21.2. Обработка металлов давлением
и монтировочные операции
Прокатка и волочение. Слиток прокатывают для уменьшения его толщины и увеличения длины. Между вращающимися валками (рис.377) слиток обжимается по высоте и вследствие трения между валками и поверхностью слитка продвигается вперед. Эти два основных процесса лежат в основе прокатки, рис.378,а.
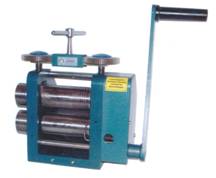 |
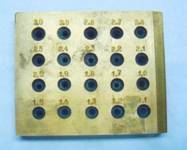 |
а) |
б) |
Рис.377. Вальцы (а) и фильерная доска (б)
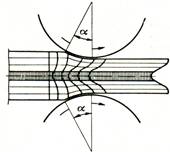 |
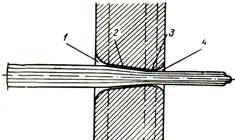 |
а) |
б) |
Рис.378. Схема пластической деформации:
а – прокатка толстого слитка
(α – зона деформации); б – схема волочения и участки волочильного фильера: 1 – входной конус, 2 – протяжной конус, 3 – цилиндрическая часть,
4 – выходной конус
Волочение – это процесс уменьшения диаметра проволоки путем протягивания ее через коническое отверстие инструмента, называемого матрицей и фильером (фильерной доской), рис.378,б.
Ковка. В процессе ковки заготовке, помещенной на наковальню, под ударами молотка (рис.379) придается требуемая форма за счет пластического течения металла. Различают предварительную ковку, когда слиток путем пластической деформации подготавливают для последующей окончательной или чистовой обработки для прокатки, волочения, штамповки, и другие виды пластической деформации, рис.380, 381.
а)
б)
Рис.379. Многоцелевой молоток (а) и шперак-наковальня (б)
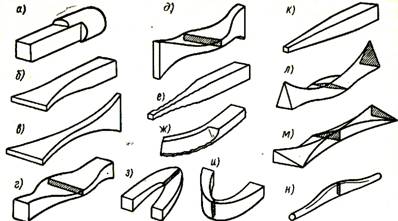
Рис.380. Основные формы заготовок, получаемых методом ковки: а – проковка круглой заготовки на квадрат; б - клиновидное уширение штабика; в – заготовка в форме винта: г – заготовка с расплющенной средней частью; д – клинообразные концы с расширенной серединой; е – заготовка с утонением одного конца; ж – получение заготовки треугольного профиля; з – дугообразная разностенная заготовка; и – то же с разной толщиной вершины дуги; к – заготовка с заостренным концом; л – заготовка треугольного профиля с переменными по длине сечениями; м – кованая заготовка сложной формы; н – круглая заготовка, прокованная на плоскость посередине [6]
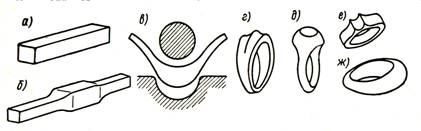
Рис.381. Переходы ковки обручальных колец: а – заготовка-штабик; б – провальцованная развертка заготовки кольца; в – гибка заготовки на свинцовой плите; г – ж – различные окончательные формы колец [6]
При изготовлении кольца ковкой выполняют следующие переходы:
- Четырехгранный штабик подготавливают по толщине и ширине до наибольшего поперечного сечения средней части кольца (см.рис.380,а). Затем концы штабика прокатывают в вальцах до размеров сечения будущих частей шинки (см.рис.380,б).
- Посредством молотка на вставной наковальне (флахштоке) головке и частям будущих частей шинки придают предварительную форму.
- Предварительно откованной заготовке придают форму кольца гибкой. Для этого берут стальную оправку диаметром, несколько большим внешнего диаметра кольца, вбивают ее молотком в свинцовую пластину и получают гибочный желоб. В этот желоб укладывают заготовку кольца так, чтобы средняя часть заготовки находилась посередине желоба (см.рис.381,в). Тонкие концы шинки подгибают окончательно в тисках на оправке.
- Концы заготовки состыковывают и запаивают твердым припоем. Далее шинку рихтуют на ригеле или на роге наковальни и, согласно эскизу, производят окончательную ковку кольца.
Затем шинку делают тоньше с обеих сторон, равномерно суживая ее и по ширине. Среднюю часть кольца выковывают на роге наковальни, придавая ей в сечении форму пологой крыши, постепенно сходящей на нет. Получившиеся наклонные поверхности отделывают пуансоном (чеканом), формуя желобки (см.рис.381,г).
Для изготовления кольца, показанного на рис.381,д, необходимо применить материал с высокой пластичностью, так как исходный штабик должен иметь ширину массивной средней части, а затем вытягиваться по концам с большими обжатиями для получения малого сечения шинки кольца. Формообразование шинки вначале производится так же, как и в предыдущем случае. Далее правильно закругленное кольцо проковывают до получения полукруглого сечения по всему периметру и отделывают среднюю часть. В случае необходимости окончательную форму кольцу придают опиливанием.
Толщина верхней части кольца, показанного на рис.381,е, значительно больше, чем на шинке. После запаивания и рихтовки шинки ее насаживают на рог наковальни, делают тупоугольным зубилом надруб в верхней части и специальной оправкой формуют желобок. Кольцо, изображенное на рис.381,ж, по форме напоминает старинное обручальное кольцо. Оно имеет полукруглое поперечное сечение. Верхняя часть кольца более массивная, чем нижняя. При изготовлении его используются те же приемы, что и при изготовлении вышеописанных колец. Откованную полосу загибают в кольцо, спаивают, рихтуют и на однорогой наковальне и ригеле отковывают полукруглый профиль.
Гибка и правка. Гибку и правку проволоки, тонких листов можно производить вручную, щипцами и с применением вспомогательных средств, рис.382, 383.
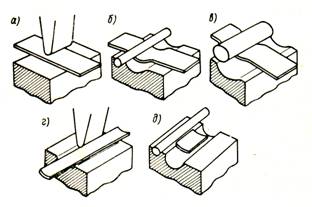
Рис.382. Гибка листа на различных опорных плитах: а – молотком на свинцовой подкладке; б – оправкой на свинцовой подкладке; в – оправкой на деревянном бруске; г – молотком на стальной форме; д – оправкой на стальной плите
Вспомогательными средствами для листогибочных работ являются подкладки и плиты из различных материалов, обычно снабжаемые гибочным желобом и играющие роль матрицы гибочного штампа, а также оправки с различными поперечными сечениями, играющие роль пуансона штампа. Гибка полос и листов производится между оправкой, накладываемой сверху на заготовку, и стенками желоба подкладной плиты.
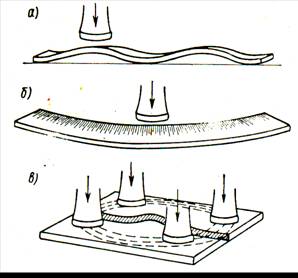
Рис.383. Правка листов: а -правка листа на рихтовочной плите;
б – правка односторонней проковкой;
в – правка листа разгонкой металла
Резка и распиливание. Резку металла осуществляют с помощью различных ножниц: ручных, рычажных и гильотинных. Распиливание металла осуществляют пилой, как правило, лобзиком. Принцип действия пилы показан на рис.384.
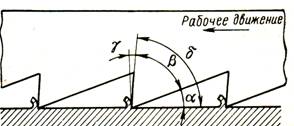
Рис.384. Действие зубьев пилы
Расположенные друг за другом клиновидные зубья пилы режущего полотна вырывают при каждом ходе пилы небольшие частички металла и прочно удерживают их во впадинах до тех пор, пока они не выйдут из металла. Форма и размер зубьев пилы определяются видом и свойствами разрезаемого материала. Для твердых материалов необходимо иметь большой угол заострения клина, чтобы зубья не разрушались. В таких случаях угол β увеличивают до такой степени, что передний угол γ составляет 0°. Опыт показывает, что хороших результатов достигают при соотношении следующих углов на зубьях пилы: задний угол α = 40-20°; передний угол γ = 5-0°; угол заострения β = 65-50°; угол резани δ = 90-85°.
Опиливание. Снятие стружки, подгонка размеров изделия в соответствии с чертежом (рисунком, эскизом), выравнивание поверхности изделия и целый ряд других операций осуществляется с помощью напильников, рифилей и надфилей. Принцип действия напильника аналогичен действию пилы, но отличается формой и заточкой зубьев, рис.385.
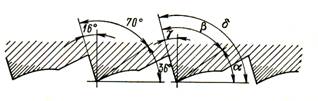
Рис.385. Форма зубьев напильника
Форма каждого зуба напильника образована насеченным углублением и острым выдавленным ребром, поэтому зуб напильника по его действию соответствует режущему клину с отрицательным передним углом, который скорее скоблит, чем режет частицы металла. Для уменьшения износа зубьев необходимо, чтобы угол заострения составлял около 70°. В итоге получаются примерно следующие значения углов: задний угол α= 36°, угол заострения β = 70°, передний угол γ = - 16°, угол резания δ = 106°.
Сверление и фрезерование. Сверлением получают в заготовке углубление или отверстие цилиндрической формы. При необходимости форма углубления или отверстия может изменяться последующим фрезерованием, опиливанием, распиливанием и т.п. операциями. На рис.386 показаны основные виды сверл, применяемых в ювелирном производстве.
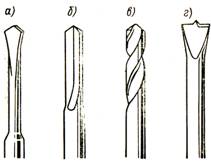
Рис.386. Виды сверл: а – перовое сверло; б – сверло «Эйрека»;
в – спиральное сверло; г – центровое сверло
В современных условиях наряду с ручной дрелью в основном используются бормашинки.
Фрезерованием обрабатывают плоские и выпуклые поверхности в зависимости от формы фрезы, т.е. такие поверхности, которые невозможно или затруднительно опиливать напильником. На рис.387 приведены основные виды фрез.
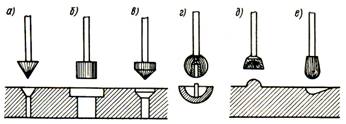
Рис.387. Виды фрез: а – коническая; б – цилиндрическая торцевая;
в – комбинированная остроконечно- цилиндрическая; г – шаровая;
д – полостная сферическая; е – фасонная
Пайка металлов. Пайкой называется процесс неразъемного соединения металлических деталей, находящихся в твердом состоянии, посредством расплавленного связующего металла или сплава – припоя, имеющего более низкую температуру плавления. Между расплавленным припоем и основным твердым металлом происходят на небольшой глубине процессы взаимного проникновения и диффузии, в результате которых при затвердевании припоя получается прочное соединение деталей. Химикаты, применяемые при пайке металлов, которые удаляют из расплавленного припоя оксиды и защищают шов от окисления, называются флюсами. На рис.388 показана структура паяного шва.
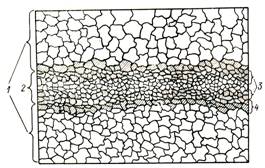
Рис.388. Структура паяного шва: 1 – основной металл;
2 – припой; 3 – зона диффузии припоя;
4 – зона диффузии основного металла
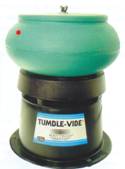 |
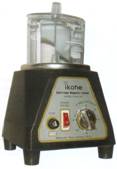 |
а) |
б) |
Рис.389. Виброгалтовка (а) и магнитоголтовка (б)
Очистка и полировка. Очистка ювелирных изделий в большинстве случаев производится в слабых растворах минеральных и органических кислот (отбелах). Полировка может осуществляться с помощью различных паст, содержащих абразивный порошок, методом электрополировки и в галтовочных установках, рис.389.