4.10.4. Упрочняющая обработка ППД
В результате ППД изменяются не только размеры заготовки, шероховатость поверхности, но и физико-механические свойства периферийного слоя металла с образованием в нем остаточных напряжений (в основном сжимающих).
Основным назначением процессов упрочняющего ППД является повышение несущей способности поверхностного слоя деталей.
Упрочняющее накатывание
Упрочняющее накатывание – это накатывание, при котором происходит поверхностное упрочнение. Накатывание по выпуклой или плоской поверхности материала называется поверхностным обкатыванием.
Обкатку выпуклых или плоских деталей производят роликами или шариками (одним или несколькими), имеющими разные рабочие профили (рис.4.45). Обкатка осуществляется продольным перемещением ролика или шарика по обрабатываемой поверхности с нагружением его определенной силой или только нагружением без продольного перемещения. В результате обкатки в значительной степени повышается долговечность деталей, работающих в условиях циклических нагружений. При обкатке в зависимости от ее режима может быть снижена или повышена шероховатость поверхности.
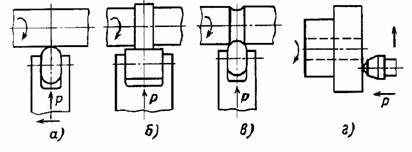
Рис. 4.45. Схемы процесса обкатывания
Если необходимо получить большую глубину наклепанного слоя с большими остаточными напряжениями сжатия, обкатку производят при высоких давлениях роликами со сферическим контуром.
Наряду с упрочняющей широкое применение получает упрочняющее-сглаживающая обкатка, при которой снижается шероховатость обрабатываемой поверхности до Ra=0,040…0,160 мкм, что в ряде случаев позволяет изменить чистовое шлифование обкаткой роликами.
Влияние режима обкатки усилия на ролик, подачи, скорости и числа проходов на качество обработки зависит от свойств обрабатываемых материалов и назначения обкатки (сглаживающая или упрочняющая обработка).
Наиболее широко упрочняющую обкатку роликами применяют для упрочнения крупных деталей – локомотивных и вагонных осей, торсионных валов, зубчатых колес и других деталей. Особая эффективность упрочнения крупных деталей объясняется возможностью получать в процессе обкатки большую глубину (до 35 мм) и высокую степень наклепа. Например, обкатка подступичной части осей вагонов при глубине наклепа 13…19 мм увеличивает срок их службы в 25 раз.
Центробежно-шариковая обработка
На практике получают все более широкое распространение методы упрочняющей обработки металлов, основанные на динамическом действии (ударе) инструмента на обрабатываемую поверхность. К этим методам относятся чеканка, обработка вибрирующими роликами и шариками, ценробежно-шариковая обработка, обработка механическими щетками, дробеструйная обработка и др.
Способ упрочнения центробежно-шариковым наклепом основан на использовании центробежной силы стальных шариков диаметром 7…12 мм, свободно вращающихся со скоростью 20…40 м/с над обрабатываемой поверхностью (рис.4.46). Встречая на своем пути заготовку, движущуюся навстречу шарикам со скоростью 30…90 м/мин, каждый шарик с силой ударяется об обрабатываемую поверхность, производит наклеп ее и сглаживание шероховатостей. В качестве оборудования применяются токарные, шлифовальные и другие станки как общего, так и специального назначения.
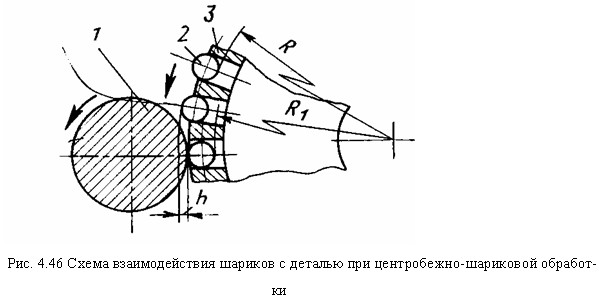
Режим процесса центробежно-шариковой обработки характеризуется окружной скоростью упрочнителя V,натягом i, количеством шариков в сепараторе z и их диаметром dm, окружной скоростью заготовки Vз, величиной продольной подачи Sо, количеством проходов К. Необходимый натяг iобеспечивается установкой упрочнителя на определенном расстоянии от заготовки при помощи поперечного винта суппорта или стола станка.
Режим центробежно-шариковой обработки в значительной мере определяется числом ударов шариков по определенной площади обрабатываемой поверхности. Число ударов шариков, приходящихся на 1 мм2 обрабатываемой поверхности, определяется по формуле
.
В качестве уплотнителя может быть использована ротационная головка с роликами, установленными по винтовой линии подобно зубьям двухзаходной червячной фрезы.
Обработка вибрационными эксцентриковыми и ультразвуковыми упрочнителями
Центробежно-шариковые упрочнители при наклепывании детали основную силу удара шарика передают в направлении касательной к поверхности обрабатываемой заготовки. В результате этого поверхностный слой металла деформируется и смещается в тангенциальном направлении. При таком характере деформирования недостаточно точно назначенный режим обработки может вызвать нарушение целостности поверхностных слоев металла, а в ряде случаев – нарушение поверхностного слоя.
В настоящее время разработан новый способ динамического наклепа поверхностного слоя металла, при котором сила удара шарика об обрабатываемую поверхность обеспечивается инерционной эксцентриковой массой. При этом в зависимости от необходимости удар деформирующего шарика можно осуществлять в разных направлениях: нормальном, тангенциальном (окружном), осевом и в любом промежуточном направлении (рис. 4.47, а).
Получила распространение и обработка ППД с ультразвуковыми колебаниями деформирующего инструмента. В процессе ультразвукового упрочнения инструменту сообщаются ультразвуковые колебания в направлении, перпендикулярном к обрабатываемой поверхности, и прикладывается статическое усилие поджима (рис.4.47, б). Как показали исследования, в том случае, когда инструменту сообщаются колебания ультразвуковой частоты, в зоне обработки температура достигает 1000…1200°С. В результате чего осуществляется не холодное пластическое, а термопластическое деформирование поверхностного слоя металла.
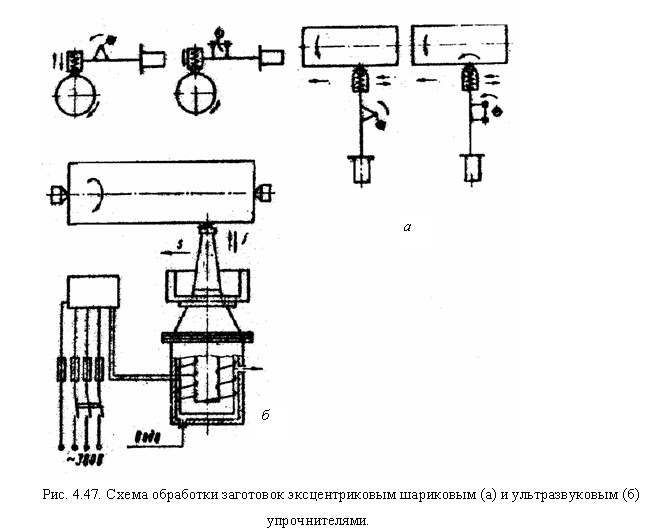
Упрочняющая чеканка
При упрочняющей чеканке происходит упрочнение поверхностным наклепом.
Сущность способа упрочнения чеканкой заключается в том, что с помощью специального приспособления – механического, пневматического и электромеханического типа наносят удары по упрочняемой поверхности. В результате удара инструмента (ударника с бойком) изменяется качество поверхности , и в тонком поверхностном слое создаются остаточные напряжения сжатия до 100 кг/мм2. Шероховатость поверхности обычно находится в пределах Rz= 160…40 мкм. Глубина наклепа при чеканке может быть получена до 35 мм. Твердость поверхности заготовки, обработанной чеканкой, на 30…50% выше исходной твердости. Для достижения низкой шероховатости поверхности после чеканки следует предусмотреть механическую обработку на глубину до 0,5 мм или сглаживающие проходы по галтелям бойками увеличенных радиусов.
Исследования показывают, что соответствующим подбором режимов шага чеканки, количества проходов, скорости и энергии удара бойка можно достичь равнопрочности ступенчатого вала в галтелях и гладкой части и повысить несущую способность вала в 1,5 раза и более. Способ упрочнения чеканкой наиболее эффективен и экономически выгоден (по сравнению с обкаткой роликами и шариками) при упрочнении таких элементов деталей машин, как галтели, сварочные швы и др.
Обработка механическими щетками
Механические щетки используются для снятия заусенцев, скругления острых кромок, очистки поверхности от окалины, шлака, декоративной отделки поверхностей металлов, дерева и пластмасс, подготовки поверхностей и упрочнения слоя осаживаемого металла при гальванических покрытиях, полирования и упрочнения поверхностей для повышения износостойкости, усталостной прочности и коррозионной стойкости деталей машин и т.д.
Механическими щетками (рис.4.48) обрабатываются детали из различных металлов до и после термической обработки. При определенных условиях и режимах обработки можно получить поверхность с шероховатостью Ra=0,16…0,08 мкм.
В процессе обработки деталей дисковая, цилиндрическая или торцовая щетка, установленная на шпинделе станка или непосредственно на валу электродвигателя, приводится во вращение. В момент контакта рабочей поверхности щетки (образованной торцами проволочек) с поверхностью заготовки происходит удар и формирование поверхности детали.
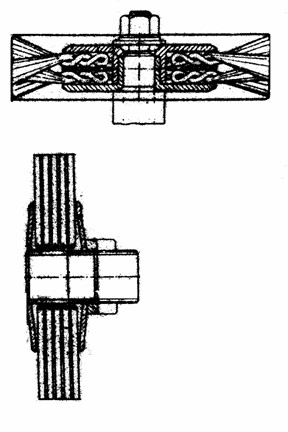
Рис. 4.48. Механические щетки
В процессе вращения щетки с определенной скоростью отдельные ее проволочки не только срезают и сглаживают вершины гребешков микронеровностей, но и проникают во впадины микропрофиля. При этом все риски, царапины и микротрещины поверхностного рельефа сглаживаются, металл в местах концентрации напряжений упрочняется, что приводит к значительному повышению усталостной прочности обработанных деталей.
Качество поверхности. Получаемое при обработке деталей проволочными механическими щетками, зависит от высоты микронеровностей исходной поверхности, материала обрабатываемой детали, материала и размера проволоки, идущей на изготовление щетки, скорости деформирования, контактного давления, продолжительности и условий обработки, а также вида смазочно-охлаждающей жидкости.
По конструкции щетки разделяют на кольцевые, дисковые, цилиндрические и иглофрезы (жесткие металлические щетки).
Обработка дробью
Обработка дробью – это поверхностное пластическое деформирование металла ударами дроби.
Обработка дробью – эффективный и распространенный технологический метод повышения выносливости и износостойкости поверхностным пластическим деформированием деталей.
Главной особенностью этого метода является его универсальность. Обработкой дробью можно упрочнять любые сложные поверхности, например такие, как зубья шестерен, витые пружины, рессоры, перо лопаток компрессора и т.п.
Упрочнение сухой дробью в основном осуществляется на дробеструйных и дробеметных установках. В первом типе установок дроби сообщается кинетическая энергия в дробеструйном сопле сжатым воздухом, подаваемым через воздушную форсунку, во втором типе – в центробежном дробеметном колесе (рис.4.49).
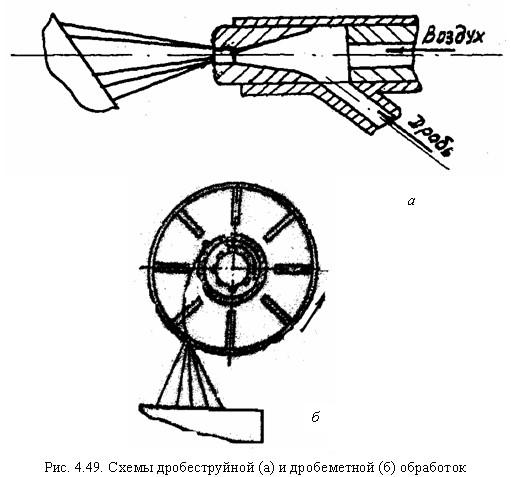
Сущность процесса заключается в том, что поверхность заготовки бомбардируется потоком дробинок, летящих с большой скоростью. При ударе о поверхность каждая дробинка оставляет микровмятину, в результате чего поверхностный слой пластически деформируется и упрочняется. Внутренние напряжения сначала растут пропорционально времени обработки, но затем через 1…2 мин наступает «насыщение». Дальнейшая обработка становится уже вредной, так как ведет к появлению микротрещин (перенаклепу).
Оптимальное время обработки и угол падения дроби (70…90°) определяют в зависимости от материала детали и глубины упрочнения экспериментально.
Дробь рекомендуется применять стальную возможно меньшего диаметра (0,8…1,0 мм). Размеры дробинок должны быть такими, чтобы они попадали на дно галтелей, выточек или канавок. Радиус дроби применяют, равным половине радиуса галтелей.
При выборе режимов обработки следует иметь в виду, что на качество обработки оказывает влияние следующие технологические факторы: скорость дроби при встрече с обрабатываемой поверхностью; размер, качество и расход дроби; продолжительность обработки; направление потока дроби (угол атаки); обрабатываемый материал; плотность, с которой дробь покрывает поверхность; расстояние от места вылета дроби.
От перечисленных технологических факторов дробеструйной обработки находятся в зависимости шероховатость поверхности, глубина наклепа и остаточные напряжения.
Шероховатость поверхности улудшается с увеличением твердости обрабатываемого материала. Практически шероховатость поверхности путем дробеструйной обработки может быть получена от Rz =20 мкм до Ra = 2,5 мкм. А на твердых материалах – до Ra = 0,16 мкм.
Глубина наклепа и остаточные напряжения связаны с пластической деформацией, но их величина в первую очередь определяется физическими и механическими свойствами материала.
Одной из главных характеристик материала, определяющих удельную работу дроби при вдавливании, является динамическая твердость Ндин. Глубина наклепа при дробеструйной обработке может быть определена по формуле
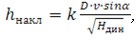
где D - диаметр дробинок; v - скорость дроби при встрече с обрабатываемой поверхностью; a угол атаки; k – коэффициент пропорциональности.
Удары дроби вызывают пластическую деформацию на глубину 0,15…3 мм, в результате улучшаются механические свойства поверхностного слоя при одновременном появлении благоприятных остаточных напряжений сжатия.
Приближенно средние остаточные напряжения δнакл в наклепанном слое будут пропорциональны динамической твердости материала:

где m – коэффициент пропорциональности.
В настоящее время создан гидродробеструйный способ упрочнения, сущность которого заключается в обработке деталей шариками, эжектирумыми смазывающе-охлаждающей жидкостью. Гидродробеструйный способ упрочнения – качественно новый процесс, отличающийся от дробеструйного более высоким качеством обработки поверхности.
Вибрационная ударная обработка
Вибрационная ударная обработка (виброгалтовка, виброударная обработка) – это ППД соударением незакрепленных или закрепленных заготовок и рабочих тел в замкнутом объеме при их перемещении, вызванном колебательным движением рабочего органа.
Процесс сопровождается последовательным нанесением на поверхность обрабатываемых заготовок большого числа микроударов частицами рабочей среды при их взаимном соударении и скольжении. Удары вызваны действием направленных вибраций, сообщаемых рабочей камере инерционным вибратором (рис. 4.50). Рабочая камера подвергается вибрации от инерционного вибратора. При этом детали и рабочая среда, непрерывно подвергаясь переменным по знаку ускорения, совершает два вида движения: колебание и медленное вращение всей массы (циркуляционное движение). От стенок рабочей камеры вибрация передается прилегающим слоям рабочей среды, которые передают ее следующим слоям и т.д.
В качестве рабочих сред широкое применение в практике виброударной обработки получили стальная и чугунная дробь, литые звездочки, рубленая проволока, стальные полированные шарики и др.
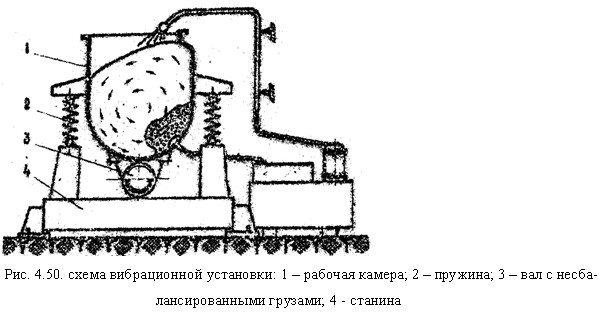
В процессе вибрационного упрочнения обеспечивается пластическое деформирование поверхностного слоя, следствием чего является повышение микротвердости, образование сжимающих остаточных напряжений первого рода и уменьшение шероховатости поверхности.
Виброударное упрочнение является универсальным методом упрочнения обработки. Наиболее наглядны его преимущества при обработке деталей сложной формы, а также при упрочнении деталей небольших размеров разнообразной номенклатуры.
Интенсивность виброударной обработки зависит от режима и продолжительности обработки, характеристик и размеров частиц рабочей среды, объема рабочей камеры и степени ее заполнения, механических свойств материала обрабатываемых деталей и др.
Контрольные вопросы:
- Перечислите основные способы восстановления ренодеталей.
- Какие способы восстановления являются лидирующими в процессах ремонта деталей?
- В чем сущность процесса напыления?
- Перечислите основные способы пластического деформирования.
- Какие современные способы нанесения покрытий применяются в настоящее время?
- Сформулируйте понятие процесса ППД.
|