3. ПРОЕКТИРОВАНИЕ ПЕРЕДАЧ ПЛАНЕТАРНЫХ РЕДУКТОРОВ
3.1. Исходные данные для проектирования
Для проектирования планетарного редуктора нужно знать:
– требуемый момент на выходе редуктора Твых;
– требуемую частоту вращения ведомого вала редуктора nвых;
– требуемое передаточное число редуктора uр;
– условия и режим работы привода;
– требуемый ресурс привода;
– вид производства, для которого предназначен данный проект.
3.2. Выбор числа сателлитов
Планетарная передача – многопоточная передача. Обычно сателлиты размещаются в ней симметрично относительно главной оси и на равных расстояниях друг от друга. Постановка нескольких параллельно работающих сателлитов значительно уменьшает диаметральные размеры проектируемой передачи. Чаще всего число сателлитов k принимается в пределах от 3 до 8. При этом необходимо принимать конструктивные меры для выравнивания нагрузки между ними.
3.3. Синтез планетарных передач
Задача синтеза заключается в определении числа зубьев z зубчатых колёс принятой кинематической схемы, обеспечивая требуемое передаточное число редуктора. Кроме этого, поскольку планетарные передачи соосные и многопоточные, необходимо выполнить условия:
– соосности;
– сборки;
– соседства.
Создавая планетарную передачу, необходимо помнить, что варианты с большими значениями z предпочтительны, так как с их ростом повышается плавность работы, уменьшается шум и виброактивность, снижается скольжение и уменьшаются потери на трение. Кроме того, с увеличением z при данном диаметре снижается масса зубчатого колеса и объём металла, снимаемого при фрезеровании зубьев.
Но с ростом z падает несущая способность зубьев по изгибающим нагрузкам. Это важнейший ограничитель при назначении z. Поэтому при проектировании передач проверки на выносливость при изгибе и изгибную прочность обязательны.
Исходными данными для решения задачи синтеза служат:
– принятая кинематическая схема редуктора;
– требуемое передаточное число редуктора ;
– принятое число сателлитов k.
3.3.1. Передача типа 2k–h (рис. 2.1)
3.3.1.1. Принимаем , если передача нарезана без смещения инструмента, и , если передача нарезана со смещением инструмента. Нужно чтобы было кратным числу сателлитов.
3.3.1.2. Передаточное число такой схемы:
.
Отсюда находим .
3.3.1.3. По условию соосности .
При одинаковых модулях зубчатых колёс .
Отсюда находим: .
3.3.1.4. Проверяем:
– по условию сборки , где Ca – целое число;
– по условию соседства ,где = .
По передаточному числу и условию соосности не проверяем, так как они были использованы при определении чисел зубьев.
Пример 1.
Выполнить синтез редуктора, по кинематической схеме (рис. 2.1), если его передаточное число а принятое число сателлитов k = 3.
П1.1. Принимаем = 21 (кратное числу сателлитов).
П1.2. Находим ( ) = 21×(6 – 1) = 105.
П1.3. Находим .
П1.4. Проверяем:
– по условию сборки: – целое число.
– по условию соседства:

21+2 (42+21)
23 < 54,55.
3.3.2. Передача типа 2k–h (рис. 2.2).
Модули зубчатых колёс одинаковые.
Условие соосности зубчатых колёс .
При одинаковых модулях оно имеет вид: 
Условие сборки определяется тем, что число зубьев каждого центрального колеса должно быть кратно числу сателлитов ; = .
Здесь Са и Сb– целые числа, кратные числу сателлитов.
Условия соседства в этом случае:
и .
Синтез такой передачи может быть выполнен в результате следующих действий.
3.3.2.1. Принимаем > 17–30, если передача нарезана без смещения инструмента, и > 13,
если передача нарезана со смещением инструмента.
Нужно, чтобы было кратным числу сателлитов.
3.3.2.2. Определяем абсолютную величину передаточного числа обращенной передачи
(то есть передачи с «остановленным» водилом)
= .
3.3.2.3. Полученную величину разбиваем на две близкие части
(две – так как редуктор двухступенчатый) так, чтобы
; .
3.3.2.4.Определяем .
3.3.2.5. Определяем требуемое , так как
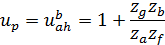
.
3.3.2.6. Определяем 
Учитывая, что и условие соосности ,
получаем .
3.3.2.7. Определяем .
3.3.2.8. Проверяем:
– по условию соосности ;
– по условиям сборки
; или = ;
– по условиям соседства
;
;
– фактическое передаточное число редуктора =1+ .
Если зубчатые колёса нарезаются без смещения инструмента, то необходимо подобрать такое сочетание чисел зубьев колёс, чтобы оно обеспечило получение требуемого передаточного числа редуктора и соблюдение всех необходимых условий.
Пример 2.
Выполнить синтез редуктора, по кинематической схеме (рис. 2.2),
если его передаточное число а принятое число сателлитов k=3.
П2.1. Принимаем =18 (кратное числу сателлитов).
П2.2. 
П2.3. Принимаем .
П2.4. .
П2.5. .
П2.6. .
П2.7. .
П2.8. Проверяем:
– по условию соосности 18+54 = 96 -24→72=72;
– по условию сборки – целое число;
= 32 – целое числo
– по условиям соседства
;
54 + 2 (54+18) → 56 < 62,35;
;
24+2 (96-24) → 26 < 62,35;
– фактическое передаточное число редуктора
=1+ .
Примечание: если принять = 21, то полученные при этом числа зубьев не обеспечат выполнение условия сборки, а если обеспечить при = 21 условие сборки, то без смещения инструмента при нарезке зубьев не будет выполнено условие соосности. Поэтому, если поставлена задача обеспечить все необходимые условия без смещения инструмента при нарезке зубьев, то нужно подбирать соответствующие числа зубьев зубчатых колёс. Иногда без изменения передаточного числа редуктора это не удаётся сделать.
Модули зубчатых колёс разные.
В этом случае задачу можно решать разными способами. Простейшим представляется изложенный ниже.
Условие соосности при разных модулях имеет вид 
при 
Для первого ряда стандартных модулей соотношение

= 1,250; 1,200; 1,333; 1,250; 1,200; 1,333 и т.д.
Этим соотношением задаёмся. Всё остальное аналогично разобранному выше.
Нужно только помнить, что это ориентировочный расчёт: оба модуля должны быть стандартными, и соотношение между ними – с. Окончательно этот вопрос решается при расчёте передачи на прочность.
3.3.3. Передача (рис. 2.3)
При одинаковом модуле у всех зубчатых передач условие соосности
.
По условиям сборки
; = ; ,
где числа , , – целые числа.
По условиям соседства
;
.
Передаточное число такой схемы
.
Числа зубьев зубчатых колёс такой планетарной передачи удобнее определять по табл. 5.3 [14], табл. 6.7 [11]. Но и в этом случае следует проверить выполнение всех условий и определить фактическое передаточное число редуктора.
3.4. Частоты вращения подвижных элементов планетарного редуктора
3.4.1. Вычисление количества оборотов звеньев планетарного редуктора
Исходные данные:
– кинематическая схема привода;
– кинематическая схема редуктора;
– передаточное число редуктора ;
– числа зубьев зубчатых колёс редуктора.
По этим данным частоты вращения определяются в следующем порядке.
3.4.1.1. Частота вращения закреплённого элемента равна нулю.
3.4.1.2. Частота вращения входного (ведущего) элемента редуктора nвх равна частоте вращения двигателя или ведомого звена предыдущей передачи в зависимости от принятой схемы привода (рис. 2.4).
3.4.1.3.Частота вращения выходного (ведомого) элемента редуктора

3.4.1.4. Частота вращения водила (если оно не ведомое звено) должна быть определена в первую очередь. С этой целью составляют формулу Виллиса таким образом, чтобы передаточное отношение в относительном движении бралось от звена, угловая скорость которого задана к неподвижному звену.
3.4.1.5. Частота вращения того звена, для которого можно записать передаточное число в относительном движении между этим звеном и неподвижным звеном
Примечания:
– если использовать неподвижное центральное колесо, то в формуле Виллиса окажется неизвестной угловая скорость только одного звена;
– следует обязательно учитывать знак передаточного числа в относительном движении, выраженном через числа зубьев.
3.4.1.6. Полученные результаты могут быть проверены с помощью планов линейных и окружных скоростей механизма. Нужно помнить, что план скоростей, как всякое графическое решение, даёт весьма приблизительные результаты (50 об/мин). В настоящем пособии построение плана скоростей не приводится.
3.4.2. Передача типа 2k–h (рис. 2.1)
Исходные данные:
– кинематическая схема привода;
– передаточное число редуктора ;
– кинематическая схема редуктора;
– числа зубьев зубчатых колёс ; ; .
3.4.2.1. Из кинематической схемы редуктора следует
угловая скорость колеса b .
3.4.2.2. Частота вращения входного (ведущего) вала редуктора равна
частоте вращения двигателя или ведомого звена предыдущей передачи
в зависимости от принятой схемы привода (рис. 2.4).
3.4.2.3. Частота вращения выходного (ведомого) вала редуктора (для этой схемы – частота вращения водила) .
3.4.2.4. Частота вращения сателлита вместе с водилом (абсолютная скорость сателлита) , где .
3.4.2.5. Частота вращения сателлита относительно водила (относительная скорость сателлита) .
Знак минус означает, что элемент вращается в сторону противоположную вращению ведущего вала редуктора.
3.4.3. Передача типа 2k–h (рис. 2.2)
3.4.3.1. Из кинематической схемы следует .
3.4.3.2. Частота вращения входного (ведущего) вала редуктора равна частоте вращения двигателя или ведомого звена предыдущей передачи в зависимости от принятой схемы привода (рис. 2.4).
3.4.3.3. Частота вращения выходного (ведомого) вала редуктора (для этой схемы – частота вращения водила) .
3.4.3.4. Частота вращения сателлита вместе с водилом (абсолютная скорость сателлита) , где ;
, где ;
3.4.3.5. Частота вращения сателлита относительно водила
(относительная скорость сателлита) , .
3.4.4. Передача (рис. 2.3)
Порядок и суть действий аналогичны приведенным ранее,
поэтому сразу рассмотрим пример.
Пример 3.
Для привода по схеме рис. 2.4,а с планетарным редуктором,
у которого по схеме , определить частоты вращения валов,
если вал двигателя делает ,
число зубьев зубчатых колёс
, , , .
П3.1. Из кинематической схемы следует, что .
П3.2. = .
П3.3. =35,75 об/мин.
П3.4. Определяем частоту вращения водила , об/мин:
→ ; 
.
П3.5. Определяем частоту вращения сателлита вместе с водилом , об/мин:
→ ; =2,44;
об/мин.
П3.6. Определяем частоту вращения сателлита относительно водила , об/мин:
.
3.5. Коэффициент полезного действия
планетарных передач
Потери в планетарных передачах обусловлены трением в зацеплениях зубчатых колёс, трением в опорах и затратами на размешивание и разбрызгивание масла при прохождении зубчатыми колёсами масляной ванны, если смазка картерная.
КПД планетарных передач принято выражать через потери в обращённой передаче (то есть в передаче с «остановленным» водилом)
,
где – сумма потерь в зацеплениях при «остановленном» водиле;
– сумма потерь в опорах;
– потери на размешивание и разбрызгивание смазки (гидравлические потери).
Расчётным путём с наибольшей достоверностью могут быть определены потери в зацеплениях, обусловленные скольжением профилей. Для одной пары эти потери определяют по формуле .
Здесь (+) – для внешнего зацепления, (–) – для внутреннего.
Коэффициент трения обычно принимается
. Приближенно .
Потери мощности в подшипниках планетарной передачи меньше, чем в простой передаче, так как при симметричном расположении сателлитов силы в зацеплении уравновешиваются и не нагружают валы и опоры.
Гидравлические потери в планетарной передаче могут быть значительно больше, чем у простой. Это происходит вследствие того, что вращающимся с большой скоростью сателлитам необходимо выдавливать смазку из впадин зубьев, что создаёт большое гидравлическое сопротивление.
Раздельная оценка потерь в опорах и гидравлических потерь затруднена, поэтому на практике используют зависимость
.
Величина КПД определяется конкретной кинематической схемой. Общие правила:
– разветвление потока мощности от центрального колеса на несколько сателлитов не влияет на потери в зацеплении, поэтому вычисляют только для одного потока мощности;
– для передач 2k–h в сумме должны быть учтены два члена (по числу центральных колёс);
– для передач 3k учитывают только два члена для зацеплений центральных колёс с внутренними зубьями, но пренебрегают потерями в зацеплении центрального колеса с наружными зубьями;
– при определении суммы учитывают полное число подшипников основных звеньев и только одного сателлита, для передач с элементами на подшипниках качения и при числе сателлитов k ≥ 3:
– если со стороны двигателя или рабочего органа к внешним валам не приложены существенные изгибающие моменты, то потерями в опорах центральных колёс и водила можно пренебречь;
– в передачах 2k–h при частоте вращения водила < 500–800 об/мин обычно пренебрегают потерями в опорах сателлитов;
– в передачах 3k потери в опорах сателлитов можно не учитывать, если несколько завысить значение коэффициента трения в зацеплении, например, до .
Пример 4.
Определить КПД передачи если ; ; .
П4.1. Приняв = 0,1, найдём потери для пары колёс a и g:
=2,3 .
П4.2. Аналогично для пары зубчатых колёс g и b получаем:
.
П4.3.Приняв , получаем:
3.6. Проектный расчёт передач планетарного редуктора.
3.6.1. Вследствие соосности зацеплений, если размер передачи не ограничен какими-либо условиями, величину межосевого расстояния определяют из расчёта на контактную выносливость только одного из зацеплений – наиболее нагруженного. Необходимую изгибную прочность обычно удаётся обеспечить подбором соответствующего значения модуля m. Модуль, чаще всего, принимается одинаковым для всех передач редуктора.
Передачу для определения межосевого расстояния планетарного редуктора получают из исходной схемы «остановкой» водила. Для рассматриваемых передач (А, В, 3k) принимаются следующие положения.
Передача типа 2k–h (рис. 2.1)
3.6.3. При подсчёте числа циклов нагружения зубьев для определения допускаемых напряжений следует учитывать только скорость вращения колёс относительно друг друга и то, что центральные колёса a и b находятся в зацеплении с k сателлитами и одновенцовый сателлит работает двумя сторонами зуба.
3.6.4. При прочностном расчёте зубчатой планетарной передачи мотор-редукторов, наружный диаметр корпуса редуктора определяется диаметром присоединительного фланца электродвигателя. С определения этого размера начинается расчёт передачи. Его рационально назначать примерно равным диаметру фланца электродвигателя, а диаметр корончатых колёс принимать на 20–30 мм меньше. Затем по передаточному числу определяют диаметры колёс, модуль передачи и диаметры остальных зубчатых колёс, то есть выполняют геометрическое проектирование передач, а потом проверочные расчёты на прочность.
3.6.5. Ширина зубчатых колёс определяется из условий контактной и изгибной прочности зубьев и после подбора подшипников сателлитов. Окончательно принимается наибольшее значение.
3.6.6. Для изготовления зубчатых колёс планетарных передач используются те же материалы, что и для передач обычных редукторов. При этом повышение твёрдости рабочих поверхностей зубьев является эффективной мерой снижения массы планетарных передач.
Для передач с неограниченно большим числом циклов изменения напряжений ( ) при переходе от HB230 к HB350 масса редуктора снижается в два раза, а при переходе к цементированным колёсам с твёрдостью HRC60 – примерно в пять раз. При небольшом сроке службы передача с цементированными колёсами (HRC60) по сравнению с передачей с твёрдостью рабочих поверхностей зубьев HB250 может иметь большую нагрузку (в 5–10 раз).
Высокая твёрдость обеспечивается также закалкой токами высокой частоты (ТВЧ). В этом случае модуль колёс должен быть m³ 2,5. Наилучшие результаты такая обработка даёт, когда форма закалённого слоя повторяет очертания впадины.
Таблица 2
Значения величин, используемых при расчётах
зубчатых передач планетарных механизмов типа А, В, 3k
Планетарная
передача |
Рассчитываемая
зубчатая пара |
Передаточное число u = |
Передаваемый
момент, Т |
А, В, 3k
(рис. 3.4,а) |
a–g при |
|
|
А, В, 3k
(рис. 3.4,б) |
a–g при |
|
|
А, 3k (рис. 3.4,в) |
b–g |
|
|
B (рис. 3.4,в) |
b–f |
|
|
3k (рис. 3.4,в) |
с–f |
|
|
При твёрдости зубьев колеса HB £ 350 желательно иметь твёрдость зубьев шестерни не меньше, чем наибольшая твёрдость зубьев колеса.
При назначении твёрдости боковых поверхностей зубьев передач, выполненных по схеме А и предназначенных для многочасовой ежедневной работы, нужно помнить, что диаметры, полученные из условия требуемой работоспособности подшипников сателлитов, могут превысить размеры, полученные из условия прочности зубьев.
В тех случаях, когда несущая способность передач лимитируется изгибной прочностью зубьев (это часто, например, вторая ступень в передаче 3k), нужно применять материалы, подвергнутые нормализации или улучшению.
Если требуемая точность не превышает степень 7, то после закалки ТВЧ зубья можно не подвергать дополнительной механической обработке.
3.6.7. Применение в планетарной передаче нескольких параллельно работающих сателлитов уменьшает нагрузку, передаваемую каждым из них в отдельности, теоретически в k раз.
Исследования показывают, что планетарная передача очень чувствительна к ошибкам в шаге, межосевом расстоянии, угловом размещении сателлитов, соосности центральных колёс. Эти и другие погрешности приводят к неравномерности распределения нагрузки на сателлиты. При этом резко возрастают радиальные нагрузки на центральные колёса, подшипники сателлитов, зубья колёс. Большая неравномерность может даже выключить часть сателлитов из работы. Очевидно, что неравномерность распределения нагрузки приводит к увеличению габаритов, утяжелению и удорожанию передачи. Поэтому обеспечение более равномерного распределения нагрузки на сателлиты является основной задачей при конструировании передач.
Основными путями обеспечения более равномерного распределения нагрузки по сателлитам являются:
– высокая точность производства;
– подбор сателлитов по зазорам в зацеплении;
– постановка «плавающих» звеньев (как центральных, так и сателлитов).
Возможны и другие меры.
Одно из направлений решения этой задачи – применение плавающих (то есть безопорных) зубчатых колёс. Плавающим может быть любое из трёх основных звеньев или одновременно два из них (рис. 3.2). Для установки плавающих звеньев наибольшее распро-странение получили соедини -тельные муфты с одним или двумя зубчатыми сочленениями, обеспечива- ющими радиальную подвижность основных звеньев в процессе компен- сации ошибок изготовления и сборки (рис. 3.3; 3.4). Это приводит к усложнению конструкции и увеличению осевого габарита редуктора. Но, одновременно, позволяет снизить требования к точности изготовления и монтажа.
а) б)
Рис. 3.2. Изображение плавающих звеньев на кинематических схемах:
а) колесо а – плавающее; б) колёса a и b – плавающие
1 – зубчатая муфта с двумя зубчатыми венцами;
2 – центральное зубчатое колесо а с внешними зубьями;
3 – центральное зубчатое колесо b c внутренними зубьями;
4 – зубчатая муфта с двумя зубчатыми венцами
Часто муфты выполняют тем же инструментом и числом зубьев, что и соответствующие зубчатые колёса.
Соединительные муфты, имеющие одно зубчатое соединение (рис. 3.3,а,б; 3.4,а,б), выполнены как одно целое с плавающим центральным колесом. У этих муфт соотношение bм/dм не превышает 0,01–0,03. Муфты, выполненные на центральных колёсах внешнего зацепления при малом диаметре могут быть нагружены в большей степени, поэтому для них возможно соотношение bм/dм= 0,2–0,3.
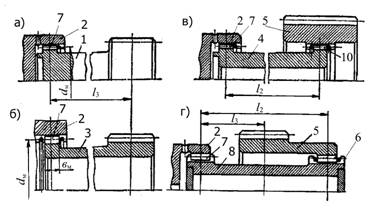
Рис. 3.3. Конструктивные решения плавающих зубчатых колёс
внешнего зацепления: 1– сплошное колесо а с одним венцом зубчатой муфты 7;
2 – элемент ведущей детали; 3– полое колесо а с одним венцом зубчатой муфты 7;
4 – зубчатая полумуфта с двумя венцами 7 и 6; 5 – зубчатое колесо а
(li – расстояние между центрами соединительных муфт и деталей)
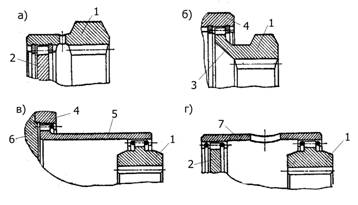
Рис. 3.4. Конструктивные решения плавающих зубчатых колёс внутреннего зацепления: а – плавающее колесо внутреннего зацепления (1)
и диск зубчатой муфты (2); б – плавающее колесо внутреннего зацепления
с одним венцом зубчатой муфты (3) и зубчатая полумуфта (4);
в – плавающее колесо внутреннего зацепления
и зубчатая полумуфта с двумя разносторонними венцами (5)
и элементами корпуса (6); г – зубчатая полумуфта с двумя односторонними венцами (7)
Муфты с двумя зубчатыми сочленениями более сложны, но обеспечивают меньшую неравномерность нагружения при тех же геометрических параметрах, что и муфты, имеющие одно зубчатое соединение.
Параметры соединительных муфт центральных колёс внешнего зацепления в планетарных передачах общего машиностроения могут выбираться аналогично параметрам муфт по ГОСТ 5006–55 или по ОСТ 92–8764–76. Муфты колёс внутреннего зацепления или водил, муфты быстроходных планетарных передач имеют нестандартные параметры.
При проектировании нестандартных муфт расчётный диаметр зубчатого венца dм может быть найден ориентировочно по эмпирической формуле, мм:
,
– отношение рабочей ширины зубчатого венца к расчётному диаметру,
= bм/dм (задаёмся, см. выше);
kM – коэффициент, зависящий от твёрдости рабочих поверхностей зубьев муфты:
при 40–50 HRC kM <6; при 58–62 HRC kM <12.
С целью предупреждения интенсивного изнашивания выполняется расчёт по условному давлению:
,
где =1,11 и = 1,0
соответственно при коэффициенте высоты зуба = 0,8 и = 1,0;
– коэффициент неравномерности удельной нагрузки для муфт,
нарезанных на жестких деталях, =1,1; = 1,3 – для муфт,
нарезанных на тонкостенном ободе центральных колёс.
Допускаемое давление в зависимости от вида термообработки зубьев принимается,
МПа:
– улучшение (НВ < 350) 3,6–4,6;
– закалка (HRC < 55) 5,3–6,7;
– термохимическая обработка (HRC < 62) 10–12.
Толщина обоймы муфты определяется из расчёта на кручение или вначале конструируется, а потом проверяется на кручение.
В муфтах планетарных передач общего машиностроения центрирование деталей сочленения осуществляется по окружности выступов зубчатых колёс daили по боковым поверхностям зубьев. В муфтах быстроходных передач центрирование производится по da с минимальными зазорами. Ориентировочно боковой зазор принимается 0,05m муфт, нарезаемых на жестких деталях, и примерно 0,08m для муфт, нарезаемых на тонкостенных податливых деталях.
Зубчатые муфты часто осуществляют осевую фиксацию плавающих звеньев. Для этого в центре или с двух сторон внешних или внутренних зубьев протачивают канавки, в которые закладывают пружинные кольца прямоугольного или круглого сечения. Для удобства монтажа концы колец круглого сечения могут быть отогнуты в радиальном или осевом направ- лении, а концы плоского кольца – просверлены. Соответствено по размеру отогнутых концов кольца должна быть выфрезерована часть зубьев на торце или сделаны пазы в ободе одной из деталей.
Для повышения износосойкости зубьев полумуфт их рабочие поверхности термически обрабатывают: более твёрдыми делают зубья полумуфт внешнего зацепления, менее твёрдыми – внутреннего.
В мелкосерийном производстве контакт зубьев по длине и степень участия в контакте всех зубьев проверяют по краске. В серийном произ -водстве начальный контакт полностью определяется принятой точностью изготовления сопряженных деталей.
Для учёта неравномерности нагружения сателлитов в расчёты вводится
поправочный коэффициентΩ ,
представляющий собой отношение максимальной нагрузки на сателлит к средней нагрузке, найденной в предположении равномерного распределения. Чем точнее изготовление колёс и тщательнее монтаж, тем меньше значения Ω. Если k = 3 и одно или два основных звена редуктора плавающие, передача выполнена с высокой точностью (не ниже 6 по ГОСТ 1643-81), то можно принимать Ω = 1. Если эти условия не выполняются, но точность изготовления колёс высокая,
то при k=3 рекомендуется принимать Ω = 1,1–1,15. Если же все колёса и водило не плавающие,
то Ω» 1,35–1,45, а при недостаточной точности изготовления и монтажа он ещё более возрастает до значений Ω» 1,6–1,8.
Нужно стремиться к выполнению условия Ω 1,1–1,3.
Пример 5.
Выполнить проектный расчет передач планетарного редуктора по следующим данным:
– кинематическая схема привода – рис. 2.4,а;
– мощность на входе привода Nэф = 15 кВт;
– электродвигатель 4А160М4У3: Nдв=18,5 кВт, nдв=1467 об/мин;
– кинематическая схема планетарного редуктора – схема , рис. 2.2;
– требуемое передаточное число редуктора up = 13;
– требуемый срок службы – 5 лет;
– коэффициенты использования во времени: в течение года – 0,5; в течение суток – 0,3;
– режим нагружения – средний равновероятный по ГОСТ 21354-87;
– максимальный возможный момент – 1,4 Т;
– привод работает в условиях закрытого отапливаемого помещения;
– привод – самостоятельная сборочная единица;
– редуктор будет использован в приводе серийной машины.
П5.1. Синтез передач редуктора.
П5.1.1. Принимаем:
– число сателлитов k = 3;
– в редукторе будут использованы прямозубые цилиндрические зубчатые колеса;
– в качестве плавающего звена будет вход редуктора – для подачи момента на шестерню a используется муфта с одним зубчатым венцом (по типу рис. 3.3, а). Тогда кинематическая схема редуктора принимает вид, приведенный на рис. П5.1.
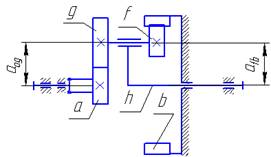
Рис. П5.1. Кинематическая схема редуктора
П5.1.2. Принимаем число зубьев шестерни кратное числу сателлитов zа = 27.
Варианты с zа = 21 и zа = 24 не проходят по условиям сборки .
Действуем, как в примере 2, получаем:
П5.1.3. Принимаем
.
П5.1.4. Проверяем:
– по условию сборки ;
– по условию соседства
\
;
– фактическое передаточное число редуктора
Таким образом: zа = 27; = 144; = 81; = 36.
П5.2. Частоты вращения валов редуктора
П5.2.1. Частота вращения ведущего вала
(вход редуктора, частота вращения солнечного колеса), об/мин:
П5.2.2. Частота вращения неподвижного колеса, об/мин:
П5.2.3. Частота вращения ведомого вала
(выход редуктора, частота вращения водила), об/мин:
П5.2.4. Частота вращения сателлита g–f вместе с водилом, об/мин:
или
П5.2.5. Частота вращения сателлита g–f относительно водила, об/мин:
Ведущий вал и водило вращаются в одну сторону, а сателлит g–f – в другую.
П5.3. Расчёт на прочность пары a–g
Размеры редуктора, выполненного по схеме , определяются передачей a–g при (табл. 2).
Материалы зубчатых колес a и g: сталь 40ХН; термообработка – сквозная закалка ТВЧ; предел текучести сердцевины ;
твердость боковых поверхностей зубьев:
шестерни , колеса .
П5.3.1. Допускаемые напряжения для расчета на контактную выносливость
,
где – допускаемое напряжение для расчета
на контактную выносливость при неограниченном сроке службы;
– пределы контактной выносливости при сквозной закалке: шестерни ;
колеса ;
SH – коэффициент безопасности;
SH = 1,2, так как ;
ZR – коэффициент, учитывающий влияние шероховатости рабочей поверхности зубьев,
при шероховатости 2,5 мкм, ZR = 0,95;
– коэффициент, учитывающий окружную скорость,
так как расчет ориентировочный и точное значение окружной скорости пока неизвестно,
принимаем .
При этих значениях:
для шестерни: ;
для колеса .
Коэффициент долговечности:
Для закаленных материалов .
При расчетах на контактную выносливость m = 6.
NHO – базовое число циклов, соответствующее 
.
При назначенных твердостях рабочих поверхностей зубьев:
для шестерни (za)
циклов;
для колеса (zg)
циклов.
NHE – фактическое число циклов нагружения:
где NH –число циклов нагружения за срок службы привода при заданном режиме эксплуатации,
цикл:
,
где сi – число зацеплений шестерни 1 за один оборот; в рассматриваемом случае c1 = 3;

t – требуемый ресурс привода, ч,
По таблице стандарта при средневероятном режиме нагружения
При таких данных:
,
В результате сравнения , поэтому принимаем KHL1=1;

Допускаемые напряжения,
МПа:
Поскольку передача прямозубая для расчетов принимаем меньшее значение
П5.3.2. Допускаемое напряжение для расчета на контактную прочность для закаленных материалов, МПа:
П5.3.3. Допускаемое напряжение для расчета на изгибную выносливость
где
предел изгибной выносливости при сквозной закалке ТВЧ:
;
коэффициент безопасности SF = 1,75;
коэффициент, учитывающий реверсивность работы = 0,75.
Таким образом:
Коэффициент долговечности:
Для закаленных материалов ;
– базовое число циклов, соответствующее пределу выносливости, цикл:
– фактическое число циклов нагружения
,
где – число циклов нагружения за срок службы привода при заданном режиме эксплуатации
;
;
по таблице стандарта
В результате сравнения в обоих случаях и .
Принимаем
Допускаемые напряжения для расчета на изгибную выносливость
П5.3.4. Допускаемые напряжение для расчета на изгибную прочность для закаленных материалов,
МПа
П5.3.5. Определение межосевого расстояния пары a–g из расчета на контактную выносливость,
мм
,
где – для прямозубых передач;
передаточное число проектируемой пары a–g:
T2 – момент на колесе этой пары, Нмм:

Считаем, что описанные условия (п. 3.6.7)
выполняются частично и принимаем .
Тогда
Потерями на трение для этой ситуации пренебрегаем (п. 3.5);
– коэффициент ширины колеса относительно межосевого расстояния;
принимаем =0.5.
– коэффициент нагрузки:
твердость рабочих поверхностей зубьев ; .
Таким образом, получаем, мм:
.
П5.3.6. Модуль зацепления, мм:
По стандарту принимаем m = 2,0 мм. Можно было принять m=1,5 мм, но, несколько снижая требования к точности изготовления, принимаем m=2,0 мм.
П5.3.7. Геометрические параметры передачи, мм:
солнечное колесо ;
сателлит .
Межосевое расстояние .
Ширина колес:
сателлит ;
солнечное колесо .
П5.3.8. Проверка зубьев зацепления a–g на изгибную выносливость.
Так как в редукторе применяются прямозубые передачи, то
где – коэффициент нагрузки при расчетах на изгибную;
– момент, действующий на i-ое колесо пары;
– коэффициент формы зуба i-го колеса пары;
– начальный диаметр i-го колеса пары;
так как колеса нарезаны без смещения инструмента
начальный диаметр равен делительному .
Расчет ведется по той детали, у которой частное меньше.
Коэффициент формы зуба находится по графикам (прил. 11, 12)
для внешнего зацепления в зависимости от величины смещения инструмента
при нарезке зубьев и числа зубьев:
при числе зубьев ,
при .
Таким образом,
Следовательно, расчет ведется по шестерне, МПа
П5.3.9. Проверка зуба зацепления a–g на контактную прочность
,
где sН – действующие контактные напряжения, МПа
Тmax - величина максимальной нагрузки, (техн. зад. примера 5);
sНmax – допускаемое напряжение для расчетапо максимальным нагрузкам,
Максимальные допускаемые напряжения, МПа <
П5.3.10. Проверка зуба на изгибную прочность
,
где (п. П5.3.4);
(техн. зад. примера 5);
(п. П5.3.4);
.
П5.3.11.Силы в зацеплении a–g:
– окружная сила на солнечном колесе a, Н
– окружная на колесе g, Н
– радиальная, Н
;
.
П5.4. Расчёт на прочность пары f–b.
П5.4.1. Исходные данные:
– модуль 
(получен в предыдущем расчете);
– межосевое расстояние

(получен в предыдущем расчете);
– передаточное число u=4 (получено в предыдущем расчете);
– момент на колесе f Tf =126945 Нмм (получен в предыдущем расчете);
– момент в зацеплении с колесом b Tb= Tf× u=126945×4= =507780 Нмм;
– момент на выходе (момент на водиле) Th=Tb k=507780×3 = =1523340 Нмм;
– делительные диаметры, мм:
; ;
– ширина колёс, мм: сателлит fb= ψbaa=0,5108=54;
колесо bb= fb + 6= 54+6 = 60.
П5.4.2. Принимаем:
– для сателлита f – материал сталь 40ХН, термообработка – улучшение, твердость 300НВ;
– для неподвижного колеса b – материал сталь 40Х, термообработка – улучшение, твердость 280НВ.
П5.4.3. Допускаемые напряжения:
Повторяя действия и используя пособия [10, 13, 14], с учётом вида зацепления, указанной в техническом задании возможной перегрузки, принятой термической обработки и частоты вращения деталей рассматриваемой пары, получаем допускаемые напряжения для расчётов:
– на контактную выносливость
МПа;
– на изгибную выносливость
, МПа;
– на контактную прочность ;
– на изгибную прочность .
П5.4.4. Расчёт на контактную выносливость
Фактически действующие в зацеплении f–b контактные напряжения:
Подставляя параметры передачи (не забывая, что зацепление внутреннее),
получаем, МПа:
.
П5.4.5. Проверка зубьев зацепления b–f на изгибную выносливость
Так как в редукторе применяются прямозубые передачи, то
Коэффициент формы зуба находится по графикам в зависимости от величины смещения инструмента при нарезке зубьев и числа зубьев (не нужно забывать о том, что пара f–b c внутренним зацеплением). Смещения инструмента при нарезке в данном случае нет,
а при числе зубьев ,
при .
Таким образом,
.
Следовательно, расчет ведется по колесу.
.
П5.4.6.Проверка зуба на изгибную прочность, МПа:
,
при (п. 4.5.6);
(техн. зад. примера 5)
П5.4.7. Проверка зуба на контактную прочность, МПа:
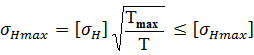
,
где , МПа;
величина максимальной нагрузки .
Максимальные действующие контактные напряжения, МПа:
П5.4.8. Силы в зацеплении f–b:
– окружная, МПа

– радиальное усилие, Н

|