3.2. Виды и типовые конструкции технологической оснастки, используемой ремонтно-восстановительном производстве
Приспособлениями в машиностроении называют вспомогательные устройства к технологическому оборудованию, используемые при выполнении операций обработки, контроля и сборки.
Технологическая оснастка ремонтно-восстановительного производства представляет собой устройства, которые расширяют технологические возможности оборудования и применяют только вместе с ним. Технологическую оснастку и заготовку устанавливают на технологическое оборудование с целью выполнения части технологического процесса.
Станочное приспособление – это технологическая оснастка, предназначенная для установки или направления предмета восстановления либо инструмента при выполнении технологической операции.
Отличительной особенностью выбора и конструктивных решений ТО при ее проектировании, является:
- непостоянство форм и размеров однотипных деталей в пределах партии запуска;
- невозможность использования для закрепления однотипных поверхностей и элементов, в силу их износа или вообще в силу их отсутствия;
- невозможность приложения одинаковых сил и моментов к поверхностям из-за неравномерности физико-механических свойств.
Как видно, возникают сложности с прямым использованием типовых конструкций ТО, применяемых при изготовлении деталей.
Таким образом, необходимо предусмотреть использование в процессе обработки ренодеталей оснастки, оснащенной, специальными и унифицированных элементами базирования и закрепления, с возможностями быстрой переналадки и регулировки.
Так же необходимо предусмотреть создание специальной оснастки для процессов нанесения восстановленного слоя, оснастив приспособления устройствами перемещения, поворота, деления и транспортирования в рабочей зоне применяемого оборудования.
Применение приспособлений при восстановлении изделий позволяет:
- устранить разметку ренозаготовок перед обработкой, повысить ее точность при установке и изготовлении;
- увеличить производительность труда на восстановительной операции;
- снизить себестоимость продукции;
- облегчить условия работы и обеспечить ее безопасность;
- расширить технологические возможности оборудования;
- организовать многостаночное обслуживание;
- применить технически обоснованные нормы времени и сократить число рабочих, необходимых для выпуска продукции.
Частая смена объектов ремонтно-восстановительного производства, связанная с нарастанием темпов технического процесса, требует создания новых конструкций приспособлений, методов их расчета, проектирования и изготовления, обеспечивающих неуклонное сокращение сроков подготовки производства.
Затраты на изготовление технологической оснастки составляют 15…20% от затрат на оборудование для технологического процесса изготовления ренодеталей машин или 10…24% от стоимости восстановления изделия.
Классификацию приспособлений проводят по следующим признакам:
- по целевому назначению приспособления делят на 5 групп:
- станочные приспособления для установки и закрепления обрабатываемых ренозаготовок на станках. В зависимости от вида обработки различают токарные, фрезерные, сверлильные, расточные, шлифовальные и др.;
- приспособления для закрепления режущего инструмента. Они характеризуются большим числом нормализованных деталей и конструкций, что объясняется нормализацией и стандартизацией самих режущих инструментов;
- сборочные приспособления используют при выполнении сборочных операций, требующих большой точности сборки и приложения больших усилий;
- контрольно-измерительные приспособления применяют для контроля восстановленных изделий, промежуточного и окончательного контроля, а также для проверки собранных узлов и машин.
Контрольные приспособления служат и для установки мерительного инструмента;
- приспособления для захвата, перемещения и перевертывания обрабатываемых ренозаготовок, а также для отдельных деталей и узлов при сборке.
- По степени специализации приспособления делят на универсальные, специализированные и специальные;
- По степени механизации и автоматизации приспособления подразделяют на ручные, механизированные, полуавтоматические и автоматические;
- По функциональному назначению элементы приспособлений делят на установочные, зажимные, силовые приводы, элементы для направления режущего инструмента, вспомогательные механизмы, а также вспомогательные и крепежные детали (рукоятки, сухари, шпонки). Все эти элементы соединяются корпусными деталями.
Станочные приспособления занимают наибольший удельный вес по стоимости и трудоемкости изготовления в общем количестве различных типов технологической оснастки и имеют следующие классификационные признаки:
Сборно-разборные приспособления из стандартных узлов (СРП), применяемые при обработке различных заготовок(в том числе и на станках с программным управлением) в серийном и крупносерийном производстве часто сменяемых изделий. Приспособления СРП позволяет сократить в 3…4 раза трудоемкость проектирования и изготовления оснастки и до 10…20 ч цикла оснащения операций.
СРП содержат комплексы функциональных узлов с универсальными и специализированными базовыми поверхностями для сборки компоновок как специальных, так и наладочных, фрезерных, токарных, сверлильных и других приспособлений. Они обеспечивают высокую производительность оборудования, точное базирование заготовок, быструю переналадку и перекомпоновку.
Универсальные приспособления (УП) используют, как было указано выше, для расширения технологических возможностей металлорежущих станков. К ним относятся: универсальные, поворотные, делительные столы, самоцентрирующие патроны.
Универсальные бесподналадочные приспособления (УБП) применяются для базирования и закрепления однотипных ренозаготовок в условиях единичного и мелкосерийного производства. К этому типу принадлежат универсальные патроны с кулачками, универсальные фрезерные и слесарные тиски.
Универсально-наладочные приспособления (УНП) используют для базирования и закрепления заготовок в условиях многономенклатурного производства. К ним относятся универсальные патроны со сменными кулачками, универсальные тиски, скальчатые кондукторы.
Специализированные бесподналадочные приспособления (СБП) используют для базирования и закрепления заготовок, близких по конструктивным признакам и требующих одинаковой обработки. К таким приспособлениям принадлежат приспособления для обработки ступенчатых валиков, втулок, фланцев, дисков, корпусных деталей.
Специализированные наладочные приспособления (СНП) применяют для базирования и закрепления заготовок, близких по конструктивно-технологическим признакам и требующих для их обработки выполнения однотипных операций и специальных наладок. CНП, как и УНП, сокращают цикл оснащения операций до 10…15 ч. Они содержат комплексы конструкций со специализированными базовыми поверхностями для установки наладок, обеспечивающих точное базирование заготовок и быструю переналадку.
Универсально-сборочные приспособления (УСП) применяют в условиях серийного производства для базирования и закрепления конкретной ренодетали. Из комплекта УСП собирают специальное приспособление, которое затем разбирают, а элементы УСП многократно используют для сборки других приспособлений.
Повышение эффективности использования универсальных станков достигается на основе роста уровня оснащенности технологических процессов и, в первую очередь, за счет применения высоко производительной переналаживаемой стандартной оснастки.
Преимущества системы УСП:
- значительно сокращаются цикл и сроки проектирования и изготовления оснастки, сборка приспособления средней сложности зажимает всего лишь 2,5..5ч., в большинстве случаев она выполняется по чертежу обрабатываемой ренодетали;
- резко снижаются трудоемкость и себестоимость изготовления оснащения для осваиваемого нового изделия.
Специальные универсально-сборные станочные приспособления из стандартных узлов и деталей, применяются при обработке ренозаготовок различной формы в условиях единичного и мелкосерийного производства. Компоновка приспособлений УСП осуществляется на специализированных сборочных участках. Время сборки компоновки 1,5…3 ч. При разовой сборке происходит экономия средств на изготовление и материала.
Специальные приспособления (СП) используют для выполнения определенной операции и при обработке конкретной ренодетали. Такие приспособления называются одноцелевыми. Их применяют в крупносерийном производстве.
Современные приспособления – большой класс технологических объектов, отличающихся многообразием конструкций, многокомпонентностью и иерархичностью структуры, сложной геометрией составляющих элементов и широким диапазоном изменения размеров, а также различной степенью универсальности и назначением.
Выбор конструкции приспособления во многом зависит от характера производства.
Основными исходными данными при проектировании приспособлений являются: чертежи и технические условия на изготовление ренодетали, паспортные данные оборудования, ГОСТы и ведомственные нормали на детали, и узлы приспособления, требуемые производительность и точность.
При проектировании приспособлений необходимо стремиться к увеличению одновременно работающих инструментов, к повышению режимов резания и уменьшению времени на установку ренозаготовки.
Для снижения себестоимости необходимо сокращать сроки проектировании и изготовления приспособлений, обеспечивать широкую нормализацию деталей и облегчать условия труда.
Режущий инструмент – это тоже элемент технологической оснастки, служащий для воздействия на предмет восстановления с целью изменения его состояния, которое определяют с помощью мер и измерительных приборов.
Выбор режущих инструментов производится в зависимости от:
- вида обработки восстанавливаемого изделия и типа станка;
- размеров и формы восстанавливаемого изделия;
- с точности обработки и шероховатости поверхности;
- материала ренозаготовки и физико-механических свойств материала покрытия;
- типа производства.
При всех типах производства следует стремиться использовать для выполнения ремонтно-восстановительного процесса нормализованные инструменты. Применение специальных инструментов целесообразно на крупных специализированных предприятиях ремонтно-восстановительного производства.
Выбранный и изготовленный инструмент, например, режущий должен обеспечить:
- высокие скорости резания и период стойкости;
- заданную точность и шероховатость обработки;
- наименьшую себестоимость обработки.
Виды инструментов их характеристика, область применения, необходимые параметры, порядок выбора подробно описаны в справочниках.
Выбор средств технического контроля производится в зависимости от:
- размеров и формы измеряемой поверхности;
- требуемой точности контроля;
- типа производства;
- затрат на приобретение и эксплуатацию на крупных ремонтно-восстановительных предприятиях, непосредственно на механических участках. Используются в основном калибры и шаблоны, в мелкосерийном и единичном производствах – универсальные измерительные инструменты и приборы (раздел 2).
На рис 3.6[19] изображен пневматический скальчатый кондуктор. В конструкцию любого скальчатого кондуктора входят постоянные узла (корпус; две или три скалки, несущие кондукторную плиту; механизм перемещения скалок; механизм закрепления обрабатываемой заготовки) и сменные узлы (наладки) (кондукторная плита с комплектом кондукторных втулок; установочно-зажимные узлы и др.).
С помощью скальчатых кондукторов можно обрабатывать самые разнообразные по форме и размерам детали: валики, кронштейны рычаги, корпуса. В корпус 1 кондуктора встроен цилиндр 2, где перемещается поршень со штоком 3, заменяющим собой одну из трех скалок. На скалках установлена плита 4, в которой непосредственно или в прикрепляемой к ней сменной плите монтируются кондукторные втулки. Сменная подставка для установки обрабатываемых деталей базируется по плоскости корпуса и двум установочным штифтам 6 Сменная кондукторная плита базируется по нижней плоскости плиты 4 и двум установочным штифтам 5. Сжатый воздух поступает в цилиндр; через штуцера 7.
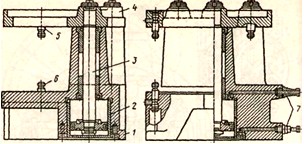
Рис. 3.6. Пневматический скальчатый кондуктор
1- корпус; 2 – цилиндр; 3 – шток; 4 – кондукторская плита; 5 и 6 установочные штифты; 7 - штуцера
Универсально-сборное приспособление (УСП) — наиболее распространенная система переналаживаемых приспособлений. Оно применяется в условиях мелкосерийного и серийного производства. На рис.3.7 показано приспособление, предназначенное для базирования и закрепления детали типа «рычаг» при обработке по контуру на фрезерных станках с ЧПУ.
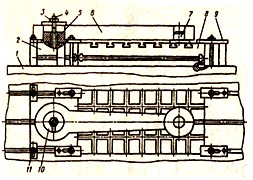
Рис. 3.7. Приспособление для установки рычага
- стол; 2 – гидроцилиндр; 3 – гайка; 4 – шпильки; 5 втулка 6 заготовка установочные штифты; 7 – плавающий штырь; 8 - базовая плита 9 и 11 – прихваты; 10 - сменная шайба
На рис. 3.9 приведена компоновка переналаживаемого круглого накладного кондуктора для сверления отверстий, расположенных неравномерно по окружности.
При обработке заготовок на многоцелевых станках с ЧПУ используется универсально-сборная переналаживаемая оснастка (УСПО) (рис.3.8). На рис. 4.10. изображено двухместное гидравлическое приспособление, предназначенное для базирования и закрепления двух заготовок корпусных деталей.
Механизация и автоматизация являются одним из основных направлений в проектировании приспособлений для специальных и специализированных ремонтно-восстановительных производств.
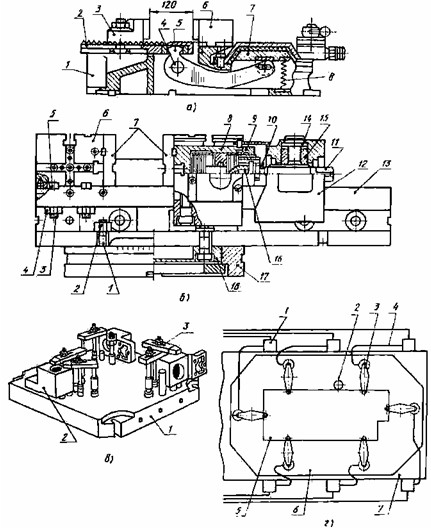
Рис.3.8. Конструкции зажимных приспособлений
для станков с ЧПУ (а-г)
Время машинной работы (резание) в среднем не превышает 50% от времени работы за смену. Остальное время затрачивается преимущественно на вспомогательную работу: установку и закрепление ренодетали, управление станком, контроль в процессе их изготовления.
В зависимости от серийности производства вспомогательное время составляет 25...60% от времени рабочей смены.
При проектировании приспособлений и загрузочных устройств можно обеспечить механизацию или автоматизацию любого из следующих приемов вспомогательной работ на станке:
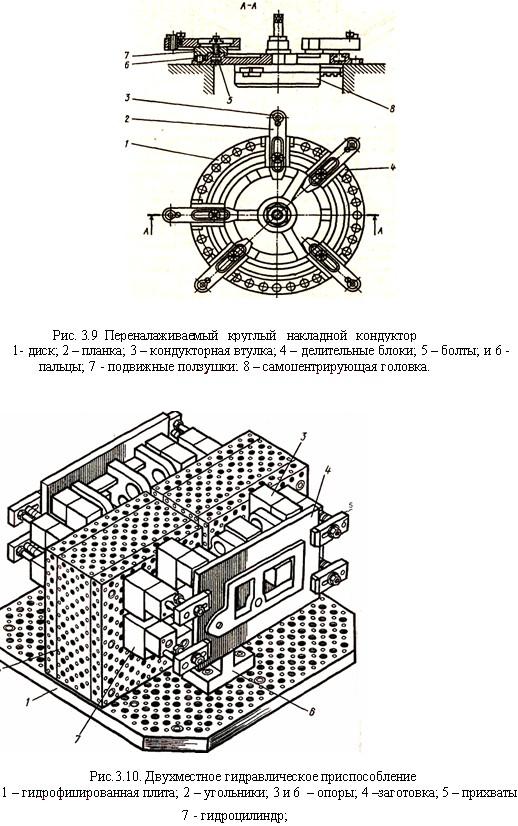
- загрузку обрабатываемых ренодеталей в рабочую зону приспособления (производится с помощью загрузочного устройства или механической руки, а при обработке из прутка – с помощью специального подающего устройства;
- базирование ренодеталей, т.е. доведение их базовых поверхностей до полного контакта с установочными элементами приспособления (производится вспомогательными цилиндрами и мембранами, обычно сблокированными с цилиндрами, осуществляющими окончательный зажим);
- закрепление и открепление;
- периодические повороты ренодеталей при обработке с последующей фиксацией и зажимом поворотной части приспособления;
- вращение при непрерывной обработке, например, при непрерывном фрезеровании с механизированным или автоматизированным закреплением обрабатываемых ренодеталей на вращающимся столе;
- удаление обработанных ренодеталей из рабочей зоны приспособления (выталкивание пружинным, пневматическим или гидравлическим плунжером, скатывание по желобу), в ряде случаев работу выталкивателя блокируют с действием зажимного устройства;
- очистку установочных поверхностей приспособления от стружки струей сжатого воздуха, охлаждающей жидкости или путем отсоса стружки с помощью специальных устройств.
Уровень автоматизации того или иного приспособления определяется количеством рабочих приемов, охваченных механизацией или автоматизацией.
|