4.9. Вибрационные механохимические покрытия
Вибрационные механохимические покрытия получили распространение в основном, как антифрикционные, защитные и защитно-декоративные. Эффективность процесса нанесения вибрационных механохимических покрытий определяется следующими факторами: типом оборудования (рис 4.27), амплитудой и частотой колебаний, материалом и формой рабочей среды и детали, взаимодействием химических растворов.
Сущность метода заключается в том , что изделия вместе с рабочей средой, порошком металла или активаторами и водой загружают в вибрационную установку (зависит от вида покрытия). Под действием вибрации наносимое покрытие или вбивается в поверхность изделий или формируется за счет химической реакции на поверхности металла. Равномерное распределение покрытия на поверхности изделий обеспечивается активаторами, смесь состоящую из кислотных реагентов, противопенных и диспергирующих добавок поверхностно-активных веществ. Совершая вращательно-колебательные движения рабочая среда вызывает пластическую деформацию и активацию поверхностных слоев металла тем самым дает возможность формироваться покрытию. При этом, в зависимости от применяемых усилий, наблюдается преобладание или механической составляющей процесса, или химической, или равное воздействие обоих на съем окислов металла, сглаживание микронеровностей, улучшение физико-механических свойств покрытия (микротвердость, остаточные напряжения, структура), коррозионную стойкость и т д..
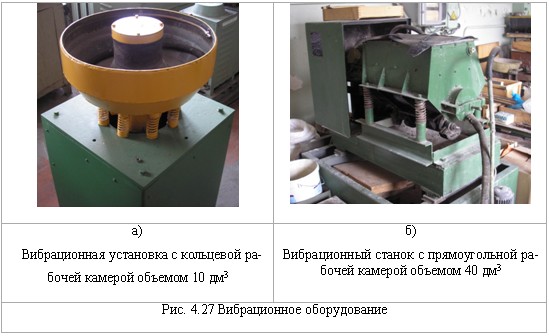
Вибрационные механохимические покрытия (ВиМХП) имеют следующие преимущества перед гальваническими:
- одновременная механическая обработка поверхности, хороший внешний вид покрытия;
- повышенная коррозионная стойкость;
- простота конструкции оборудования вследствие отсутствия токоподводов;
- не происходит наводороживания изделий;
- возможны покрытия «трудно покрываемых» металлов;
- возможно соосождения различных металлов;
- использование малого количества электролита;
- менее жесткие требования к предварительной подготовке поверхности.
Для более предметного понимания процессов рассмотрим схемы модели образования ВиМХП:
Вибрационное механохимическое антифрикционное твердосмазочное покрытие на основе дисульфида молибдена
Порошкообразное неметаллическое антифрикционное вибрационное механохимическое покрытие наносят на поверхность деталей подшипников и других пар трения. Покрытие наносят на установках с прямоугольной рабочей камерой (рис 4.27, б) при режиме обработки амплитуда колебаний 2-3 мм и частоту колебаний 24-36 Гц. В рабочую камеру загружают мелкодисперсный порошок дисульфида молибдена, детали, рабочую среду (металлические шары) нанесение покрытия происходит в течение 1 часа. Схематично процесс нанесения представлен на рис 4.28
- Механический контакт и адсорбция частиц МоS2. В момент приложения внешней нагрузки, благодаря силе соударения шара с поверхностного обрабатываемого материала, происходит упругая, пластическая и упруго-пластическая деформация в зоне контакта. За счет сближения наносимого покрытия с деталью происходит адсорбции частиц на поверхности металла (рис 4.28 а).
- Активация поверхностного слоя металла(рис 4.28 а). Активация поверхности осуществляется в результате пластического деформирования и увеличения плотности дислокаций, разрушения окислых пленок и образования участков поверхности, увеличения площади поверхности.
- Образование граничного слоя. Этот этап осуществляется вследствие размельчения кристаллов МоS2 разрушения ими окислых пленок во впадинах микрорельефа, внедрения частиц порошка и адсорбции их к поверхностному слою активизирующего металла(рис 4.28 б).
- Образование слоя смазки. Этот этап характеризуется утолщением частиц нанесенного покрытия, размельчением кристаллов, слипанием их друг с другом, образованием сплошного слоя смазки (рис 4.28 б).
- формирование поверхностного слоя покрытия. В результате скольжения частиц рабочей среды относительно образуемой поверхности частиц порошка ориентируется базовыми плоскостями параллельно поверхности трения(рис 4.28 в).
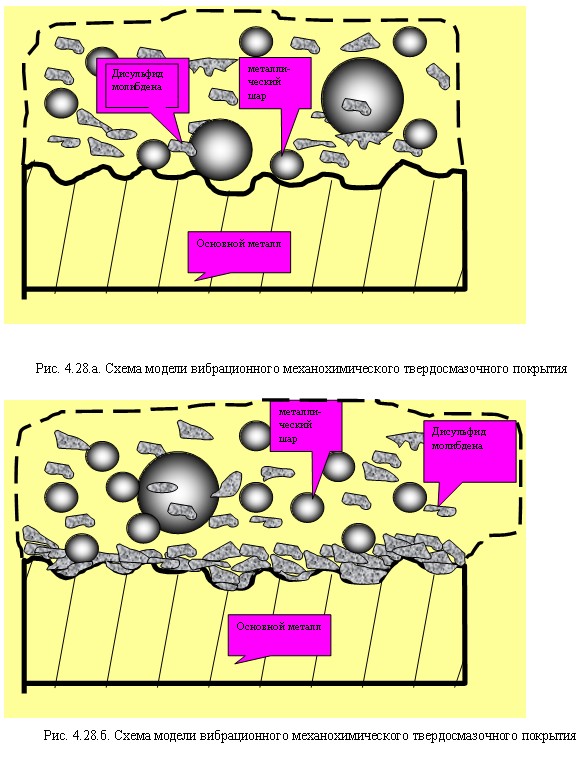
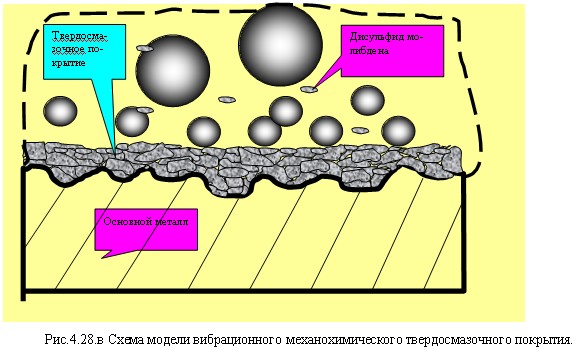
Рис.4.28.в Схема модели вибрационного механохимического твердосмазочного покрытия.
Вибрационное механохимическое цинкование
Порошкообразное металлическое вибрационное механохимическое защитное покрытие наносят на поверхность деталей (крепежные, колодки, балансиры и т.д.) Покрытие наносят на установках с прямоугольной рабочей камерой (рис 4.27, б) и с кольцевой рабочей камерой (рис 4.27, а) при режиме обработки амплитуда колебаний 1-3 мм и частоту колебаний 24-36 Гц. В рабочую камеру загружают мелкодисперсный порошок цинка, предварительно подготовленные детали, заливают водный раствор хлористого цинка, рабочую среду (фарфоровые шары) нанесение покрытия происходит в течении 45-120 мин. Схематично процесс нанесения представлен на (рис 4.29).
1.Механохимический контакт деталей с рабочей средой. В момент приложения нагрузки вследствие соударения шаров с поверхностью обрабатываемого материала происходит пластическая деформация в зоне контакта. На поверхности металла адсорбируется ионы, молекулы в растворе (рис 4. 29 а).
2.Активация и огретый поверхностного слоя металла. Активация поверхности происходит в результате пластического деформирования, увеличилось иллюстрация дислокаций и активных центров, образуя ювенальных участников поверхности. Одновременно осуществляющих активацию ионов и молекул раствора (Zn++, Zn) их адсорбция на поверхности(рис 4. 29 а).
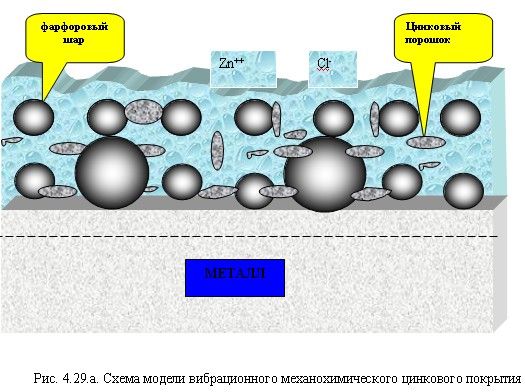
В результате динамического воздействия и перемешивания рабочей среды происходит подача свежего раствора и отвод отработавшего. Вместе с отработавшим раствором с поверхности металла учащаются жировые загрязнения, таким образом, осуществляется совмещение процессов очистки от загрязнений и улучшение качества поверхности слоя.
3.Образ цинкового покрытия. Участники поверхности образуют, место с высокой активностью адсорбирует ион Zn++, который, разряжаясь, осаждается в виде цинкового покрытия.
Zn+++2e=Zn
Вибрирующая среда позволит к обрабатывающей поверхности также Znпорошок, который адсорбируется под действием механических усилий, запрещается на поверхности металла (рис 4. 29 б).
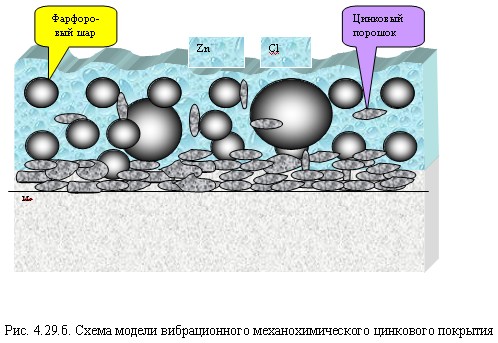
4.Рост Znпокрытия. Под влиянием виброусилий и активации составляющих процесса цинкования происходит формирование, и рост Znпокрытие растет линейно в зависимости от времени обзора (рис 4. 29 б).
5.Формирование повторного слоя под влиянием виброобработки нарушается, часть пленки подвергается формированию, сминаются и разрушаются гребешки, выставив, удаляются мелкие неровности, в результате снижается шероховатость поверхности и увеличится блеск обрабатываемой поверхности(рис 4. 29 в).
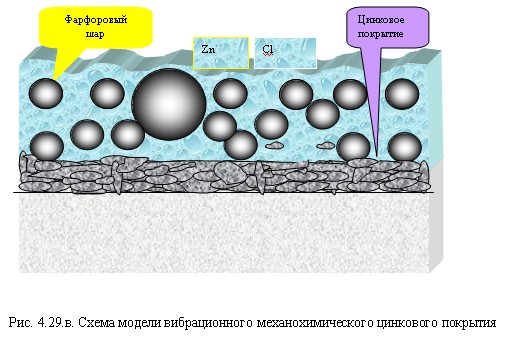
Вибрационное механохимическое оксидирование
Вибрационное механохимическое защитно-декоративное покрытие наносят на поверхность деталей (крепежные, заклепки, кронштейны и т.д.) Покрытие наносят на установках с прямоугольной рабочей камерой (рис 4.27, б) и с кольцевой рабочей камерой (рис 4.27, а) при режиме обработки амплитуда колебаний 1 мм и частоту колебаний 16-24 Гц. В рабочую камеру загружают, предварительно подготовленные детали, заливают оксидирующий раствор, рабочую среду (полиэтиленовые шары) нанесение покрытия происходит в течении 10-20 мин. Схематично процесс нанесения представлен на (рис 4.30).
1. Механический контакт деталей с рабочей средой.
В момент приложения нагрузки, вследствие соударения шаров с поверхностью обрабатываемого материала, происходит пластическая деформация в зоне контакта(рис. 4.30.а.). На поверхности металла адсорбируется оксидирующий раствор (ионы, молекулы).
2. Активация и очистка поверхностного слоя металла (рис. 4.30.б.)
Активация поверхности происходит в результате пластического деформирования, увеличения плотности дислокаций и образования активных центров, разрушения естественной оксидной пленки и образования ювинильных участков поверхности. Одновременно осуществляется активация ионов раствора ( ) их адсорбция на поверхности металла и взаимодействие с жировыми загрязнениями и окислами.
В результате динамического воздействия и перемещения рабочей среды происходит подача свежего оксидирующего раствора к поверхности металла и отвод отработавшего, ослабленного после реакции. Вместе с отработавшим раствором с поверхности металла удаляются окислы, жировые загрязнения и продукты реакции.
Таким образом, осуществляется совмещение процессов очистки от загрязнений и окислов и подготовки поверхности под оксидирование, с улучшением качества поверхностного слоя.
3. Образование оксидной пленки(рис. 4.30.в.).
Участки поверхности обрабатываемого металла с высокой активностью адсорбируют гидроксил-ион , взаимодействуют с ним с образованием гидроксида алюминия по реакции:

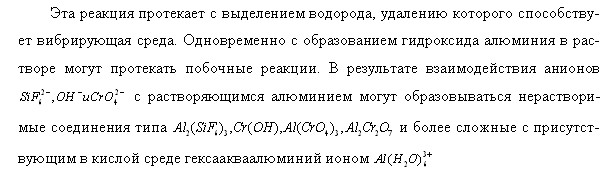
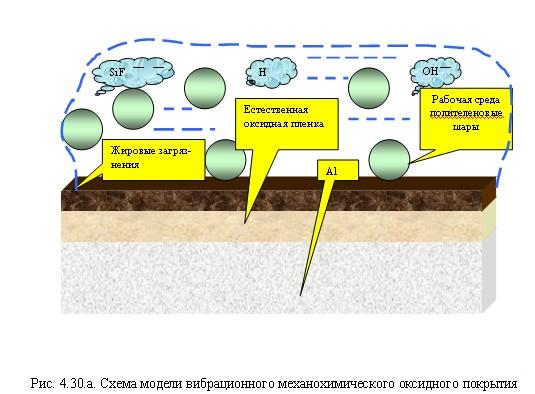
4. Рост оксидной пленки (рис. 4.30.г.)
Под влиянием виброусилий и активации всех составляющих процесса оксидирования происходит формирование и рост оксидной пленки.
Образовавшаяся на поверхности металла оксидная пленка увеличивается за счет самого металла. Постоянный приток свежего раствора к поверхности металла через поры в оксидной пленке обеспечивает взаимодействие металла с раствором и рост пленки.
Разрыхление ее обеспечивается вибрацией и притоком оксидирующего раствора к обрабатываемой поверхности.
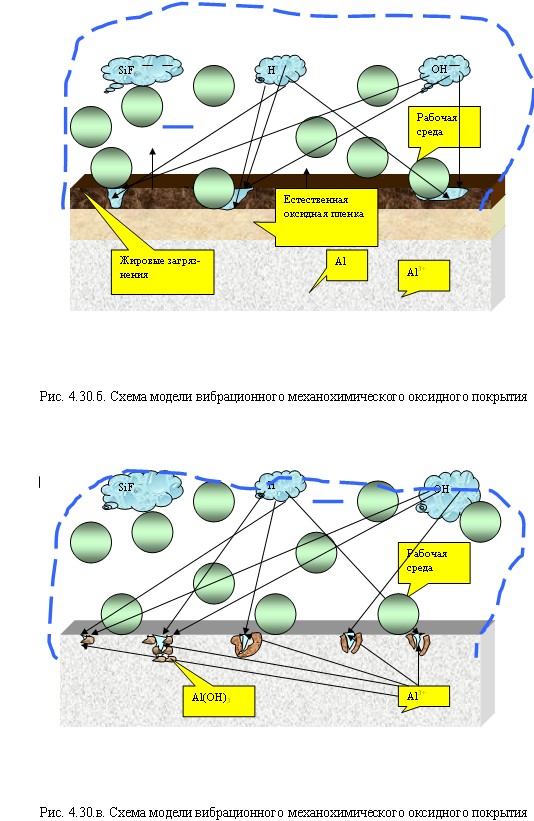
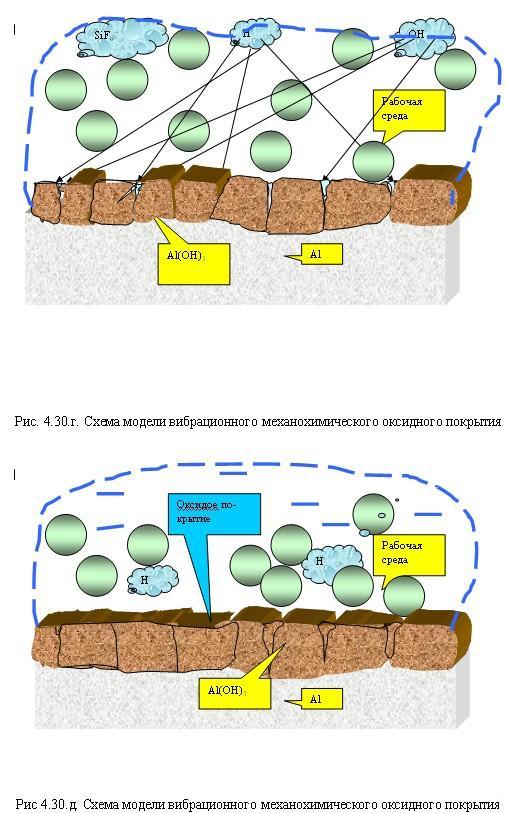
5. Формирование поверхностного слоя покрытия (рис. 4.30.д.).
Под влиянием виброобработки наружная часть пленки подвергается деформированию, сминаются и разрушаются гребешки выступов, удаляются мелкие неровности, в результате снижается шероховатость поверхности в увеличивается блеск обрабатываемой поверхности. Блеск усиливается под влиянием полирующего действия полиэтиленовых шаров.
|