Краткая теория.
При соблюдении необходимых требований к чистоте гидросистемы удаётся повысить надёжность гидроприводов и уменьшить эксплуатационные расходы на 50%. Повышение тонкости фильтрации рабочей жидкости в гидросистеме с 25 до 5 мкм увеличивает ресурс насосов в 10 раз и гидроаппаратуры - в 5-7 раз.
Однако фильтрация (или другие средства очистки) обеспечивает наибольший эффект лишь при комплексном соблюдении требований по типам применяемых масел, правилам их хранения и транспортирования, качеству очистки и гермети-зации гидросистем, регламентам их эксплуатации.
Для очистки рабочих жидкостей используют механические фильтры, а также различные методы очистки в силовых полях.
Гравитационная очистка основывается на законе всемирного тяготения - на твёрдые частицы (загрязнения) находящиеся в рабочей жидкости действует сила тяжести. Под действием силы тяжести твёрдые частицы осаждаются на дно ёмко-сти, откуда после слива рабочей жидкости они удаляются. Относительная ско-рость, а следовательно и время очистки, при свободном падении загрязняющей частицы в рабочей жидкости гидросистем зависит от размера, формы и плотности частицы, а также плотности и вязкости рабочей жидкости гидросистемы.
Магнитная очистка. При длительной работе гидропривода происходит износ (выкрашивание) в подвижных соединениях оборудования. При применении маг-нитной очистки из рабочей жидкости гидросистем удаляются мелкие ферромаг-нитные частицы размером 0,5-5 мкм, наличие которых приводит к загрязнению фильтров тонкой очистки (особенно бумажных), значительно снижая срок их службы. Кроме того, такие частицы являются активным катализатором при окис-лении рабочих жидкостей. Помимо ферромагнитных частиц, магнитные фильтры частично улавливают органические засорения, абразивные частицы, песок и дру-гие засорения. Этому способствует эффект электризации немагнитных частиц.
В магнитном сепараторе очистка рабочей жидкости от взвешенных в ней ферромагнитных частиц происходит под действием магнитного поля. Основным рабочим (активным) элементом сепаратора является постоянный магнит. Все маг-нитные сепараторы можно разделить на две группы: сепараторы, в которых отде-ление ферромагнитных частиц из рабочей жидкости и их концентрация осуществ-ляются непосредственно постоянным магнитом (или группой магнитов); сепара-торы, в которых отделителями и концентраторами частиц служат специальные ферромагнитные элементы, помещенные в силовом поле постоянного магнита (или группы магнитов).
Наиболее простыми сепараторами первой группы являются магнитные уло-вители и магнитные патроны. Уловитель (ГОСТ 17429—72) или магнитная пробка состоит из корпуса 1 (рис. 1), изготовляемого из алюминиевого сплава, и постоянного магнита 2.
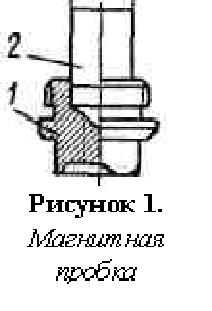
Допускается изготовление корпуса и из других немагнитных материалов. В корпусе магнит крепится клеем из эпоксидной смолы или развальцовкой верхнего буртика корпуса. Магнитные уловители устанав-ливают в сливных трубопроводах, отстойниках и резервуарах гидравлических, смазочных систем машин и систем подачи охлаждающих жидкостей металлоре-жущих станков. Скорость потока рабочей жидкости в зоне установки уловителей не должна превышать 0,01 м/мин. Для магнитных уловителей в технических дан-ных указывается масса магнитных частиц, задерживаемых магнитом, и мини-мальный размер частиц, которые могут задерживаться уловителем.
Магнитный патрон (рис. 2) состоит из нескольких постоянных магнитов 2, скрепленных стяжкой 3 и помещенных в герметичный корпус 1.
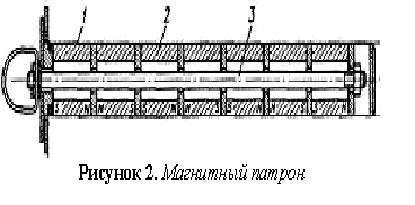
Магнитные патроны, так же как и уловители, погружают в резервуары гидравлических и сма-зочных систем. Они задерживают ферромагнитные частицы общей массой 0,03—0,4 кг в радиусе действия 20— 65 мм. Для большей эффективности рекомендуется очищать патроны через каждые 500 ч работы и помещать в зону, находящуюся по пути движения рабочей жидкости от сливной магистрали к насосу.
Электростатическая очистка. Рабочие жидкости, применяемые в гидросисте-мах, являются диэлектрическими жидкостями. Поэтому их можно очищать от за-грязняющих частиц в электростатическом поле, используя силы электрического притяжения. Загрязняющие частицы, перемещаясь вместе с жидкостью, всё время трутся о жидкость и под действием этого трения получают отрицательный или положительный заряд. Если жидкость пропустить между двумя электродами, то отрицательно заряженные частицы будут притянуты к катоду, а положительно за-ряженные - к аноду. Произойдёт электростатическая очистка рабочей жидкости.
Центробежная очистка. Процесс разделения жидких неоднородных систем в роторах под действием центробежных сил называется центрифугированием. Цен-трифугирование, при котором твёрдая дисперсионная фаза осаждается на внут-ренней поверхности сплошного ротора центрифуги, называется центробежным осаждением.
Центробежная очистка рабочих жидкостей имеет ряд преимуществ:
1. нет необходимости в процессе эксплуатации заменять отдельные узлы, центри-фуги, как, например, в бумажных или других фильтрах тонкой очистки;
2. в процессе центрифугирования из рабочей жидкости в первую очередь осажда-ются загрязняющие частицы, имеющие высокую плотность;
3. пропускная способность центрифуги по мере накопления в ней загрязнений практически не изменяется;
4. при центробежном осаждении по составу загрязнений можно судить о состоя-нии износа отдельных узлов и деталей гидравлического оборудования;
5. из рабочих жидкостей гидросистем в процессе центрифугирования не удаляют-ся активные присадки.
Для оценки эффективности работы центрифуги и скорости осаждения частиц в центробежном поле большое значение имеет так называемый фактор разделе-ния. Фактор разделения представляет собой отношение ускорений центробежного и гравитационного полей:
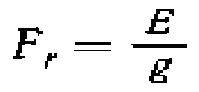
где Е —ускорение центробежной силы; g —ускорение силы тяжести.
В современных ультрацентрифугах фактор разделения достигает 250 000, в обычных промышленных фильтрующих центрифугах не превосходит 1500. По принятой в литературе классификации процессы центрифугирования в сплошных роторах разделяются по количеству твердой фазы в суспензии на центрифугаль-ное осветление и отстойное центрифугирование.
При центрифугальном осветлении объемная концентрация твердой фазы в суспензии незначительна и обычно не превышает нескольких процентов. Центри-фугальное осветление применяется обычно для обработки тонких и коллоидных суспензий и осуществляется в высокоскоростных центрифугах двумя способами: тонкослойным и толстослойным.
Тонкослойное центрифугальное осветление отличается от толстослойного тем, что в роторе центрифуги поток жидкости делится, с помощью пакета кониче-ских тарелок, на слои толщиной не больше 1 мм. Это сокращает продолжитель-ность осаждения частиц и повышает эффективность процесса.
Отстойное центрифугирование является более грубым процессом разделения суспензий, содержащих значительное количество твердой фазы. Для этого требу-ются роторы большой емкости или приспособления для удаления осадка во время работы центрифуги.
По виду привода ротора центрифуги подразделяются на центрифуги с актив-ным и гидрореактивным приводом. В центрифугах с активным приводом враще-ние ротора осуществляется внешним (как правило электрическим) двигателем.
В центрифугах с гидрореактивным приводом (рис. 3) жидкость, поступает на очистку по каналу 1, из которого через боковые отверстия поступает под стакан 2.
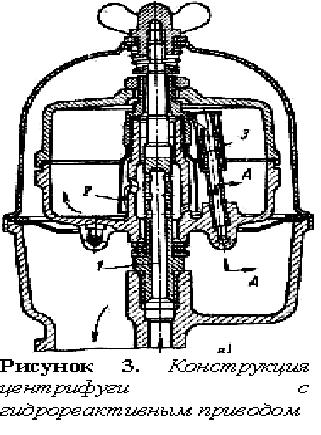
Заполнив внутреннюю полость ротора, она попадает в наклонную трубку 3 и че-рез неё к двум противоположно расположенным соплам 4 реактивного привода. Выходя из сопел под давлением, создаёт вращающий момент.
В испытательных станциях, на специализированных заводах, а также в ряде автоматизированных производств применяют централизованные системы маслоснабжения от единой станции. Этот метод обеспечивает высококачественную очистку масла и упрощает техническое обслуживание. Однако его применение связано с большими капиталовложениями на прокладку трубопроводов подачи и слива масла; этот метод неприемлем в случае, если для станков требуются различные типы масла.
В связи с этим для очистки масла от загрязнений применяют станции очист-ки гидросистем типа СОГ.
Станция очистки гидросистем типа СОГ состоит из корпуса 5 (рис.4), встро-енного 2 и основного 11 баков, центрифуги-насоса 13 типа ЦН, кранов 8, 10 и 14, приёмного штуцера 6, теплообменника 4, всасывающего 3 и напорного 7 шлангов.
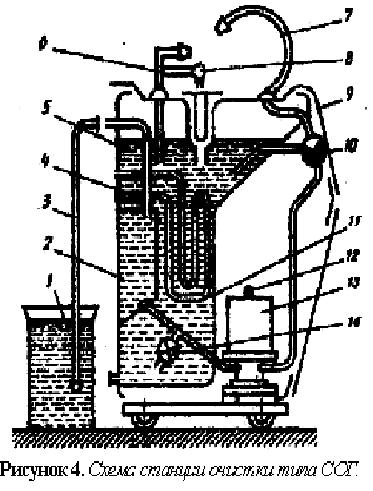
В зависимости от положения крана 14 центрифуга-насос всасывает масло из основного бака 11 или внешнего резервуара 1 и подаёт очищенное масло по шлангу 7 в гидросистему или (после поворота крана 10) возвращает в бак 11. Кран 8 служит для отбора проб масла.
На крышке 9 могут устанавливаться промываемые гидроагрегаты, т.е. аппараты, подвергшиеся ремонту или имеющие засорения. После промывки рабочая жидкость стекает по крышке в основной бак, откуда закачивается насосом-центрифугой и очищается.
Схемы потоков рабочей жидкости при различных режимах работы СОГ-903А:
1) Многократная очистка рабочей жидкости, залитой в основной бак 11: бак 11 - кран 14 (открыт) - насос-центрифуга 13 - кран 10 («Бак») - бак 11;
2) Закачивание (очистка) рабочей жидкости из основного бака 11 во внешний ре-зервуар 1: бак 11- кран 14 (открыт) - насос-центрифуга 13 - кран 10 («Потреби-тель») - дополнительный резервуар 1;
Закачивание (очистка) рабочей жидкости из внешнего резервуара 1 в основной бак 11: внешний резервуар 1 - бак 2 - кран 14 (закрыт) - насос-центрифуга 13 - кран 10 («Бак»)-бак 11;
Очистка рабочей жидкости без заполнения основного бака 11: внешний резер-вуар 1 - бак 2 - кран 14 (закрыт) - насос-центрифуга 13 - кран 10 («Потреби-тель») - внешний резервуар 1.
|