2.2.4. Выбор технологического маршрута изготовления ренодетали и определение содержания операций
Проектирование ТП изготовления ренодеталей представляет собой сложную комплексную многофакторную технико-экономическую задачу. В основе решения этой задачи рационально положить общепринятую обобщенную блок-схему технологического процесса восстановления деталей, представленной на рис.2.5. Из которой следует, что:
1.Технологическая подготовка восстановления изношенных ренопригодных деталей, СЕ и машин должна включать:
-
разборку и очистку;
-
отбор реноизделий, подлежащие восстановлению;
-
определение дефектов деталей, заполнение дефектной ведомости на ренодетали;
-
разработку плана восстановления ренозаготовки и определение типа производства;
-
выбор технологических баз для процесса механической обработки ренозаготовки до и после нанесения восстановительного покрытия;
-
расчет припуска на изготовление ренодетали. Определение толщины наращиваемого слоя;
-
подбор материала восстановительного покрытия и выбора способа и режимов восстановления и механической обработки;
-
технологическое обоснование выбранного способа восстановления ренодетали по сравнению с другими известными;
2. Процесс восстановления ренодеталей может дополнительно включать операции:
- термическо- или химико-термической обработки;
- поверхностно-пластического деформирования;
- нанесения защитных покрытий;
- отделки;
- контроля и консервации.
Рис. 2.5. Блок - схема технологического процесса восстановления реноизделия
Таким образом, основное содержание технологии изготовления ренодеталей заключается в выполнении операций:
- предварительной подготовки поверхностного слоя под последующее нанесение покрытия;
- восполнение утраченного в процессе эксплуатации поверхностного слоя;
- последующей механической обработки, с целью обеспечения необходимой точности и качества поверхности, в соответствии с заданными требованиями и ТУ.
При проектировании маршрутного ТП необходимо обеспечить решения следующих задач:
- дать общий план обработки восстановления поверхностей;
- установить состав и последовательность восстановительных операций;
- обосновать для каждой операции перечень обрабатываемых поверхностей;
- определить методы восстановления и последующей обработки;
- установить входные характеристики точности;
- выбрать и установить схемы базирования;
- определить тип средств технологического оснащения (оборудование, приспособления, режущий и мерительный инструменты).
Условием выполнения этих задач является обеспечение заданных показателей качества ренодеталей при принятых критериях экономичности, производительности и облегчения труда.
При неавтоматизированном проектировании многие этапы, связанные с анализом технических условий и показателей точности ренодеталей, исходного состояния ренозаготовки, определением технологических комплексов поверхности и способа базирования, формирования отдельных операций, их последовательности и др.; решаются на основании интуиции и опыта технолога.
В условиях автоматизированного проектирования ТП реновационного производства эти задачи могут решаться проще по аналогии с ТП обычного производства.
На рис 2.6 а и б показана универсальная схема технологического проектирования изготовления ренодеталей [9]. Схема охватывает два этапа: разработку технического задания (рис. 2.6, а) и технологического процесса
(рис. 2.6, б).
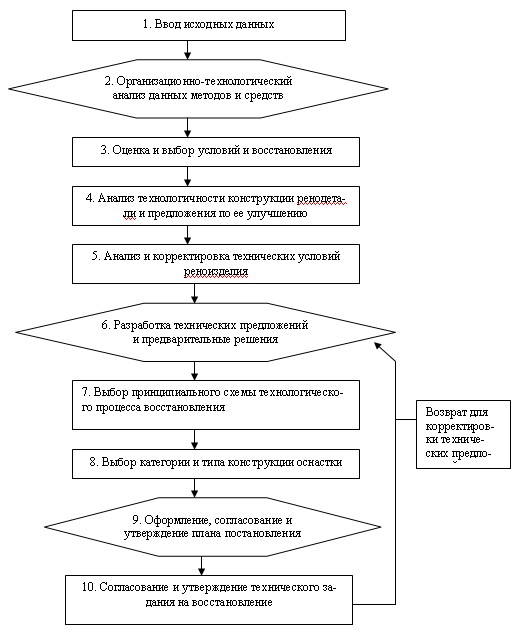
а)
Рис 2.6. Блок-схемы разработки технического задания (а) и ТП восстановления изделия (б)
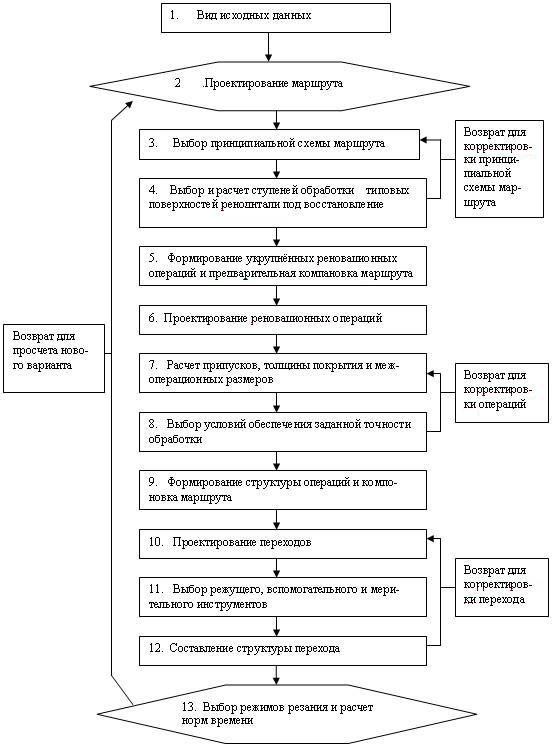
На первой стадии проектирования при обработке технического задания (рис 2.8, а) осуществляют организационно-технический анализ исходных данных и условий проектирования ТП, вырабатывают технические предложения и предварительные решения. Многие действия этапа основаны на логических рассуждениях, сопровождаемых некоторыми расчетами по рассмотрению и сравнению возможных вариантов решения задач, связанных с установлением типа и организационной формы производства, анализом конструкции ренодетали и разработкой рекомендаций по ее улучшению.
Несколько большие возможности вариантного расчетно-точностного проектирования открываются при анализе и корректировании технологических условий оценки ренодетали по параметрам точности, качеству подлежащей восстановлению поверхности и постановке размеров. Именно при таком проектировании осуществляется перевод требовании к качеству реноизделия в технические условия его приемки, выявляются функциональные параметры точности изделия, устанавливаются функциональные и сборочные допуски для исходных звеньев функциональных сборочных размерных цепей; рассчитываются нормы точности для обработки, осуществляется проверка на совместимость допусков различных геометрических параметров точности.
При решении этих частных задач на стадии разработки технического задания уже формируется основные направления поиска общего, наиболее рационального технологического решения, которые далее последовательно уточняются при анализе технологичности ренодетали, выборе схем базирования и способов достижения заданных параметров точности. Опыт и интуиция проектанта здесь подкрепляются рекомендациями справочной и технической литературы, результатами статистических исследовании, которые позволяют количественно оценить рассматриваемые варианты.
Вторая стадия проектирования технологического процесса включает в себя решения большого числа новых задач разработки ТП восстановления изделия, начиная от проектирования схемы маршрута до проектирования условий выполнения переходов.
Проектирование технологического маршрута изготовления ренодетали осуществляют на основе комплексного размерного - точностного анализа и описания размерных связей изделия, а также составления и пересчета размерных цепей. Этот процесс достаточно сложен как для неавтоматизированного проектирования, так и особенно при автоматизации. Не все задачи этого этапа можно решить расчетным путем.
Перспективным для задач по выбору баз является метод матричного анализа совокупностей поверхностей ренодетали, при котором на основании точностных характеристик поверхностей и их взаимного расположения определяется искомый вариант базирования и последовательность обработки восстанавливаемых поверхностей.
Расчетные и статистические способы применяют в настоящее время при оценке вариантов решения одной из центральных задач проектирования технологического маршрута – выбор ступеней обработки элементарных поверхностей ренодетали.
Расчетный способ, например, основан на определении затрат, связанных с изменением состояния поверхности при переводе её из состояния ренозаготовки в состояние готовой ренодетали различными технологическими методами.
Наиболее точно необходимое число ступеней (плана) обработки поверхности ренодетали можно определить с помощью расчетно-точностных методов, открывающих существенные резервы повышения производительности механической обработки. Выбор маршрута изготовления ренодетали, планов обработки отдельных поверхностей, дающих представление о количестве переходов и методов их выполнения, а также установление вида оборудования и типа производства, в условиях которого будет осуществляться изготовление ренодеталей, является исходной предпосылкой для разработки и определения содержания операций технологического процесса (ТП).
Возможны два пути поиска решений плана обработки отдельных поверхностей.
Первый путь – использование типовых планов обработки отдельных поверхностей, рекомендуемых справочниками и технической литературой. Обычно такие рекомендации решают обеспечение точности для сочетаний параметров (точности размеров, формы, качества поверхности).
Второй путь поиска решений плана обработки – определение числа ступней обработки на основании расчетов по формулам связывающих их с уточнением .
Уточнение технического процесса есть отношение погрешности заготовки к погрешности обработанной детали.

Определение количества ступней обработки осуществляется расчетным методом.
Количество ступней обработки – это результат разложения общего уточнения на составляющие 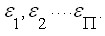
Общее уточнение может быть представлено, как произведение уточнений, осуществляемых на каждой ступени обработки.

При разделении общего уточнения на сомножители (ступени) следует учитывать следующие рекомендации:
- для первой ступени черновой обработки достижимая величина уточнения 
- для промежуточных ступеней получистовой обработки 
- для ступеней чистовой обработки с допусками точности JT5… 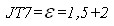
Таким образом, если нам необходимо получить поверхность на заготовке с допуском ?=1,5 мм, то потребное количество ступеней обработки будет определено следующим образом:

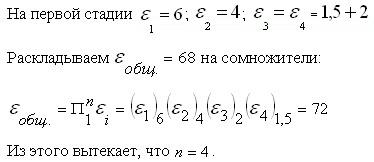
Следовательно, чтобы получить размер из литой ренозаготовки JT7 точности, необходимо предусмотреть ее 4 ступени обработки.
Количество ступеней обработки можно получить и по экспериментальной формуле
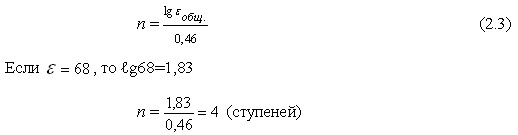
Наиболее простым методом является метод определение количества ступеней обработки табличным способом.
Определение количества ступеней обработки литых заготовок, например, устанавливается по ГОСТ 26645-85. Он устанавливает зависимость количества ступеней обработки от отношения допуска готовой детали к допуску заготовки.
Первоначально проектант определяет тип литой заготовки, класс ее точности и допуски на интересующие поверхности. Затем определяет отношение ?дет/ ?заг, а также это же соотношение допусков формы детали и заготовки.
Возможные варианты планов обработки элементарных поверхностей проверяют на: совместимость решений, принятых для разных параметров точности (размеров, нормы, шероховатости поверхности); применимость этих решений для других поверхностей того же типа; производительность и экономичность (по укрупненным расчетам); соответствие с решениями принципиальной схемы последовательности обработки ренозаготовки (станки, методы обработки, схемы установок и т.п.).
Целесообразность разделения ТП на стадии обработки обуславливается необходимостью получения деталей заданной точности и рационального использования оборудования, так как это связано с числом и содержанием операций ТП.
На основании выбранного плана обработки формируется технологический маршрут изготовления ренодетали, представляющий собой последовательность выполнения технологических операций. При механической обработке, например, когда задается точность и шероховатость поверхности выбор стадий (плана) обработки восстанавливаемой поверхности ренозаготовки можно определить (табл. 2.6.)
Таблица 2.6.
Выбор стадий обработки поверхностей в зависимости от требований по точности и шероховатости
Стадии обработки |
Достижимые точность (квалитет) и шероховатость Ra(Rz), мкм |
12/(80) |
10/(20) |
7/0,63 |
6/0,16 |
черновая |
1 |
1 |
1 |
1 |
чистовая |
- |
2 |
2 |
2 |
тонкая |
- |
- |
3 |
3 |
отделочная |
- |
- |
- |
4 |
Проектирование схемы технологического маршрута на первом этапе технического проекта завершается формированием укрупненных операций и компоновкой их последовательности.
Вариантное решение этих задач основывается на использовании принципов технологической совместимости и анализе размерных связей ренодетали. Операции группируются по стадиям до термообработки и после нее, перечень их упорядочивается с учетом принципиальной схемы технологического процесса, намеченной на стадии технического задания и, рассмотрения размерных связей, обеспечивающих восстановление ренодетали в соответствии с требованиями чертежа.
Весьма ответственным этапом разработки технического проекта является проектирование технологических операций. Для проектирования технологических процессов разработаны расчетные методы решения основных задач это этапа. В число их, прежде всего, входят расчет припусков и межоперационных размеров по количественным зависимостям между припусками и методами обработки, определяющими геометрические и качественные характеристики детали; выбор условий обеспечения заданной точности на основе анализа факторов, влияющих на точность и экономичность обработки; формирование структуры операции по результатам анализа размерных связей деталей, с учетом множества переходов, методов размерной наладки, возможности образования при различных с максимальным выполнением операций, основных погрешностей обработки и оценки их влияния на параметры точности детали.
Проектирование технологического процесса механической обработки восстановленной поверхности завершается определением условий выполнения переходов технологических операций и составляется технологический маршрут. При этом следует исходить из того, что составление маршрута представляет сложную задачу с большим числом возможных вариантов решения. Его цель – дать общий план обработки заготовок, наметить содержание операций технологического процесса и выбрать тип оборудования.
Технологический маршрут – это последовательность изготовления ренодетали по операциям, начиная с заготовительной. При его разработке определяют:
- последовательность и содержание технологических операций;
- оборудование для их выполнения;
- необходимую технологическую оснастку (приспособления, штампы, пресс-формы и т.д.).
Маршрут изготовления ренодетали устанавливает последовательность обработки поверхностей детали с целью обеспечения ее заданного качества. Особое внимание следует обратить на применение новых методов обработки: электрофизических и электрохимических, режущих инструментов на основе сверхтвердых материалов, в том числе алмазов, и др.
Маршрутный технологический процесс оформляется в табличной форме (табл. 2.7).
Таблица.2.7.
Табличная форма оформления маршрутного процесса восстановления
№ п/п |
Наименование
операции |
Содержание
операции (переходы) |
Тип
станка |
Приспособление |
1 |
2 |
3 |
4 |
5 |
Техническое обоснование маршрута обработки выполняется на основе сопоставления различных вариантов последовательности выполнения операций и схем установки заготовки и в связи с этим различных вариантов маршрута обработки.
При сопоставлении схем установки заготовки необходимо провести анализ точности обработки. Определяются погрешности базирования, суммируя которые с погрешностями закрепления, вычисляют погрешности установки. Добавив к погрешности установки статической и динамической настройки системы “станок – приспособление – инструмент - заготовка”, получают производственную погрешность на данной операции, т. е. после рассеивания выбранного параметра качества заготовки (например, размера).
Анализ базирования и расчет точности механической обработки могут быть проведены только на основе анализа и решения соответствующих технологических размерных цепей.
При этом следует исходить из следующего:
- при установлении общей последовательности обработки следует сначала обрабатывать поверхности, принятые за технологические базы;
- затем обрабатывают остальные поверхности в последовательности, обратной степени их точности; чем точнее должна быть обработана поверхность, тем позже ее обрабатывают;
- последней необходимо обрабатывать ту поверхность, которая является наиболее точной и имеет наибольшее значение для работы детали в машине.
Для своевременного выявления раковин в восстановленном слое и других дефектов ренодетали сначала проводят черновую, а если требуется, и чистовую обработку поверхностей, на которых эти дефекты не допускаются. В случае обнаружения дефектов ренозаготовку либо бракуют, либо принимают меры для исправления брака.
В производстве точных и ответственных реноизделий маршрут обработки часто делят на стадии: черновую, чистовую и отделочную. На первой снимают основную массу металла в виде ликвидов, припусков; вторая имеет промежуточное значение; на последней, обеспечивается заданная точность и шероховатость поверхностей. На стадии черновой обработки появляются сравнительно большие погрешности, вызываемые деформациями восстанавливаемого изделия после температурного воздействия при нагреве нанесения покрытия, от сил резания и сил закрепления заготовки, а также её интенсивный нагрев. Чередование черновой и чистовой обработок в этих условиях не обеспечивает заданную точность. После черновой обработки наблюдаются наибольшие деформации заготовки в результате нагрева и перераспределения остаточных напряжении в восстановленном слое. Группируя обработку по указанным стадиям, увеличивают разрыв во времени между черновой и отделочной обработкой и позволяют более полно проявится деформациям до их устранения на последней стадии обработки. Вынесением отделочной обработки в конец маршрута уменьшают риск случайного повреждения окончательно обработанных поверхностей в процессе обработки и транспортировки. Кроме того, черновую обработку могут выполнять рабочие более низкой квалификации на малоточном изношенном оборудовании.
Изложенный принцип построения маршрута, однако, не во всех случаях является обязательным. При жесткой ренозаготовке и малых размерах обрабатываемых поверхностей окончательную обработку отдельных элементов можно выполнять в начале маршрута.
Последовательность обработки реноизделия зависит от системы простановки размеров. В первую очередь следует обрабатывать ту поверхность, относительно которой на чертеже координировано большее число других поверхностей. Вспомогательные операции (сверление мелких отверстий, снятие фасок, прорезка канавок, зачистка заусенцев и т.д.) обычно выполняют на стадии чистовой обработки. На данном этапе маршрута последовательность выполнения этих операций часто может меняться; она не влияет на качественные показатели и экономику процесса в целом.
Предварительное содержание операций устанавливаем объединением тех переходов на данной стадии обработки, которые могут быть выполнены на одном станке. На содержание операций влияет также необходимость сокращения числа переустановок ренозаготовок со станка на станок. При составлении маршрута обработки ренозаготовки по отдельным операциям следует установить также тип станков и другого технологического оборудования. На последующих этапах обработки технологического процесса эти наметки уточняются, путем определения основных размеров и характеристик станков, а также их конкретных марок и моделей. Итоги работы по данному этапу (перечень и содержание операций, оборудование и оснастку) заносим в технологическую маршрутную карту (МК). Принципиально правильный подход к составлению маршрута обработки ренозаготовок различного класса точности для данных производственных условий должен определяться на базе типизации технологических процессов.
Знать маршрут обработки отдельных поверхностей необходимо для последующего расчета промежуточных, общих припусков на обработку, а также промежуточных размеров ренозаготовки по технологическим переходам обработки. Маршрут обработки устанавливаем исходя из требований рабочего чертежа и принятой ренозаготовки. По заданному классу точности, шероховатости данной поверхности и с учетом размера, массы и формы ренозаготовки, выбирают один или несколько возможных методов окончательной обработки. Решение этой задачи облегчается при использовании технологических характеристик методов обработки. Зная вид реноизделия, подлежащего восстановлению, таким же образом выбирают первый начальный метод маршрута. При точной ренозаготовке сразу можно начинать чистовую, а в некоторых случаях и отделочную обработку.
При построении маршрута исходят из того, что каждый последующий метод должен быть точнее предыдущего.
Примерные маршруты обработки поверхностей приведены в табл.2.8.
Таблица 2.8.
Примерные маршруты механической обработки поверхностей
Квалитет точности |
Шероховатость , мкм |
Код материала |
Маршрут обработки поверхностей |
Наружных цилиндрических |
Внутренних цилиндрических |
плоских |
1 |
2 |
3 |
4 |
5 |
6 |
14-12
11-10 |
2,5,0-
6,3
5,0-2,5 |
1,2,3
1,2,3
1,2,3
4
4
4
1,2,3
1,2,3
1,2,
4
4
4 |
0
-
-
О, ТО
ТО, Ш
Оп, Оч
ОШ
Оп, Оч, ТО
Оп, ТО, Ш |
С
З
РТ
СТ, О
З, ТО
РТ, ТО
С, З, Р
С, РТ, Р
-
С, З, ТО, Ш
С, РТ, ТО
Зп, Зч, ТО, Ш |
СТ
A
O
СТ, ТО
Ф, ТО
О, ТО
Фп, Фч
-
ТО, Шп
Ф, Шп
Ф, ТО, Шп
СТ, ТО, Шп
О, ТО, Шп |
9-7 |
1,25-0,63 |
1,2,3
1,2,3
1,2,3
1,2,3
1,2,3
1,2
1
4
4
4
4 |
Оп, Оч, От
-
-
-
-
О, Ш
Шп, Шч
Оп, Оч, ТО, Ш
Шп, ТО, Шч
-
-
|
РУ, Р
С, З, Рп, Ру
С, РТп, РТч
С, З, РТч
С, П
РТп, РТч, РТт
С, РТ, ТО, Ш
РТп, Рч, ТО, Ш
С, З, ТО, Ш
РУ, ТО, Х |
С, П
Ф, П
-
-
-
Ф, Шч
Ф, ТО, Шч
С, ТО, Шч
О, ТО, Шч |
|
0,32-0,16 |
3
3 |
Оп, Оч, ПО
Оп, Оч, От, ПО |
-
- |
Фп, Фч, ПО
Оп, Оч, ПО |
|
0,08-0,04 |
3
4
1,2,3
1,2,3
1,2,3
1,2,3
1,2,3 |
Оп, Оч, От, ПОЧ,
Пот
Оп, Оч, ТО, Шп,
Шт, ПО
Оп, Оч, От, ПО
-
-
-
-
|
-
-
-
РУ, Рп, Рч
С, З, Рп, Рч
С, З, РТч
РТт
РТп, РТч, РТт
С, З, П |
Оп, Оч, ПО
Пот
Фп, Фч, ТО
Шп, Шт, ПО
СТ, Фт, ШБ
Фп, Фт, ШБ
-
-
- |
6 |
0,32-0,16 |
1
1
1,2
3
4
4
4
4 |
О, Ш, СУ
О, Шп, Шт, П
-
-
О, Шп, ТО, Шт
О, Шп, ТО, Шт, СУ
Оп, Оч, ТО, Шч, СУ |
-
-
-
-
РТ, ТО, Ш, Х
С, З, ТО, Ш, Х
С, П, ТО, Х
РУ, Р, ТО, Х |
-
-
Фп, Фч, Шч, ПО
Фп, Фч, То, Шч, Д
С, Фт, ТО, Д
Ф,ТО, Шп, Шч, Д
О, Шп, ТО, Шч ,Д |
|
0,32-0,16 |
3
4
4
4
4
4 |
Оп, Оч, От
Оп, Оч, ТО,Шч, СУ
О, Шп, ТО, Шч, Шт, СУ
О, Шп, ТО, Шч, Д
-
- |
РТ, ТО, Ш, Х, Д
С, З, ТО, Щ, Х, Д
С, П, ТО, Хп, Хч
РУ, ТО, Х, Д
С,РТч,Рт,ТО,Х,Д |
СТ, ТО, Шч, Шт, Д
Ф, ТО, Шч, Шт, Д
Ф, Шп, ТО, Шч,Шт,Д
О,Шп,ТО,Шч,Шт,Д
- |
5 |
0,08 – 0,04 |
I
2
2
I,2
4
4
4
4
4 |
Оп, Оч, Шп, Шч, СУп, СУч
-
-
-
Оп,Оч,Шч,СУч
Оп,Оч,ТО,Шч,Шт,Д
Оп,Оч,ТО,Шч,Дп,
Дч
Ш,ТО,Шч,СУп,СУч
- |
-
С,З,Р,Х,Дп,Дч
РУ,Х,Дп,Дч
-
РУ,Р,ТО,Х,Дп,
Дч
С,З,Р,ТО,Дп,Дч
С,П,ТО,Х,Дп,Дч
РТ,РТт,ТО,Дп,
Дч
С,РТ,РТт,ТО,Х,Д |
-
-
-
Ф,Шп,Шч,Шт,ПО
СТ,ТО,Шп,Шч,Шт,ПО
Ф,ТО,Шп,Шч,Шт,ПО
О,ТО,Шп,Шч,Шт,Д
О,ТО,Шп,Шч,Шт,Д
- |
Примечание. О – обтачивание, Ш – шлифование, СУ – суперфиниширование, ПО – полирование, Д – доводка, ТО – термическая обработка, С – сверление (рассверливание), РТ – растачивание, РУ – ружейное сверление, Р – развертывание, РТ – растачивание, П – протягивание, Х – хонингование, СТ – строгание, Ф – фрезерование, ШБ – шабрение;
II – предварительное, ч – чистовое, т – тонкое;
I – незакаленные стали, 2 – чугуны, 3 – цветные металлы и сплавы, 4 – закаленные стали.
В МАДИ разработана методика формирования маршрутов восстановления ренодеталей и оптимизации их количества путём последовательного перебора и объединения сочетаний повреждений.
По мере образования необходимого количества ренодеталей формируются их партии, которые направляются на рабочие места нанесения покрытий, установки и закрепления дополнительных ремонтных деталей, восстановления разрушенных элементов изделия, пластического деформирования и обработки.
Учёт отдельных крупных ренодеталей и партий мелких ренодеталей с их повреждениями служит основой прогноза трудоёмкости и продолжительности восстановления этих реноизделий.
Коротко это можно изложить так, что при разработке маршрутов восстановления деталей следует учитывать следующие основные принципы:
- сочетание повреждений в каждом маршруте восстановления детали должно быть объективно существующим. Сочетания повреждений устанавливают исследованием большого количества ренодеталей;
- число маршрутов восстановления ренодеталей должно быть минимальным. Большое количество маршрутов затрудняет организацию, требует большой площади складов. Число маршрутов может быть уменьшено путём объединения подобных сочетаний повреждений, отличающихся друг от друга незначительными по трудоёмкости повреждениям, а также исключением маршрутов с редко встречающимися сочетаниями повреждений. Сокращать количество маршрутов можно объединением операций по устранению взаимосвязанных повреждений (восстановление соосных отверстий, ориентированных относительно друг друга плоскостей);
- содержание маршрута учитывает требования к точности взаимного расположения поверхностей детали. Так, если аварийно изношена одна шейка коленчатого вала и принят способ восстановления её наплавкой, механической и термической обработкой, то в маршрут восстановления включают все шейки независимо от того, что остальные шейки не повреждены;
- восстановление ренодетали по каждому отдельному маршруту должно быть экономически целесообразным.
В качестве критерия эффективности выступают затраты на восстановление, а сравнительной базой является цена новой детали. Затраты на восстановление ренодетали включают затраты прошлого (овеществлённого) и живого труда.
|