Порядок выполнения работы
1.Измерить исходные размеры образца (длину и высоту полосы).
2.Закрепить установку для прокатки на верстаке, измерить диаметр валков.
3.Для заданного размера поперечного сечения заготовки увеличивать зазор между валками
(начиная от 0,5 мм) с шагом 0,5 мм. При этом, задавая заготовку в валки
без дополнительного усилия заталкивания, а также при приводе валков
одностороннем или двустороннем, регистрировать момент устойчивого
захвата заготовки.
4.Пункт 3 выполнять для участков валков : а) полированного; б)
шлифованного; в) рифленого. (Порядок проведения эксперимента указан
цифрами в левом верхнем углу в ячейках таблицы ).
5.После захвата и прокатки заготовки в рифленой части валков последовательно уменьшать
– абсолютное обжатие от 0,4 до 0,1 мм с целью прокатки в шлифованной части валков.
6.Повторить пункт 5, уменьшив
после деформации полосы в шлифованной части валков от 0,3 до 0,1 мм, с
целью прокатки в полированной части валков и выяснения условия захвата
в них.
7.Для определения коэффициента трения в шлифованной части валков
уменьшать от 1,5 мм с шагом 0,1 мм и регистрировать момент захвата.
8.Результаты исследований занести в таблицу и оформить в виде графиков зависимости углов захвата
от 
9.Определить экспериментальные коэффициенты трения для данного
материала образца и валков, а также условий контактного трения.
10.Провести расчеты геометрического угла захвата
, используя зависимость:
где
-
угол захвата валков, рад; r - радиус валков, мм ;
-абсолютное обжатие, мм.
Используя
соотношение
-
коэффициент трения, определить теоретические коэффициенты
трения.
Рассчитать
для случая холодной прокатки в шлифованной части валков
теоретический коэффициент трения по формуле :
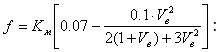
где
-
окружная скорость валков, м/с;
-
поправочный коэффициент, зависящий от условий смазки валков;
=1-
вода, керосин;
=1,35
машинное масло;
=1,55-
без смазки.
11.Сравнить
полученные результаты теоретического расчета коэффициента трения
с экспериментальными данными.
|