4.3. Напыление металлических покрытий
Газопламенное напыление порошковых материалов. Основа процесса газопламенного нанесения — пластификация порошка в высокотемпературном источнике тепла (ацетилено-кислородном пламени) и нанесение его газовыми потоками на предварительно подготовленную изношенную поверхность.
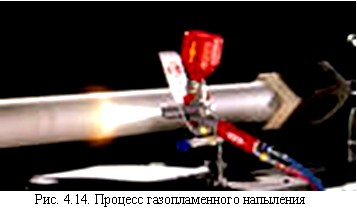
Преимущества газопламенного нанесения состоят в высокой производительности процесса, локальности обработки, незначительном влиянии на подложку, возможности нанесения покрытий на изделия больших размеров, отсутствии ограничений на сочетания материалов покрытия и подложки, что позволяет охватить большую номенклатуру восстановления изношенных ренодеталей.. Рассматриваемый способ позволяет, восстанавливать детали типа вала с износом до 2,5 мм на сторону; Восстановленные детали устойчивы против коррозии, абразивного изнашивания, действия высоких температур. На рис 4.14.показан процесс газопламенного напыления.
Технологический процесс газопламенного нанесения, в основном, состоит из трех этапов: нагрева поверхности детали до 200…250 °С; нанесения подслоя, который дает основу, необходимую для наложения основных слоев; нанесения основных слоев, позволяющих получить покрытия с необходимыми физико-механическими свойствами. К основным факторам, влияющим на прочность сцепления покрытия с основой, относятся: способ подготовки поверхности и используемый при этом абразивный материал, параметры струйной обработки поверхности, время выдержки после обработки, наличие предварительного подогрева, применение подслоя и использование термореагирующих порошков, способ распыления, эффективная мощность пламени, параметры процесса распыления, состав материала покрытия (наличие поверхностно-активных добавок в покрытии зависит и от применяемого оборудования и от присадочных материалов). Основой конструкции аппаратов для напыления и горелок для наплавки является базовая схема сварочной горелки. Сварочная горелка служит для смешивания горючего газа с кислородом и получения газового пламени. Мощность, состав и форма сварочного пламени зависят от мундштуков наконечников горелок. Сварочные горелки подразделяют: по способу подачи горючего газа и кислорода в смесительную камеру на инжекторные и безынжекторные; по роду применяемого горючего газа на ацетиленовые и для газов заменителей; по назначению на универсальные (сварка, наплавка) и специализированные (выполнение одной операции): по форме пламени на однопламенные и многопламенные; по мощности пламени на микромощные (до 60 л/ч), малой мощности (до 700 л/ч), средней мощности (до 2500 л/ч), большой мощности (до 7000 л/ч); по способу применения —- на ручные и машинные.
Горелки для газопорошковой наплавки, выполненные на базе сварочных горелок, отличаются от этих горелок принципом работы и конструкцией [в аппаратах и горелках предусмотрен питатель (бункер) с порошковым материалом]. Основное назначение аппарата для напыления — подавать порошок в ядро факела пламени. На рис.4.15 представлена типовая схема установки газоплазменного напыления порошкового материала
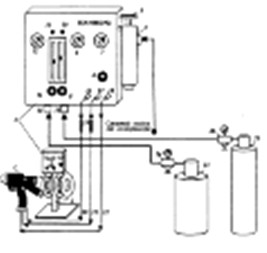
Рис.4.15. Установка газопламенного напыления порошкового материала:
1 – порошковый бункер; 2 – направляющая трубка; 3 – многотепловой наконечник; 4 – база сварочной горелки.
Установка состоит из пульта управления, термораспределительного пистолетного устройства для его крепления в суппорте токарного станка. Пульт управления служит для настройки рабочих режимов напыления с помощью манометров, регулирующих расход газов, обратных клапанов и других элементов, обеспечивающих безопасную и стабильную работу пистолета.
Газотермическое напыление. При ремонте оборудования с помощью газотермического напыления восстанавливают размеры изношенных деталей оборудования (шеек валов лесопильных рам, валов деревообрабатывающих станков, шеек осей конвейеров и тележек и т. д.), уменьшают внутренние размеры изношенных посадочных отверстий под подшипники, втулки и другие детали; наносят на подшипники и втулки антифрикционные покрытия из псевдосплавов, образуемых в результате одновременного распыления двух или трех разных металлов. Этот вид напыления характеризуется своей простотой, технологической доступностью и компактностью. Газотермическое напыление дает стойкие антикорозионные, жаростойкие, электроизоляционные и износостойкие покрытия.
Существуют дуговые и газоплазменные способы нанесения покрытий. Дуговые способы покрытия энергетически выгодны, однако пригодны лишь для распыления металлических стержней. Для порошковых материалов примелем только газопламенный способ. Перед началом напыления поверхность деталей необходимо очищать механическим, а если потребуется, то и химическим путем.
В данной области используются установки и аппаратура порошкового и проволочного типов. Остановимся на их характеристиках:
установка УГПЛ предназначена для ручного напыления термопластовых, цинковых и других материалов с температурой плавления 800°С. Используют в качестве напыляемого материала порошок. При работе используют ацетилен и воздух;
установка УГПТ— для ручного напыления тугоплавких покрытий из хромборникелевых сплавов. Напыляемый материал — порошок. Рабочие газы — ацетилен или кислород;
установка МГИ-4П — ручное напыление деталей из алюминия, стали, цинка. Напыляемый материал — проволока. Используемые газы — кислород, воздух, бутан, пропан;
установка МГИ-4 имеет те же характеристики, что, и МГИ-4П, но использует только ацетилен, кислород и воздух.
На рис. 4.16 представлены: металлизатор газовый МГИ-4 и установка УГПЛ. Газопитание аппарата МГИ-4 горючим газом, как правило, осуществляется от баллона для разрядной рампы. В обоих случаях давление горючего газа должно поддерживаться не менее 0,06 МПа (0,6 кгс/см2).
Металлизация. Металлизация – один из распространенных способов получения металлических покрытий поверхностей нанесением на эти поверхности расплавленного металла.
Сущность процесса состоит в следующем: металл, расплавленный дугой (при электрометаллизации) или ацетиленокислородным пламенем (при газовой металлизации) и распыленный струей сжатого воздуха (давление до 0,6 МПа), покрывает поверхность восстанавливаемой детали.
Процесс дуговой металлизации осуществляют специальным аппаратом — металлизатором.
Аппарат (рис. 4.16) действует следующим образом. С помощью протяжных роликов по направляющим наконечникам непрерывно подаются две проволоки, к которым подведен электрический ток. Возникающая между проволоками электрическая дуга расплавляет металл. Одновременно по воздушному соплу в зону дуги поступает сжатый газ под давлением 0,6 МПа.
Большая скорость движения частиц металла (120…300 м/с) и незначительное время полета, исчисляемое тысячными долями секунды, обусловливают в момент удара о ренодеталь ее пластическую деформацию, заполнение частицами неровностей и пор поверхности детали, сцепление частиц между собой и с поверхностью, в результате чего образуется сплошное покрытие. Последовательным наслаиванием расплавленного металла можно получить покрытие, толщина слоя которого может быть от нескольких микрон до 10 мм и более (обычно 1…1,5 мм для тугоплавких и 2,5….3 мм для легкоплавких металлов).
Такие покрытия из недефицитных металлов отличаются высокими антифрикционными свойствами, их используют взамен специальных баббитов и бронз. Из-за пористости напыленного слоя металла в него впитывается некоторое количество масла. Это улучшает условия смазывания и обеспечивает длительную работу этих деталей без смазки, но и без заеданий.
В зависимости от источника расплавления металла различают газопламенную, дуговую, высокочастотную и плазменную металлизацию.
При ремонте оборудования наибольшее распространение получила дуговая металлизация.
Небольшие объемы работ по металлизации выполняют переносными (ручными) дуговыми электрометаллизаторами ЭМ-ЗА; значительные по объему работы — станочными электрометаллизаторами ЭМ-6 и высокочастотными металлизаторами МВЧ-1, МВЧ-2. Покрытия на поверхностях ренодеталей из разнородных металлов получают с помощью многофазных металлизаторов УМА-1. Питание электрометаллизаторов осуществляется либо от трансформаторов специальной конструкции (СТЭ-43-2с), либо от обычных сварочных трансформаторов (без дросселей) с дополнительными отводами от витков вторичной обмотки, допускающими регулирование напряжения в пределах 20…55 В (с промежутками через 4…5 В) при токе не менее 250 А. При восстановлении поверхностей ренодеталей под неподвижные посадки применяют малоуглеродистую проволоку из стали 08, 10, 15, 20. Для получения износостойких покрытий на ренодеталях, работающих в подвижных соединениях, применяют проволоку из высокоуглеродистых сталей У7, У7А, У8, У10. В ручных электрометаллизаторах (ЭМ-ЗА) применяют высокоуглеродистую проволоку диаметром более 2,5 мм, предварительно отожженную при температуре 760 °С в электропечи. Образовавшаяся окалина на проволоке должна быть удалена пескоструйной обработкой. При нанесении слоя покрытия на поверхность детали ее нагрев до 50….70 °С не вызывает никаких структурных изменений в металле детали, т. е. его механические свойства сохраняются, благодаря чему можно наносить слой.
Механизированное напыление покрытий проволокой из цинка, алюминия и других металлов. Напыление вручную покрытий с проволокой из цинка, алюминия и других металлов напыление с использованием проволоки (диаметр 1,5— 2 мм) из цинка, алюминия, стали, молибдена и других металлов в виде проволоки в целях защиты от коррозии, восстановления и упрочнения деталей машин и механизмов.
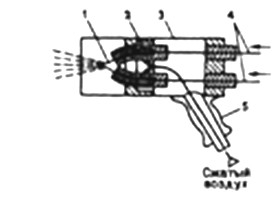
4.16. Схема принципа действия металлизатором:
1 – проволока; 2 – мунштук; 3 – корпус; 4 – проволока; 5 – рукоятка.
С помощью рассматриваемых способов осуществляют заделку трещин в ренодеталях из алюминиевых сплавов (сплавы: АД, АМц, АМг) покрытия на любые материалы: металл, пластмассу, дерево, резину и т. п. Металлизация обеспечивает высокую твердость напыленного слоя, что способствует увеличению сроков службы восстанавливаемых деталей. Напыляют самые разнообразные металлы. Например, для напыления может быть использована биметаллическая проволока из алюминия и свинца, что позволяет не только заменять дорогостоящие оловянистые баббиты и бронзы, но и значительно увеличить срок службы подшипников.
При подготовке поверхности ренодеталей к металлизации отдельные операции выполняют в такой последовательности: очищают ренодетали от загрязнений, пленок, окислов, жировых пятен, влаги и продуктов коррозии; выполняют предварительную обработку резанием поверхности для придания ей правильной геометрической формы; получают на поверхностях восстанавливаемых деталей шероховатость, необходимую для удержания нанесенного слоя металла; обеспечивают защиту смежных поверхностей деталей, не подлежащих металлизации.
Поверхности деталей, подлежащих металлизации, очищают от загрязнений в моечных машинах, щетками, промывают в бензине или растворителях, нагревают в печах пламенем газовой горелки или паяльной лампы. Обработкой резанием исправляют геометрическую форму детали и доводят размеры детали до размеров, при которых возможно нанесение покрытий заданной толщины. На концах цилиндрических поверхностей оставляют буртики и протачивают замки в виде кольцевых канавок, предохраняющие покрытие от разрушения.
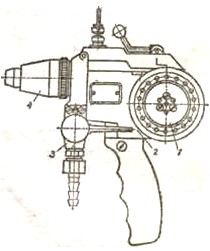
Рис. 4.17. Газовый металлизатор МГИ-4:
1— воздушная турбина; 2 — червячный редуктор; 3— пробковый кран; 4 – сопло.
Газодинамическое нанесения покрытий. Технология включает в себя нагрев сжатого газа (воздуха), подачу его в сверхзвуковое сопло и формирование в этом сопле сверхзвукового воздушного потока, подачу в этот поток порошкового материала, ускорение этого материала в сопле сверхзвуковым потоком воздуха и направление его на поверхность обрабатываемого реноизделия. Принципиальная схема способа представлена на рис. 4.18.
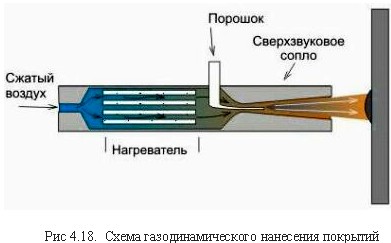
В качестве порошковых материалов используются порошки металлов, сплавов или их механические смеси в добавке с керамическими порошками. При этом путем изменения режимов работы оборудования можно либо проводить эрозионную обработку поверхности изделия, либо наносить металлические покрытия требуемых составов. Изменением режимов можно также менять пористость и тол
щину напыляемого покрытия. На рис. 4.19 показана структура напыляемого покрытия.
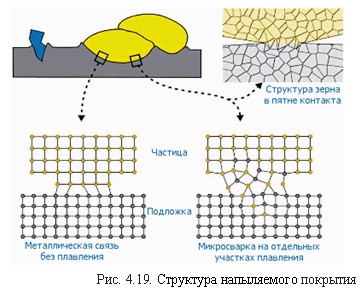
В наиболее распространенных газотермических методах нанесения покрытий для формирования покрытий из потока частиц необходимо, чтобы падающие на подложку частицы имели высокую температуру (обычно выше температуры плавления материала). В данном случае с твердой подложкой взаимодействуют частицы, находящиеся в нерасплавленном состоянии, но обладающие очень высокой скоростью. Ускорение частиц покрытия до нужных скоростей осуществляется сверхзвуковым воздушным потоком с помощью специальных установок. Закрепление твердых металлических частиц, обладающих большой кинетической энергией, на поверхность положки происходит в процессе высокоскоростного удара.
|