3.3
Электрогидроимпульсная штамповка (ЭГИШ)
Основана
на преобразовании электрической, накопленной в
конденсаторной батарее, в
механическую энергию гидродинамического
возмущения, используемую
для осуществления требуемой технологической
операции.
Параметры
давления, возникающего в разрядной камере при
высоковольтном
электрическом разряде в жидкости, характер его
распределения на
поверхности деформируемой заготовки являются
определяющими при расчете техпроцесса ЭГИШ.
Амплитуда
давления в камерах малого объема при выделившейся
энергии W и емкости С
конденсаторной батареи может быть рассчитана по
формуле [2]

Зная
давление, необходимое для выполнения конкретной
технологической операции, определяют энергию конденсаторной
батарее
электрогидроимпульсного пресса [2]
Электрогидроимпульсная вырубка.
Расчет
энергозатрат для операции ЭГИ вырубки осуществляется в
следующей последовательности:
•
определение величины давления в разрядной камере, необходимого
зля осуществления разделительных операций.
• расчет
величины запасаемой энергии
Wзап и Uраб
рабочего напряжения Uраб
заряда конденсаторной батареи при заданных остальных параметрах
разрядного контура.
Величина давления может быть
подсчитана
,
где Pв
min
-
минимальное усилие
пробивки, достаточное для разделения
штампуемого материнала;
F-
площадь деформируемой части заготовки;
Усилие
пробивки-вырубки можно найти из выражения

где II -
периметр пробиваемого отверстия;
-
динамический предел прочности,

Величина давления (Н/м2)
в разрядной камере для пробивки отверстия без подпора
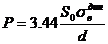
с подпором
,
где
-
величина зазора между режущей кромкой матрицы и подпором,

Схема
вырубки без подпора осуществляется с относительным диаметром
пробиваемых отверстий
D/S=50-100.
При
МПа
,
а при
;
Точность
получаемых изделий соответствует 11-12 квалитетам.
Штамповку
деталей сложной формы при D/S>150 следует вести с
подпором. Точность
штампуемых деталей этим способом не ниже 7-8
квалитета.
Для ЭГИ
вырубки-пробивки других материалов (гетинакс, стеклоткани,
техническая резина и др.)
применяют дополнительную деталь-спутник,
стальная
прокладка толщиной S=0.1-1.5 мм. Основной недостаток этой схемы
- увеличение затрат энергии на 20%.
Электрогидроимпульсная вытяжка
(ЭГИВ) используется при значениях
относительной толщины S0/Dзаг=1/60...
1/500 из листовых материалов
толщиной
0.5-3.0 мм.
Коэффициент вытяжки
за
один разряд. Усилие
прижима при ЭГИВ следует
рассчитывать из условия, что величина
давления прижима в 3-5
раз больше, чем при штамповке со статическими нагрузками. Радиус
перетяжного ребра матрицы рекомендуется выбирать в пределах
rм=(6-10)S0,
причем для заготовки с меньшим значением S0/Dз
следует выбирать большие значения радиусов. Прямая вытяжка
целесообразна при S0/Dз
следует выбирать большие значения радиусов. Прямая вытяжка
целесообразна при S0/Dзаг 0.003
и h/dм=0.3
(d – диаметр очка матрицы).
Вытяжка с
применением подпора (жесткого или эластичного) позволяет
значительно увеличить относительную глубину вытяжки до 30%.
Остальные
операции ЭТИВИ
-
формовка, отбортовка, калибровка и правка и др. Являются
производными рассмотренных выше операций и не вызывают особых
трудностей при расчете.
Технологические процессы штамповки деталей
из пространственных заготовок ограничиваются размерами в плане
от 40.. .250 мм, высотой до 800 мм и толщиной стенки в пределах
(0.2...2.5) мм.
Последовательность разработок технологических процессов ЭГИ
штамповки
Разработка технологического процесса осуществляется в
соответствии с пунктами указанными в разделе 2.
В случае
штамповки деталей из плоской заготовки эта задача сводится к
выбору диаметра (или формы и размеров в плане) плюс величина
припуска необходимая для зажима и уплотнения фланца заготовки.
В случае
пространственной заготовки при вытяжке с утяжкой фланца следует
учитывать величину его перемещения.
При
выборе оптимальных схем ЭГИ - штамповки тая каждого перехода
решаются следующие задачи:
• выбор
зоны разряда относительно деформируемых участков заготовок;
•
определение формы канала разряда и способа его формирования;
• выбор
типовых для каждой группы деталей конструкций разрядной камеры
или разрядного устройства.
При
проектировании оснастки необходимо конструктивно решить
следующие задачи:
•
надежное уплотнение торцов заготовки в течение всего процесса
деформирования
• полное
удаление воздуха из пространства между заготовкой и матрицей при
формоизменяющих операциях
•
надежный зажим торцов заготовок в случае обрезки
•
полное
и быстрое удаление отходов при выполнении разделительных
операций
•
возможность механизации и автоматизации |