4.8. Нанесение покрытий с использованием высококонцентрированных потоков энергии
Среди методов нанесения защитных покрытий, основанных на воздействии на поверхность ренодетали потоков частиц и квантов с высокой энергией, большое внимание привлекают вакуумные ионно-плазменные методы. Характерной их чертой является прямое преобразование эклектической энергии в энергию технологического воздействия, основанной на структурно-фазовых превращениях в осажденном на поверхности конденсате или в самом поверхностном слое ренодетали, помещенной в вакуумную камеру.
Основным достоинством данных методов является возможность создания весьма высокого уровня физико-механических свойств материалов в тонких поверхностных слоях, нанесение плотных покрытий из тугоплавких химических соединений, а также алмазоподобных, которые невозможно получить традиционными методами.
Кроме того, эти методы позволяют: обеспечивать высокую адгезию покрытия к подложке; равномерность покрытия по толщине на большой площади; варьировать состав покрытия в широком диапазоне, в пределах одного технологического цикла; получить низкую шероховатость поверхности покрытия; экологическую чистоту производственного цикла. В настоящее время разработано большое число очень высоко эффективных методов нанесения защитных покрытий и модифицирования поверхностных слоев[6]
Методы вакуумной ионно-плазменной технологии:
1. Модифицирование поверхностных слоев:
- ионно-диффузионное насыщение (ионное азотирование, науглероживание, борироване и др.);
- ионное (плазменное) травление (очистка);
- ионная имплантация (внедрение);
- отжиг в тлеющем разряде;
2. Нанесение покрытий:
- полимеризация в тлеющем разряде;
- ионное осаждение (триодной распылительной системе, диодной распылительной системе, с использованием разряда в полом катоде);
- электродуговое испарение;
- ионно-кластерный метод;
- катодное распыление (на постоянном токе, высокочастотное);
- химическое осаждение в плазме тлеющего разряда.
Современные вакуумные ионно-плазменные методы упрочнения (модифицирование) поверхностей деталей машин включают следующие этапы:
- генерацию (образование) корпускулярного потока вещества;
- его активизацию, ускорение и фокусировку;
- конденсацию и внедрение в поверхность деталей (подложек).
Генерация: корпускулярного потока вещества возможна его испарением (сублимацией) и распылением. Испарение: переход конденсированной фазы в пар осуществляется в результате подводок тепловой энергии к испаряемому веществу. Твердые вещества обычно при нагревании расплавляются, а затем переходят в газообразное состояние. Некоторые вещества переходят в газообразное состояние минуя жидкую фазу. Такой процесс называется сублимацией.
Нагрев испаряемого вещества может осуществляться:
- за счет выделения джоулева тепла при прохождении электрического тока через испаряемый материал или через испаритель;
- в результате бомбардировки поверхности метала ускоренным потоком электронов (электронно-лучевой нагрев) или квантами электромагнитного излучения (лазерный нагрев);
- высокочастотным электрическим магнитным полем (индукционный нагрев);
- электрической дугой.
Выбор способа нагрева и вид испарения зависят от природы испаряемого материала, его исходной формы (гранулы, порошок, проволока), требуемой скорости испарения, постоянства во времени и т.д.
Наибольшее распространение получил нагрев при помощи электронной бомбардировки, что позволяет достигать температуры 4000 градусов Цельсия и высокой плотности энергии в луче.
Электронно-лучевой способ нагрева состоит в, что на реноизделие направляют поток электронов от катода и ускоренных электрическим полем до энергии 5…25 кэВ. Поток электронов (электронный луч) получают с помощью электронно-лучевых пушек.
В результате образования активированного корпускулярного потока в контакт с подложкой метала ренодетали входят нейтральные частицы (возбужденные и невозбужденные) с высокой энергией и ионы. Процесс взаимодействия такого сложного по составу потока с поверхностью метала сводится к протеканию взаимосвязанных физических явлений: конденсации, внедрение и распыление.
Ионное распыление
Ионные распылители разделяют на две группы:
- плазменные, в которых мишень находится в газоразрядной плазме, создаваемой с помощью тлеющего, дугового и высокочастотного разряда. Распыление происходит в результате бомбардировки мишени ионами, извлекаемыми из плазмы;
- автономные источники без фокусировки и с фокусировкой ионных пучков, бомбардирующих мишень(ренозаготовку)
В наиболее простом случае система распыления состоит из двух электродов, помещенных в вакуумную камеру (рис.4.25)
Распыляемую мишень из наносимого материала располагают на катоде. На другом электроде на расстоянии в несколько сантиметров от катода, устанавливают детали (подложки).
Камеру вакуумируют, наполняют рабочим газом (чаще всего аргоном) до давления 1,33Па, зажигают газоразрядную плазму и бомбардировкой ионами производят очистку реноизделия от поверхностных загрязнений, далее отрицательный потенциал прикладывают к мишени и распыляют ее. Распыляемые частицы движутся через плазму разряда, осаждаются на деталях и образуют покрытие. Большая часть энергии ионов, бомбардирующих мишень (до 25%) переходит в тепло, которое отводится водой, охлаждающей катод.
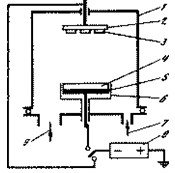
Рис. 4.25. Принципиальная система распыления:
1 – камера; 2 – подложкодержатель; 3 – детали (подложки); 4- мишень; 5- катод; 6- экран; 7 – подвод рабочего газа; 8 – источник питания; 9 – откачка.
Достоинства способа: возможность получения покрытий из тугоплавких металлов, сплавов и химических соединений.
Магнетронное распыление. Нанесение покрытий в вакууме с помощью магнетронных систем заключается в распылении твердой мишени напыляемого материала ионами инертного газа, образующимися в плазме аномального тлеющего разряда при наложении на него магнитного поля, силовые линии которого ортогонально пересекают силовые линии магнитного поля (рис.4.26) .
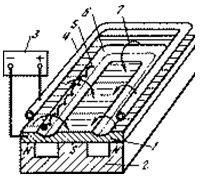
Рис.4.26. Схема магнетронной распылительной системы с плоской мишенью:
1- катод (мишень); 2- магнитная система; 3- источник питания; 4- анод; 5- траектория движения электрона; 6- зона распыления; 7- силовая линия магнитного поля.
Основными элементами магнетрона является катод( мишень), анод и магнитная система. Cиловые линии магнитного поля замыкаются между полюсами магнитной системы. При подаче постоянного напряжения между мишенью (отрицательный потенциал) и анодом (положительный потенциал) возникает неоднородное электрическое поле и возбуждается тлеющий разряд. Наличие замкнутого магнитного поля к распыляемой поверхности мишени позволяет локализовать плазму разряда непосредственно у мишени. Эмитированные с катода под действием ионной бомбардировки электроны захватываются магнитным полем, и им сообщается сложное циклоидальное движение по замкнутым траекториям у поверхностей мишени. Электроны оказываются как бы в ловушке, создаваемой с одной стороны магнитным полем, возвращающим их на катод, а с другой стороны – поверхностью мишени, их отталкивающей. Электрон циркулирует в этой ловушке до тех пор, пока не произойдет несколько ионизирующих столкновений с атомами рабочего газа, в результате которых он потеряет полученную от электрического поля энергию. Таким образом, большая часть энергии электрона, прежде чем он попадает на анод, используется на ионизацию и возбуждение, что значительно увеличивает эффективность процесса ионизации и приводит к возрастанию концентрации положительных ионов у поверхности мишени и росту скорости осаждения покрытия.
Ионное осаждение покрытий. Этот способ нашел в реновационном производстве они нашли применение для получения износостойких и коррозионностойких покрытий как из чистых металлов, так и из соединений.
К методам ионного осаждения покрытий относят методы, в которых осаждаемая пленка подвергается интенсивному воздействию ионного компонента корпускулярного потока, обеспечивающего изменения в структуре и свойствах, так и самого покрытия. Такой результат возможен либо при высокой степени ионизации корпускулярного потока (газообразного или металлического) осаждаемого вещества, либо при высокой энергии ионного компонента корпускулярного потока.
По типу источника генерации металлического компонента потока различают ионно-термические системы распыления и холодные системы. В первых системах перевод переносимого материала из твердого в парообразное состояние осуществляется в результате термического нагрева, во- втором- распылением с поверхности интегрально холодной мишени (катода).
Эти методы позволяют получать покрытия с высокими служебными характеристиками кристаллизации пленок и их свойствами.
Ионно-диффузионное насыщение. Этот метод наиболее широко применяется при азотировании сталей и металлов. Преимущества перед печами обычного газового азотирования: сокращение длительности цикла в 3…5 раз; уменьшение деформации восстанавливаемых деталей в 3…5 раз; возможность проведения регулируемых процессов азотирования с получением слоев с заданным составом и структурой; возможность уменьшения температуры процесса азотирования до 350…400 0С, что позволяет избежать разупрочнения материалы сердцевины реноизделий; уменьшение хрупкости слоя и повышение его служебных характеристик; простота защиты отдельных участков ренодеталей от азотирования; устранение опасности взрыва печи; снижение удельных расходов электрической энергии в 1,5…2 раза и рабочего газа в 30…50 раз; улучшения условий труда термистов.
Система ионного насыщения представляет собой вакуумную камеру, в электрическом плане реализующую двухэлектродную схему: катод-электрод с деталями; второй электрод (анод)- заземленный корпус вакуумной камеры. Для проведения процесса ионам насыщения в вакуумную камеру подается легирующий материал (элемент или химическое соединение) в газообразном (парообразном) состоянии, а к ренодеталям прикладывается отрицательный потенциал- 300….1000 В. Поверхность реноизделия бомбардируется положительными ионами легирующего элемента из газоразрядной плазмы, что позволяет значительно сократить длительность процесса насыщения поверхности.
К недостаткам можно отнести: невозможность ускорения процесса путем увеличения плотности ионного потока.
Ионное легирование (имплантация) Имплантация существенно снижает износ и трение, увеличивает антикоррозионные свойства металла.
При имплантации тонкий поверхностный слой реноизделия насыщается вносимым элементом, потоком ионов которого поверхность ренодетали обрабатывается (бомбардируется).
Имплантированный элемент может входить в кристаллическую решетку основы в виде твердого тела, или образовывать весьма мелкокристаллические выделения химических соединений с компонентами материала основы. Кроме того, при внедрении иона в кристаллической решетке инициируется смещение атомов, приводящих к образованию большого количества дефектов кристаллической решетки. Толщина этого насыщенного дефектами и вследствие этого упрочненного слоя во много раз превышает глубину проникновения ионов. Толщина модифицированного слоя несколько микрон.
|