ФЕДЕРАЛЬНОЕ АГЕНСТВО ПО ОБРАЗОВАНИЮ
ДОНСКОЙ ГОСУДАРСТВЕННЫЙ ТЕХНИЧЕСКИЙ УНИВЕРСИТЕТ
Кафедра «Машины и технология обработки металлов давлением»
Методические указания
к выполнению курсового проекта по дисциплине «Технология ковки и объемной штамповки»
Ростов-на-Дону 2007
Составитель: к.т.н., доцент А.И. Шнпулин
УДК 621.73:37». 147.85 (07)
Методические указания к выполнению курсового проекта по дисциплине «Технология ковки и объемной штамповки./ДГТУ. Ростов-на-Дону,,
Методические указания предназначены для студентов дневного и заочного обучения специальности 15.0201 - « Машины и технология обработки металлов давлением ».
Печатается по решению методической комиссии факультета «Технология машиностроения».
Научный редактор д.т.н., профессор Б.С.Мороз Рецензент к. Т. Н., доцент Г.Г. Калинин
Донской государственный технический университет.2007
1. Цели и задачи курсового проектирования
Выполнение курсового проекта по технологии ковки и объемной штамповки один из этапов подготовки специалистов в области технологии обработки металлов давлением.
Целью курсового проектирования является систематизация, закрепление и расширение теоретических знаний по дисциплине «Технология ковки и объемная штамповка», а также более глубокое изучение отдельных разделов данной дисциплины, приобретение опыта самостоятельного решения вопросов, связанных с разработкой технологического процесса и конструирования штампов.
Курсовой проект студенты выполняют самостоятельно с учетом передового опыта кузнечно-штамповочного производства, применения прогрессивных технологий горячей объемной штамповки и современных методов расчетов.
Работа над курсовым проектом и его защита должны выявить общую техническую и экономическую подготовку студента, глубину его теоретических и инженерных знаний.
2. Состав, содержание и объем курсового проекта.
2.1. Задание на курсовой проект
Задание на курсовой проект составляется руководителем проекта и утверждается заведующим кафедрой.
Как правило, тематика курсовых проектов предусматривает разработку технологического процесса горячей объемной штамповки, хотя в отдельных случаях может быть и технология ковки
В задании формулируется тема курсового проекта, указывается годовая программа производства поковок. К заданию прилагается чертеж готовой детали (детали после механической обработки) с техническими условиями на изготовление.
2.2.Состав, объем и содержание курсового проекта
Курсовой проект состоит из двух основных частей: пояснительной записки объемом страниц, набранных на ЭВМ на формате A4 ( ) и графической части ( ), выполненных в карандаше на стандартном формате A1, в соответствии с ГОСТ 2.301-68 или с помощью графического редактора на ЭВМ.
Пояснительная записка состоит из двух основных частей: технологической и организационно-экономической.
К технологической части курсового проекта относятся все расчеты, связанные с технологическим процессом и конструированием штампов.
К организационно-экономической части курсового проекта относятся составление технологической карты штамповки и определение технологической себестоимости поковки.
Графическая часть проекта, в зависимости от разработанного технологического процесса может содержать: лист технологических переходов;
сборочный чертеж основного штампа; сборочный чертеж обрезного штампа;
лист деталировки обрезного штампа и другие. Количество и содержание листов курсового проекта согласуется с руководителем проекта.
3. Указания к выполнению курсового проекта
Курсовой проект выполняется в следующей последовательности: выбор варианта технологического процесса; разработка чертежа поковки; расчет переходов штамповки и определение размеров заготовки; определение нормы расхода материала; тепловой режим штамповки; расчет и конструирование ручьев штампа, определение технологического усилиям и выбор оборудования; конструирование штампа в целом; определение усилия обрезки облоя, прошивки отверстия и выбор обрезного пресса; конструирование штампа для обрезки облоя и прошивки отверстия; разработка организационно-экономической части. Ниже излагаются указания по выполнению каждого раздела курсового проекта.
3.1. Выбор варианта технологического процесса
Для выбора варианта технологического процесса штамповки используют способ укрупненного проектирования технологии, при котором расчет основных технико-экономических параметров выполняется по эмпирическим формулам без подробной разработки технологии штамповки на различном кузнечном оборудовании. В качестве критерия выбора варианта технологического процесса принимают минимальные приведенные затраты. Величина, которых определяется по формуле
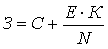
где C - себестоимость изготовления поковки;
E - нормальный коэффициент окупаемости капитальных эатрат. Принимаем . Большее значение коэффициента принимают при разработке технологического процесса с частичной механизацией и автоматизацией;
K - капитальные затраты (стоимость различных видов кузнечного оборудования),
N - программа годового выпуска поковок.
Расчет себестоимости изготовления поковки выполняется по следующей методике: в соответствии с классификацией поковок выбираются эмпирические формулы, предложенные в работе [10] для определения массы поковки и заготовки, критерия сложности поковки, усилия деформирующего оборудования и себестоимости поковки. Затем определяются приведенные затраты по каждому варианту технологического процесса. Допускается использование ЭВМ для расчета выбора варианта технологического процесса.
3.2. Разработка чертежа поковки
Исходным документом для разработки чертежа поковки является чертеж детали.
Чертежи поковки рекомендуется разрабатывать в следующем порядке: выбор линии разъема; назначение припусков на механическую обработку, допусков на размеры поковки и напусков; определение штамповочных уклонов и радиусов закругления, конструирование наметки и определение толщины перемычки под прошивку, оформление чертежа поковки.
3.2.1. Выбор линии разъема
При выборе линии разъема в общем случае необходимо учитывать возможность свободного извлечения поковки из окончательного ручья, заполнения ручья за счет осаживаемой заготовки, контроля сдвига верхней и нижней части поковки. Кроме этого желательно, чтобы линия разъема совпадала с плоскостью двух габаритных наибольших размеров детали.
3.2.2 Назначение припусков на механическую обработку,
допусков на размеры поковки и припусков
Припуски на механическую обработку штампованной поковки и допуски на изготовление поковки определяются ГОСТ 7505-89 в зависимости от массы поковки, класса точности изготовления, группы стали, степени сложности, размеров летали и чистоты обрабатываемой поверхности [1].
С учетом характера производства устанавливается класс точности изготовления поковки. Первый класс - поковки повышенной точности, полученные в условиях массового производства. Второй - поковки нормальной точности, полученные в условиях серийного производства.
Стандарт выделяет две группы стали M1 -углеродистые и легированные стали с содержанием углерода до 0,45% и легирующих элементов до 2%, М2 -легированные стали, кроме указанных выше.
Степень сложности поковки определяется отношением массы (объема) поковки к массе (объему) геометрической фигуры, в которую вписывается поковка ГОСТ7505-89 предусматривает четыре степени сложности поковок.
При горячей штамповке припуски на механическую обработку и допуски на размеры поковки назначаются только на сопрягаемые размеры детали. Припуск на механическую обработку увеличивается в зависимости от массы поковки, если заготовку, из которой изготавливают поковку, будут нагревать в пламенной печи.
3.2.3. Назначение штамповочных уклонов и радиусов закругления.
При изготовлении поковок на молотах и прессах штамповочные уклоны должны устанавливаться на всех поверхностях поковки, располагающихся параллельно движению инструмента. При изготовлении поковок на горизонтально-ковочной машине штамповочные уклоны назначаются на поверхности, располагающиеся перпендикулярно движению главного ползуна, а также на поверхности выступов и углублений, располагающиеся параллельно движению ползуна. Величина внутренних штамповочных уклонов долям быть на 2° или 3° больше наружных штамповочных уклонов ГОСТ 7505-19 предусматривает ряд значений штамповочных уклонов 3°. 5°, 7°; 10°; 12°; 15°.
Минимальные значения радиусов закругления внешних углов поковок должны быть на 0,5+1мм больше величины нормального припуска на механическую обработку этой поковки. Величина внешнего радиуса закругления зависит от массы поковки и глубины полости ручья.
Внутренние радиусы закруглений на поковках должны быть в 3÷4 раза больше внешних радиусов закруглений для данной поковки ГОСТ 7505-89 предусматривает ряд значений радиусов закруглений: 1; 1,5; 2; 2,5; 3; 4; 5; 6; 8; 10; 12,5; 15; 20; 25 мм.
3.2.4 Конструирование наметки и определение толщины
перемычки под прошивку.
Согласно ГОСТ 7505-89 сквозные отверстия и углубления в поковке выполняются, если диаметр отверстия или углубления не менее 30÷25 мм и ось совпадает с направлением движения инструмента. При этом получается наметка с тонкой перемычкой, которая определяется по формуле [1] в зависимости от диаметра отверстия и глубины наметки.
Вид наметки под прошивку зависит от соотношения глубины наметки и диаметра отверстия.
3.2.5. Оформление чертежа поковки.
Чертеж холодной поковки - основной технологический документ, который разрабатывается по табличным и расчетным данным с учетом следующих правил: чертеж поковки строится в таком виде, как поковка получается в окончательном ручье основного технологического оборудования; чертеж поковки рекомендуется выполнять в масштабе 1:1 (допускается уменьшение и увеличение масштаба), контур детали на чертеж поковки наносится тонкой линией; система простановки размеров поковки должна соответствовать системе размеров детали и учитывать удобство проверки величины припуска, измерения размеров поковки, простоту разметки поковки при контроле.
На чертеже поковки должны быть указаны основные технические требования: термообработка и твердость, способ очистки поковок от окалины, допускаемые величины смещения поковки по линии разъема штампа и остатков заусенца после обрезки, допускаемая глубина поверхностных дефектов и дефектов формы.
3.3. Расчет переходов штамповки и определение размеров заготовки
Определение нормы расхода металла.
Выбор переходов штамповки зависит от применяемого кузнечного оборудования и классификации поковок, штампуемых на этом оборудовании.
3.3.1. Определение объема заусенца
Для расчета переходов штамповки в открытых ручьях, необходимо знать объем заусенца. При штамповке на молоте тип и размеры облойной канавки выбираются в зависимости от толщины заусенца, которая определяется по формуле с. 65 [1]. Выбрав облойную канавку, определяется объем заусенца по формуле с.66 [1].
При штамповке на кривошипном горячештамповочном прессе форму и размеры заусенца определяют по таблице [1] в зависимости от усилия пресса, которое определяется ориентировочно с 208 [1], а затем определяется объем заусенца по формуле с 183 [1].
При штамповке на горизонтально-ковочной машине размеры заусенца определяются по таблице с 283 [1] в зависимости от диаметра высаживаемой части поковки.
3.3.2 Расчет переходов штамповки на молотах и КГШП
и определение размеров заготовки.
Для поковок первой группы (поковок удлиненной формы) расчет переходов штамповки рекомендуется производить в следующей последовательности:
- построить расчетную заготовку и эпюру сечений согласно методике, приведенной в работе [1];
- по расчетной заготовке определить коэффициенты α и β;
- в зависимости от массы поковки и коэффициентов α и β по диаграмме А. В. Ребельского [3] выбрать заготовительные переходы.
Если для поковок, штампуемых на KI1UII. требуется подкатка или протяжка, то следует применить одновременную штамповку двух поковок, расположив их «валетом». При том уменьшится перепал в площадях поперечных сечений у объединенной расчетной заготовки, что даст возможность устранить переходы протяжки и подкатки, заменив их пережимом. Штамповка поковок «валетом» допускается при массе одной поковки не более 3 кг. Для поковок больше 3 кг следует профилирование заготовки осуществлять на ковочных вальцах. Разработку процесса вальцовки заготовок на ковочных вальцах рекомендуется производить в соответствии с методикой [7].
После выбора переходов штамповки определяется объем заготовки с учетом угара металла при нагреве по формуле
,
где Vуг, Vоб – объём поковки и объём заусенца. Определяются совместно по эпюре сечений;
Vуг – объём угара, который принимается в процентах в зависимости от способа нагрева.
В зависимости от принятых заготовительных переходов определяется площадь поперечного сечения и диаметр заготовки. Затем диаметр заготовки уточняется по ГОСТ и определяется длина заготовки.
При штамповке поковок второй группы (поковок круглых и квадратных в плане) определяется объем и диаметр заготовки из условии устойчивости заготовки, т. е. отношения высоты заготовки к диаметру, которое должно быть меньше или равно 2,5. Затем диаметр заготовки уточняется по ГОСТ и определяется длина заготовки. В зависимости от сложности поковки, для данной группы принимаются заготовительные переходы: осадка, расплющивание, высадка или специальная протяжка.
3.3.3. Определение размеров заготовки
и переходов штамповки на ГКМ.
Переходы штамповки на ГКМ существенно отличаются от переходов, применяемых на молотах и прессах. На ГКМ производят набор, формовку, прошивку и пробивку, обрезку и отрезку. Набор выполняется для увеличения толщины заготовки и может осуществляться в несколько переходов, которые являются заготовительными. Штамповочными переходами являются формовка или прошивка.
При выборе переходов штамповки на ГКМ и определении размеров заготовки прежде необходимо решить вопросы о виде окончательного формовочного ручья, виде заготовки и применении переднего или заднего упоров.
Для поковок первой группы (стержень с утолщением) диаметр заготовки принимается равный диаметру недеформируемой части поковки, т.е. диаметру стержня. Затем определяется объём высаживаемой части поковки с учетом объема заусенца (при наличии его) и угара металла при нагреве. Зная объем и диаметр заготовки, определяется длина высаживаемой части заготовки. Общая длина заготовки определяется как сумма длины стержня и длины высаживаемой части.
Наборной (заготовительный) переход выбирается из условия, что отношение длины высаживаемой части к диаметру заготовки больше 2,5. Расчет наборного перехода выполняется в соответствии с методикой [1]. После расчета наборного перехода определяется отношение длины к среднему диаметру конуса и если это отношение больше 2,5, то требуется следующий наборной переход. Гели это отношение меньше или равно 2,5, то следующий наборной переход не требуется.
Для поковок второй и третей групп диаметр заготовки определяется из построенной расчетной заготовки (методика построения расчетной заголовки та же, что и для молотовых поковок).
Длина заготовки (длина высаживаемой части) определяется по формуле
,
где Vф – объём формовочного окончательного ручья.
Заготовительные наборные переходы рассчитываются так же, как и для поковок первой группы. Формовочно-прошивные переходы выбираются в зависимости от отношения глубины прошивки к диаметру отверстия и рассчитываются по методике, предложенной в работе [11].
3.3.4. Определение нормы расхода металла.
Расчет нормы расхода металла выполняется в следующей последовательности:
- определяется длина торцевого обрезка по формуле [3]
;
- принимается, что потери на некратность равны половине длины заготовки;
- определяется полезная длина прутка по формуле [3]
,
где Ln - длина прутка в соответствии с требованиями поставки;
- определяется заготовительный коэффициент использования металла по формуле [3]
;
- определяется норма расхода металла по формуле

3.4. Тепловой режим штамповки.
В тепловой режим штамповки входит: определение температурного интервала ковки и штамповки, продолжительности нагрева заготовки; выбор типа нагревательного устройства.
Тип нагревательного устройства выбирается на основании производительности штамповочного оборудования. После выбора типа нагревательного устройства необходимо дать его техническую характеристику.
3.5. Расчет и конструирование ручьев штампа
При расчете и конструировании ручьев следует использовать в качестве исходных данных расчеты по переходам штамповки.
Расчет ручьев при штамповке на молотах и прессах начинается с расчета и конструирования окончательного ручья. Окончательный (чистовой) ручей разрабатывается по чертежу горячей поковки, размеры которой определяются по размерам холодной поковки с учетом коэффициента усадки металла (для стали коэффициент усадки составляет 1,2... 1,5%). Чертеж должен представлять поковку в таком виде, в каком она получается в окончательном ручье. При оформлении чертежа горячей поковки необходимо учитывать следующее: размеры проставляются таким образом, чтобы построение фигуры при разметке ручья не вызывало затруднений; размеры по высоте привязываются к линии разъема, на чертеже горячей поковки не проставляются допуски на размеры поковки; в примечаниях к чертежу делаются указания о неоговоренных штамповочных уклонах, радиусах закругления и проие надписи, облегчающие чтение чертежа.
Предварительные и заготовительные ручьи рассчитываются в соответствии с методикой [1].
При расчете и конструировании ручьев на КГШП необходимо помнить, что каждый ручей располагается в своей паре вставок. Размеры вставок выбираются в зависимости от размеров ручья и размеров универсального блока на данный кривошипный горячештамповочный пресс.
В соответствии с применяемыми переходами штамповки в штампах на ГКМ могут быть наборные, формовочные, прошивные, пробивные, обрезные и отрезные. Каждый наборной, формовочный и прошивной ручей состоит из двух частей, рабочей части, форма которой соответствует форме поковки и зажимной части, предназначенной для удержания заготовки. Расчет ручьев штампа на ГКМ выполняется в соответствии с методикой [1]. При этом рассчитываются: профиль зажимной части, диаметр и длина вставки, диаметры матриц и пуансонов; наружный диаметр и длина вставок.
3.6. Определение технологического усилия и выбор оборудования
Номинальная масса падающих частей паровоздушного молота определяется по формуле [1] или по номограмме. Затем по ГОСТ 7024-75 выбирается молот с большей ближайшей массой падающих частей и дается его техническая характеристика.
Номинальное усилие кривошипного горячештамповочного пресса и горизонтально-ковочной машины определяется по формуле [1] Затем по каталогу выбирается КГШП или ГКМ с большим ближайшим номинальным усилием и дается их техническая характеристика. Для ГКМ проверяется возможность размещения штампа с требуемым числом ручьев в штамповом пространстве машины. Если штамп по высоте не проходит, то выбирается большая ближайшая машина, а иногда и следующая машина, т.е. через одну ступень.
3.7. Конструирование штампов
3.7.1. Расчет и конструирование молотового штампа
Расчет и конструирование молотового штампа выполняется в следующей последовательности:
- выбирается расположение ручьев в штампе по таблице с. 113 [1]. Штамповочные ручьи размешаются в/близи центра штампа. Заготовительные ручьи располагаются так, чтобы первый заготовительный ручей был расположен с противоположной стороны от сопла для сдува окалины;
- при штамповке поковок с изогнутой осью предусматривается уравновешивание сдвигающих усилий, т. е смещение верхней части штампа относительно нижней Сдвигающие усилия могут быть компенсированы штамповкой сдвоенной поковки; соответствующим выбором поверхности разъема (поворотом поковки): устройством в штампе специальных направляющих (замков);
- определяется толщина стенок штампа, которая зависит от глубины полости ручья, штамповочного уклона и радиуса закругления Толщина стенок определяется с помощью вспомогательной величины Т, которая может быть определена по номограмме (с. 115 [1]) или по формуле [5];
- рассчитываются габаритные размеры штампа, и выбирается штамповочный кубик. Размеры штампа определяются в соответствии с числом, размерами, расположением ручьев и расстоянием между ними. Размеры штамповых кубиков предусмотрены ГОСТ 7831-55. Затем выбранный кубик проверяется на смятие Свободная от ручьев поверхность соударения должна составлять не менее 300 см2 на каждую тонну массы падающих частей молота.
- оформляется чертеж молотового штампа, который содержит вид спереди на штамп в сомкнутом состоянии, вид на нижнюю половину штампа сверху и все необходимые разрезы и сечения ручьев, обеспечивающие изготовление штампа. На штампе изготавливается контрольный угол, который необходим для разметки ручьев и контроля смешения верхней и нижней частей штампа
Размеры на чертеже штампа проставляются от контрольного угла.
Размеры окончательного ручья на чертеже штампа не проставляются, а указывается, что этот ручей следует изготовлять по чертежу горячей поковки, который вычерчивается в правом верхнем углу. На всех остальных ручьях размеры проставляются. Допуски на размеры и чистоту поверхности ручьев на чертеже штампа не указывают, а оговаривают в общих технологических условиях на изготовление молотовых штампов. Размеры стандартных хвостовиков, штамповочных пазов, подъемных отверстий не проставляются, а указываются в примечаниях к чертежу.
3.7.2. Расчет и конструирование штампа на КГШП
Отсутствие ударных нагрузок позволяет использовать на КГШП сборные штампы. Расчет и конструирование штампа на КГШП сводится к выбору универсального блока в зависимости от номинального усилия пресса. В зависимости от выбранного универсального блока определяется закрытая высота вставок. Рассчитываются выталкиватели, конструируется механизм выталкивателя поковки из ручья.
Чертеж штампа на КГШП оформляется так же, как и чертеж молотового штампа. На чертеже штампа должно быть три проекции: вид на нижнюю часть штампа, вид спереди и сбоку в разрезе.
3.7.3.Расчет и конструирование штампа на ГКМ
Расчет и конструирование штампа на ГКМ сводится к выбору блока пуансонов, определенного расстояния между передним торцом блока пуансона и опорной поверхностью блока матриц; габаритных размеров блока матриц и составлению чертежа штампа.
В соответствии с выбранной ГКМ по таб. 3 с.256 [1] принимается конструкция и размеры блока пуансонов и определяется расстояние между передним торцом блока пуансонов и опорной поверхностью блока матриц.
Высота блока матриц определяется как сумма размеров-диаметров вставок и минимально допустимых толщин стенок. Размер блока по длине находится как сумма наибольших длин вставок рабочей части ручья и зажимной части с учетом толщины стенки в долевом направлении. Полученные таким образом значения уточняются в соответствии с характеристикой штампового пространства ГКМ.
Чертеж штампа на ГКМ должен содержать главный вид по линии разъема на подвижную часть штампа и блок пуансонов с набором пуансонов в крайнем заднем положении. Допускается вид сверху на сомкнутые неподвижную и подвижную части штампа. На общем виде штампа должны проставляться габаритные размеры, закрытая высота ГКМ, размеры от базовой поверхности до каждого ручья.
3.8.Определения усилия обрезки облоя, прошивки отверстия
и выбора обрезного пресса
Обрезка облоя и прошивка отверстия в поковках чаше всего производится в горячем состоянии на кривошипных обрезных прессах, которые устанавливаются в одну технологическую линию с основным кузнечным оборудованием. Расчетное усилие обрезки облоя и прошивки отверстия определяется по формуле [1; 9] . Затем по ГОСТ10026-75 выбирается обрезной пресс. Номинальное усилие обрезного пресса обычно значительно превышает расчетное, так как обрезной пресс выбирается в зависимости от номинального усилия КГШП или массы падающих частей молота.
3.9.Конструирование штампов для обрезки облоя и прошивки отверстия
Расчет и конструирование штампов для обрезки облоя и прошивки отверстия начинается с выбора типа штампа. Штамп может быть простого, последовательного и совмещенного действия.
Конструирование штампа производится в следующем порядке: конструирование режущего контура матрицы и определения габаритных размеров матрицы, расчет и конструирование рабочей части пуансона с учетом зазоров между пуансоном и матрицей; определение закрытой высоты штампа; выбор башмака и способов крепления матрицы в башмаке; выбор способа крепления пуансона и съема обрезанного облоя с пуансоном; оформления чертежа штампа.
Штамп для обрезки облоя и прошивки отверстия вычерчиваются в сборе со всеми необходимыми размерами, габаритными и посадочными размерами. В примечании к чертежу указывается; что фигуры в пуансоне и матрице следует выполнять по чертежу поковки и подогнать по специальной отливке из свинца; величина зазора между пуансоном и матрицей; тип и усилие обрезного пресса.
3.10.Разработка организационно-экономической части
Организационно-экономическая часть курсового проекта состоит из схемы организации рабочего места и состава бригады; расчета нормы времени на штамповку; определения технологической себестоимости; составления технологической карты штамповки.
3.10.1 Составление схемы организации рабочего места
Организация рабочего места представляет собой типовое расположение оборудования, на котором выполняется данный технологический процесс, с учетом передачи заготовки от одного оборудования к другому. Затем по запроектированному технологическому процессу и схем» организации рабочего места определяется состав бригады и каждому рабочему бригады присваивается разряд.
3.10.2 Расчет нормы времени на штамповку
Расчет нормы времени на штамповку (штучное время) ведется по наиболее трудоемкой работе, чаще всего это работа штамповщика на основном кузнечном оборудовании.
Штучное время рассчитывается по формуле [13]
,
где Тос - основное (машинное) время, т.е. время работы машины при выполнении данного технологического процесса;
Твс - вспомогательное время, т.е. время затрачиваемое на установку, перенос заготовки из ручья в ручей, сброс в тару;
К - плановый процент затрат рабочего времени на обслуживание рабочего места, отдых и личные надобности. Принимаем 12132% [13].
Для определения основного и вспомогательного времени составляется таблица, в которой по пунктам расписан весь технологический процесс, и для каждого пункта определяется затрачиваемое время. Затем суммируется отдельно основное время и вспомогательное и подставляется в формулу.
Норма выработки определяется как отношение продолжительности смены к штучному времени.
3.10.3.Опредеденне технологической себестоимости поковки
Технологическая себестоимость поковки складывается из следующих элементов стоимости основного материала; зарплаты производственных рабочих; стоимости энергии на работу оборудования, амортизации оборудования, стоимости инструмента (штампов); затраты на текущий ремонт и содержание оборудования.
Методы расчета каждого элемента технологической себестоимости изложены в работе [13].
3.10.4.Составление технологической карты штамповки
Карта технологического процесса горячей штамповки составляется согласно ГОСТ 3.1403-74.
4. Требования к оформлению пояснительной
записке курсового проекта
Пояснительная записи к курсовому проекту должна быть написана от руки черными чернилами на одной стороне листа формата Л4 (210х297 мм) разборчиво и аккуратно. Расстояние между строками должно составлять 1,5÷3мм.
Допускается набор и распечатка пояснительной записки на ЭВМ. Каждый лист пояснительной записки должен иметь рамку. Расстояние от края листа до рамки должно быть: слева — 20 мм; сверху, снизу, справа — 5 мм. Расстояние от рамки формы до границ текста следует оставлять в начале и в конце строк не менее 3 мм. Расстояние от верхней и нижней строки текста до верхней или нижней рамки формы должно быть не менее 10 мм.
Абзацы в тексте начинают отступом, равным 15-17 мм. Написание наименований разделов и подразделов, их расположение в тексте выполнять по ГОСТ 2.105 - 95. Номер раздела, подраздела ставится в начале текста и отделяется от заголовка точкой. В конце заголовка точка не ставится. Не допускается перенос слова в заголовке. Заголовки в тексте выделяются интервалами. Расстояние между заголовком и предыдущим текстом должно быть равно 3+4 межстрочным интервалам (т.е. 10÷12 мм).
Нумерация страниц пояснительной записки должна быть сквозной. Титульный лист считается первой страницей, задание на курсовой проект — второй (номера на этих листах не проставляются). Номера страниц, начиная с третьей, проставляются арабскими цифрами в правом верхнем углу.
Все иллюстрации (схемы, графики, эскизы и др.) в пояснительной записке именуются рисунками. Рисунки нумеруются последовательно а пределах раздела арабскими цифрами. Номер рисунка должен состоять из номера раздела и порядкового номера рисунка, разделенных точкой. Рисунки должны размещаться в записке сразу после ссылки на них в тексте. Каждый рисунок должен иметь подпись, расположенную под рисунком в одну строку с его номером.
Цифровой материал и результаты однотипных расчетов рекомендуется в пояснительной записке проводить в таблицах, по ГОСТ 2.106 68. Таблицы нумеруются последовательно в пределах раздела арабскими цифрами. Номер таблицы должен состоять из номера раздела и порядкового номера таблицы, разделенных точкой. Над правым верхним утлом таблицы размешают надпись "Таблица" с указанием номера. Таблицу следует пометать после первою упоминания о ней в тексте.
Применяемые в расчетах формулы должны быть выделены в отдельную строку. Значения символов и числовых коэффициентов должны приводиться под формулой в той же последовательности, в какой они даны в формуле. Значение каждого символа и численного коэффициента следует писать с новой строки. Первую строку начинают со слова "где", двоеточие после него не ставят.
При написании пояснительной записки необходимо делать ссылки на литературу. При ссылках на литературу следует указывать порядковый номер литературного источника по списку в квадратных скобках (например. [4]). При необходимости сделать ссылку на стандарты, технические условия и другие подобные документы, но приведенные в списке литературы, указывают в круглых скобках обозначение и номер документа (например, ГОСТ 1505 - 89).
5. Требования к оформлению графической части курсового проекта
Графическая часть курсового проекта выполняется на листах чертежной бумаги стандартного формата (А1) в карандаше в соответствии с основными требованиями ЕСКД. В зависимости от соотношения габаритных размеров или размещения проекций формат может быть использован в любом положении, т.е. длинную сторону формата можно ориентировать как по горизонтали, так и по вертикали.
Все чертежи курсового проекта следует выполнять в соответствии с правилами, установленными ГОСТ 2.109-68.
На сборочных чертежах позициями указываются все детали штампа. Номера позиций указывают на полках линий-выносок, располагая их параллельно основной надписи чертежа вне контура изображения и группируя их в колонку или строчку по возможности на одной линии. Линии-выноски проводят от линии видимого контура составных частей.
Основная надпись на чертеже выполняется согласно ГОСТ 2.104-68. Заполнение граф основной надписи производится чертежным шрифтом по ГОСТ 2.304-68 в соответствии со следующими указаниями. В графе 1 указывается Наименование чертежа. В графе 2 указывается обозначение чертежа. Принято обозначение чертежей шифром, состоящим из четырех групп, разделенных черточкой (КП9Я-1301-0812 СБ). Первая группа представляет собой индекс проекта и год выполнения его (например, КП98-курсовой проект 1998 года). Вторая группа представляет собой четырехзначное число, принимаемое согласно МН74-59... M81 - 59 (1301 -штамп молотовой). Третья группа представляет собой номер чертежа: первые два числа - номер студенческой группы, вторые два числа порядковый номер фамилии студента в списке группы (0812 -группа Д-IV-8, 12 - порядковый номер в списке группы). Четвертая группа-шифр вида чертежа. Эта группа обозначается буквами: СБ - сборочный чертеж; Д - плакат (лист переходов штамповки и др.). При обозначении деталей, входящих в состав штампа, вместо четвертой группы вводится через косую черту двузначное число, обозначающее номер позиции детали на сборочном чертеже. В графе 3 основной надписи чертежей деталей указываются материал, из которого изготавливается деталь. В сборочных чертежах 3 графа не заполняется.
Спецификации составляются на штампы в соответствии с ГОСТ 2.108-68. как -самостоятельный конструкторский документ и выполняют на формате А4 с присвоением обозначения Основная надпись на первом листе спецификации выполняется так же, как и на чертежах, с учетом следующего: в графе 1 указывается название чертежа с добавлением слов;» «спецификация»: в графе 2 указывается обозначение чертежа без четвертой группы (шифра вила чертежа) Форма спецификаций выполняется по ГОСТ 2.108 -68 без дополнительных граф. Заполнение формы производится сверху вниз.
6. Организация проектирования и защиты курсовых проектов
Студент выполняет курсовой проект в соответствии с графиком выполнения курсовых проектов, разработанным на кафедре.
Руководитель проекта консультирует студента по принципиальным вопросам и контролирует выполнение курсового проекта. Перед защитой необходимо подписать пояснительную записку и чертежи у руководителя проекта. Подпись руководителя проекта удостоверяет, что курсовой проект выполнен в установленном объеме, соответствует заданию и не содержит грубых ошибок. За принятые решения, оформление чертежей, записки и правильность вычислений отвечает студент.
Защита курсовых проектов производится на заседании комиссии, состоящей из трех преподавателей, утвержденной заведующим кафедрой.
Порядок проведения защиты:
- доклад студента (для доклада 5÷7 мин., в течение которых должен обосновать правильность технических решений, кратко остановиться на технологических разработках, привести данные о технико-экономических показателях);
- ответы на вопросы членов комиссии в соответствии с темой и содержанием курсового проекта.
Проект и его защита оцениваются на заседании комиссии. При оценке проекта комиссия принимает во внимание: качество проработки технических решений; тщательность оформления графической части и соблюдения норм ЕСКД; уровень технических расчетов, полноту и уровень составления пояснительной записки; четкость доклада и правильность ответов на вопросы; планомерность работы над курсовым проектом.
Список рекомендованной литературы
- Ковка и штамповка. Справочник. Под ред. Е. М. Семенова, том I. М., «Машиностроение», 1986.
- Ковка и штамповка. Справочник. Под рсл. Е. М. Семенова, том 2. М., «Машиностроение», 1986.
- Ковка и объемная штамповка стали. Справочник. Под ред. М. В. Сторожсва, том 1. М., «Машиностроение», 1967
- Ковка и объемная штамповка стали. Справочник. Под ред. М. В. Сторожсва. том 2. М., «Машиностроение». 1967
- Охрименко Е. М. Технология кузнечно-штамповочного производства. М., «Машиностроение», 1966.
- Журавлев А. 3. Основы теории штамповки в закрытых штампах М., «Машиностроение», 1973.
- Атрошенко А. П. Технология горячей вальцовки. М. «Машиностроение», 1976.
- Соколов Н Д. Горячая штамповка выдавливанием стальных деталей М.,
«Машиностроение», 1967.
- Атрошенко А П.. Салов С.Н„ Хесин С. М. Современные штампы для об-резкиоблоя Л., «Машиностроения», 1966.
- Тетерин Г. П., Полухин П.И. Основы оптимизации и автоматизации проектирования технологических процессов горячей объемной штамповки. М., «Машиностроение». 1979.
- Бабснко В.А., Бойцов В. В, Волик Ю. П. Объемная штамповка (Атлас схем и текстовых конструкций штампов). М. «Машиностроение», 1982.
- Норнцин И. А., Власов В.И. Автоматизация и механизация технологических
процессов ковки и штамповки. М., «Машиностроение», 1976
- Курганская Н. И. Методические указания по оценке экономической эффективности технологических процессов кузнечно-прессовых цехов в дипломном проекте/Ростов-на-Дону, РИСХМ, 1988
Составитель: к.т.н., доц. Анатолий Иванович Шипулин
Методические указания к выполнению курсового проекта по дисциплине «Технология ковки и объемной штамповки».
Редактор Отечном А. А.
|