ФЕДЕРАЛЬНОЕ АГЕНСТВО ПО ОБРАЗОВНИЮ
ГОСУДАРСТВЕННОЕ ОБРАЗОВАТЕЛЬНОЕ УЧРЕЖДЕНИЕ
ВЫСШЕГО ПРОФЕССИОНАЛЬНОГО ОБРАЗОВАНИЯ
ДОНСКОЙ ГОСУДАРСТВЕННЫЙ ТЕХНИЧЕСКИЙ УНИВЕРСИТЕТ
Кафедра «Машины и технология обработки металлов давлением»
МЕТОДИЧЕСКИЕ УКАЗАНИЯ
к практическим занятиям по дисциплине
«Технология ковки и объемной штамповки»
Ростов-на-Дону 2007
Составитель: кандидат технических наук, доцент Шипулин А.И.
Методические указания к практическим занятиям по дисциплине «Технология ковки и объемной штамповки» для студентов дневного и заочного обучения по специальности 150201 «Машины и технология обработки металлов давлением».
Ростов-на-Дону: Издательский центр ДГТУ, 2007, с.9
Печатается по разрешению методической комиссии факультета «Технология машиностроения»
Научный редактор- д.т.н., профессор Резников Ю.Н.
Рецензент- к.т.н.. доцент Калинин Г.Г.
@ Издательский центр ДГТУ, 2007
1. Общие положения
Выполнение практических занятий по технологии ковки и объемной штамповки является одним из этапов подготовки специалистов в области технологий обработки металлов давлением.
Целью практических занятий является закрепление полученных теоретических знаний и оценка качества усвоения лекционного материала по дисциплине «Технология ковки и объемной штамповки», а также приобретение опыта самостоятельного решения вопросов, связанных с разработкой технологического процесса ковки.
В процессе практических занятий студент должен:
- разработать технологический процесс ковки;
- освоить работу со специальной технической литературой;
На практических занятиях рассматриваются следующие вопросы разработки технологического процесса:
- выбор варианта технологического процесса ковки;
- разработка чертежа поковки;
- выбор вида и определение размеров заготовки;
- выбор основных кузнечных операций и их последовательности. Выбор основного инструмента;
- установление температурного режима ковки;
- определение технологического усилия и выбор оборудования по мощности;
- организации рабочего места при ковке и определение состава бригады рабочих. Расчет нормы времени.
2. Указания к разработки технологического процесса ковки
2.1. Выбор варианта технологического процесса
Выбор варианта технологического процесса ковки сводится к определению на каком ковочном оборудовании будет производиться ковка данной поковки. В современных условиях ковка поковок деталей из стали может производиться на ковочных молотах и гидравлических ковочных прессах. На молотах обычно куют поковки, средняя масса которых составляет (фасонные поковки), а простых поковок типа гладких валов до из стального проката или мелких слитков. Поковки большей массы изготавливают на гидравлических ковочных прессах в основном их средних и крупных слитков. В соответствии с рекомендациями работы [1] в качестве критерия выбора варианта технологического процесса является масса детали после механической обработки.
2.2. Разработка чертежа поковки
Исходным документом для разработки чертежа поковки является чертеж детали.
Чертеж поковки представляет собой чертеж детали с увеличенными размерами на величину припуска на механическую обработку, менее жесткими допусками на размеры и упрощенной формой, более удобной для ковки.
Припуском называется слой металла в поковке, подлежащий удалению механической обработкой для получения требуемых размеров по чертежу готовой детали и заданного качества поверхности.
Допуском называется допустимое отклонение размеров поковки, обусловленное невозможностью изготовления ее с абсолютно точными размерами.
Напуском называется дополнительный объем металла, добавленный к поковке для упрощения формы.
В разработку чертежа поковки входит: назначение припусков, допусков и при необходимости напусков; составление чертежа поковки; определение объема и массы поковки.
Припуски и допуски на поковки назначаются в зависимости от формы и размеров поковки, а также вида оборудования. Для поковок, изготавливаемых ковкой из углеродистой и легированной сталей на молотах припуски и допуски назначаются по ГОСТ7828-70, в котором все поковки разбиты на 17 групп. Для поковок, изготавливаемых ковкой на гидравлических ковочных прессах припуски и допуски назначаются по ГОСТ7062-79, в котором все поковки разбиты на 18 групп.
Для получения рациональной формы поковки, при которой значительно упрощается технология ковки ГОСТами регламентированы напуски на наименьшие размеры выемки, выступа, бурта, фланца. С напусками отковывают поковки деталей с отверстиями, у которых диаметр отверстия меньше 60mm.
При составлении чертежа поковки поковку вычерчивают в масштабе M 1:1 или в меньшем масштабе в зависимости от размеров поковки сплошными линиями, внутри контура поковки тонкими сплошными линиями наносят контур детали. Размеры проставляют для поковки, а в скобках ниже размера поковки наносят размеры детали. При простановке размеров следует указывать общую длину поковки и оставлять участок с непроставленной длиной, получаемой как разность между проставленными размерами. Номинальные размеры поковки, изготавливаемой на молотах, допускается округлять до ближайших целых чисел (в большую сторону), а у поковок изготавливаемых на прессах – до чисел, оканчивающихся на 5 или 0. Все размеры поковки, необходимые для ее изготовления, следует проставлять с указанием допусков. Кроме того, на чертеже следует указать все дополнительные сведения о поковке, такие как твердость материала поковки и вид термической обработки, величины допустимой глубины поверхностных дефектов, бочкообразности и дефектов формы, способа очистки поковки от окалины.
Затем по чертежу поковки определяют ее объем, как сумму элементарных объемов. Массу поковки определяют по формуле

где плотность стали. Принимаем
2.3. Выбор вида и определение размеров заготовки
Определяющим фактором при выборе вида заготовки является масса поковки и марка материала. Если масса фасонной поковки из углеродистой или легированной стали не превышает 200кг, а поковки типа вал не превышает , то принимают стальной прокат. Во всех остальных случаях принимают слиток.
Объем заготовки в общем случае определяем по формуле
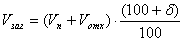
Где объем отхода металла. Принимаем для заготовок из слитка 
объем прибыльной, донной частей слитка, которые принимаются в процентах от объема слитка
объем отходов в виде обсечки, обрубки конца, перемычки при прошивке. Принимается в процентах от массы поковки или определяется по таблицам, графикам или рассчитывается по формулам в соответствии с рекомендациями работы [1] (с.476-477)
угар металла при нагреве. Принимается в процентах от массы нагреваемого металла (с.477 [1]).
Затем определяют массу заготовки по формуле

Зная объем (массу) и вид заготовки, определяют размеры заготовки. На выбор размеров заготовки оказывает влияние основной формоизменяющей операции при ковке. При ковке поковки из слитка по известной массе заготовке выбирают слиток с ближайшей большей массой и поперечными размерами по сечению с учетом укова (общий уков при ковке из слитка должен быть с.477 [1]). Если выбранный слиток не обеспечивает требуемый уков, то необходимо ввести дополнительно операцию осадки.
При ковке из проката поперечное сечение заготовки выбирают по сортаменту с учетом того, что
Где y - уков, который принимается равный y=1.25(с.477 [1])
Зная размеры поперечного сечения и объем заготовки, определяем длину заготовки.
2.4. Выбор основных кузнечных операций и их последовательности.
Выбор основного инструмента
Выбор основных кузнечных операций и их последовательность производится в соответствии с классификацией поковок, получаемых ковкой (таб.74 с.478 [1]). Принадлежность к то или иной группе по классификации определяется формой изготавливаемой поковки, материалом и техническими условиями на поковку.
Затем производится расчет размеров и составление эскиза заготовки после выполнения основной кузнечной операции и выбор необходимого кузнечного инструмента для выполнения кузнечных операций.
2.5. Установление температурного режима ковки
В температурный режим ковки входит: выбор типа нагревательного устройства, определение температурного интервала ковки и расчет продолжительности нагрева заготовки.
Выбор типа нагревательного устройства определяется видом, размерами и материалом нагреваемой заготовки, а также видом и мощность основного кузнечного оборудования. Так заготовки из стального проката и небольшие слитки, которые в основном куются на ковочных молотах, рекомендуется нагревать в камерных пламенных печах, а крупные слитки в методических и полуметодических печах. Выбрав нагревательное устройство необходимо дать его техническую характеристику.
Температурный интервал ковки определяется таб.1 с.219 [1] или по диаграмме состояния железоуглеродистых сплавов в зависимости от марки стали.
Продолжительность нагрева заготовок под ковку в камерных печах определяется по формуле с.48 [2]
При ковке из проката поперечное сечение заготовки выбирают по сортаменту с учетом того, что
( )
где a коэффициент, зависящий от вида заготовки и марки стали. Принимаем для: - углеродистых и низколегированных сталей из проката a=12.5; из слитков a=20
высоколегированных и инструментальных сталей из проката, слитка a=25; a=30
Dзаг диаметр заготовки, м
Продолжительность нагрева заготовок в методических печах определяется по формуле с.449 [2]
(мин)
где S толщина заготовки, см
2.6. Определение технологического усилия и выбор оборудования по мощности
Выбор кузнечного оборудования производится по наибольшему технологическому усилию необходимого для выполнения основных кузнечных операций. Технологическое усилие определяется по формулам (с.444; с.445; с.446 [1]). При наличии в технологическом процессе операции осадки достаточно определить усилие осадки по формулам (с.441 [1]) и по нему выбрать необходимое оборудование. Выбрав кузнечное оборудование, необходимо дать его техническую характеристику.
2.7. Организация рабочего места при ковке и определение состава
бригады рабочих. Расчет нормы времени.
Организация рабочих мест при ковке построена на основе агрегатирования. Основной машиной в агрегате является ковочный молот или гидравлический ковочный пресс. Молотовой агрегат включает: молот, печи, кран поворотный, манипулятор (для крупных молотов). Прессовый агрегат включает: гидравлический ковочный пресс, печи, загрузочную машину, кран с кантователем, манипулятор.
Кроме того к агрегатам придается определенный набор универсального инструмента и приспособлений. Пример организации рабочего места показан в приложениях 1 и 3.
Состав бригады рабочих для обслуживания ковочных агрегатов определяется в зависимости от типа основного кузнечного оборудования и его мощности и выбирается по таблице (см. приложения 2; 4).
Норма времени на ковку определяется по формуле
где T0 - основное (машинное) время, т.е. время работы кузнечной машины при выполнении технологического процесса;
Tвс - вспомогательное время, т.е. время затраченное на подачу, установку и манипулирование заготовкой при ковке, подачи инструмента, удаления поковки, отходов. Определяется по таблицам [3; 4];
K - плановый процент затрат рабочего времени на обслуживание рабочего места, отдых и личные надобности. Принимается K=30%.
Для определения основного и вспомогательного времени составляется таблица, в которой по пунктам расписан весь технологический процесс с указанием затраченного времени на каждую операцию. Затем отдельно суммируется основное и вспомогательное время и рассчитывается норма времени ( ).
Литература:
- Ковка и штамповка. Справочник том 1. //ред. Семенова Е.И. М., «Машиностроение», 1986
- Шипулин А.И., Шипулин И.А. Нагрев и нагревательные устройства. Учеб. пособ. Ростов-на-Дону, ДГТУ, 2000
- Общемашиностроительные нормативы времени для технологического нормирования работ по свободной ковке под молотами. М., «Машиностроение», 1967
- Общемашиностроительные нормативы времени для технологического нормирования работ по свободной ковке под парогидравлическими прессами. М., «Машиностроение», 1967
Приложение 1
Схема организации рабочего места при ковке на молотах
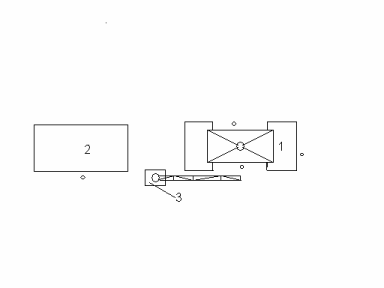
1. Молот ковочный паровоздушный
2. Камерная нагревательная печь
3. Кран поворотный
Приложение 2
Состав бригады, обслуживающей агрегаты ковочных молотов
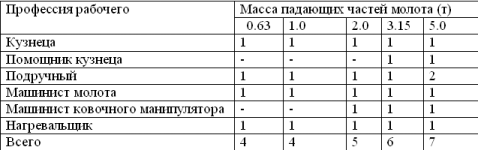
Приложение 3
Схема организации рабочего места при ковке на гидравлических прессах
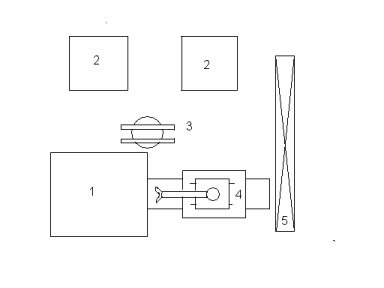
1. Пресс гидравлический ковочный
2. Печи нагревательные
3. Плита поворотная (стол)
4. Манипулятор
5. Ковочный мостовой кран
Приложение 4
Состав бригады, обслуживающей агрегаты ковочных гидравлических прессов
Редактор
В печать . Объем 0.5 усл. п. л., уч.- изд.л. Офсет.
Бумага тип №3. Формат 60х84/16. Заказ № . Тираж 100. Цена
Издательский центр ДГТУ
Адрес университета и полиграфического предприятия:
344010, г. Ростов-на-Дону, пл. Гагарина, 1. |