении градуировочной характеристики получают семейство реализаций, в котором каждая реализация является действительной градуировочной характеристикой, полученной при данном опыте.
где Yсм – смещение уровня исходной настройки; n – число реализаций.
Математическим ожиданием градуировочной характеристики является детерминированная функция 2, которая при каждом значении параметра равна математическому ожиданию соответствующего сечения градуировочной характеристики (7). Под сечением понимается значение случайной функции, соответствующее определенному размеру d.
Номинальную градуировочную характеристику стремятся выполнить линейной. Поэтому примем, что номинальная градуировочная характеристика 1 линейна при начальных условиях Y=0 при d=0, а выходной сигнал Y=id , где i- коэффициент преобразования, выражающий отношение выходного сигнала к вызвавшему его входному сигналу значение i равно tga , где a – угол наклона номинальной градуировочной характеристики. В механических приборах параметр i часто называют передаточным отношением.
Отношение DC, равное разнице по оси абсцисс точек функций 2 и 1 (см. рис. 19а), определяет систематическую составляющую погрешности Рассеивание градуировочной характеристики определяет случайную погрешность d. Из рис. 19а следует, что любое искажение измерительного сигнала в зоне передачи непрерывной информации приводит к погрешности, которая может принимать сколь угодно малое значение.
Градуировочная характеристика редко нормируется в СИ, так как ее определение является весьма трудоемкой задачей. У большинства СИ систематические и случайные погрешности нормируются в заданных точках градуировочной характеристики.
В зоне передачи информации механическими элементами, которые, как правило, передают непрерывную информацию, причинами систематических погрешностей могут быть: схемные погрешности механизмов, неуравновешенность деталей механизмов, податливости элементов, погрешность изготовления деталей; причинами случайных погрешностей являются: трение в соединениях, нестабильность работы упругих элементов. Погрешности передачи измерительной информации механическими элементами, а так же пути их компенсации и исключения рассмотрены в работах (15,27).
В зоне передачи электрических аналоговых сигналов причинами систематических погрешностей могут быть; нелинейность элементов, отклонение параметров усилительно-преобразующих элементов от номинальных значений; причинами случайных погрешностей являются: колебания параметров электропитания, воздействие импульсных помех и наводок, рассеивание порогов срабатывания элементов и их нестабильность.
Для компенсации и уменьшения систематических погрешностей в измерительную цепь с механическими [27] и электрическими [25] элементами должны быть введены специальные компенсаторы и регулировочные устройства, приближающие при регулировке действительную градуировочную характеристику к номинальной.
В зонах передачи и преобразования дискретных измерительных сигналов (рис. 19,б) каждая реализация измерительной функции или градуировочной характеристики описывается уравнением
Yi = YCM + φ(d) = inCM + inH = i(n + n ), (6)
где i - дискретность одного элементарного кванта; пCM - число элементарных квантов, соответствующих смещению уровня настройки; nH -число элементарных квантов, соответствующих измеряемому размеру.
Из уравнения (6) и рис. 19,б следует, что выходной сигнал изменяется ступенчато; при изменении размера в пределах одного кванта изменение выходного сигнала не происходит. В некоторых случаях в пределах одного кванта происходит непрерывное изменение информации, однако оно не фиксируется в качестве выходного сигнала (например, в фотоэлектрических позиционных и растровых преобразователях). Так как выходной сигнал состоит из определенной комбинации элементарных квантов, погрешность в зоне передачи дискретных сигналов всегда больше дискретности i. Например, погрешность, связанная с нелинейностью градуировочной характеристики, в общем случае будет выражена уравнением
Δ = ±{Kξ + i),
где К - нелинейность действительной характеристики; ξ – диапазон измерения.
Погрешность квантования N - разрядного двоичного числа в случае преобразования аналогового сигнала в цифровой определяется по формуле [9]
ΔKB = ±0.5 (7)
где V - скорость изменения входного сигнала, выраженная через число единиц младшего по весу разряда; Т - апертурное время, определяемое обычно временем преобразования.
Как следует из уравнения (7), погрешность квантования достигает одной единицы младшего разряда, т.е. дискретности.
При определении градуировочной характеристики СИ по образцовому СИ с дискретностью t0 и фиксацией начального момента очередного показания поверяемого СИ погрешность от нелинейности будет выражаться формулой
Δ = ±{Kξ + i0).
Для анализа погрешностей при передаче дискретных сигналов некоторые авторы предлагают "сглаживание" функции по усредненным высотам интервалов квантования [13]. Тогда измерительная функция описывается непрерывной функцией. Однако при этом всегда необходимо помнить, что в зонах передачи дискретных сигналов погрешности носят также дискретный характер и их величина больше дискретности i.
В некоторых зарубежных приборах нормируется погрешность квантования дискретного сигнала, как правило, равная дискретности i, которую иногда ошибочно принимают за погрешность прибора.
В зоне передачи дискретных сигналов систематическая погрешность может быть вызвана отклонением дискретности от номинального значения. К случайным погрешностям приводят причины аналогичные тем, которые возникают при передаче аналоговых сигналов, а также колебание интервалов элементарных квантов.
Погрешности зоны передачи дискретных сигналов могут быть учтены путем введения избыточных кодов [30] и введением компенсирующей программы с помощью микропроцессорной техники.
В каждом сечении градуировочная характеристика как аналоговых, так и дискретных СИ является случайной величиной, для которой могут быть определены: вероятность значений, плотность распределения, функция распределения, корреляционная функция, начальные и центральные моменты. Уравнения, определяющие эти параметры для случайных аналоговых и дискретных сигналов, и примеры их расчета подробно описаны в работах [7, 30].
Преобразование аналоговых сигналов в дискретные осуществляется аналого-цифровыми преобразователями, рассмотренными в работах [23, 30]. В этой зоне сочетаются погрешности аналоговых и дискретных сигналов.
Значительные погрешности возникают в зоне преобразования перемещений в электрический сигнал. Эти преобразования осуществляются в измерительных преобразователях как в аналоговой, так и дискретной форме; они тесно связаны с принципом действия преобразователей.
Одной из самых ответственных зон, в которой возникают существенные погрешности, является зона формирования команд в пороговом устройстве. Характер образования погрешностей в пороговом устройстве показан на рис.19,в.
Порог срабатывания элемента, воспринимающего измерительную информацию, настраивается на определенную величину выходного сигнала предыдущего блока измерительной цепи. Эта величина может быть выражена как уровнем аналогового сигнала, так и кодом дискретного сигнала. На рис. 19,в в качестве примера показано преобразование непрерывного сигнала в команду от принадлежности детали к определенной группе.
Рассеивание порога срабатывания воспринимающего элемента является случайной величиной. В связи с этим можно найти математическое ожидание MПРi порога срабатывания и предельные величины Ynpi выходного сигнала, при которых может сработать элемент порогового устройства. Рассеивания порога срабатывания приводит к случайной погрешности δП. Рассеивание случайной функции в границах YПР MAX YПР MIN приводит к случайной погрешности δР. Тогда случайную суммарную погрешность формирования команды δФ можно определить по формуле
δФ = кσф, причем ,
где σ - среднее квадратичное отклонение.
При отнесении деталей к одной из групп сортировки или контроля эта погрешность будет выражаться в рассеивании границы, а интервал сортировки ξс или диапазон контроля ξК определяться разницей порогов срабатывания соседних групп. Отклонение интервала сортировки или диапазона контроля от номинального значения ξн является в этом случае систематической погрешностью данного экземпляра СИ
Эта погрешность может быть уменьшена за счет введения специальных peгулировочных устройств [25].
Если величина сигнала помехи Yn больше сигнала YnP, вызывающего срабатывание порогового элемента, то может произойти ложное срабатывание; если сигнал YH, поступающий на пороговое устройство, снимается до величины, меньшей YnP ,то происходит потеря измерительной информации. Это вызывает ложную команду, деталь направляется не по заданному адресу и погрешность может превысить интервал сортировки или диапазон контроля. Для избежания получения ложной информации должны быть выдержаны условия:
YПР MAX < YПР MIN ; (8)
YПР MAX > YПР MIN . (9)
На участках передачи измерительной информации после порогового устройства (рис. 19,г) также должны быть выдержаны условия (8) и (9) и созданы зоны запаса Y3 [26].
Во избежание ложных срабатываний исполнительных органов условия (8) и (9) должны быть также выдержаны в устройствах реализации измерительной информации. Если не соблюдаются условия (8) и (9), то информация должна быть зафиксирована, а измеренная деталь должна быть изъята из транспортирующей цепи. Например, для этого случая прилагается устройство, направляющее деталь на повторную перепроверку или в группу "брак".
Динамические характеристики СИ определяются передаточной функцией, переходной и амплитудно-частотной характеристиками [29,30].
Учитывая, что передача сигналов измерительной информации производится системами управления в большинстве случаев после успокоения подлежащей измерению детали или после достижения входным сигналом установившегося значения, можно полагать, что на вход СИ или отдельного блока подается единичное воздействие [27]. А так как измерительная цепь большинства СИ состоит из линейных элементов, динамические характеристики СИ и блоков могут быть выражены переходной характеристикой, которую наиболее просто получить экспериментально, и которая поэтому чаще всего используется на практике.
Переходная характеристика определяет реакцию выходного сигнала Y(t) на единичную функцию l(t), которая выражается соотношениями
В СИ распространены цепи, состоящие из апериодических и колебательных звеньев. Переходная функция описывается следующими уравнениями:
для апериодических звеньев (рис. 20,а)
для колебательных звеньев (рис. 20,б)
где τ - постоянная времени; k - коэффициент затухания колебательного звена; со - собственная частота колебаний; F0 - установившееся значение выходного сигнала.
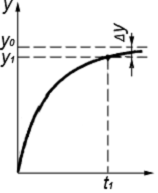
а)
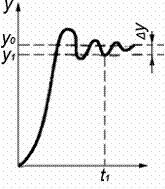
б)
Рис. 20. Переходные характеристики элементов измерительной цепи: а - апериодических звеньев; б - колебательных звеньев
Для двух предыдущих уравнений при .
В момент времени снятия отсчета или фиксации выходного сигнала будет равно . Тогда динамическая погрешность , т.е. погрешности выходного сигнала, приведенного ко входу. По переходной характеристике, задаваясь наибольшим допустимым отклонением , можно найти время установления показаний или выходного сигнала , равное времени, при котором динамическая погрешность пренебрежимо мала. Время установления показаний нормируется для большинства СИ.
В целях минимизации погрешностей измерительной цепи должны соблюдаться следующие условия:
1. Число блоков в измерительной цепи должно быть сведено к минимуму.
2. Аналого-цифровой преобразователь и пороговое устройство должны быть расположены как можно ближе к началу измерительной цепи.
3. Все блоки измерительной цепи должны содержать регулировочные элементы для компенсации систематических погрешностей.
4. В конструкцию всех блоков измерительной цепи должны быть введены элементы, уменьшающие воздействие влияющих и возмущающих величин на выходные сигналы.
|