Основы конструирования цилиндрических передач
3.1. Зубчатые колёса
Зубчатые колёса изготовляются из легированных сталей с соответствующей термообработкой. Конструкция зубчатых колёс зависит от серийности производства и технологии получения заготовки.
Ориентировочно можно выполнить конструкцию по приведенным рекомендациям для цилиндрических зубчатых колёс. При необходимости от этих рекомендаций можно отступать, но с учётом того, что изложено ниже для каждого из основных элементов конструкции.
Рис.6. Зубчатое колесо
Обод воспринимает нагрузку от зубьев и должен быть достаточно прочным. В то же время он должен быть податливым, чтобы способствовать равномерному распределению нагрузки по длине зуба. Кроме того, он должен быть достаточно жёстким, чтобы обеспечить требуемую точность изготовления зубчатого колеса. С учётом всего этого, рекомендуется выполнять (рис.6)
,
меньшие значения для крупных модулей.
Ступица служит для соединения колеса с валом. Длина её может варьироваться в широких пределах (рис.6):
,
меньшие значения при посадках с гарантированным натягом, большие – при переходных и подвижных, для массового производства предпочтительно .
Минимальное значение длины ступицы определяется при расчёте соответствующего соединения для передачи крутящего момента. Корректируется полученная величина на основании следующего:
-увеличение длины ступицы повышает точность центрирования и устойчивость колеса на валу в плоскости, перпендикулярной оси вращения вала;
-требования к устойчивости возрастают при увеличении диаметра колеса, наличии осевых сил в зацеплении, отсутствии осевого поджатия ступицы к буртику вала, подвижной посадке колеса;
-длинные ступицы увеличивают габариты, массу и усложняют производство.
Наружный диаметр ступицы принимается (рис.6): .
Здесь меньшие значения для соединений с гарантированным натягом и зубчатых соединений, большие – для шпоночных.
Ступица может быть расположена симметрично или несимметрично относительно обода. Это определяется конструктивными или технологическими условиями.
Диск соединяет обод и ступицу. Для цилиндрических колёс рекомендуется принимать (рис.6)  . Меньшие значения рекомендуются для штампованных и литых колёс, большие – для кованных. Иногда в дисках выполняют 4-6 отверстий. Эти отверстия используются при транспортировке и обработке колёс, а при больших размерах и для уменьшения массы. При больших размерах литых колёс диски усиливают рёбрами или заменяют спицами.
Для свободного заполнения нагретым металлом полостей штампа и для освобождения штампа от заготовки она должна иметь уклоны и довольно большие радиусы закруглений. Обычно принимаются уклоны около , а радиусы закруглений (рис.7):
мм,
мм.
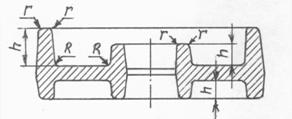
Рис.7. Радиусы закруглений заготовки колеса
Фаски по торцам зубчатого венца  ; фаски по торцам ступицы мм.
В единичном и мелкосерийном производстве зубчатые колёса диаметром до 150 мм изготавливают из круглого проката или цельными из штампованных заготовок без углублений. Зубчатый венец колёс малого диаметра делается как одно целое с валом (такую систему называют вал- шестерня), если толщина обода в месте, ослабленном шпоночным пазом, будет S 2.5m, рис.8, а также при высоких требованиях к точности центрирования.
Валы-шестерни изготовляют обычно из кованных заготовок, так как при изготовлении их из проката может оказаться большим расход металла в стружку.
Форма колёс, получаемых из круглого проката или свободной ковкой, должна быть предельно проста – в виде плоского диска (рис.9 а,б,в). У таких колёс обрабатывают все поверхности. При этом торцевые поверхности ступиц (базовые при монтаже) и торцевые поверхности венцов (базовые при нарезании зубьев) обрабатывают с шероховатостью не ниже 5…2.5 мкм
Зубчатые колёса небольших диаметров (до 200 мм) выполняют в виде дисков со ступицами или без ступиц (см. рис.9 г,д,е,ж).
Колёса средних диаметров получают свободной ковкой, штамповкой в подкладных штампах.
При диаметрах 600мм и более в индивидуальном производстве иногда рационально применить сварную заготовку (рис.10).
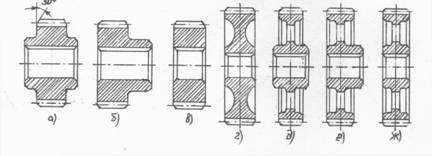
Рис.9. Возможные конструкции зубчатых колёс единичного или
мелкосерийного производств
В серийном и массовом производствах преобладает ковка заготовок колёс диаметром до 600мм в двухсторонних штампах. При больших размерах колеса заготовки изготовляются литьём.
Рис 10. Сварное Колесо
Штамповка отличается высокой производительностью и максимально приближает форму заготовки к форме готовой детали. Многие нерабочие по-
верхности не требуют механической обработки.
3.2. Валы. Некоторые рекомендации по конструированию
Конструкция вала зависит от типа и размера расположенных на нём деталей и способа закрепления этих деталей в окружном и осевом направлениях.
Валы передач, как правило, ступенчатые. В индивидуальном и мелкосерийном производствах такие валы вытачивают из поковок, полученных свободной ковкой, или из круглого проката. В массовом и крупносерийном производствах ступенчатые валы изготовляют из штампованных заготовок, что значительно сокращает объём механической обработки и расход металла.
Существует ряд правил, которые необходимо выполнять при конструировании валов:
- при изготовлении вала из круглой болванки расход металла тем меньше, чем меньше разность диаметров его ступеней, поэтому перепад последовательных диаметров должен назначаться минимальным, при посадках с натягом не более 5%;
- при конструировании валов со спадом диаметров в обе стороны от середины желательно унифицировать диаметры ступеней, выполняемых с одинаковым допуском;
- посадочные ступени вала не должны иметь лишнюю длину посадочной поверхности, поэтому образуются дополнительные перепады диаметров или используется посадка, гарантирующая свободный проход насаживаемой детали до своего посадочного места;
- если посадка с гарантированным натягом сочетается со шпоночным пазом, то необходимо обеспечивать возможность направить паз ступицы на шпонку до начала участка посадки с натягом, для этого можно либо удлинить направляющую фаску, либо заменить направляющую фаску посадкой с зазором, либо удлинить шпонку за ступицу;
- если на валу имеются два шпоночных паза, то они должны быть расположены по одной образующей, при этом желательно, чтобы пазы были одинаковой ширины, поэтому размеры шпонки, установленной на меньшем диаметре, можно принимать для всех шпонок данного вала;
- шпоночные пазы, изготовленные дисковой фрезой, вызывают меньшую концентрацию напряжений, чем изготовленные пальцевой (торцевой) фрезой, кроме того обработка дисковой фрезой более производительна, поэтому при применении дисковых фрез нужно предусматривать выход фрезы, при этом участок выхода может распространяться на упорные бурты или, частично, на шейки валов, предназначенные для размещения подшипников (рис.11);
- значительная концентрация напряжений возникает в местах перехода шлицевых участков к большему диаметру, поэтому в таких местах необходимо выполнять проточку глубиной до внутреннего диаметра шлицев;
- для сокращения номенклатуры инструмента и повышения производительности труда унифицируются размеры фасок, проточек, галтелей на протяжении всего вала.
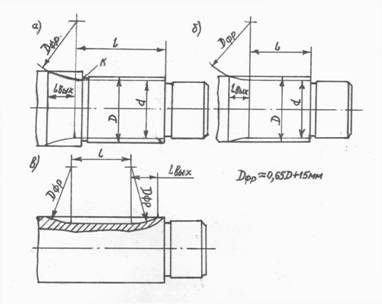
Рис.11. Участки выхода фрезы в конструкциях валов: а,б - с зубьями, в –
с призматическими шпонками
3.3. Подшипниковые узлы
Основными вопросами, которые решаются при проектировании подшипниковых узлов на подшипниках качения является восприятие осевых нагрузок, действующих на вал или ось, и предотвращение осевого смещения вала. При этом следует иметь в виду, что для одних и тех же условий могут быть использованы подшипники разных типов, поэтому нужно учитывать стоимость подшипников, сложность конструкции и опыт эксплуатации узлов, подобных проектируемому.
Нужно решить два вопроса: конструкция элементов крепления подшипников на валах и фиксирование их в корпусе.
Фиксирование подшипников в корпусе осуществляется по одной из схем, представленных на рисунке 12.
С х е м а l. В корпусе жестко закрепляется наружное кольцо одного из подшипников, воспринимающих осевую нагрузку в обоих направлениях- фиксирующая опора, вторая опора выполняется плавающей, т.е. подшипник в ней устанавливается так, что может скользить относительно корпуса при силовых и тепловых деформациях. Схема может применяться при любой длине вала. Недостаток схемы – необходимость использовать подшипник, воспринимающий осевые нагрузки в обоих направлениях и малые радиальная, осевая и угловая жесткости вала.
С х е м а ll. В фиксирующей опоре устанавливаются два подшипника, при регулировке которых сводят к минимуму радиальную и осевую игру вала. Сдвоенный подшипник значительно увеличивает угловую жесткость вала. Недостаток схемы – некоторое усложнение конструкции фиксирующей опоры.
С х е м а lll. Внешние торцы наружных колец подшипников упираются в торцы крышек или других деталей, жестко связанных с неподвижным корпусом редуктора - установка подшипников в распор.
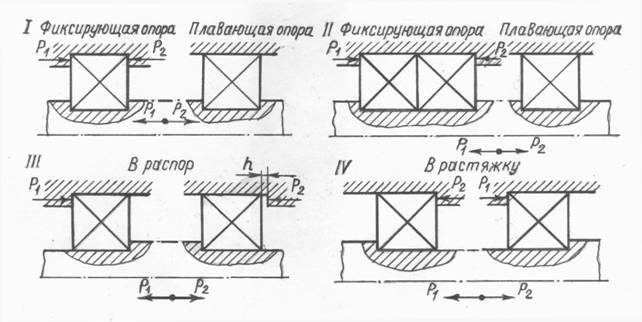
Рис.12. Возможные схемы закрепления подшипников в корпусе
Наиболее часто эта схема применяется для коротких жестких валов, которые должны занимать точное осевое положение. В схеме используются радиально - упорные шариковые или роликовые подшипники с небольшим углом контакта (12 ). Если некоторая осевая игра вала допустима, то можно использовать радиальные, а также сферические шариковые или роликовые подшипники при условии восприятия ими осевых сил или . Обычно расстояние между опорами вала при применении этой схемы не превышает 250…300мм.
С х е м а lV. Это осевая фиксация в растяжку: наружные кольца подшипников своими внутренними торцами упираются в соответствующие торцы корпуса или стакана, установленного в корпус. Установка в растяжку гарантирует, что непроизойдёт заклинивание подшипников вследствие температурного удлинения вала. Однако такая схема конструктивно сложна и поэтому применятся сравнительно редко.
Основные принципы конструирования подшипниковых узлов следующие:
- посадочные места подшипников каждого из валов должны быть соосны; это достигается расточкой напроход, а если возможно, шлифовкой напроход гнёзд под подшипники для каждого вала; т.е. в расточке корпуса не должно быть буртиков;
- стаканы и переходные втулки следует применять только тогда, когда конструктивное решение без них невозможно; таким образом, улучшается соосность и отвод тепла от подшипника;
- конструкция должна обеспечивать возможность монтажа - демонтажа подшипника и узла в целом;
- вращающееся кольцо должно быть жестко связано с соответствующей деталью небольшим натягом; для невращающихся колец натяг заменяется небольшим зазором; посадки с большими натягами допустимы лишь при очень больших и особенно при ударных нагрузках;
- плавающий подшипник жёстко фиксируется своим вращающимся кольцом, а второе кольцо устанавливается по посадке, позволяющей ему с малым сопротивлением перемещаться при тепловых деформациях вала или корпуса;
- фиксируется, как правило, более нагруженный подшипник;
- отклонения от перпендикулярности заплечиков вала и корпуса к оси вращения должно быть минимальным: в зависимости от точности узла 2…20 мкм, причём для крупных подшипников допустимы несколько большие отклонения;
- необходимо исключать регулировку осевого смещения подшипников резьбовыми деталями, так как даже при резьбе с малым шагом перекос упорного торца неизбежен;
- осевое крепление концевых подшипников на валах необходимо только при значительных и особенно при ударных нагрузках;
- при небольших нагрузках допустимо для осевой фиксации использование пружинных колец, вставляемых в проточки вала или корпуса;
- жидкие смазки заливаются в корпус до уровня тела качения, расположенного в подшипнике ниже всех других тел качения;
- пластичные смазочные материалы должны закладываться в объёмах не более 1/3 свободного пространства, не занятого подшипником; зазор в маслоотбойных шайбах относительно корпусного гнезда не должен превышать 0.3…1.0 мм ( в зависимости от точности изготовления и сборки ).
|