4.5. Нанесение гальванических покрытий
Наиболее распространены следующие способы нанесения гальванических покрытий: хромирование, железнение, никелирование, цинкование, кадмирование и др.
Для упрочнения ренодеталей и восстановления их размеров наиболее широко распространены хромирование и железнение.
Хромирование, например, используют: для увеличения твердости, износостойкости поверхности, химической стойкости и прирабатываемости, обеспечения трения со смазочным материалом, восстановления размеров изношенных деталей, а также для декоративных целей. Осадки хрома различают по внешнему виду и по физическим и механическим свойствам. Для улучшения связи хромовых покрытий с поверхностью ренодеталей и получения химически стойких покрытий наращивание хрома часто осуществляют на подслой из других металлов.
Железнение (осталивание) применяют, главным образом, для восстановления размеров деталей машин. Твердость электролитического железа достигает 8000 МПа и более. Ренодетали после железнения можно подвергать термической и термодиффузионной обработке.
Электролитическое хромирование. Хромирование подразделяют на: коррозионно-стойкое, износоустойчивое, пористое декоративное.
Различают три группы ренодеталей, наращиваемых хромом, отличающихся условиями эксплуатации и режимами осаждения, придающими различные свойства эксплуатируемым покрытиям.
Первую группу составляют ренодетали, наращиваемые хромом с целью восстановить размеры и создать переходные посадки и посадки с натягом.
Вторая условная группа состоит из ренодеталей, работающих на трение при малых и средних давлениях и окружных скоростях, при постоянной или переменной загрузке. К таким деталям относятся валы, плунжеры, цилиндры, поршни, мерительный инструмент и многие другие.
К деталям третьей группы могут быть отнесены ренодетали, работающие при больших давлениях и значительных знакопеременных нагрузках, для которых необходимы максимальная прочность связи слоя хрома с поверхностью ренодеталей и вязкость осадков хрома. Покрытия электролитическим хромом получают при осаждении хрома из водных растворов в результате прохождения через раствор электрического тока. Установка для нанесения гальванических покрытий представлена на рис.4.21.
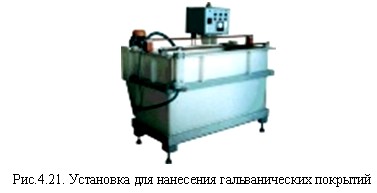
Качество хромового покрытия в основном зависит от состава электролита, плотности тока, температуры электролита и интенсивности его перемешивания в ванне. Изменяя указанные элементы технологического процесса и время осаждения, получают покрытия разной толщины с различными физико-механическими свойствами и равномерностью. Основными составляющими электролитов являются хромовый ангидрид и серная кислота.
Хромирование крупногабаритных ренодеталей (или их отдельных мест) в стационарных ваннах не всегда целесообразно. Поэтому для таких ренодеталей используют переносные ванны, в которые ренодеталь не погружают, а пристраивают ванну к ренодетали. Этот способ осаждения хрома особенно эффективен в том случае, когда хром наносят на поверхности внутренних полостей, которые могут служить емкостями для электролита. Питание постоянным током переносных ванн осуществляется от передвижного низковольтного генератора или выпрямителя тока.
При наращивании гильз и цилиндров применяют подвески. Поршневые кольца и червяки червячных передач хромируют, используя специальные приспособления. Для лучшего удержания смазки на ренодеталях применяют пористое хромирование, так как плотный беспористый хром плохо смачивается маслами. Применение специальных пористых хромовых покрытий улучшает смачиваемость поверхностей: самой детали примерно в 3…5 раз, а сопряженной с ней детали в 1,5…2 раза. Степень пористости хромового покрытия в значительной мере зависит от температуры электролита и плотности тока. При увеличении температуры пористость уменьшается и сетка каналов становится более редкой. Последующая после хромирования электрохимическая обработка (анодное травление) окончательно формирует сетку каналов. Скорость этого формирования зависит от интенсивности процесса травления, т. е. от плотности тока. Плотность тока при анодном травлении должна составлять 40…60 А/дм2, время выдержки 5…12 мин. Анодное травление осуществляют в растворе для хромирования. Обработку резанием можно выполнять перед анодным травлением или после него. На шлифованной поверхности получают более равномерную сетку и одинаковую ширину каналов. Выбор типа хромового покрытия зависит от условий эксплуатации деталей. Так, например, покрытие с пористостью в виде частой сетки целесообразно применять для поршневых колец цилиндров. Такая пористость лучше способствует притирке колец к поверхности цилиндров. Однако поверхность цилиндров лучше работает при применении хромированных поршневых колец с редкой сеткой каналов. При электроосаждении периодическое изменение направления постоянного тока существенно изменяет некоторые свойства покрытий. Одна из характерных особенностей хромирования с применением реверсирования тока — возможность получения покрытия толщиной 300 мкм и более с малыми внутренними напряжениями.
Хромирование проводят при следующем режиме: температура электролита 50…60 °С, катодная плотность тока 60…120 А/дм2, длительность катодного периода 1…5 мин, длительность анодного периода 5…25 с. При периодических изменениях направления тока применяется электролит, содержащий 200…250 г/л хромового ангидрида Cr03 и 2…2,5 г/л серной кислоты Na2S04, или саморегулирующийся электролит. Реверсирование позволяет ускорить процесс осаждения хрома в 1,5…2 раза по сравнению с обычными режимами. Качественные и количественные изменения в процессе хромирования возможны из-за применения тока высокой плотности, при котором выход хрома возрастает. С увеличением скорости протекания электролита от 0 до 200 см/с микротвердость осажденного металла повышается от 7000 до 10 000 МПа при ведении процесса с плотностью тока 45 А/дм2 и температуре электролита 45 °С.
Многослойные электролитические покрытия получают, последовательно наращивая на детали разные металлические покрытия в различном сочетании. К типу многослойных покрытий может быть отнесено и так называемое двухслойное хромовое покрытие. Последнее получают при нанесении различных осадков хрома с изменяющимися свойствами. Если необходимо защитить деталь от коррозии при одновременном увеличении ее износостойкости, наносят два слоя хрома: нижний — беспористый молочный и верхний — блестящий. Слой молочного хрома толщиной 15 мкм осаждают при температуре 70 °С и плотности тока 30 А/дм2. Температура электролита 50°С, плотность тока 50 А/дм2.
Хромирование производят в двух ваннах с электролитами одинакового состава (250 г/л хромового ангидрида и 2,5 г/л серной кислоты).
При изготовлении деталей с хромовым покрытием и износе поверхностей трущихся деталей возможны повреждения защитного слоя.
Электролитическое железнение. При железнении, как и при других электролитических процессах, состав и свойства осажденного металла зависят от состава электролита и режимов наращивания.Процесс покрытия электролитическим железом осуществляют с использованием растворимых (стальных) и нерастворимых (угольных) электродов. При восстановлении изношенных деталей железнением иногда возникает необходимость снятия неполноценного слоя электролитического железа. Для этой цели применяют специальные растворы. Затем деталь подвергают анодной обработке в 30 %-ном растворе серной кислоты.
Электролит для железнения необходимо выбирать с учетом возможности подбора соответствующих материалов для изготовления ванн. Перед помещением в ванну ренодеталей, подвергающихся железнению в горячих электролитах, необходимо производить кратковременный их прогрев (до температуры электролиза) в течение 3….5 мин до включения тока.
Химическое никелирование. Используют при наращивании равномерных по толщине покрытий на ренодеталях из стали, меди, латуни, никеля и алюминия.
Получение покрытий при химическом никелировании основано на восстановлении гипофосфитом ионов никеля из водных растворов солей этого металла. В результате реакции на поверхности наращиваемых. деталей осаждается покрытие, состоящее из никеля и фосфора. Содержание фосфора в никелевых покрытиях зависит от режима технологического процесса и колеблется от 5 до 13 %,при этом в поверхностном слое микротвердость 3500...5000 МПа, которая растет с увеличением содержания фосфора в осадке.
Термическая обработка улучшает также прочность сцепления поверхности наращиваемой детали с покрытием, которая после осаждения равна примерно 35 МПа, а после нагрева до 200…250 °С в течение 40…60 мин 280 МПа.
Наращивание химического никеля осуществляется как в щелочных, так ив кислых растворах. Щелочные растворы характеризуются лучшими технико-экономическими показателями по сравнению с кислыми. Скорость наращивания покрытия при химическом никелировании в этих растворах может быть постоянной и поддерживаться на уровне 10…12 мкм/ч. никеля, гипофосфита и раствора аммиака в соответствии с заданной рецептурой. Необходимо поддерживать величину рН в пределах 8,5…8,7.
Цинкование. Покрытия применяют для защиты изделий из черных металлов (листов, труб, проволоки, деталей станков, автомобилей, приборов, крепежных изделий) от коррозии. В реновационном производстве покрытия в частности используют для защиты от коррозии крепежных деталей.
Электроконтактное цинкование (натирание) применяют для восстановления посадочных мест под подшипники с небольшим износом, например, проушины вилок карданных валов.
Цинкование проводят в электролите, содержащем, г/л: сернокислого цинка 280…300, борной кислоты 20…40. Процесс начинают вести при плотности тока 30…50 А/дм2. Скорость перемещения анодного тампона относительно покрываемой поверхности 10 м/мин. Обычно используют размерное цинкование, т. е. покрытые поверхности не обрабатывают резанием. При цинковании с применением периодического тока свойства покрытий улучшаются, а процесс интенсифицируется в 2…3 раза.
|